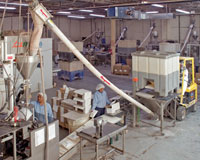
Forklift operator sets a tote atop an 8-cu.-ft. hopper from which a 15-ft. flexible screw conveyor transports blends to a packaging machine. Source: Flexicon.
World Flavors’ Packaging Manager Russ Perry recalls the days before the company installed its flexible screw conveyors. “Previously, we manually scooped material into the filling machine hoppers.” The company now runs eight 4-in. diameter, flexible 15-ft. screw conveyors. Produced by Flexicon Corporation, the conveyors consist of a polymer tube that encloses a flexible stainless steel screw driven by an electric motor. As it rotates, the screw propels material through the tube while providing sufficient clearance between the screw and the tube wall to eliminate or minimize product degradation. World Flavors standardized on the Model 1450 conveyor so spare parts would be a negligible issue.
Three of the conveyors run on lines dedicated to cappuccino mix, but during the holiday season, the company runs the cappuccino on six lines. The other conveyors run a variety of spice blends and individual spices (e.g., cinnamon and vanilla) throughout the year. World Flavors is diligent in preventing the separation of blended products (often comprised of disparate particle sizes and shapes) as they move from blending to packaging.
Following World Flavors’ formulas, workers combine ingredients, and then load each batch into one of seven blenders according to batch weight, typically 300 lb. (small), 1,400 lb. (medium) and 8,000 lb. (large). Uniform blends are discharged from blenders into rigid-plastic, 38-in.-square totes holding 1,600 lb. After passing quality control, workers move the totes to a holding area.
When a production run is readied on one of the eight packaging lines, a forklift operator sets a tote atop a flexible screw conveyor’s 38-in.-high, 8-cu.-ft. hopper. The operator opens the 10-in. slide gate at the bottom of the tote, and the material flows into the hopper. When the hopper is full, the operator activates the flexible screw conveyor, which conveys the material at a 45
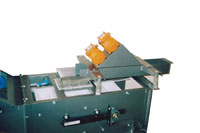
Boot-mounted rotary feeders
A new line of boot-mounted rotary feeders for retrofitting existing bucket conveyors and elevators from Gough Econ provides a controlled and consistent feed of bulk materials. The feeders can be retrofitted on all bucket conveyors from 9 to 48 inches in width. Powered by two vibratory motors mounted directly onto the load unit of existing bucket conveyors and elevators, the feeders are designed to transfer the product at a velocity consistent with bucket travel for gentle handling.Gough Econ; 800-264-6844; www.goughecon.com

Bag discharging system
With an automatic bag loop retractor and liner tensioner to provide complete material discharge from the bag without operator involvement, NBE’s Funnel Flow bag hanger changes the geometry of the bulk bag into a cone, eliminating dead spots where product can collect. The pneumatic massage paddles enhance material flow, pushing the product toward the discharge spout of the bulk bag. The E-3 traveling tube provides dust containment and product discharge from the bag. The Posi-Flo agitator paddles pull material toward the discharge, eliminating the potential for material bridging or rat holing above the conveyor inlet; and the Helicon flexible screw conveyor is a 16 ft.-long helical screw in a stainless steel tube.NBE; 616-399-2220;www.nbe-discharge.com

Vertical sanitary conveyor
Dorner’s AquaPruf LPZ Series vertical conveyor provides a high level of sanitation without product spillage on incline or decline applications. The sprocket-driven conveyor can be disassembled without tools for cleaning by one person. The machine uses a positive-driven Mol Industries USDA-approved TheromDrive solid urethane belt for smooth, consistent operation in wet, humid environments.Dorner Manufacturing;
800-397-8664; www.dorner.com
Dry depositor
The Hinds Bock dry ingredient depositor works in applications with dry, free-flowing products such as sugar, sprinkles, chocolate chips, oat flakes, sliced nuts, flour etc. The depositor can be mounted on existing equipment or new conveyors supplied by the company. Available with portable cantilevered frames, the machine’s construction is made of stainless steel, its speed is variable and its deposit is targeted. An operator interface stores multiple recipes for easy operator setup.Hinds-Bock Corp.; 877-292-5715; www.hinds-bock.com
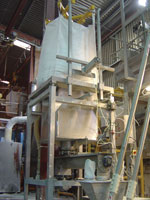
Loss-in-weight discharger
Spiroflow’s Type 3 loss-in-weight bag discharger provides controlled dispensing of powder material while keeping the bag safely above floor level. Dust and contamination free, the discharger accurately dispenses from 22 lb. to 3,300 lb. batches by using electronic load cells directly below the top bag holding frame, which assures that the bag and load cells are safely off the floor and out of the way of facility hazards such as forklifts.Spiroflow Systems; 704-291-9595; www.spiroflowsystems.com
Conveyors for small spaces
Constructed of 316L stainless steel, PIAB’s C2100-64 compact conveyor moves powders and bulk materials in spaces with very low ceilings or limited space. The hygienically designed conveyor features the company’s COAX multistage ejector technology, consuming less air and energy than other compressed-air-driven machines.PIAB; 800-321-7422;www.piab.com

