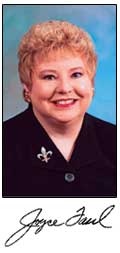
This issue featuresFood Engineering’s 17th annual packaging trends survey. Each year, thanks to you, our readers, we are able to present a definitive look at where packaging machinery and material decisions will be heading in the next few years.
Given the events of the past year that have effected both the nation’s safety as a whole and have included some large product recalls, it is no surprise that our survey found product safety to be the number one issue impacting food packaging.
However, right on the heels of the safety issue, cost of materials ranks as the second most important packaging challenge facing food manufacturers. Herein lies the dilemma—simultaneously providing improved safety for the consumer throughout the supply chain, within the plant, within the product and on the package itself without driving up costs. Doing more with less has become the mantra not just for food packaging and processing, but for all industries and services.
According to Food Engineering readers, consumer convenience is still high on the list of issues that most impact food packaging decisions. It came in as the number five most important factor in food packaging decisions, according to our survey.
Recently I’ve learned that convenience packaging can help people in very surprising ways. While this instance of how convenience packaging made the difference in one person’s life is extremely rare, I thought I’d share it with you for a number of reasons.
A few weeks ago I attended a major automation conference in Florida. While I did expect to learn more about the latest and greatest in the high tech processing arena, some of the last things I expected to take away were simple ideas on how food packaging made a serious difference in one individual’s life, and how a complex problem can often be solved with a simple solution.
One of the motivational speakers featured at this conference was Jamie Clark, an adventurer who attempted to climb Mount Everest three times and finally conquered the summit in 1997.
Want to know what made the difference in getting to the top? Pringles potato chips. (This is not a joke. Repeat. This is not a joke.)
According to Clark, the exhausted and hungry climbers brought along bags of potato chips to reward themselves after a tough day on the top of the world. However they neglected to take into account the effect extremely high altitudes would have on the bags of chips. The disappointed climbers had to contend with the tiny and unsatisfying morsels of chips that resulted. They didn’t reach their goal on that trip.
Next time around they decided to take along some Pringles. The climbers got the eating satisfaction they desired with the potato chips totally intact.
In his speech Clark was certainly not endorsing one brand of chips over another. But his point was clear. The Mount Everest adventurers had spent month after month and year after year plotting and planning every detail of their next trip and agonizing over the mistakes of the past. But it was not improved physical or mental training or the latest equipment that helped them achieve their goal. It was a simple change in the food packaging they brought along that helped them to the top of Mount Everest.
We all face tough challenges in our jobs and in our lives, but sometimes it’s nice to be reminded that keeping things simple and in focus can make the world of difference.
Maybe a few simple manufacturing solutions are right under your nose. Keeping it real, keeping it simple may be just what you need to accomplish more with less.