Water Gets Its Due
The
sustainability bandwagon is groaning under the weight of corporations climbing
aboard. The time for water resource management has never been
better.
Cheap and plentiful utilities are taken for granted, and on a planet where 71% of the surface is covered with water, supplies understandably can be mistaken for limitless. The cost at the tap hardly encourages judicious use either. Paybacks from efficiency investments can stretch out for years. The result is usage patterns that make compressed air, a notoriously wasteful plant utility, look like a model of efficiency.
The party isn’t over, but in some instances, Mother Nature is signaling last call. On Oct. 23, Georgia Gov. Sonny Perdue ordered non-farm water-permit holders in the 61 northern counties to pump 10% less water this winter than last year. The state has ignored its looming water shortage for decades, and drought-like conditions that saw rainfall reduced by half in 2007 finally forced action. A spokesman in the governor’s office says homeowners are shouldering the conservation burden for now, with bans on lawn watering and an emphasis on public awareness that is expected to enable municipal waterworks to satisfy the restrictions.
Outreach programs are being developed for state employees and teachers, and Atlanta’s biggest corporate citizen recently distributed home conservation kits to thousands of its employees. Gov. Perdue helped muster support by leaving voice-mail messages for 5,500 Coca-Cola workers, urging them to use the kits and start practicing water conservation. When 98% of your employer’s product is water, after all, sustainable water use is tied to job security.
Georgia is not alone. Critical conditions are developing in pockets of Wisconsin and other areas. As in the Peach State, authorities are sheltering industry for now, though huge infrastructure investments could drive costs up substantially. In California, the Orange County Water District is building a $481 million groundwater replenishment system that will use reverse osmosis (R/O), ultraviolet light, peroxide and other sanitizing remedies to clean wastewater and inject it underground. Those types of infrastructure improvements, along with replacement costs, have not been included in US water costs, leaving rates artificially low. The national average fee was $1.93 per 1,000 gallons in 1999, according to the EPA, compared to $4.35 in the UK and $6.89 in Germany.
If infrastructure upgrades are included, public water prices could spike to the $3.60-$4.70 range, says Warren Green, process engineering manager at Cincinnati’s Hixson Inc. As it is, “tap fees have tripled over the last 25 years,” with fees approaching $4 per 1,000 gallons in some areas, Green says. When disposal costs that often include BOD removal are factored, the lifecycle cost of water doesn’t look so cheap.
Water use varies widely for different types of processing plants, and regulatory requirements can greatly increase the amount of water needed. Ready-to-eat (RTE) meat processors have significantly increased their usage in recent years to better control possible Listeria contamination, for example. Based on his experience auditing water use in food facilities, Green developed average water demands per 1,000 lbs. of finished goods at different plant categories (see sidebar on page 126). Within a given category, usage patterns vary widely. He has documented water demands from 740 to 2,300 gallons for RTE meat, for example.
Water re-use can push consumption to the low end of the scale. So-called grey water cannot contact edible products, be used in product formulations or create unsanitary conditions. Additional prohibitions are detailed in 21 CFR 416.2 (g) and, for meat and poultry processing, in FSIS Directive 11,000.1. Industry has made progress in cutting waste, but plenty of re-use opportunities remain, Green notes.
“In a typical CIP cycle, water from the last rinse now is typically used in the first rinse of the next cycle,” he points out. That wasn’t always the case, and one-pass use of heat-exchanger water remains fairly common. Some equipment vendors are incorporating simple automatic devices to reduce water waste. Solenoid valves that turn off a 5-gallon-per-minute flow through a dairy homogenizer can save millions of gallons over the life of the equipment. “The last thing processors want to worry about is if the water is running or not, and leaving it running all the time eliminates that worry,” says Green. “It’s the same trade-off as with compressed air, which is convenient but also the most expensive air in a plant.”
Simple actions such as repairing water and steam leaks and using low- flow/high-velocity water for cleaning can conserve large amounts of water. Water brooms are another big resource waster and can be replaced with dry clean-up systems. Re-use systems usually require a capital outlay, and a long payback can be a deal killer. On the other hand, programs like the US Green Building Council’s Leadership in Energy and Environmental Design (LEED) program are encouraging corporations to tackle longer-term water projects. “A three- or four-year payback might be acceptable instead of two years,” observes Green.
“The technology to turn systems on and off automatically and for re-use is available; the issue is getting CEOs and executive managers interested in being creative and developing cross-disciplinary programs between engineering and marketing,” adds Dave Zepponi, executive director of Portland, OR-based North West Food Processors Association (NWFPA). “There’s a good opportunity for engineers and operations managers to work with marketers to package water savings as a sustainability program, but you need a systematic way of doing it.”
