Water Efficiency: Don't Let Your Liquid Assets Go Down the Drain
Food processors confront both financial and behavioral issues when implementing green water practices.

What’s another name for a high-pressure hose?
Answer: A broom.
Bad joke or pithy observation? Either way, it describes the long-standing approach to water use in manufacturing environments. Blessed with seemingly infinite availability and absurdly low costs, food and beverage manufacturers traditionally had little reason to curtail water consumption and disposal in their plants.
Change is coming, and it’s arriving with a vengeance in pockets of America. Disposal fees and surcharges are putting the viability of some plants at risk, and a closer look at the total cost of water that is treated, heated and chemically reconstituted is making conservation more attractive. At the same time, the social and environmental aspects of sustainable business practices make wasteful water use unacceptable. But investing in technology is only part of the solution. Fundamental changes in the behavior of people within the organization also are required.
“Mechanical methods” to remove solid fruit waste-brooms, rakes, squeegees and shovels-replaced the water hose two years ago at Southern Gardens Citrus in Clewiston, FL. Sweeping reduces water needed for sanitation “but also minimizes the organics we put into our wastewater,” points out John Webb, utilities team leader at Southern Gardens, a subsidiary of US Sugar Corp. Drains in production buildings carry process water to an industrial wastewater treatment plant, where it is treated and routed to orange groves.
While fruit and vegetable processors long have placed processing facilities in close proximity to raw materials, Southern Gardens was founded in 1994 on the principle of zero-waste from a vertically integrated juice company. Now as the largest supplier of private-label, not-from-concentrate orange juice, the company is placing increasing emphasis on sustainable practices, partly in recognition of the impact of corporate behavior on shoppers’ purchase decisions. As a practical matter, water conservation and re-use is needed to sustain Southern Gardens’ 2.2 million orange trees. Rooted in the Lake Okeechobee watershed, those trees enjoy abundant rainfall much of the year, but the region is parched in the spring. The 196.2 million gallons of water pumped from the wastewater collection system are critical for the plant’s raw materials. The storm water reservoir has evolved into a nesting area for thousands of birds, in aesthetic contrast to the cattle pastures that once marked the land.
Staff involvement in water conservation is a low cost, high return activity at Southern Gardens. A water conservation team organized two years ago by Vice President Tris Chapman has been instrumental in identifying opportunities and encouraging efficient practices.
Operators are urged to report malfunctioning solenoid valves that regulate pressurized water when conveyor belts stop. Leaky faucets, running toilets and steam leaks are more quickly repaired when everyone is on the lookout for them, points out Juan Maldonado, environmental specialist. “Continuous improvement in conservation efforts not only boosts our sustainability profile,” he says, “it increases our profits at the same time.”
Survivability, not profitability, drives some of the most ambitious water projects underway in food processing. HJ Heinz’s Ore-Ida plant on the Snake River in Ontario, OR, is in the midst of an ambitious wastewater recovery project that will polish, filter and re-use as much as 96% of the 3 million gallons of water used each day in potato processing. The plant was fined $1 million for discharging untreated waste into the Snake River in 1994, an event that culminated with a mandate to significantly upgrade its wastewater treatment. Sharply rising sewer-use fees throughout the US are pushing many other food and beverage manufacturers to install anaerobic digesters and undertake other reclamation projects to throttle down BOD and COD levels in their wastewater streams. Reverse osmosis and other technologies typically associated with desalination are finding a niche at some plants, though nothing on the scale of Orange County, CA’s groundwater replenishment project (see related story on page 47).
Water efficiency is an easier sell in areas where water availability is an issue. A compact, automatic tunnel washer that fits into limited space is a popular option for plant operators who value a small footprint, points out Kevin Lemen, president of Douglas Machines Corp., Clearwater, FL. A longer version that consumes about a fifth as much water as the compact unit is the machine of choice in drought-sensitive areas. “We always sell the longer tunnel in California,” says Lemen. “They don’t want the space-saver.”
Incidental ROI
Saving water does not provide enough payback to motivate any processors to install a washing and sanitizing system, Lemen continues. Automation projects still turn on the labor savings they provide. “The standards for cleaning and sanitizing have increased, and quick turnaround time for a changeover is being emphasized more,” but reduced water consumption is far down the benefits list.
