Significant progress has been made on thermochemical conversion of swine waste to crude oil in the last 10 years, but chemical engineers are not rushing to market.
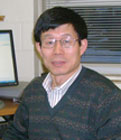
Yuanhui Zhang, professor of agricultural and biological engineering, University of Illinois at Urbana-Champaign.
Mother Earth used heat, pressure and the absence of air to convert dinosaur remains to crude oil, but the process took eons. Technologies such as thermal depolymerization and thermochemical conversion also focus on the application of heat and pressure to break down long-chain polymers in carbon waste into short-chain petroleum hydrocarbons, and complete the process in a considerably shorter period of time.
Thermal depolymerization was first out of the gate. In 2003, the Renewable Environmental Solutions (RES) plant came on line in Carthage, MO. A joint venture between Changing World Technology (CWT) and ConAgra, which operates a Butterball turkey processing facility 100 yards away, RES renamed the technology “thermal conversion process” and ballyhooed it as a “green” solution to foreign-oil dependency. Up to 200 tons of turkey offal was supposed to be converted economically to 600 barrels crude oil No. 4 every day, with no pollutants and only water as a byproduct. Instead, output never reached half that level, construction costs were double the original estimate, the stench from the facility generated multiple lawsuits and the cost of production was twice the selling price of the crude. Plans for three additional plants are on hold.
Thermal depolymerization was first out of the gate. In 2003, the Renewable Environmental Solutions (RES) plant came on line in Carthage, MO. A joint venture between Changing World Technology (CWT) and ConAgra, which operates a Butterball turkey processing facility 100 yards away, RES renamed the technology “thermal conversion process” and ballyhooed it as a “green” solution to foreign-oil dependency. Up to 200 tons of turkey offal was supposed to be converted economically to 600 barrels crude oil No. 4 every day, with no pollutants and only water as a byproduct. Instead, output never reached half that level, construction costs were double the original estimate, the stench from the facility generated multiple lawsuits and the cost of production was twice the selling price of the crude. Plans for three additional plants are on hold.
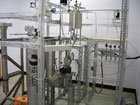
A skid with a continuous thermochemical conversion reactor sits in the research lab in the agricultural engineering sciences building in Urbana-Champaign, IL. Upgrading from a batch reactor was one of the development program breakthroughs. Source: University of Illinois-Urbana.
Thermal depolymerization was developed by a Chicago microbiologist, and the feedstock claims made by CWT were extravagant. Medical waste, corn stalks, old tires and plastic as well as turkey offal all would yield oil, according to published reports. Unlike the biochemical conversion process that generates ethanol, the science that converts those biomasses into short-chain carbon and hydrogen remains shrouded in secrecy.
Another type of pyrolysis has been labeled thermochemical conversion (TCC) and is being nurtured by a team of engineers at the University of Illinois at Urbana-Champaign. A decade ago, members of the agricultural and biological engineering department began experimenting with TCC using swine manure. Because the raw material contains less lignin than most other biomass, the conversion to oil was easier than with other feedstocks. However, doing it economically is another matter, and the scientists continue work to optimize a process involving moderate heat and pressure. In the meantime, the engineers have begun working with entrepreneurs at Worldwide BioEnergy LLC, a Jefferson City, MO, group that will fabricate a mobile pilot plant that moves TCC out of the lab and into field tests.
Heading the project is Yuanhui Zhang, professor of agricultural and biological engineering at the University of Illinois (U of I). A native of China, Zhang earned a BS in agricultural engineering at Shandong Institute of Technology before moving to Canada’s University of Saskatchewan, where he completed post graduate and doctoral work in agricultural engineering. He served as an adjunct professor in Saskatchewan and as an engineering research scientist at Prairie Swine Center in Canada before joining the U of I faculty in 1996.
Another type of pyrolysis has been labeled thermochemical conversion (TCC) and is being nurtured by a team of engineers at the University of Illinois at Urbana-Champaign. A decade ago, members of the agricultural and biological engineering department began experimenting with TCC using swine manure. Because the raw material contains less lignin than most other biomass, the conversion to oil was easier than with other feedstocks. However, doing it economically is another matter, and the scientists continue work to optimize a process involving moderate heat and pressure. In the meantime, the engineers have begun working with entrepreneurs at Worldwide BioEnergy LLC, a Jefferson City, MO, group that will fabricate a mobile pilot plant that moves TCC out of the lab and into field tests.