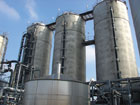
Naperville, IL-based Nalco began offering water audits at industrial sites in Europe in 2000. In recent years, the service has expanded to the United States and Canada. The service benchmarks plant water use against similar operations, then performs mass balancing to determine what became of the difference between water input and output.
Water is becoming a galvanizing issue. In Georgia, public prayer meetings were staged to solicit divine intervention from drought (rainfall did follow). For those with faith in science, audits can best determine how water is used and where the opportunities for improvement lie.
The process begins by gathering 12-18 months of plant water and energy data, followed by an on-site evaluation by a team of two to five specialists. Finally, computer models are applied, and best-available technologies for water treatment and sanitation practices are considered to come up with recommendations. “There are great variations in the savings, and surprising results sometimes, but at a minimum, plants can reduce consumption 5-15% on an annual basis without any capital-intensive projects,” says Binot. As corporations become more receptive to loosening purse strings in the name of sustainability, multi-million dollar projects with five-year ROIs have attracted funding.
Low-hanging fruit can be found in almost every plant. Adding a sensor to turn off a spray bar on a conveyor line can save both water and the cost of chemicals added to the water. Matching the appropriate hose and trigger to an application can effect big savings in sanitation. Re-using filtered and softened water as boiler feed or in refrigeration cooling towers reduces both water intake and disposal costs. “In many cases, people don’t really understand the value of a water stream as it goes through a process until they undergo an audit,” says Binot.
Volumetric use may be greatest in sanitation. Besides the raw water, additional filtration or purification steps may be used and heat and chemicals added. While food safety can’t be compromised, the cost of equipment cleaning is being scrutinized. Sanitary already is part of equipment evaluation; now, some companies are taking it to the next level, factoring in the time and volume of water needed to sanitize.
In February, a side-by-side test was set up on trim lines in a poultry plant’s deboning area to evaluate cleaning requirements for two types of conveyor belts. The week-long test involved six identical 25-ft. conveyors, half using interlocked plastic modules, the others with solid, extruded thermoplastic belts. Mol Industries, the Grand Rapids, MI fabricator of the solid belts, set up the test. Plant engineers timed the sanitation workers and metered water consumption.
According to Barry Whitman, vice president-market development at Mol, the solid belts consumed 105.9 gallons for each cleaning, compared to 190.7 gallons for the modular belts. Labor was clocked at 13.5 minutes per cycle for the solid belts vs. 21.6 minutes.
Similar trials are being conducted in other meat and poultry plants, says Whitman, and the company sees potential in other washdown environments, such as dairies and fresh-cut produce facilities. Modular belts are better suited for turns, he concedes, but for straight-aways, solid belting could produce significant water savings.
“Processors’ customers are demanding that they go green because it provides better PR for them,” Whitman says. “Saving millions of gallons of water might not cut water bills thousands of dollars, but the associated savings make reduced water use a no-brainer.”
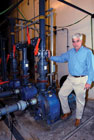
Anheuser-Busch Companies Inc. calls its anaerobic digesters bio-energy recovery systems (BERS), a renewable energy source that results in the light-hearted boast that the brewer is the King of BERS. The company isn’t bashful about promoting the water conservation and energy recovery aspects, points out NWFPA’s Zepponi. “Budweiser is able to use the productivity improvement as a marketing tool,” which makes it easier to justify shifting money from the marketing budget to additional BERS investments.
A yeast plant in Old Bridge, NJ was the first A-B facility to install BERS 30 years ago. “It worked so well, we said, ‘This is the future,’” recounts John Stier, director of environmental compliance. Ground recently was broken on an anaerobic system at the St. Louis company’s Fairfield, CA plant, which will be the tenth US brewery outfitted with BERS (the Wuhan, China brewery also has BERS). An installation at the company’s Virginia brewery is being evaluated. That would leave the Ft. Collins, CO plant as the only domestic facility without the technology.
An 80% reduction in wastewater is realized, and solid waste is cut in half. The gold is in the gas, however: The methane from digesters meets 10-15% of each brewery’s energy needs. Ten years ago, A-B put the savings from eight BERS-equipped facilities at $40 million annually. Since then, gas prices have more than doubled, pushing current value past $100 million.
When A-B began its BERS journey, about 80% of the off gases were captured. Today, “we’re in the 99%-plus category,” Stier says. “It’s a continuous improvement process. The design refinements in Fairfield will get us closer to 100%.
