
Glitzy graphics and gaudy price tags were the knock on simulation models in years past, but the situation is rapidly improving. Packages that accurately emulate the hybrid processes that characterize food and beverage manufacturing are making simulation more than just a snazzy presentation tool for upper management. Just as importantly, they are being offered at prices that won't break the bank.
Palo Alto, Calif.-based Imagine That Inc. has shattered the $1,000 mark with the stripped down edition of its Extend version 5 program. A beefier package at $2,000 is more appropriate for large food companies, but that's still considerably less than users had to pay a few years ago.
To borrow a clich?the programs are more user-friendly than ever before. Food engineers no longer need an advanced degree in computer science and the ability to write FORTRAN to make use of the technology. Windows-based operating systems are now standard, and libraries of equipment icons let users rough out their production and packaging lines on screen to gain insight into the dynamics of their lines and where and why bottlenecks occur.
With the exception of high-profile firms like Coca-Cola, Kraft, Nestle and a handful of others, food companies have been slow to embrace simulation. That is likely to change as software suppliers gear up for a concerted education and sales effort targeting the industry. Lanner Group Inc., whose Witness program is the world's most widely used simulation software in process industries, is focusing on food and beverage firms this year, according to Peter Tiernan, U.S. director of marketing. Arena is another widely used program, and its developer was acquired last year by Rockwell Software. "The food industry is going more toward a service model than a product purchase approach," explains Rockwell's Vivek Bapat, so Rockwell is throwing its considerable marketing muscle behind selling Arena on a project consulting basis.
"Most simulation vendors have not targeted the food industry in the past," points out Bapat. With automotive, semiconductor and other industries making simulation a standard operating procedure for capital projects in the 1990s, food looms as one of the last untapped process manufacturing sectors. Now vendors are making food companies a priority.
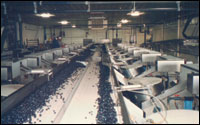
Food processing's special needs
The drop-and-drag age of Windows simplifies the task of simulation modeling, though getting engineers to abandon traditional text-based methodologies will take some persuading. The best argument for embracing the new is the better-mousetrap nature of simulation. Traditional models present a static view of the factory floor. That's fine if the same product is produced and packaged the same way, day after day. That's not the case in food manufacture today. Frequent changeovers are the rule, not the exception, and behind the pretty graphics of a simulation model are formulas that account for lines' dynamism.Andrew J. Siprelle, president of Simulation Dynamics Inc., cites the "slurp factor" in beverage filling to illustrate packaging dynamics. The surge that occurs when a bottle is filled varies in proportion to the volume of the bottle, he explains. A traditional model would pinpoint the bottleneck that occurs when one particular bottle size is used with a line's filler; a simulation would demonstrate how that pinch-point migrates to different places, depending on the size of the bottle being filled.
"For years, simulation has worked well in discreet industries like automotive, where each piece of material is treated as an entity," Siprelle says. "The models are based on item architecture, which is all about pieces and parts. But if you apply that to food production, the model will take longer to run than the actual product, which would make it useless." To make their products useful to food companies, software vendors are embracing flow architecture, a rate-based approach that lends itself to "high-speed packaging or continuous processes in the food industry," he adds.
Bell-Carter Foods, a $120 million olive copacker in Lafayette, Calif., used Siprelle's simulation system three years ago to model production capacity and determine what additional equipment would be needed to meet anticipated increases in processing volume. At the front end, olives have to be batched according to size and then run through pitting machines, a major bottleneck. A changeover for different-sized olives takes two hours, notes Robert Rugeroni, MIS director. But there are many other choke points, particularly in packaging after olives have been filled in cans and retorted, "and they're not in the places you would expect them to be," Rugeroni says.
The exercise helped set capital spending priorities to meet anticipated capacity needs at Bell-Carter, which does extensive private-label packing. It also shed light on optimum scheduling, and that may be simulation's greatest potential contribution to food processors.
"We're all held captive to our scheduling," reflects Malcolm Beaverstock, manager of advanced control and simulation at General Mills in Minneapolis, and the complexity of food processes can sometimes make the optimum scheduling solution seem counter-intuitive. To illustrate, he cites his own experience with a General Mills cereal plant.