Flexible sleeves
Nu-Con’s flexible sleeves connect spouting in offset, inline and oscillating equipment, and provide benefits not found in traditional worm-gear hose clamps. Advantages include ability to remove and replace flexible sleeves in seconds without tools, no risk of injury to people or damage to equipment from screwdrivers, crevice-free design that eliminates any chance of product build up, choice of straight or tapered sleeves, USDA-3A approvals and an airtight seal to eliminate dust. Each assembly consists of two SS adapters and one flexible sleeve.Nu-Con Equipment; 877-939-0510; www.nucon.com

Screen changer
The Russell Finex screen changer speeds changes on sieves, screeners and separators while reducing the risk of operator injury and mesh damage. It enables mesh screens to be changed quickly and safely by a single operator without manual lifting or additional tools. The changer can be used with most round separators from 48 to 60 inches in diameter from almost any manufacturer. It lifts up to four sieve, screener or separator decks at once with or without deblinding devices and allows the bottom screen to be changed without disassembling the decks above it.Russell Finex, Inc.; 704-588-9808;www.russellfinex.com

High-speed feeders
High-speed (HS) and high-deflection (HD) vibratory cross feeders and conveyors from Eriez distribute product directly into vertical, fill and seal (VFS) or weigh scale equipment using peripheral discharge trays capable of delivering from 100 to 1,000 cu. ft. of material per hour. Both HS and HD feeders feature low-energy AC electromagnetic drives to provide reliability and precise cycling.Eriez; 800-300-3743; www.eriez.com
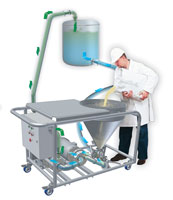
Mixing powders into liquids
Providing consistent powder delivery, Admix’s Fastfeed powder induction system works in applications with high viscosity and solids levels, reducing plugging and fouling. The product offers the benefits of an inline, skid-mounted dispersion system that feeds powders and disperses them instantly, delivering powder inline at controlled feed rates from 3 to 200 pounds per minute. Further processors can add dry ingredients to mix vessels in a more ergonomic fashion, drastically reducing operator injuries.Admix; 800-466-2369; www.admix.com
Mixing and dispersing
With the ability to mix and disperse in a single operation, Powder Technologies’ Ystral Dispermix head works according to the principle of a rotator-stator system and provides 100% homogeneous mixing and simultaneous dispersing. The unit offers short processing times, high rationalization potential and fast deagglomeration.Powder Technologies, Inc.; 609-914-0521;
www.powdertechusa.com
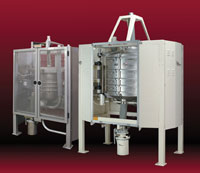
Inline sifters
Great Western Manufacturing’s Tru-Balance inline sifters can be directly inserted into a vacuum or pressure pneumatic conveying line as a quality assurance tool for removing a small amount of oversized impurities from the product. The sifters eliminate the need for equipment such as cyclone receivers, airlocks, receiving hoppers and blowers, which would be required if a standard atmospheric pressure sifter were used. Potential applications include scalping, grading and fines removal from dry, free-flowing powders and granular materials.Great Western Manufacturing; 913-682-2291; www.gwmfg.com

Bulk bag discharger
The Material Master bulk bag discharging system from MTS includes a bag break station and screw conveyor. A Sure-Seal pneumatic clamp system ensures dust-tight operation while a Flo-Master massaging system ensures positive material flow.Material Transfer; 800-836-7068; www.materialtransfer.com
Blending system
The IBC column blender from IEDCO is designed to receive, lock, lift and blend multiple bulk ingredients in an intermediate bulk container (IBC), which allows a homogeneous blend without segregation and cross-contamination. The blender eliminates the need to transfer material to and from other machines.IEDCO; 856-728-6400; www.iedco.com