“BERS is a great match for the food industry because of all the organics in these wastestreams,” he adds. The days of flaring methane are over, he believes. “We’re the world’s largest operators of these systems, and the ultimate compliment is the calls we get from other food companies considering similar investments.” Just as bakers maintain a Mother Sour of complex yeasts to make sourdough bread, the anaerobic bacteria in A-B’s tanks are highly evolved organisms. To help other companies get their systems up and running, Stier says A-B occasionally loads a rail car with starter bugs for their ferment.
One grateful recipient was Gatorade Blue Ridge, the sports drink company’s gold-certified LEED plant in Wytheville, VA (see “Gatorade: Sustainability with attitude,” Food Engineering, October 2007). Methane from the anaerobic digesters fire a boiler used to generate hot water for the plant. BOD discharges are reduced to a tenth of typical levels, and the electrical cost to run blowers and the aeration system in an aerobic treatment system is eliminated.
Blue Ridge’s LEED application won points for the wastewater technology. Water credits also were generated from the selection of nanofiltration from GE Water & Process Technology over R/O, a substitution that will save 50 million gallons of water a year. Another 50 million gallons is saved with an innovative waterless bottle-rinsing system. Arguably the most sustainable improvement comes from volumetric fillers that eliminate 8,000 gallons of spilled product per line per day, an advance that also reduces BOD levels. All told, the plant uses 20% less water per unit of production than comparable hot-fill facilities.
Nestlé SA is another major food company trying to boost its water-use cred with a recovery system that will return up to 100,000 gallons a day from a dairy wastestream at a new $359 million plant in Anderson, IN. The recovered water will be used in the refrigeration system’s cooling towers. Nestlé is seeking LEED certification.
The Swiss food giant began beating the sustainability drum before the term was in vogue. Environmental stewardship was the term of choice several years ago, and Nestlé North America backed up the talk with capital projects like the cascade system using both carbon dioxide and ammonia refrigerants at its Stouffer’s frozen entrees plant in Jonesboro, AR (“Refrigeration, Naturally,” Food Engineering, November 2003). The new Indianapolis area dairy takes advantage of R/O and filtration technology from GE to recover cooling-tower water.
The 880,000-sq.-ft. facility was built by Stellar Group and is expected to begin production in the spring. Five lines will produce the fast-growing Nesquik ready-to-drink and Nestlé Coffee-Mate liquid products.
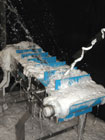
Engineer Kyle Booth designed the system. In minimizing the footprint, Booth had to deal with tank configurations that require a lot of suction to discharge. He opted for five Gorman-Rupp centrifugal pumps that move 180 gallons a minute. “Trying to save money in the short term with less expensive solutions can lead to increased costs, lost time and bad publicity in the long run,” maintains Booth. A robust treatment system helps minimize fines from municipal sewer authorities.
Biology is at least as important as engineering when dealing with wastewater. Aerobic treatment systems are susceptible to BOD surcharges when volumes surge and water can’t be held long enough at times to allow dry bacteria to become active. Two years ago, Irving, TX-based EcoBionics developed a compact cabinet with a 3-liter container that acts as an on-site fermenter of Pseudomonas and bacillus bacteria strains to treat sugars, animal fats, proteins and carbohydrates. The fermenter produces 31 trillion bacteria a day, the equivalent of 17-25 lbs. of dry bacteria. More importantly, they begin their conversion work as soon as they hit the waste soup.
Eight incubators were installed at a Texas facility producing 600 million lbs. of sauces, dressings and other products. BOD effluency overages were exceeding $600,000 a year, according to Tom Schroeder, EcoBionics’ business development manager. Average BOD levels were cut 42%, and variability was reduced by 65%. The plant, owned by one of the world’s largest food companies, realized net savings of $256,000 and recently received an environmental quality award from the state.
Rugged construction and simplicity of design are the keys to any waste treatment or water re-use system, concludes Hixson’s Green. Steam condensate return units are probably the most widely used recovery systems, and materials of construction are pipes, a condensate receiver tank with level control, pumps, starter motors and a simple control panel.
Pegging the total cost of 1,000 gallons of potable water at $4.50, he says the ROI from a simple re-use system from a single dairy homogenizer to a cooling water application is less than one year. Such a system can be installed for about $7,500 and operates on $250 worth of electricity a year. At a flow rate of 5 gallons a minute, the savings would be almost $8,500.
