Possible changes in GMPs are just background noise for food professionals focused on manufacturing.

As agribusiness heads into the fall harvest, the state of food manufacturing might best be described as "in flux." This year's Food Engineering State of Food Manufacturing study presents the observations of plant professionals who are dealing with an increased emphasis on automation, shifting staffing levels and other production challenges. While they wrestle with those priorities, however, change may be afoot in plant-operation fundamentals.
In July and August, a U.S. Food and Drug Administration panel conducted public meetings on possible changes to the Good Manufacturing Practices (GMPs) specified in 21 CFR Part 110, the federal code affecting food processors. Noting that GMPs have not been revised since 1986 and do not reflect contemporary understanding of food-safety threats, acting FDA commissioner Lester M. Crawford hopes to draft a list of possible changes before the end of the year. A 60-day comment period would follow, and a final guidance could codify GMP revisions in early 2005.
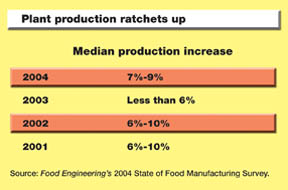
"Since food GMPs are an integral part of the nation's control over food safety problems, it is essential that they adequately address the needs of today's food processes and food borne hazards," Crawford said in a prepared statement. Likening the effort to a similar overhaul of medical-product GMPs, he said the effort "will improve the safety of these products and create new opportunities for introducing better manufacturing techniques."
Ironically, the GMP initiative comes at a time when food safety is slipping as a priority in food manufacturing (see chart above). While food safety is and will remain a core concern, other issues are becoming more dominant, FE's annual State of Food Manufacturing study suggests. The push to increase automation and reduce headcounts in particular is dominating the priority lists of processing professionals.
FDA is framing the GMP discussion around 11 questions, including the need for additional controls for chemical, physical and biological hazards and steps to prevent undeclared allergens in food. The possibility of different preventive controls for plants of varying sizes and processes for different types of food also is raised. But the key change, according to industry trade representatives, concerns documentation of employee training, sanitation procedures, validation of control measures, raw material testing and other programs and procedures for which no written log currently is required.
"The records aspect is what is missing in the current GMPs," according to Jenny Scott, senior director of food safety program for the National Food Processors Association. How the matter plays out-and how quickly-is the great unknown, she says. "It's early in the game, or maybe it's late."

A boost in budgets
While the GMP issue plays out in Washington, DC, plant managers and engineers are contending with matters such as plant security, supply chain integration and structural changes within their organizations and their impact on throughput. On a positive note, budgeted spending for plant equipment, upgrades and automation is the strongest it has been in years, according to respondents to the State of Food Manufacturing survey.
Asked to compare their 2004 budgets for production, packaging and process control equipment with the previous year, 37 percent of respondents indicated spending plans were up by an average of 23 percent (see chart on page 60). Only 11 percent of the sample has fewer dollars this year than last. The net effect is the strongest budgetary environment in years.
The same pattern holds for plant improvement and upgrade spending this year: 38 percent have an average of 28 percent more dollars to invest in 2004, while 11 percent have 25 percent less for facility improvements than in 2003.

The most bullish budgeting is occurring for automation systems and control hardware and software. Only 9 percent of plants are coping with tighter budgets, and the cuts are half the levels experienced three years ago. Fully one-third of respondents have more dollars to spend, and budgets are up 22 percent, the biggest boost in years.
Maintenance-related automation is also getting a lift: 28 percent report increased spending, compared to 24 percent last year. Only 8 percent will spend less, down from 10 percent in 2003.
More automation means machines are replacing humans, and that cause and effect is reflected in the structural changes occurring at respondents' companies. One in five say manufacturing staffs have been downsized in the last year, double the proportion three years ago. Similarly, 15 percent downsized their engineering staffs, versus 9 percent in 2001.
For every action, there is an opposite reaction, though not necessarily equal: 19 percent report their companies added manufacturing staff members, a modest number compared to 2001, when 29 percent beefed up their workforces. Eleven percent hired engineers, the strongest hiring trend since 2001, when 14 percent boosted in-house engineering talent.
The outsourcing trend in food and beverage is getting stronger. In 2001, nine percent of respondents indicated more work was outsourced. The figure grew to 13 percent last year, and 17 percent reported more outsourcing in this year's survey. Asked where outsourcing has increased most dramatically during their food industry careers, 62 percent of respondents cited the movement of engineering projects out of house (caveat: two-fifths of respondents are engineers). Copacking was mentioned by one-third of respondents, followed by sanitation services (32%) and maintenance (26%). Shifting manufacturing offshore was cited by 12 percent, almost twice the frequency of offshore sourcing of engineering (7%).
The most frequently cited organizational change was plant expansion or added capacity (47%). Manufacturing consolidation drives much of that. Consolidating activity into fewer locations was a challenge faced by 60 percent of respondents whose companies had undergone a merger or acquisition. That's a significantly higher proportion than those who cited it as a M&A challenge in recent years. In many cases, the merged entity is little more than the sum of its parts. While plant-specific production increases are consistent with previous year's surveys-22 percent expect to increase output 10 percent or more as they pick up slack from shuttered facilities-company-wide increases are at their most modest levels in the 21st Century. Almost half (46%) anticipate corporate increases of only one to six percent. A quarter or fewer respondents in the last three years pegged company-wide increases at similarly modest levels.
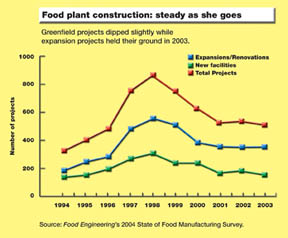
Tools for improvement
After talking about supply chain integration for years, processors are getting off the fence and doing something about it. Half of all respondents in 2002 and 2003 indicated their companies were doing little or nothing about supply-chain efficiencies. This year, only one-third are still sitting on the sidelines.
Questionnaires listed five specific integration activities, from EDI order-capture and invoicing to web portals for customers and suppliers. In all cases, respondents reported higher levels of activity. Additionally, 22 percent indicated that their companies had RFID-tag initiatives underway.

