Where technology meets technique
The connection between food companies and NASCAR usually only goes as deep as a decal on a car. A notable exception a few years ago was General Mills Inc.'s work with a Winston Cup pit crew to help improve line changeovers. The Minneapolis-based food company sent a team to work with a pit crew to gain insights into how they might improve changeover performance in their own plants.

The connection between food companies and NASCAR usually only goes as deep as a decal on a car. A notable exception a few years ago was General Mills Inc.'s work with a Winston Cup pit crew to help improve line changeovers.
The Minneapolis-based food company sent a team to work with a pit crew to gain insights into how they might improve changeover performance in their own plants. Many of the lessons mirrored tactics taught at manufacturing workshops that long have defined the changeover challenge-replacing standard bolts with bolts requiring only a quarter turn, for example, and stocking tool carts with replacement sprockets that can be quickly slid into place-but the cereal team also learned the value of technological tools, such as videotaping changeovers and then critiquing performance. The payoff was significant: at a Betty Crocker facility in Lodi, CA, line changeovers that had been taking up to 4.5 hours were reduced to 12 minutes, according to several news reports.
The NASCAR project boiled down to three lessons, recalls Rory Delaney, senior vice president of strategic technology at General Mills: queue theory, parallelism and the value of teamwork. It also underscored the importance of applying existing technology in creative ways to get a leg up on today's plant issues before they become tomorrow's problems. "If you're not working on a solution until it's needed," says Delaney, "you're three years late."
Technology and teamwork come together every time a changeover occurs on a processing or packaging line. Lean manufacturing and other continuous improvement strategies are great tools for sharpening the teamwork aspect of changeovers, but the technology part of the equation often gets pushed aside as just another capital expenditure.
"The way to do a good changeover project hasn't changed;" minimal use of tools, modular components that can be swapped out and other tactics are as valid today as they were 30 years ago, observes Jim Pfister, senior project manager with Sebesta Blomberg engineering. "What has changed is the availability of data-collection systems at your disposal." Proximity switches, photo eyes and other technology generate the data needed to improve changeover performance. The problem, he adds, is that unless they are part of a new line or new machine, the return on these investments comes too slowly to satisfy capital investment hurdle rates.
Data collection is a starting point in the changeover-improvement challenge. Analysis and solution-deployment follows. Another element is knowledge retention, and this may be the weakest link in current practice. Changeover authority John Henry uses the NASCAR analogy to promote "lean changeover," a program he likens to "a Kaizen event" for team building and in-house solutions to changeover. His two four-day workshops address the analysis and solution-deployment aspect, but if team members leave, the knowledge goes with them. Capturing and maintaining that knowledge is critical, and technology can help.
A simple checklist or flip chart suffices if plant workers have decades of on-the-job experience, acknowledges Brad Pepin of Sebesta Blomberg's Minneapolis office. Traditionally, long tenure was the rule in food and beverage, which made paper-based materials appropriate job-performance aids. As the workforce changes and new organizational systems are put into place, a checklist may no longer suffice.
"If a company uses high-performance work teams where people rotate to different jobs, gaining a lot of breadth but not a lot of depth, you might need to go beyond what to do and include how to do it and, by the way, here are some pictures to help you," says Pepin, who leads the engineering firm's Knowledge Solutions Group. Hand-held devices to deliver digital photos, movie files and even multilingual audio instructions have been incorporated into the "electronic performance support systems" his group creates for clients. "Something as pedestrian as a PDF file presented on a tablet PC could meet a client's needs," he says.
Clients in the Pentagon and at universities are more comfortable with the "wow factor" of technological tools such as PDAs and tablet PCs, Pepin allows. But food and beverage manufacturers also are dabbling in new media for changeover and other maintenance-improvement projects. In a presentation at Food Engineering's 2005 Food Automation and Manufacturing Conference, Kraft Foods scientist Dragan Filipovic provided a glimpse of the company's Visually Guided Servicing and Training (VGST) Project.
Successfully tested in a plant, VGST relies on belt-mounted 3.2 gigahertz computers to bring video clips, PowerPoint graphics and other materials to the plant floor so that changeover routines and maintenance procedures can be executed by technicians without prior experience with a machine. Text and visuals are viewed through miniature monitors mounted on customized goggles worn by the technicians. A camera also is mounted on the goggles to allow collaboration with a remote expert.