Opportunities like that have existed all along, of course, but efficiency is a tough sell, particularly when it involves an inexpensive commodity. The moral dimension of water stewardship never has played well, but thanks to sustainability programs, this commodity has been elevated to the status of valued resource. The time may never be better to capitalize on food manufacturing’s water re-use and treatment opportunities while embellishing the organization’s sustainability reputation. For more information:
Tom Schroeder, Ecobionics,
972-438-0694,
tom.schroeder@nch.com
Ellen Mellody,
GE Water & Process
Technologies, 215-942-3307, ellen.mellody@ge.com
Warren Green, Hixson Inc.,
513-241-1230,
wgreen@hixson-inc.com
Barry Whitman, Mol Industries, 616-453-2484
Ed Binot, Nalco Co.,
630-305-1000, ebinot@nalco.com
Jud Walker, Stellar Group,
904-899-9275,
jwalker@stellar.net
Category Gallons used
Soft drinks 185
Fruit drinks 310
Fresh bakery products 210
Frozen bakery (pies, pizza) 320
Fluid dairy 200
Cheese 330
Ice cream 380
Processed meat 1,500
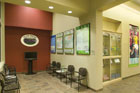
The principles of sustainable operations and resource use are posted in Gatorade’s Blue Ridge plant to build staff understanding and support. Water-use credits were a big part of the facility’s LEED gold certification. Source: The Gatorade Co.
The party isn’t over, but in some instances, Mother Nature is signaling last call. On Oct. 23, Georgia Gov. Sonny Perdue ordered non-farm water-permit holders in the 61 northern counties to pump 10% less water this winter than last year. The state has ignored its looming water shortage for decades, and drought-like conditions that saw rainfall reduced by half in 2007 finally forced action. A spokesman in the governor’s office says homeowners are shouldering the conservation burden for now, with bans on lawn watering and an emphasis on public awareness that is expected to enable municipal waterworks to satisfy the restrictions.
Outreach programs are being developed for state employees and teachers, and Atlanta’s biggest corporate citizen recently distributed home conservation kits to thousands of its employees. Gov. Perdue helped muster support by leaving voice-mail messages for 5,500 Coca-Cola workers, urging them to use the kits and start practicing water conservation. When 98% of your employer’s product is water, after all, sustainable water use is tied to job security.
Georgia is not alone. Critical conditions are developing in pockets of Wisconsin and other areas. As in the Peach State, authorities are sheltering industry for now, though huge infrastructure investments could drive costs up substantially. In California, the Orange County Water District is building a $481 million groundwater replenishment system that will use reverse osmosis (R/O), ultraviolet light, peroxide and other sanitizing remedies to clean wastewater and inject it underground. Those types of infrastructure improvements, along with replacement costs, have not been included in US water costs, leaving rates artificially low. The national average fee was $1.93 per 1,000 gallons in 1999, according to the EPA, compared to $4.35 in the UK and $6.89 in Germany.
If infrastructure upgrades are included, public water prices could spike to the $3.60-$4.70 range, says Warren Green, process engineering manager at Cincinnati’s Hixson Inc. As it is, “tap fees have tripled over the last 25 years,” with fees approaching $4 per 1,000 gallons in some areas, Green says. When disposal costs that often include BOD removal are factored, the lifecycle cost of water doesn’t look so cheap.
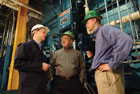
Audits of in-plant water re-use possibilities and benchmarking against similar plants are being used by some food and beverage companies to help improve efficiency and reduce waste. Source: Nalco Co.
Water re-use can push consumption to the low end of the scale. So-called grey water cannot contact edible products, be used in product formulations or create unsanitary conditions. Additional prohibitions are detailed in 21 CFR 416.2 (g) and, for meat and poultry processing, in FSIS Directive 11,000.1. Industry has made progress in cutting waste, but plenty of re-use opportunities remain, Green notes.
“In a typical CIP cycle, water from the last rinse now is typically used in the first rinse of the next cycle,” he points out. That wasn’t always the case, and one-pass use of heat-exchanger water remains fairly common. Some equipment vendors are incorporating simple automatic devices to reduce water waste. Solenoid valves that turn off a 5-gallon-per-minute flow through a dairy homogenizer can save millions of gallons over the life of the equipment. “The last thing processors want to worry about is if the water is running or not, and leaving it running all the time eliminates that worry,” says Green. “It’s the same trade-off as with compressed air, which is convenient but also the most expensive air in a plant.”
Simple actions such as repairing water and steam leaks and using low- flow/high-velocity water for cleaning can conserve large amounts of water. Water brooms are another big resource waster and can be replaced with dry clean-up systems. Re-use systems usually require a capital outlay, and a long payback can be a deal killer. On the other hand, programs like the US Green Building Council’s Leadership in Energy and Environmental Design (LEED) program are encouraging corporations to tackle longer-term water projects. “A three- or four-year payback might be acceptable instead of two years,” observes Green.