Plant security is another industry hot button. Almost two-thirds of readers say they have instituted tighter controls for raw materials and incoming supplies, up from 57 percent last year. Tighter screening of plant personnel was administered by 61 percent, the same level as last year. The most popular security initiatives were tighter building and perimeter control (79%) and stricter enforcement of existing security procedures (75%).
Programmable logic controllers remain the number one item on plant professionals' automation shopping lists, and the PLC's popularity appears to be growing: 85 percent will purchase PLCs this year, compared to 69 percent in 2003, 79 percent in 2002 and 64 percent in 2001. Human-machine interfaces and sanitation/CIP systems were the next most-frequently mentioned automation items, both at 29 percent.
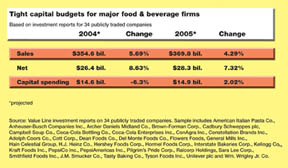
Computerization is not a productivity panacea, however. People skills also are critical, and awareness of the need for better skills training is growing. Better training of line operators topped the list of actions needed to boost plant productivity, with one-third indicating that there is a great need for improvement in this area. Better skills training of line supervisors is not far behind, with 28 percent saying there is great need. Only one in 10 regarded training as a low priority.
Improved communication between marketing and production slipped to the third highest productivity priority, though the ratio of respondents (27%) saying there was great need for improvement was consistent with past surveys. In fact, a growing number of respondents is recognizing the need for better communications throughout the organization, including between manufacturing areas and between engineering and IT.
Despite generally favorable trends in capital spending for 2004, the study suggests some belt-tightening at food and beverage plants. Readers indicated the portion of their facility budgets allocated for equipment purchases will average 16 percent this year, down from 19 percent in 2003. The comparable 2002 figure was 15 percent and in 2001 it was 18 percent.

At the time Food Engineering readers were completing their State of Manufacturing surveys, the Institute of Supply Management (ISM) was issuing revised projections of capital spending by U.S. manufacturers for 2004. ISM's survey of purchasing and supply executives suggests capital expenditures will increase 6 percent, up sharply from a 2.7 percent gain in 2003 and considerably more robust than the 3.2 percent increase forecasted in a similar survey in December. The survey also found that 10 industrial sectors, including food, were operating at more than 85 percent capacity.
Among 34 publicly traded food and beverage companies, capital spending forecasts for 2004 are less optimistic (see chart on page 58). Based on Value Line analyst reports in May, capital outlays at those corporations are expected to decline 6.3 percent this year, despite strong overall growth in gross sales and net profits. However, spending cutbacks at a handful of firms skew the numbers. If those companies are factored out, capital outlays are essentially flat for the group.
For example, Cadbury Schweppes reported record capital spending in 2003 and expects to slash outlays almost in half this year. The company purchased gum maker Adam's confectionery last year and plans to rationalize the purchase by shuttering 26 plants worldwide and laying off 5,500 workers. Anheuser-Busch also experienced unexpectedly large capital outlays in 2003 and now is bringing spending closer to historical patterns.
Another wild card is the Atkins diet. Baked goods and grain-based foods have suffered declining sales because of carb-conscious consumers, and those manufacturers are mothballing plants and slashing production accordingly. If those companies are taken out of the sample, capital spending actually increases 3.25 percent.
Between shifting consumer preferences, more outsourcing and continued pressure to deliver the safest food possible, processing professionals have their hands full. "It used to be production at any cost," one respondent writes. "Now corporate is driving safe production, and all of our production numbers are going up." The only hope for meeting those numbers lies in automation. "New equipment and technology automation will increase productivity and decrease manual labor," another reader observes. That's the game plan, anyway. Now it's manufacturing's challenge to execute it.
Who answered the survey?
This year's State of Food Manufacturing Study is based on 400 usable questionnaires completed by Food Engineering readers. Questionnaires were mailed to 4,000 readers in April, with an additional 5,800 subscribers receiving e-mail messages asking them to complete the survey on the Food Engineering website (www.foodengineeringmag.com). Response rate for mailed surveys was eight percent and two percent for those surveys completed via the web.
Two-fifths (39%) of respondents are involved in engineering, with operations management (23%) and production management (12%) representing the next most-frequent job functions. The remaining sample is distributed between general administrative management, R&D, quality control, packaging, purchasing and other duties.
Meat production was the focus of 26 percent, followed by bakery (21%), beverage (19%), dairy (15%) and flavors and ingredients (15%).
One-third work at facilities with 100 to 249 employees, with another 28 percent at plants with 250 to 499 workers. Almost equal numbers worked at plants with fewer than 50 or more than 2,500 employees.