Lean builds steam
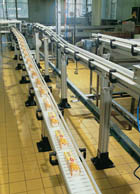
A 15-year recession cooled enthusiasm for adopting Japanese methods. How good could they be, after all, when employment for life gave way to an economy where more than half of adults under 35 have never held a steady, full-time job?
Rejection of all things Japanese means ignoring the stunning manufacturing success of Toyota Motor Corp. The Toyota Production System is the leading example of lean manufacturing, and as Toyota took ever-larger bites out of Detroit's lunch, US automakers and the manufacturers who supply them have scrambled to adopt lean. In the process, the language of industrial engineering has acquired a Japanese accent, with principles of efficiency such as continuous improvement (kaizen), elimination of waste (muda) and visible records of production flow (kanbans) being expressed with new terms. Lean also demands a partnership between supervisors and line workers because, unlike Six Sigma and other systems built around the expertise of a chosen few, lean leverages the knowledge of everyone in the organization to eliminate processes and procedures that do not add value. The top-down team participation is one of the most difficult principles to graft onto Western organizations.
"Two out of three companies that attempt lean manufacturing fail the first time out because they don't have an understanding at the executive level, and they don't approach it as an enterprise-wide initiative," suggests Dennis Staman, director of industrial services in the Atlanta office of CH2M Hill (formerly Lockwood Greene). "It's much broader than a manufacturing initiative; it's enterprise wide." Without management involvement, lean initiatives peter out after a few early successes.
While a third of US manufacturers say they have applied lean principles, fewer than one in 20 plants actually run lean. Changing an existing plant culture is difficult, which is why many manufacturers jump at the chance to go lean when a new facility is built. For example, Glanbia Foods Inc. launched a lean initiative at the $192 million Southwest Cheese Co. project it will manage in Clovis, NM, before the plant opened.
New facilities are the exception in food and beverage processing, though, and there are other barriers to lean in this industry. "Lean doesn't look as applicable in the food environment as it does in other industries," allows Andy Carlino, a partner in Novi, MI-based Lean Learning Center, "but the information flow, the commitment between maintenance and the operators and between quality assurance and processing that it engenders is the glue that holds lean together."
Food manufacturers are not dealing with the intense foreign competition that automakers are, though switching to lean while in crisis mode is not the best situation. Food professionals are put off by some of the tools of lean, such as the 5-S system. Two of the points-shine and inspect and sort through and sort out-sound suspiciously like basic sanitation. "If things aren't organized and clean in a food plant, you're already in trouble," points out Carlino. Lean is geared toward everyday processes, not problems that threaten a plant's viability.
Some principles of lean have to be tweaked or scrapped if lean is to be relevant, he adds. For example, assembly operations are advised to design U-shaped work cells that can be moved around the plant as needed, but that's not transferable to a food plant. Similarly, lean disciples label production in advance of orders as waste, but a dairy must process milk when the cows produce it, not when customers place their orders.
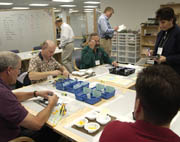
Hello muda, hello fada
Land O' Lakes, Wm. Wrigley Co. and Wise Foods are among the food companies to send top executives, plant managers and line operators to Carlino's center for five-day total emersion in the rules, tools and philosophy of lean. "The ability to identify and eliminate the daily problems in a process is a basis of lean," Carlino says. "Without training, management by walking around is just industrial tourism."
Last summer's workshops drew a contingent from Glanbia's four brownfield plants in Idaho. Although some of those facilities have operated for three decades, the first few kaizen events are breaking down resistance to lean. "Whereas Southwest Cheese doesn't have a baseline to measure against, we can immediately show tangible benefits," points out Steve Christiansen, Glanbia's corporate training and development manager. "I want to get an ROI on lean."
An early success involves changeovers from whey protein to whey lactose filtration, a process that can take up to 20 hours to complete. Changeovers also generate waste: 18 to 25 bags weighing 55 lbs. each had to be scrapped as animal feed each time because they did not meet purity specifications. CIP procedures and changeover processes were studied and discussed, and incremental changes such as a new valve to speed the process were incorporated. Waste was lowered to eight bags, then three for each changeover. "That got people's attention," recalls Christiansen.
Out-of-stocks on safety glass and other must-have items was another kaizen target at one facility. Now the plant is never out. "That got maintenance people at the other plants to say, ‘We want that,'" he says.
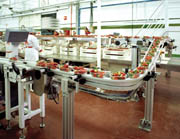
The two-year lean development timeframe applies particularly to supply-chain efficiencies and other changes beyond the four walls of the factory. By that yardstick, Siloam Springs, AR-based Simmons Foods Inc. is on the brink of cashing in on lean. The poultry processor began plotting its war on waste three years ago, when Seth Kaufman was director of training. When he became director of poultry management accounts two years ago, Kaufman began dispatching personnel to the Lean Learning Center for indoctrination. By year's end, all salaried workers will have gone through the center's week-long indoctrination. "It may be a little over-ambitious, but our goal at the operator level also is 100 percent training," says Kaufman. The company has 4,200 workers at six plants.