The plant had relied on carts to manually move cereal exiting a dryer to packaging. Upper management assumed a system of conveyors could more efficiently handle the task, and one of Beaverstock's earliest simulation projects was to verify that.
Instead, the model determined that productivity would actually drop, at least the way the conveying system was initially designed. The manual transport system offered flexibility that was completely lost with the automated solution. Subsequent simulation tests helped devise a system that ultimately produced a more efficient conveying system, but the lesson was clear: changes in one area can produce unforeseen bottlenecks in another area. Traditional models are ill equipped to detect those snafus, but a simulation can.
"Don't go through a whole simulation if you're just going to tweak a line," Beaverstock advises. "But if you're adding a conveyor, changing storage-tank sizes or adding a new packing line, that's where simulation comes in."
Simulation also proved valuable when General Mills acquired Lloyd's Barbeque Co. two years ago. "By studying the simulation of the smokehouse operation, we showed they could produce enough product to meet anticipated needs from expanded distribution without additional equipment," he reports. That kind of analysis will get a more rigorous test when the pending merger of Pillsbury Co. into General Mills is completed.
Better asset utilization is only part of the payback from simulation, Beaverstock suggests. Of the $5 million he estimates General Mills has saved from 40 simulation models in recent years, $3 million came from scrapping projects that would have been counterproductive. "Cost avoidance is a concept accountants hate, but it's real," he says.
Byron Reed is a food engineer who is plunging into the simulation world with the Witness program, a popular software choice for major food and beverage corporations. "It's going to be a rocky road to start," says Reed, senior processing engineer with Webber/Smith Associates, but simulation is essential for solving highly complex manufacturing issues that can't be addressed with conventional tools. Firms like the Lancaster, Pa., A/E firm are the only practical providers of simulation's benefits to most of the industry, Reed believes.
"Smaller clients are never going to spend $17,000 on this package and then take the time to master it," he says. Yet the potential benefits are enormous.
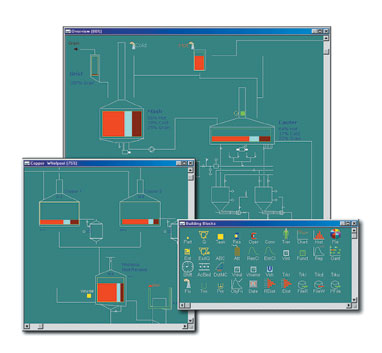
Skill-set challenge
Mastering these models may prove to be simulation's biggest hurdle. While it will take some time for him to learn Witness, Reed is confident his background as an industrial engineer will enable him to build the statistical profiles that are essential at the front end. Likewise, Beaverstock's advanced degrees in chemical engineering and computer science helped him find his way through the vagaries of Extend. "The value of a simulation is to the person who does the simulation," he maintains, so Beaverstock teaches plant engineers to run their own simulations.The support structure at General Mills won't be found at small and mid-sized food companies. At Bell-Carter Foods, simulation work proved to be a pilot project that ended when it failed to find an internal champion. "I can expose people to the technology, but I can't sell it," bemoans Rugeroni, and no one was prepared to become the in-house simulation expoert.
The entrepreneurial nature of food manufacturing can discourage a disciplined approach like simulation, vendors allow, and the business's thin margins are an additional obstacle. "The lower the value or margin on the end product, the less likely the manufacturer is to use simulation modeling," notes Matt Rohr, vice president of simulation at Bountiful, Utah-based AutoSimulations. "Food manufacturers have to see a much bigger gain than 20 percent in production to justify simulation. But in some situations, these models can deliver 50 to 70 percent improvements."
Originally a specialist in material handling simulation, AutoSimulations has branched into packaging, food and beverage with its Tanks & Pipes module. It features the same AutoMod 3-D animations that are the firm's mark of distinction. "Visualization helps the model builder verify that he has built an accurate model," Rohr explains, "and it helps communicate to people who are not versed in the guts of the simulation information." In other words, slick graphics help sell the benefits of an equipment expenditure to top brass unfamiliar with engineering models.