Quicker sanitation cycles is a big motivator, agrees Marty Hurdt of Atlanta-based AmeriVap Systems Inc., but municipal water authorities also are extending carrots for water conservation to complement the stick of wastewater surcharges. He cites a bakery client that will qualify for tax incentives if it can slash daily water use to 3,800 gallons a day from 30,000. Much of the savings will come from switching from hoses that spray 8-10 gallons of water a minute to dry steam generators that consume 2-3 gallons an hour while delivering localized steam at 365°F.
Recalling his background at a northeastern Ohio bakery, the corporate sanitarian says the removal of water after a traditional washdown is a time-consuming activity that can add more suspended solids to a plant’s wastewater load. Hurdt remembers four instances when the bakery was fined $20,000 or more for excess loads. Today’s fines are even stiffer, he notes.
Comprehensive audits of a plant’s water use and the costs associated at each stage are giving way to more actionable projects that deliver hard savings. The plug was pulled on a comprehensive audit program from JohnsonDiversey and Nalco Corp. in 2007, and while Naperville, IL-based Nalco still offers a full-blown audit, “we’re trying to zero in quickly on projects that are going to offer the greatest overall savings,” explains Ed Binot, senior industry development manager. “Altruism or public image is not a minor consideration for large soft drink companies and breweries,” he allows, but mainstream food and beverage companies are interested in project-oriented solutions, not comprehensive reviews.
“Right now, there are companies with lofty goals, but they’re making decisions based on the financial returns,” agrees Staffan Akerstrom, chief operating officer and technology chief at Costa Mesa, CA-based EPS Corp., an energy analytics firm that helps manufacturers manage energy programs. “Water use has a great impact on the energy side, but it’s not the most expensive commodity and [it] tends to get bundled with other goals,” such as a percentage reduction in greenhouse gases and waste. EPS recently completed an anaerobic system tied to a cogenerator at Miller Brewing’s Irwindale, CA, brewery and is developing a comprehensive water treatment system at a Texas brewery, but those projects are driven by the cost of power and discharge fees, not by water-efficiency goals.
Unless a company is spending at least $500,000 a year to treat wastewater, an anaerobic digester doesn’t make economic sense, Akerstrom continues. After that threshold is passed, the best-use analysis of methane production is rendered meaningless if the project is not managed and maintained effectively, he cautions.
Passing muster
Fats and proteins in kill facilities add considerable complexity to water handling. When further processes involving marinades and other steps are part of the mix, the effluent can be nasty. Yet the Monett, MO, Tyson Foods plant has gone 10 years without a discharge violation and has earned numerous honors from environmental groups. It also received its third consecutive Gold Stewardship Award from corporate this year.
“We’re taking sustainability from a corporate mandate to the heart of the plant’s culture,” Plant Manager David Young told attendees at this year’s Food Automation & Manufacturing Conference. “We’re in the chicken business, but we also wanted to change processes and make something real that will be here 20 years from now.”
Twenty years of discussions over an enhanced pretreatment facility in Monett ended in October when a new dissolved air flotation system came on line. “We were good before we did this,” Young said, but the new system-and a training program that qualifies operators to run a municipal facility-is a game changer. The system reclaims 720 gallons a minute, or 180 million gallons a year, to cool vacuum pumps, assist trench-drain flow and cool heat exchangers. It is central to a goal of reducing water consumption by 1 million gallons per week or to about a sixth of demand.
How far the Monett facility can push water treatment, conservation and re-use is tempered by the review and approval of any process changes by USDA inspectors. “The industry is still obligated to maintain the efficacy of the food safety system while trying to improve water-use practices,” Young notes. The burden of proof lies with the plant.
“FSIS regulations pose a very delicate balance,” says Nalco’s Binot, who regards water-efficiency efforts in meat and poultry “one of the most difficult to address, but one of the most interesting too.” Reducing high-pressure washdowns is a logical change to make to reduce usage, “but there are behavioral changes you have to address,” he says, and outsourced sanitation undermines control.
Changing behavior of 450 processing employees is almost as challenging as winning corporate approval for the pretreatment system, Young conceded. “If you care, they care; if you don’t, it shows.”
Younger workers in particular will default to the easy way to complete tasks, rather than the right way, unless constant reinforcement is provided. “Changing the perception that water is free requires a culture change,” Southern Gardens’ Webb says.
