Get the weight out
Lightweighting of PET containers and systems that otherwise reduce packaging costs were in abundance at PACK EXPO.
The drive to lightweight containers and effect other material
reductions is shifting into overdrive, and manufacturers stand to save
millions.
A progress report on those efforts was on display in November at PACK EXPO. Greenhouse gas emissions in making and shipping packaging materials, less any recovered materials, are being calculated for packaged goods sold at Wal-Mart, Packaging Director Amy Zettlemoyer-Lazar said in the show’s keynote address. Wal-Mart wants suppliers to reduce package weight by 5% in the next five years. She cited several examples of increased sales and positive shopper feedback from lightweighting initiatives. Kraft eliminated a fifth of the weight for salad dressing containers by altering the profile and switching to an induction seal.
Rehabilitating the PET bottle’s image is an uphill battle for greener packaging, though suppliers are throwing themselves into the challenge with gusto. Wall thicknesses have been reduced to the point of bursting. The neck now contributes the bulk of many bottles’ weight. A sleek profile helped Sidel Inc. lower the weight of its half-liter NoBottle to 9.9 grams, compared to 15g for a conventional container, according to Deborah L. Galloway, marketing manager for the firm’s Norcross, GA-based Americas Cluster. Launched a year ago, NoBottle now benefits from a blowmold line that can output 43,200 bottles an hour. The bottles’ shape memory prevents leakers as it jostles down the FlexLine, which features energy-efficient improvements that cut electric consumption 32% on a per-bottle basis.
A barrel of oil and 7,000 gallons of process water are needed to produce 315 lbs. of label adhesive, according to Nordson Corp.’s Dave Gregetic. To conserve those resources, food and beverage packages can cut adhesive consumption to as little as a tenth the quantity used by wheel-pot applicators with a spray system that spritzes a dot matrix onto a PET bottle or other surface.
Potential savings aren’t as dramatic with magazine-fed systems, but reduced maintenance and downtime were reported by a food plant that just completed a one-year field test. The manufacturer reported a six-month payback. Conversion was completed in three hours.
Shrink wrap and stretch wrap on pallets are next on Sidel’s to-do list, according to Galloway. Any reductions in material use are positive, but the landfill issues with polyethylene film remain. Additives that help microorganisms break down the film are becoming popular in Europe, with one of the world’s largest suppliers joining the fray with degradable PE film. The firm’s Shelbyville, TN division, Manuli Stretch USA, promoted the new stretch film at PACK EXPO, though Company Representative Adele Brianza expects it to be a niche product.
Alternatives to wooden pallets are proliferating. CHEP USA, a global pallet-pooling service, showed off its newest version of reusable plastic pallets, which feature fire retardants to minimize the potential of poisonous gases in the event of a warehouse conflagration. Joining CHEP in a bid for the food industry’s pooled-pallets business is Worthington Steelpac, which introduced a distribution pallet manufactured to Grocery Manufacturers Association standards.
For more information:
Dave Gregetic, Nordson Corp., 770-497-3715, dgregetic@nordson.com
Deborah L. Galloway, Sidel Inc., 770-403-5132, deborah.galloway@sidel.com
Steve Letnich, Worthington Steelpac, 313-590-2663, sjletnic@worthingtonindustries.com
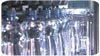
A stylish profile is left after whittling a third of the plastic from Sidel’s PET NoBottle, which now can be produced at high speeds on an energy-efficient combi line. Source: Sidel Inc.
A progress report on those efforts was on display in November at PACK EXPO. Greenhouse gas emissions in making and shipping packaging materials, less any recovered materials, are being calculated for packaged goods sold at Wal-Mart, Packaging Director Amy Zettlemoyer-Lazar said in the show’s keynote address. Wal-Mart wants suppliers to reduce package weight by 5% in the next five years. She cited several examples of increased sales and positive shopper feedback from lightweighting initiatives. Kraft eliminated a fifth of the weight for salad dressing containers by altering the profile and switching to an induction seal.
Rehabilitating the PET bottle’s image is an uphill battle for greener packaging, though suppliers are throwing themselves into the challenge with gusto. Wall thicknesses have been reduced to the point of bursting. The neck now contributes the bulk of many bottles’ weight. A sleek profile helped Sidel Inc. lower the weight of its half-liter NoBottle to 9.9 grams, compared to 15g for a conventional container, according to Deborah L. Galloway, marketing manager for the firm’s Norcross, GA-based Americas Cluster. Launched a year ago, NoBottle now benefits from a blowmold line that can output 43,200 bottles an hour. The bottles’ shape memory prevents leakers as it jostles down the FlexLine, which features energy-efficient improvements that cut electric consumption 32% on a per-bottle basis.
A barrel of oil and 7,000 gallons of process water are needed to produce 315 lbs. of label adhesive, according to Nordson Corp.’s Dave Gregetic. To conserve those resources, food and beverage packages can cut adhesive consumption to as little as a tenth the quantity used by wheel-pot applicators with a spray system that spritzes a dot matrix onto a PET bottle or other surface.
Potential savings aren’t as dramatic with magazine-fed systems, but reduced maintenance and downtime were reported by a food plant that just completed a one-year field test. The manufacturer reported a six-month payback. Conversion was completed in three hours.
Shrink wrap and stretch wrap on pallets are next on Sidel’s to-do list, according to Galloway. Any reductions in material use are positive, but the landfill issues with polyethylene film remain. Additives that help microorganisms break down the film are becoming popular in Europe, with one of the world’s largest suppliers joining the fray with degradable PE film. The firm’s Shelbyville, TN division, Manuli Stretch USA, promoted the new stretch film at PACK EXPO, though Company Representative Adele Brianza expects it to be a niche product.
Alternatives to wooden pallets are proliferating. CHEP USA, a global pallet-pooling service, showed off its newest version of reusable plastic pallets, which feature fire retardants to minimize the potential of poisonous gases in the event of a warehouse conflagration. Joining CHEP in a bid for the food industry’s pooled-pallets business is Worthington Steelpac, which introduced a distribution pallet manufactured to Grocery Manufacturers Association standards.
For more information:
Dave Gregetic, Nordson Corp., 770-497-3715, dgregetic@nordson.com
Deborah L. Galloway, Sidel Inc., 770-403-5132, deborah.galloway@sidel.com
Steve Letnich, Worthington Steelpac, 313-590-2663, sjletnic@worthingtonindustries.com
Looking for a reprint of this article?
From high-res PDFs to custom plaques, order your copy today!