Operating equipment efficiency often drops to 40 percent or lower in the first hour after a changeover, Filipovic said, as adjustments are made to return OEE to the optimum rate. By displaying the precise machine settings for optimal performance, VGST offers the promise of high OEE from the outset, he suggested.

Multi-channel sensors are coming on stream to eliminate the need for resetting sensors when a product changeover occurs. "With conventional sensors, every time you have a new product coming down the line, you have to make adjustments," notes Robert Lee, sensor group marketing manager at Schaumburg, IL-based Omron Electronics. Retuning an array of sensors can be time consuming, and installing product-specific sensors adds cost and complexity. Omron began to address this issue two years ago with E3X-DA11TW-S, a sensor with a dual-channel output that can be programmed to detect two different objects. The corrosion-resistant fiber optic cable that links the sensor to its amplifier eliminates the need for multiple relays.
Dual channels are twice as useful as single-channel sensors but half as good as four. Omron leapfrogged that progression recently with the introduction of ZFV smart sensors, vision-based technology with eight memory banks and an icon-driven reprogramming feature. The sensors often are applied to date-code reading on dairy and beverage lines, where bottle rotation and high speeds can overwhelm traditional sensors. "It's a complicated version of a photo-electric sensor but with simplified programming requirements," says Lee.
Eight light emitting diodes are built into the sensor's fiber-optic head to illuminate a target up to 11 inches away. The emitter beam is reflected off the surface of the target and back to the charged couple device, then fed back to the amplifier and, finally, the receiver. Total response time is 4 milliseconds.
Code reading is only one of the sensor's possible uses. Lee recently oversaw the retrofit of a carton-former at a brewery to perform glue inspection of carton bottoms before beer was packed. "The equipment that was produced by the OEM did not accommodate this faculty, so we were called to solve the problem using a ZFV," he reports.
While sensors are adept at quality assurance and inspection functions, they do little to speed machine changeovers. That is the realm of electronics, and the advent of drives with both logic and motion control capabilities has signaled a sea change in packaging-line changeovers.
Flexibility trumps speed when a new case size or carton configuration is introduced, suggests Al Marin, account executive for food & packaging end-users at Bosch Rexroth, Hoffman Estates, IL. He cites the example of a soft-drink firm that selected a MeadWestvaco case packer capable of outputting 156 different carton configurations because of the "distributed intelligence" built into the machine's servo drive. "They were not scared away by the servo technology because the machine eliminated the headache of finding a plant in their network that could handle new cartons," says Marin. "They said, ‘We'll learn how to service the servos.'"
The cartoner is part of MeadWestvaco's Evotech line of machines. Atlanta-based Mead Westvaco has applied servo technology for 15 years, but the complete replacement of mechanical motion with electronic line shafting didn't occur until recently. "It would have been a monstrous problem to design a mechanical machine where cam action could be turned on and off, as needed," points out Gordon Thomsen, engineering project manager. Machines with a large number of servos can make on-the-fly adjustments with a push of a button on a HMI screen. Instead of loosening sprockets and moving assemblies to accommodate different pack sizes, the preprogrammed motors take care of the adjustment-"pretty much to the exact point you want to go," with tolerances well under 1 millimeter, adds Thomsen. By comparison, eyeballing machine settings on a mechanical system can result in long startup delays, he adds.
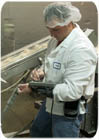
"We all think that returning to steady state is what we have to do, but that's not the case," says Strahm. "We have to make in-spec product, and that can be done before the process is all lined out."
Strahm and his partners, Gordon Huber and Rick Aberle, formerly worked at extruder-fabricator Wenger Manufacturing, where Huber helped develop the Phased Transition Analyzer (PTA), a tool for determining the temperature at which grain-based products reach a flowable state. Transition temperatures can vary by 20

A vision sensor projects red light on its target, in this case ink-jet marks on the neck of a milk bottle. With memory for eight different objects and push-button reprogramming, Omron's new ZFV smart digital CCD sensor helps minimize changeover time on packaging lines. Source: Omron Electronics.
The connection between food companies and NASCAR usually only goes as deep as a decal on a car. A notable exception a few years ago was General Mills Inc.'s work with a Winston Cup pit crew to help improve line changeovers.