Reinforcing positive behavior and encouraging the staff to tackle tasks the right way, not the easy way, takes much more diligence than installing technology, but it is an absolutely essential first step. Unless people view water as a liquid asset and not a commodity, technical solutions are unlikely to deliver the savings they promise.
For more information:
Marty Hurdt, Amerivap Systems Inc., 404-350-0239
Kevin Lemen, Douglas Machines Corp., 727-461-3477, klemen@dougmac.com
Staffan Akerstrom, EPS Corp., 866-377-7834
Ed Binot, Nalco Co., 630-305-1627
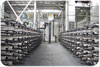
GWRS began transforming wastewater into pristine aqua three decades ago, though activity ratcheted upward last year upon the commission of a $480 million project. Emerson’s Delta V controls architecture quarterbacks the process, and a backflush every 20 minutes keeps the Siemens microfiltration membranes from fouling, but the heart of the system consists of 15 reverse-osmosis trains from Hydranautics in nearby Oceanside, CA, according to Shivagji Deshmukh, GWRS program manager. The advanced polyamide membrane elements let the R/O system operate at very low pressures with minimal fouling while allowing 85% pass-through of the fluid stream. The rejected brine is sent back to the sanitary plant, which discharges it into the ocean.
The technology is similar to seawater desalination, but the energy needed is significantly less, explains Deshmukh. The key is the R/O’s three-stage spiral wound membranes, which are chemically cleaned every six months. He expects five years service before irreversible fouling occurs.
Nearby water districts in water-starved southern California are considering similar purification plants, and GWRS is a pioneer in the application of R/O for water purification. The system’s only constraint, Deshmukh explains, is sourcing water to treat: “It’s basically a plumbing issue.”

The stormwater collection system at Southern Garden Citrus doubles as a bird sanctuary. Water conservation and re-use at the juice processor’s plant helps meet irrigation demand in the orange groves surrounding the facility. Source: Southern Garden Citrus.
What’s another name for a high-pressure hose?
Answer: A broom.
Bad joke or pithy observation? Either way, it describes the long-standing approach to water use in manufacturing environments. Blessed with seemingly infinite availability and absurdly low costs, food and beverage manufacturers traditionally had little reason to curtail water consumption and disposal in their plants.
Change is coming, and it’s arriving with a vengeance in pockets of America. Disposal fees and surcharges are putting the viability of some plants at risk, and a closer look at the total cost of water that is treated, heated and chemically reconstituted is making conservation more attractive. At the same time, the social and environmental aspects of sustainable business practices make wasteful water use unacceptable. But investing in technology is only part of the solution. Fundamental changes in the behavior of people within the organization also are required.
“Mechanical methods” to remove solid fruit waste-brooms, rakes, squeegees and shovels-replaced the water hose two years ago at Southern Gardens Citrus in Clewiston, FL. Sweeping reduces water needed for sanitation “but also minimizes the organics we put into our wastewater,” points out John Webb, utilities team leader at Southern Gardens, a subsidiary of US Sugar Corp. Drains in production buildings carry process water to an industrial wastewater treatment plant, where it is treated and routed to orange groves.
While fruit and vegetable processors long have placed processing facilities in close proximity to raw materials, Southern Gardens was founded in 1994 on the principle of zero-waste from a vertically integrated juice company. Now as the largest supplier of private-label, not-from-concentrate orange juice, the company is placing increasing emphasis on sustainable practices, partly in recognition of the impact of corporate behavior on shoppers’ purchase decisions. As a practical matter, water conservation and re-use is needed to sustain Southern Gardens’ 2.2 million orange trees. Rooted in the Lake Okeechobee watershed, those trees enjoy abundant rainfall much of the year, but the region is parched in the spring. The 196.2 million gallons of water pumped from the wastewater collection system are critical for the plant’s raw materials. The storm water reservoir has evolved into a nesting area for thousands of birds, in aesthetic contrast to the cattle pastures that once marked the land.
Staff involvement in water conservation is a low cost, high return activity at Southern Gardens. A water conservation team organized two years ago by Vice President Tris Chapman has been instrumental in identifying opportunities and encouraging efficient practices.
