Machinery integration accelerates condiment production
Servo-driven case packer not only speeds packaging, it also improves quality and overall productivity.
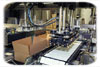
Mullins Food Products develops, manufactures and packages the condiments found in many leading fast food restaurants. The company produces a large volume of packets, so any speed improvement in the packaging line can lead to noticeable results.
One area needing improvement was the method for packing dipping sauce into larger cases for shipping, because this end-of-line process largely determines the overall speed of the line.
To better meet its customers’ demands for one-ounce cup products, Mullins commissioned a new case packing machine capable of quickly picking and placing the cups in cases for distribution. It purchased a high-speed three-axis case packer made by Soleri Design/Automation Inc. equipped with a high-performance servo system from the Bosch Rexroth Corporation Electric Drives and Controls group.
Designed to accelerate speed across the entire production line, the Soleri case packer and corresponding Rexroth components integrated with an upstream, previously installed cup-filling machine from Winpak. With this integration, Mullins significantly accelerated the overall speed of its cup line.
“In an industry governed by speed, the Soleri machine immediately produced a sizeable increase in cycle speed,” says Mullins Maintenance Manager Larry Coons.
When the filled one-ounce cups travel down the production line toward the packaging area, 50 containers are picked up with a suction head, oriented and placed into the case. A separate pick head places a cardboard slip sheet between each layer of cups to add strength and ensure the cups are not damaged during shipment. There are five layers, providing a total of 250 cups per case.
The machine is driven by Rexroth IndraDrive digital servo drives and MSK servo motors. The drives provide distributed intelligence to close all the loops in the drive, freeing up the controller to calculate and execute the pick-and-place path planning.
A key component of the system is the Rexroth PPC-R controller, a motion and logic controller that resides upstream on the Winpak cup-making machine. This system synchronizes all of the servo motions. It controls both the Winpak cup machine and the Soleri case packer. As a result, the speed of each machine directly corresponds with the tempo of the other one.
“In terms of calculating production, we are ultimately measured by cycles per minute, and with this case packer, our throughput times have accelerated nicely,” says Coons. “Prior to the install of the Soleri machine, we maxed out at around 58 to 60 cycles per minute. We’re now running at least 70 cycles per minute-about 17 percent faster production.”
Coons says package and product waste have improved also. With the servo system, the machine is designed to move slightly slower while the cups are en route to the box, but faster on the return to pick up more cups. This overall, controlled action reduces the potential for lost or damaged products, a number which Coons says has dropped by nearly 10 percent.
For more information:
Dan Throne, 847-645-3600, info@boschrexroth-us.com.
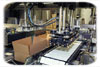
This interior view of the Soleri packaging machine shows the lifting of 50 filled cups (right of carton) and the picking and placing of the slip sheet (left of carton) as they are alternately placed in the carton. The machine integrates with an upstream Winpak filler via a Rexroth controller. Source: Bosch Rexroth.
Mullins Food Products develops, manufactures and packages the condiments found in many leading fast food restaurants. The company produces a large volume of packets, so any speed improvement in the packaging line can lead to noticeable results.
One area needing improvement was the method for packing dipping sauce into larger cases for shipping, because this end-of-line process largely determines the overall speed of the line.
To better meet its customers’ demands for one-ounce cup products, Mullins commissioned a new case packing machine capable of quickly picking and placing the cups in cases for distribution. It purchased a high-speed three-axis case packer made by Soleri Design/Automation Inc. equipped with a high-performance servo system from the Bosch Rexroth Corporation Electric Drives and Controls group.
Designed to accelerate speed across the entire production line, the Soleri case packer and corresponding Rexroth components integrated with an upstream, previously installed cup-filling machine from Winpak. With this integration, Mullins significantly accelerated the overall speed of its cup line.
“In an industry governed by speed, the Soleri machine immediately produced a sizeable increase in cycle speed,” says Mullins Maintenance Manager Larry Coons.
When the filled one-ounce cups travel down the production line toward the packaging area, 50 containers are picked up with a suction head, oriented and placed into the case. A separate pick head places a cardboard slip sheet between each layer of cups to add strength and ensure the cups are not damaged during shipment. There are five layers, providing a total of 250 cups per case.
The machine is driven by Rexroth IndraDrive digital servo drives and MSK servo motors. The drives provide distributed intelligence to close all the loops in the drive, freeing up the controller to calculate and execute the pick-and-place path planning.
A key component of the system is the Rexroth PPC-R controller, a motion and logic controller that resides upstream on the Winpak cup-making machine. This system synchronizes all of the servo motions. It controls both the Winpak cup machine and the Soleri case packer. As a result, the speed of each machine directly corresponds with the tempo of the other one.
“In terms of calculating production, we are ultimately measured by cycles per minute, and with this case packer, our throughput times have accelerated nicely,” says Coons. “Prior to the install of the Soleri machine, we maxed out at around 58 to 60 cycles per minute. We’re now running at least 70 cycles per minute-about 17 percent faster production.”
Coons says package and product waste have improved also. With the servo system, the machine is designed to move slightly slower while the cups are en route to the box, but faster on the return to pick up more cups. This overall, controlled action reduces the potential for lost or damaged products, a number which Coons says has dropped by nearly 10 percent.
For more information:
Dan Throne, 847-645-3600, info@boschrexroth-us.com.
Looking for a reprint of this article?
From high-res PDFs to custom plaques, order your copy today!