Kaufman recently led a two-day kaizen involving personnel from human resources and information services to identify ways to improve new-employee hiring and training processes. "We've had good success with lean, but it's only in the last few months that thought processes have begun to change," he says.
Lean increasingly is applied to human resources and other front-office functions. General Mills' frozen food plant in Wellston, OH, worked with consultants at TechSolve to resolve employee turnover issues. Greater job satisfaction is a residual benefit of lean, so using the tools to address retention is apt. The process led to a mentoring program and other changes that helped reduce turnover five percent, resulting in $275,000 in direct and indirect savings.
TechSolve was founded as the Institute of Advanced Manufacturing Sciences in 1982, when Japan, not China, was seen as the greatest threat to America's manufacturing base. State and local government funded the institute to help ensure the survival of Ohio's machine shops, and the application of best practices quickly spread to other manufacturing sectors.
"Food and beverage production doesn't include a lot of extraneous activities; it's by definition lean," notes Fred Fishman, manager of the strategic procurement program at TechSolve. "But a food company can be very inefficient in other areas," particularly distribution.
A criticism of lean is that the emphasis on continuous improvement and the likelihood some jobs will be eliminated can sharply increase stress levels, particularly at the operator level. Simmons management vowed at the outset, "we'll eliminate positions, we won't eliminate people," Kaufman reports. "In our case, there is creative tension, but we're seeing good success and good responses because everyone wants a chance to participate in making work easier, safer and better."
Strange bedfellows
In its purest form, lean has an almost anti-automation bias that traces to Toyota's origins as a textile manufacturer. "Creativity before capital" is a guiding principle, and equipment spending is subject to show-me skepticism. "Toyota had perfected almost-lean manufacturing systems in weaving and redeployed those systems into automotive" when the Japanese government pressed Toyota into vehicle manufacture during World War II, according to Kevin Gingerich, a director in Bosch Rexroth Corp.'s linear motion and assembly technologies group in Buchanan, MI. "A human being is more flexible than a massive piece of machinery," particularly from a 1940s perspective. Lean traditionalists still flinch at the use of automation. That would suggest an arms-length relationship between automation suppliers and lean. In fact, the opposite is true: most automation specialists are themselves practitioners of lean.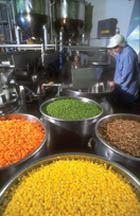
When the Twinsburg project concluded, some automation equipment had been removed-not because it didn't work but because it didn't add value. Quality inspections that no longer were needed represented inefficiencies to be eliminated.
"There was lots of automation for its own sake in the early ‘80s, and because of the way it was applied, people didn't get the benefit that they should have," he adds. The same is true today when manufacturers implement manufacturing execution systems (MES) before they have laid the lean groundwork.
Although he sells MES solutions, John Cavalenes of Citect Inc. heartily agrees. "A lot of companies want to implement MES, but if they don't have a lean culture in place to implement it, how will they recoup this six-figure investment?" he asks. "Technology can be a great tool in helping companies eliminate non-value-added activities, but first there has to be a high value placed on labor."
Some organizations reject lean and opt for alternatives such as Theory of Constraints (TOC) production planning, a framework that has been called the zen of manufacturing. Oregon Freeze Dry (OFD), Albany, OR, used TOC a few years ago to optimize throughput in the dryers at its three US plants. "Lean might give you a 5 percent reduction in inventory; TOC can double throughput with little or no additional staffing," insists Alan Huster, OFD's process engineering manager. "Before we implemented TOC, I would have believed there is a limit to what you can push through your plant with the equipment you have. I don't believe that today. Even if you're running 24/7, you are not at the limit: something within the freeze dryer is constraining you."
Contract manufacturing is OFD's growth engine, and last year Huster applied TOC-based project management software called Concerto to identify and resolve choke points in new-product development. "We could have patted ourselves on the back when completed projects increased to 98 from about 75, but we sensed that we had reached a plateau and could still grow," he says. Completed projects immediately spiked to 149, and this year Huster expects to complete 171.
Lean proponents don't see an either-or choice with TOC and other approaches. Whether a company pursues TQM, Six Sigma, lean or borrows a little from each, the key is developing a disciplined approach that works within the organization, Citect's Cavalenes says. World-class manufacturing is a big enough tent to accommodate multiple methodologies. "Six Sigma is a fantastic problem-solving tool, but few problems rise to the level of analysis that Six Sigma is geared to resolve," adds Glanbia's Christiansen. Let the resident black belts or TOC disciples deal with those issues. For organizations interested in involving all their workers in continuous improvement, lean may be indispensable.
For more information:
Kevin Gingerich, Bosch Rexroth Corp.,
269-697-5295,
kevin.gingerich@boschrexroth-us.com
Dennis Stamen, CH2M Hill,
770-849-1886
John Cavalenes, Citect Inc.,
630-621-4860,
johncavalenes@citect.com
Andy Carlino, Lean Learning Center,
248-478-1480
Ted Wodoslawski, Rockwell Automation,
440-646-3501
Fred Fishman, TechSolve,
513-948-4423
Looking for a reprint of this article?
From high-res PDFs to custom plaques, order your copy today!