Operators are urged to report malfunctioning solenoid valves that regulate pressurized water when conveyor belts stop. Leaky faucets, running toilets and steam leaks are more quickly repaired when everyone is on the lookout for them, points out Juan Maldonado, environmental specialist. “Continuous improvement in conservation efforts not only boosts our sustainability profile,” he says, “it increases our profits at the same time.”
Survivability, not profitability, drives some of the most ambitious water projects underway in food processing. HJ Heinz’s Ore-Ida plant on the Snake River in Ontario, OR, is in the midst of an ambitious wastewater recovery project that will polish, filter and re-use as much as 96% of the 3 million gallons of water used each day in potato processing. The plant was fined $1 million for discharging untreated waste into the Snake River in 1994, an event that culminated with a mandate to significantly upgrade its wastewater treatment. Sharply rising sewer-use fees throughout the US are pushing many other food and beverage manufacturers to install anaerobic digesters and undertake other reclamation projects to throttle down BOD and COD levels in their wastewater streams. Reverse osmosis and other technologies typically associated with desalination are finding a niche at some plants, though nothing on the scale of Orange County, CA’s groundwater replenishment project (see related story on page 47).
Water efficiency is an easier sell in areas where water availability is an issue. A compact, automatic tunnel washer that fits into limited space is a popular option for plant operators who value a small footprint, points out Kevin Lemen, president of Douglas Machines Corp., Clearwater, FL. A longer version that consumes about a fifth as much water as the compact unit is the machine of choice in drought-sensitive areas. “We always sell the longer tunnel in California,” says Lemen. “They don’t want the space-saver.”
Incidental ROI
Saving water does not provide enough payback to motivate any processors to install a washing and sanitizing system, Lemen continues. Automation projects still turn on the labor savings they provide. “The standards for cleaning and sanitizing have increased, and quick turnaround time for a changeover is being emphasized more,” but reduced water consumption is far down the benefits list.
Quicker sanitation cycles is a big motivator, agrees Marty Hurdt of Atlanta-based AmeriVap Systems Inc., but municipal water authorities also are extending carrots for water conservation to complement the stick of wastewater surcharges. He cites a bakery client that will qualify for tax incentives if it can slash daily water use to 3,800 gallons a day from 30,000. Much of the savings will come from switching from hoses that spray 8-10 gallons of water a minute to dry steam generators that consume 2-3 gallons an hour while delivering localized steam at 365°F.
Recalling his background at a northeastern Ohio bakery, the corporate sanitarian says the removal of water after a traditional washdown is a time-consuming activity that can add more suspended solids to a plant’s wastewater load. Hurdt remembers four instances when the bakery was fined $20,000 or more for excess loads. Today’s fines are even stiffer, he notes.
Comprehensive audits of a plant’s water use and the costs associated at each stage are giving way to more actionable projects that deliver hard savings. The plug was pulled on a comprehensive audit program from JohnsonDiversey and Nalco Corp. in 2007, and while Naperville, IL-based Nalco still offers a full-blown audit, “we’re trying to zero in quickly on projects that are going to offer the greatest overall savings,” explains Ed Binot, senior industry development manager. “Altruism or public image is not a minor consideration for large soft drink companies and breweries,” he allows, but mainstream food and beverage companies are interested in project-oriented solutions, not comprehensive reviews.
“Right now, there are companies with lofty goals, but they’re making decisions based on the financial returns,” agrees Staffan Akerstrom, chief operating officer and technology chief at Costa Mesa, CA-based EPS Corp., an energy analytics firm that helps manufacturers manage energy programs. “Water use has a great impact on the energy side, but it’s not the most expensive commodity and [it] tends to get bundled with other goals,” such as a percentage reduction in greenhouse gases and waste. EPS recently completed an anaerobic system tied to a cogenerator at Miller Brewing’s Irwindale, CA, brewery and is developing a comprehensive water treatment system at a Texas brewery, but those projects are driven by the cost of power and discharge fees, not by water-efficiency goals.
Unless a company is spending at least $500,000 a year to treat wastewater, an anaerobic digester doesn’t make economic sense, Akerstrom continues. After that threshold is passed, the best-use analysis of methane production is rendered meaningless if the project is not managed and maintained effectively, he cautions.
Passing muster
Fats and proteins in kill facilities add considerable complexity to water handling. When further processes involving marinades and other steps are part of the mix, the effluent can be nasty. Yet the Monett, MO, Tyson Foods plant has gone 10 years without a discharge violation and has earned numerous honors from environmental groups. It also received its third consecutive Gold Stewardship Award from corporate this year.