Heading the project is Yuanhui Zhang, professor of agricultural and biological engineering at the University of Illinois (U of I). A native of China, Zhang earned a BS in agricultural engineering at Shandong Institute of Technology before moving to Canada’s University of Saskatchewan, where he completed post graduate and doctoral work in agricultural engineering. He served as an adjunct professor in Saskatchewan and as an engineering research scientist at Prairie Swine Center in Canada before joining the U of I faculty in 1996.
FE: Why focus on swine manure?
Zhang: Illinois is a land-grant institution, and swine is by far the biggest livestock base in the state. We’ve done limited experimentation with poultry and other waste, though not enough to determine if there is more economic value in those raw materials. We have focused on swine waste because it is material that is a net cost to farmers and agribusiness in the state, and we wanted to find a way to extract value from it.
When TCC first was proposed 40 years ago, researchers used coal, wood and other carbon sources as the biomass to be liquefied. Economically, it wasn’t practical. When converting animal waste and food waste into a useful product, it’s a different story.
FE: Anaerobic digesters and other technologies are commercially available. Why pursue conversion to biofuel?
Zhang: The advantages with oil are portability and storability. Liquefication is another form of TCC, which initially was developed to convert coal into liquid fuels. In liquefication, carbonaceous materials are converted through a complex sequence to decrease the level of oxygen and increase the hydrogen:carbon ratio.
FE: What are some of the benchmarks you have achieved in TCC development?
Zhang: In 2000, we proved the concept as a batch process in the lab, which was pivotal. In 2004, we successfully developed a continuous reactor, which is much more promising than batch and brought industry interest. Last year, we licensed TCC to industry, though we need to do a lot more research, both theoretical and practical, before it will be ready for commercialization. Manure has less hydrogen and more oxygen than other potential biomass feedstocks, which means suboptimal energy content. A reductive chemical reagent such as hydrogen or carbon dioxide is needed to increase the oil production rate.
Making the process work with reasonable reliability was the first major hurdle we faced. It’s one thing to convert swine manure to crude oil in the lab, but you need to come up with recipes that work well with a variety of biomass on a commercial scale. Some research groups who have experimented with similar materials have done so without any focus on how this process can work economically. If a recipe works, but not well, you can end up with a negative energy value.
FE: What are the general parameters of the process?
Zhang: In the lab, oil samples with heating value comparable to furnace oil were produced at temperatures of about 305
Zhang: Illinois is a land-grant institution, and swine is by far the biggest livestock base in the state. We’ve done limited experimentation with poultry and other waste, though not enough to determine if there is more economic value in those raw materials. We have focused on swine waste because it is material that is a net cost to farmers and agribusiness in the state, and we wanted to find a way to extract value from it.
When TCC first was proposed 40 years ago, researchers used coal, wood and other carbon sources as the biomass to be liquefied. Economically, it wasn’t practical. When converting animal waste and food waste into a useful product, it’s a different story.
FE: Anaerobic digesters and other technologies are commercially available. Why pursue conversion to biofuel?
Zhang: The advantages with oil are portability and storability. Liquefication is another form of TCC, which initially was developed to convert coal into liquid fuels. In liquefication, carbonaceous materials are converted through a complex sequence to decrease the level of oxygen and increase the hydrogen:carbon ratio.
FE: What are some of the benchmarks you have achieved in TCC development?
Zhang: In 2000, we proved the concept as a batch process in the lab, which was pivotal. In 2004, we successfully developed a continuous reactor, which is much more promising than batch and brought industry interest. Last year, we licensed TCC to industry, though we need to do a lot more research, both theoretical and practical, before it will be ready for commercialization. Manure has less hydrogen and more oxygen than other potential biomass feedstocks, which means suboptimal energy content. A reductive chemical reagent such as hydrogen or carbon dioxide is needed to increase the oil production rate.
Making the process work with reasonable reliability was the first major hurdle we faced. It’s one thing to convert swine manure to crude oil in the lab, but you need to come up with recipes that work well with a variety of biomass on a commercial scale. Some research groups who have experimented with similar materials have done so without any focus on how this process can work economically. If a recipe works, but not well, you can end up with a negative energy value.
FE: What are the general parameters of the process?
Zhang: In the lab, oil samples with heating value comparable to furnace oil were produced at temperatures of about 305