
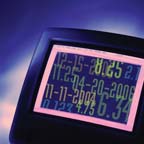
Focusing on the use of metrics as a business improvement tool, the report shows a direct correlation between the length of time these programs have been in place and business improvements. "A major factor that sets the best-in-class apart from the industry average companies is the length of time that they have had these programs in place," says Biddle. "While 75% of the best-in-class have synchronized business and plant metrics for two or more years, only 22% of the industry average companies have programs in place for that length of time."
When discussing metrics with various consultants and software vendors, the vocabulary may vary. Business Intelligence (BI) and Business Performance Monitoring (BPM) are common terms referring to measuring your business. A Key Performance Indicator (KPI) is a common term for a specific number or metric.
Regardless of what the measurements are called, a key issue is your system's ability to automatically generate these numbers as a by-product of your daily operations. A system should also support "drill down," the ability to go into greater detail and determine the "why" of business issues.
The common strategy of metrics-based programs is summed up with the phrase, "You improve what you measure." In most food plants, the two most common focus points are cost reduction and on-time delivery, which can be measured in a number of ways. Inventory reductions are the most common cost reduction effort and are usually measured by inventory turns for each type of inventory (packaging, ingredient, finished product, MRO, etc.). Maintenance work can be measured by the ratio of planned to unplanned downtime.
On-time delivery, however, is best measured against the original customer request date instead of the order commitment date. Best-in-class companies even take it one step further. They measure against the customer delivery date as supplied by their logistics providers (as opposed to ship dates versus planned ship dates). In this way, you can precisely determine when the product reached your customer, which is ultimately a factor in how he/she evaluates your service.
Best-in-class companies monitor these figures constantly at various levels of detail and can use these metrics to identify and improve areas of competitive advantage and thus measure and direct continuous improvement programs. And what if you aren't currently using metrics? Biddle suggests you "concentrate on a few, key measurements and show improvements to gain an understanding in the use of metrics. [If you have some] programs in place, concentrate on specific themes, driven by the corporate strategy."