“We’re taking sustainability from a corporate mandate to the heart of the plant’s culture,” Plant Manager David Young told attendees at this year’s Food Automation & Manufacturing Conference. “We’re in the chicken business, but we also wanted to change processes and make something real that will be here 20 years from now.”
Twenty years of discussions over an enhanced pretreatment facility in Monett ended in October when a new dissolved air flotation system came on line. “We were good before we did this,” Young said, but the new system-and a training program that qualifies operators to run a municipal facility-is a game changer. The system reclaims 720 gallons a minute, or 180 million gallons a year, to cool vacuum pumps, assist trench-drain flow and cool heat exchangers. It is central to a goal of reducing water consumption by 1 million gallons per week or to about a sixth of demand.
How far the Monett facility can push water treatment, conservation and re-use is tempered by the review and approval of any process changes by USDA inspectors. “The industry is still obligated to maintain the efficacy of the food safety system while trying to improve water-use practices,” Young notes. The burden of proof lies with the plant.
“FSIS regulations pose a very delicate balance,” says Nalco’s Binot, who regards water-efficiency efforts in meat and poultry “one of the most difficult to address, but one of the most interesting too.” Reducing high-pressure washdowns is a logical change to make to reduce usage, “but there are behavioral changes you have to address,” he says, and outsourced sanitation undermines control.
Changing behavior of 450 processing employees is almost as challenging as winning corporate approval for the pretreatment system, Young conceded. “If you care, they care; if you don’t, it shows.”
Younger workers in particular will default to the easy way to complete tasks, rather than the right way, unless constant reinforcement is provided. “Changing the perception that water is free requires a culture change,” Southern Gardens’ Webb says.
Reinforcing positive behavior and encouraging the staff to tackle tasks the right way, not the easy way, takes much more diligence than installing technology, but it is an absolutely essential first step. Unless people view water as a liquid asset and not a commodity, technical solutions are unlikely to deliver the savings they promise.
For more information:
Marty Hurdt, Amerivap Systems Inc., 404-350-0239
Kevin Lemen, Douglas Machines Corp., 727-461-3477, klemen@dougmac.com
Staffan Akerstrom, EPS Corp., 866-377-7834
Ed Binot, Nalco Co., 630-305-1627
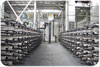
Fifteen reverse-osmosis trains remove salts that survived the filtration process before final UV treatment at Orange County’s ambitious groundwater purification plant. Source: Groundwater Replenishment System.
Pushing the water-purification envelope
Once people get past the “ugh” factor, respect for the possibilities of purification technology is the usual reaction to the Groundwater Replenishment System (GWRS) in Fountain Valley, CA. Each day, GWRS accepts 70 million gallons of discharge from the adjacent Orange County Sanitary District treatment plant, then processes it through a series of microfiltration and reverse osmosis units before an ultraviolet and hydrogen peroxide treatment, creating a finished product that rivals the best bottled water. It is then injected into 36 wells to replenish the aquifer and provide a bulwark against seawater intrusion.GWRS began transforming wastewater into pristine aqua three decades ago, though activity ratcheted upward last year upon the commission of a $480 million project. Emerson’s Delta V controls architecture quarterbacks the process, and a backflush every 20 minutes keeps the Siemens microfiltration membranes from fouling, but the heart of the system consists of 15 reverse-osmosis trains from Hydranautics in nearby Oceanside, CA, according to Shivagji Deshmukh, GWRS program manager. The advanced polyamide membrane elements let the R/O system operate at very low pressures with minimal fouling while allowing 85% pass-through of the fluid stream. The rejected brine is sent back to the sanitary plant, which discharges it into the ocean.
The technology is similar to seawater desalination, but the energy needed is significantly less, explains Deshmukh. The key is the R/O’s three-stage spiral wound membranes, which are chemically cleaned every six months. He expects five years service before irreversible fouling occurs.
Nearby water districts in water-starved southern California are considering similar purification plants, and GWRS is a pioneer in the application of R/O for water purification. The system’s only constraint, Deshmukh explains, is sourcing water to treat: “It’s basically a plumbing issue.”
Looking for a reprint of this article?
From high-res PDFs to custom plaques, order your copy today!