Field Reports: Making time
With entrepreneurial beginnings as a Swiss cheese maker dating back 60 years, Berner Foods now employs 200 workers and has sales of more than $75 million through a business that provides the US with a variety of processed cheeses and snack dips, manufactured at its state-of-the-art facilities in Dakota, IL.
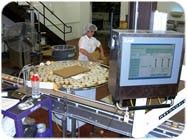
Increased demand and plans for innovative new product launches meant Berner was faced with an increasingly complex SKU mix. The company, which has an ambitious five-year growth plan, wanted to improve throughput efficiencies and reduce performance variances, cut changeover times, unplanned downtime and minor stoppages, as well as reduce re-work and waste. However, with no efficient or reliable system for collecting data, the company was unable to identify specific areas for performance opportunities.
"Our manual systems meant supervisors had to spend time collecting data and managing paperwork when they could have been interpreting and acting on the information instead," says Berner Foods' President Steve Kneubuel. Inevitably that led to a plateau in our performance improvement."
In addition, the increased demand for product was pushing Berner Foods to the point of capacity. Officials decided it was time to find a real-time performance management (RPM) system that would exploit opportunities for improved efficiency through improved rate, yield and utilization.
After an extensive evaluation of system suppliers, the company selected the eventsengine RPM solution from Miami, FL-based mvi technology. Berner, which packs its product in cups, bowls and aerosol containers, is installing the system on all six of its production lines.
Berner's Business IT Director Troy Grove led the evaluation. "We considered it to be the most robust solution and the one that offered the least risk," Grove says. "mvi also had a very methodical implementation model, which not only educated and trained the workforce, but got the ‘buy-in' of everybody involved.
The eventsengine system allows performance data (including information on operator behavior) captured at the plant floor level to be instantly visible via a KPI dashboard, alerting the operators to take any necessary remedial action, as well as feeding back real-time measurements against performance targets. It allows users to adopt a visual management approach because the information is accessible via a web browser elsewhere in the company and is role based to ensure information is deployed in the right manner to the right people at the right time. From a strategic perspective, the information is modeled in a way that enables organizations to identify specific opportunities for improvement through ‘slice-and-dice' and ‘what-if' analysis on a continuous basis.
Kneubuel believes the system will deliver significant benefits, not only in the additional capacity it will generate, but through improvements in gross margin, on-time delivery and more competitive pricing, driving further sales. "We've already identified the potential for a 20 percent improvement in efficiency in the first year, which is equivalent to four million extra jars of product," Kneubuel says. What's more, with eventsengine, the changes are sustainable. We see it facilitating a change in our company culture and it is already contributing positively to the morale and motivation of the workforce."
For more information:
Mark Sutcliffe, mvi technology; 786-235-0682; enquiries@mvitechnology.com
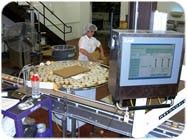
Berner Foods' new real-time management system captures performance data at the plant floor level and makes it visible on a KPI dashboard, alerting operators to make changes as necessary. Source: mvi technology.
Increased demand and plans for innovative new product launches meant Berner was faced with an increasingly complex SKU mix. The company, which has an ambitious five-year growth plan, wanted to improve throughput efficiencies and reduce performance variances, cut changeover times, unplanned downtime and minor stoppages, as well as reduce re-work and waste. However, with no efficient or reliable system for collecting data, the company was unable to identify specific areas for performance opportunities.
"Our manual systems meant supervisors had to spend time collecting data and managing paperwork when they could have been interpreting and acting on the information instead," says Berner Foods' President Steve Kneubuel. Inevitably that led to a plateau in our performance improvement."
In addition, the increased demand for product was pushing Berner Foods to the point of capacity. Officials decided it was time to find a real-time performance management (RPM) system that would exploit opportunities for improved efficiency through improved rate, yield and utilization.
After an extensive evaluation of system suppliers, the company selected the eventsengine RPM solution from Miami, FL-based mvi technology. Berner, which packs its product in cups, bowls and aerosol containers, is installing the system on all six of its production lines.
Berner's Business IT Director Troy Grove led the evaluation. "We considered it to be the most robust solution and the one that offered the least risk," Grove says. "mvi also had a very methodical implementation model, which not only educated and trained the workforce, but got the ‘buy-in' of everybody involved.
The eventsengine system allows performance data (including information on operator behavior) captured at the plant floor level to be instantly visible via a KPI dashboard, alerting the operators to take any necessary remedial action, as well as feeding back real-time measurements against performance targets. It allows users to adopt a visual management approach because the information is accessible via a web browser elsewhere in the company and is role based to ensure information is deployed in the right manner to the right people at the right time. From a strategic perspective, the information is modeled in a way that enables organizations to identify specific opportunities for improvement through ‘slice-and-dice' and ‘what-if' analysis on a continuous basis.
Kneubuel believes the system will deliver significant benefits, not only in the additional capacity it will generate, but through improvements in gross margin, on-time delivery and more competitive pricing, driving further sales. "We've already identified the potential for a 20 percent improvement in efficiency in the first year, which is equivalent to four million extra jars of product," Kneubuel says. What's more, with eventsengine, the changes are sustainable. We see it facilitating a change in our company culture and it is already contributing positively to the morale and motivation of the workforce."
For more information:
Mark Sutcliffe, mvi technology; 786-235-0682; enquiries@mvitechnology.com
Links
Looking for a reprint of this article?
From high-res PDFs to custom plaques, order your copy today!