Consultants as mentors
Despite vendors' efforts to dumb down the model-building process, simulation still requires both expertise and ongoing exposure. Food engineers who run a simulation once and put the program on the shelf for eight months might find it difficult to pick up where they left off. One possible solution is to use consultants to shorten the re-learning curve while still executing the simulation in house, suggests Beaverstock. "Unless you're working with simulation all the time, it's easy to forget some aspects of the execution," he says. "The secret may be to use a consultant as a mentor and do the actual data gathering and execution yourself."Random events drive a simulation model, and gathering data on those events is critical to model accuracy. Quantifying setup times, repair times, machine times to failure and other random events may be viewed as tedious grunt work, but it is essential for modeling the process and much cheaper if gathered on staff time than when a consultant's meter is running.
Food companies will never have simulation groups to devise precise models. The production line runs every day, and the new line needs to be operational next week. But a quick and dirty simulation that answers the question, "Does this make sense?" may be all a food company needs.
The good news is, those kinds of simulation tools now exist, and at a price even a small company can afford.
SIDEBAR 1:
Simulation Software Source Guide
While many firms offer simulation software, only a few packages have been designed to meet the specific needs of food and beverage processors. They include:
- Arena, from Rockwell Automation, Pittsburgh. Originally developed by Systems Modeling Corp. of Pittsburgh, Arena was added to the Rockwell portfolio when the firm acquired Systems Modeling last year. A related product was Tempo, scheduling software now marketed as Rscheduler. Visit www.arenasimulation.com
- AutoMod Tanks & Pipes module, from AutoSimulations, Bountiful, Utah. Allows users to include continuous and discreet processes in the same model. Call 801-298-1398 or visit www.autosim.com.
- Extend Plus Industry, from Simulation Dynamics, Maryville, Tenn. Based on the popular Extend package from Imagine That, Extend Plus offers an expanded library of simulated equipment for analyzing food and beverage lines. Call 865-982-7046 or visit www.simulationdynamics.com.
- Simul8 Process, from Simul8 Corp., Herndon, Va. Added to the company's product lineup two years ago, Simul8 Process is designed for food manufacturers and other high-volume manufactures using batch and continuous processes. Call 800-547-6024 or visit www.simul8.com.
- Witness 2001, from Lanner Group Inc., Houston. The global leader in simulation modeling for process industries, Lanner is targeting food and beverage firms with the latest version of its software. Call 713-532-8008 or visit www.lanner.com/americas.

SIDEBAR 2:
Plant tours with added dimension
Just as simulation models translate the spreadsheets of statisticians and industrial engineers into easily grasped graphical representations, 3-D imaging tools are enabling A/E firms to take their food clients on virtual tours of new facilities and reconfigured existing plants.The Washington Group uses a Cyrax modeling technique to create 3-D virtual models to replace conventional two-dimensional drawings of existing plants that are being overhauled. The result is not only a more visually exciting presentation but a more accurate representation: "We have been able to cut rework in the field to less than one percent," a fraction of the ratio when engineers try to recreate a plant's layout with line drawings based on tape measurements and plumb bobs, says Greg Lawes, manager of laser scanning services. Using a laser camera to shoot the plant from various positions, Lawes can incorporate 3-D models of new equipment and create the optimum configuration for a new production line.
Hixson Inc. has used a similar computer-aided system to take clients on "predetermined, visual-reality tours" of their plants for several years, according to Mike Steur, director of client development for the Cincinnati A/E firm. "It might have taken 24 hours to generate the frames for a 20 minute visual walk-through seven years ago," he says. "Now it takes one hour, and it gives customers a better idea of what they're getting before they spend big bucks."
There's more than sizzle to these virtual steaks. A simulation of how a dairy plant with metal walls would look like was used to persuade the local zoning board to drop a demand for brick walls, saving the client $100,000, Steur recalls. "It is a reassurance, but once people see what a building or plant interior is going to look like, they start coming up with other ideas," he adds.