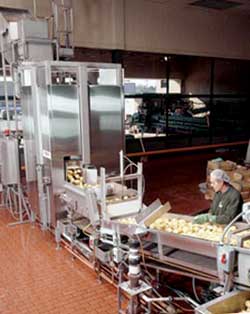

Over the past two years, Utz has been testing a new three-stage batch peeler from Heat and Control, Inc. in an effort to trim peel removal costs.
“Peel loss percentages change from fresh dug to storage potatoes,” according to Utz Plant Manager Jim Strevig. “With VersaPeel®, our fresh crop peel loss ranges from 0.5% to less than 2%, while storage crop peel loss is 6% to 8%.” This is a significant reduction from the peel loss generated by other batch peelers used at Utz, added Strevig. With VersaPeel, improvements range from 6% to 8% for storage crop, and 4% to 6% better for fresh potatoes.
Low peel loss numbers convert to a big increase in finished product output or a major savings in raw potato costs when the same production rate is maintained. According to Heat and Control, VersaPeel reduces potato usage on a 1,000 finished lb./hr. potato chip line approximately 354,000 pounds per year, or provides annual savings of $31,860 in potatoes alone (based on $0.09 / lb. potato cost, with operation at 8 hours/day, 5 days/week, and 50 weeks/year).
Another advantage is improvement in product quality and savings achieved from reduced potato waste. Potatoes leave VersaPeel with a smooth surface that aids slicer efficiency and generates less waste. “Our potatoes have a cleaner, brighter, more consistent appearance when peeled in VersaPeel,” Strevig stated. Flat spots are nearly eliminated, so our slicers produce less waste, he said. As a result, the fryer runs cleaner and wastewater treatment/starch removal requirements are also reduced.
Most abrasive peelers grind away at potato surfaces until the desired amount of peel—and much usable potato—are removed. VersaPeel tumbles potatoes against gradually finer abrasives in three retracting drums. This process rapidly removes peel—even from eyes and recesses—without significant loss of potato solids.
As potatoes enter the VersaPeel, a rotary disc at the bottom of the peeling chamber slows to minimize bruising. The disc then accelerates to the pre-set speed and potatoes gently tumble against the abrasive liner or brushes inside Peeling Drum 1. Strevig uses different combinations of brushes and abrasive liners to adjust peeling depending on the crop, time of year, and variety of potato used.
After the set peeling time, Drum 1 raises and exposes the potatoes to less abrasive brushes in Peeling Drum 2. Again the drum raises and potatoes are polished by fine brushes inside Drum 3. The rotary disc slows, Drum 3 raises, and potatoes are gently discharged through a tangential outlet to minimize damage.
The entire process is controlled from an optional PLC/ touch screen system. Peeling requirements for each potato variety are stored and recalled as needed. “Computerized controls and readouts give us instant quality control at the operator level,” Strevig explained. “Along with the automatic weight control system, this allows us to maintain our standards during all shifts.”