The Minneapolis-based food company sent a team to work with a pit crew to gain insights into how they might improve changeover performance in their own plants. Many of the lessons mirrored tactics taught at manufacturing workshops that long have defined the changeover challenge-replacing standard bolts with bolts requiring only a quarter turn, for example, and stocking tool carts with replacement sprockets that can be quickly slid into place-but the cereal team also learned the value of technological tools, such as videotaping changeovers and then critiquing performance. The payoff was significant: at a Betty Crocker facility in Lodi, CA, line changeovers that had been taking up to 4.5 hours were reduced to 12 minutes, according to several news reports.
The NASCAR project boiled down to three lessons, recalls Rory Delaney, senior vice president of strategic technology at General Mills: queue theory, parallelism and the value of teamwork. It also underscored the importance of applying existing technology in creative ways to get a leg up on today's plant issues before they become tomorrow's problems. "If you're not working on a solution until it's needed," says Delaney, "you're three years late."
Technology and teamwork come together every time a changeover occurs on a processing or packaging line. Lean manufacturing and other continuous improvement strategies are great tools for sharpening the teamwork aspect of changeovers, but the technology part of the equation often gets pushed aside as just another capital expenditure.
"The way to do a good changeover project hasn't changed;" minimal use of tools, modular components that can be swapped out and other tactics are as valid today as they were 30 years ago, observes Jim Pfister, senior project manager with Sebesta Blomberg engineering. "What has changed is the availability of data-collection systems at your disposal." Proximity switches, photo eyes and other technology generate the data needed to improve changeover performance. The problem, he adds, is that unless they are part of a new line or new machine, the return on these investments comes too slowly to satisfy capital investment hurdle rates.
Data collection is a starting point in the changeover-improvement challenge. Analysis and solution-deployment follows. Another element is knowledge retention, and this may be the weakest link in current practice. Changeover authority John Henry uses the NASCAR analogy to promote "lean changeover," a program he likens to "a Kaizen event" for team building and in-house solutions to changeover. His two four-day workshops address the analysis and solution-deployment aspect, but if team members leave, the knowledge goes with them. Capturing and maintaining that knowledge is critical, and technology can help.
A simple checklist or flip chart suffices if plant workers have decades of on-the-job experience, acknowledges Brad Pepin of Sebesta Blomberg's Minneapolis office. Traditionally, long tenure was the rule in food and beverage, which made paper-based materials appropriate job-performance aids. As the workforce changes and new organizational systems are put into place, a checklist may no longer suffice.
"If a company uses high-performance work teams where people rotate to different jobs, gaining a lot of breadth but not a lot of depth, you might need to go beyond what to do and include how to do it and, by the way, here are some pictures to help you," says Pepin, who leads the engineering firm's Knowledge Solutions Group. Hand-held devices to deliver digital photos, movie files and even multilingual audio instructions have been incorporated into the "electronic performance support systems" his group creates for clients. "Something as pedestrian as a PDF file presented on a tablet PC could meet a client's needs," he says.
Clients in the Pentagon and at universities are more comfortable with the "wow factor" of technological tools such as PDAs and tablet PCs, Pepin allows. But food and beverage manufacturers also are dabbling in new media for changeover and other maintenance-improvement projects. In a presentation at Food Engineering's 2005 Food Automation and Manufacturing Conference, Kraft Foods scientist Dragan Filipovic provided a glimpse of the company's Visually Guided Servicing and Training (VGST) Project.
Successfully tested in a plant, VGST relies on belt-mounted 3.2 gigahertz computers to bring video clips, PowerPoint graphics and other materials to the plant floor so that changeover routines and maintenance procedures can be executed by technicians without prior experience with a machine. Text and visuals are viewed through miniature monitors mounted on customized goggles worn by the technicians. A camera also is mounted on the goggles to allow collaboration with a remote expert.
Operating equipment efficiency often drops to 40 percent or lower in the first hour after a changeover, Filipovic said, as adjustments are made to return OEE to the optimum rate. By displaying the precise machine settings for optimal performance, VGST offers the promise of high OEE from the outset, he suggested.

Rick Aberle (right) holds a through-transmission near-infrared (NIR) probe. He and Brad Strahm are considering ways to combine NIR data with data from the Phase Transition Analyzer on the left to monitor a range of chemical changes in food as temperature and pressure varies in an extruder, particularly after a changeover. Source: XIM Group.
