The fine-tuned line facilitates quick changeovers and improves efficiency.
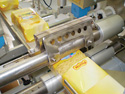
Pavan’s noodle production line automates the entire process-from mixing to final packaging. Source: Siemens.
Pavan Group, designer and manufacturer of automatic food processing equipment, built and installed an oriental noodles manufacturing line with a capacity of 1,500 kg (3,307 lbs) per hour for a major multinational customer.
The line produces dry, precooked noodles shaped in bundles having a single weight of 67.5 g (2.38 oz). The process includes mixing, lamination, cooking cutting, drying in cups, cooling and packaging of the finished product. The Pavan solution covers all processing stages, maintaining the sensorial characteristics of the handmade product. The packaging system has been customized according to client requirements; the square folded bundles are stacked and packed compactly in 400 g (14.1 oz) bags.
To meet customer needs, Pavan chose a Siemens motion control system based on the SINAMICS S120 modular drive. The drive can be used in standalone mode (ac/ac) for decentralized or single-axis applications, or in a book-size version (ac/dc) for centralized configurations where it is important to manage energy recovery from the motors.
Pavan was looking for a system that had a high degree of integration of automation hardware and software not only to optimize both programming and assembling time, but also to have a single platform to manage and maintain. The platform, Siemens’ TIA (Totally Integrated Automation), is based on drive, PLC and HMI platform integration with diagnostics capabilities at different levels: from the PLC software to communication network status, down to drive diagnosis and configuration.
With high production capacity, the error margins on the Pavan noodles pasta line were reduced to almost zero. The full line consists of various processing stations-each processing step must be synchronized with the others with absolute precision. Pavan chose Siemens 1FK7 servo motors connected via Drive-CLiQ to the SINAMICS S120.
The digital communication bus enables motor name plate self-reading and avoids assembly or replacement errors. Motors’ model and serial numbers can be automatically identified, preventing operator errors on site during production phase. With PLC control, product changeover times have been optimized, and production and line efficiency has increased. And with the more efficient design, plant floor space has been optimized.
The digital communication bus enables motor name plate self-reading and avoids assembly or replacement errors. Motors’ model and serial numbers can be automatically identified, preventing operator errors on site during production phase. With PLC control, product changeover times have been optimized, and production and line efficiency has increased. And with the more efficient design, plant floor space has been optimized.