Disruptive technology
One way to minimize the effects of changeover is to minimize the number of changeovers. Sensors are an example of field devices that are changing to accomplish this.Multi-channel sensors are coming on stream to eliminate the need for resetting sensors when a product changeover occurs. "With conventional sensors, every time you have a new product coming down the line, you have to make adjustments," notes Robert Lee, sensor group marketing manager at Schaumburg, IL-based Omron Electronics. Retuning an array of sensors can be time consuming, and installing product-specific sensors adds cost and complexity. Omron began to address this issue two years ago with E3X-DA11TW-S, a sensor with a dual-channel output that can be programmed to detect two different objects. The corrosion-resistant fiber optic cable that links the sensor to its amplifier eliminates the need for multiple relays.
Dual channels are twice as useful as single-channel sensors but half as good as four. Omron leapfrogged that progression recently with the introduction of ZFV smart sensors, vision-based technology with eight memory banks and an icon-driven reprogramming feature. The sensors often are applied to date-code reading on dairy and beverage lines, where bottle rotation and high speeds can overwhelm traditional sensors. "It's a complicated version of a photo-electric sensor but with simplified programming requirements," says Lee.
Eight light emitting diodes are built into the sensor's fiber-optic head to illuminate a target up to 11 inches away. The emitter beam is reflected off the surface of the target and back to the charged couple device, then fed back to the amplifier and, finally, the receiver. Total response time is 4 milliseconds.
Code reading is only one of the sensor's possible uses. Lee recently oversaw the retrofit of a carton-former at a brewery to perform glue inspection of carton bottoms before beer was packed. "The equipment that was produced by the OEM did not accommodate this faculty, so we were called to solve the problem using a ZFV," he reports.
While sensors are adept at quality assurance and inspection functions, they do little to speed machine changeovers. That is the realm of electronics, and the advent of drives with both logic and motion control capabilities has signaled a sea change in packaging-line changeovers.
Flexibility trumps speed when a new case size or carton configuration is introduced, suggests Al Marin, account executive for food & packaging end-users at Bosch Rexroth, Hoffman Estates, IL. He cites the example of a soft-drink firm that selected a MeadWestvaco case packer capable of outputting 156 different carton configurations because of the "distributed intelligence" built into the machine's servo drive. "They were not scared away by the servo technology because the machine eliminated the headache of finding a plant in their network that could handle new cartons," says Marin. "They said, ‘We'll learn how to service the servos.'"
The cartoner is part of MeadWestvaco's Evotech line of machines. Atlanta-based Mead Westvaco has applied servo technology for 15 years, but the complete replacement of mechanical motion with electronic line shafting didn't occur until recently. "It would have been a monstrous problem to design a mechanical machine where cam action could be turned on and off, as needed," points out Gordon Thomsen, engineering project manager. Machines with a large number of servos can make on-the-fly adjustments with a push of a button on a HMI screen. Instead of loosening sprockets and moving assemblies to accommodate different pack sizes, the preprogrammed motors take care of the adjustment-"pretty much to the exact point you want to go," with tolerances well under 1 millimeter, adds Thomsen. By comparison, eyeballing machine settings on a mechanical system can result in long startup delays, he adds.
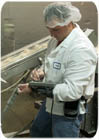
Rugged tablet PCs and other hand-held devices bring the tools of automation to the plant floor for changeover evaluation and other process improvements. Source: BOC Group.
Blocking and tackling
Instead of focusing on returning to a steady state after a changeover, processors should make in-spec production their priority, argues Engineer Brad Strahm, a principal in Sabetha, KS-based XIM Group. Rapid and frequent quality checks using technologies such as fluid particle analysis and near infrared measurement result in minimal changeover disruption."We all think that returning to steady state is what we have to do, but that's not the case," says Strahm. "We have to make in-spec product, and that can be done before the process is all lined out."
Strahm and his partners, Gordon Huber and Rick Aberle, formerly worked at extruder-fabricator Wenger Manufacturing, where Huber helped develop the Phased Transition Analyzer (PTA), a tool for determining the temperature at which grain-based products reach a flowable state. Transition temperatures can vary by 20
Looking for a reprint of this article?
From high-res PDFs to custom plaques, order your copy today!