“The technology to turn systems on and off automatically and for re-use is available; the issue is getting CEOs and executive managers interested in being creative and developing cross-disciplinary programs between engineering and marketing,” adds Dave Zepponi, executive director of Portland, OR-based North West Food Processors Association (NWFPA). “There’s a good opportunity for engineers and operations managers to work with marketers to package water savings as a sustainability program, but you need a systematic way of doing it.”
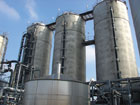
A three-pack of anaerobic digesters at Budweiser’s Houston brewery slashes water discharge into municipal treatment systems and generates millions of dollars worth of gas annually. Source: Anheuser-Busch.
More than feel-good
When the cost of chemicals, energy to heat or chill and pumps to move water are factored in, the lifecycle cost of a gallon of water starts to add up, a reality that has prompted some corporations to assign staff executives to find ways of reducing use. “Sustainability is not only PR,” insists Ed Binot, senior industry development manager at Nalco Co. “Availability is becoming critical in some places.”Naperville, IL-based Nalco began offering water audits at industrial sites in Europe in 2000. In recent years, the service has expanded to the United States and Canada. The service benchmarks plant water use against similar operations, then performs mass balancing to determine what became of the difference between water input and output.
Water is becoming a galvanizing issue. In Georgia, public prayer meetings were staged to solicit divine intervention from drought (rainfall did follow). For those with faith in science, audits can best determine how water is used and where the opportunities for improvement lie.
The process begins by gathering 12-18 months of plant water and energy data, followed by an on-site evaluation by a team of two to five specialists. Finally, computer models are applied, and best-available technologies for water treatment and sanitation practices are considered to come up with recommendations. “There are great variations in the savings, and surprising results sometimes, but at a minimum, plants can reduce consumption 5-15% on an annual basis without any capital-intensive projects,” says Binot. As corporations become more receptive to loosening purse strings in the name of sustainability, multi-million dollar projects with five-year ROIs have attracted funding.
Low-hanging fruit can be found in almost every plant. Adding a sensor to turn off a spray bar on a conveyor line can save both water and the cost of chemicals added to the water. Matching the appropriate hose and trigger to an application can effect big savings in sanitation. Re-using filtered and softened water as boiler feed or in refrigeration cooling towers reduces both water intake and disposal costs. “In many cases, people don’t really understand the value of a water stream as it goes through a process until they undergo an audit,” says Binot.
Volumetric use may be greatest in sanitation. Besides the raw water, additional filtration or purification steps may be used and heat and chemicals added. While food safety can’t be compromised, the cost of equipment cleaning is being scrutinized. Sanitary already is part of equipment evaluation; now, some companies are taking it to the next level, factoring in the time and volume of water needed to sanitize.
In February, a side-by-side test was set up on trim lines in a poultry plant’s deboning area to evaluate cleaning requirements for two types of conveyor belts. The week-long test involved six identical 25-ft. conveyors, half using interlocked plastic modules, the others with solid, extruded thermoplastic belts. Mol Industries, the Grand Rapids, MI fabricator of the solid belts, set up the test. Plant engineers timed the sanitation workers and metered water consumption.
According to Barry Whitman, vice president-market development at Mol, the solid belts consumed 105.9 gallons for each cleaning, compared to 190.7 gallons for the modular belts. Labor was clocked at 13.5 minutes per cycle for the solid belts vs. 21.6 minutes.
Similar trials are being conducted in other meat and poultry plants, says Whitman, and the company sees potential in other washdown environments, such as dairies and fresh-cut produce facilities. Modular belts are better suited for turns, he concedes, but for straight-aways, solid belting could produce significant water savings.
“Processors’ customers are demanding that they go green because it provides better PR for them,” Whitman says. “Saving millions of gallons of water might not cut water bills thousands of dollars, but the associated savings make reduced water use a no-brainer.”
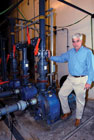
Plant Engineer Dave Muskopf stands next to one of five centrifugal pumps that move wastewater between three equalization tanks at the Ken’s Steakhouse plant in Las Vegas. Source: Gorman-Rupp Co.
Mining the wastestream
Dissolved sugars, fats and other biological loads in food plant wastestreams pose a treatment challenge that adds cost and possible surcharges. The less water discharged, the better, and investments in anaerobic treatments that recover methane and feed water to fire boilers are becoming economically attractive.Anheuser-Busch Companies Inc. calls its anaerobic digesters bio-energy recovery systems (BERS), a renewable energy source that results in the light-hearted boast that the brewer is the King of BERS. The company isn’t bashful about promoting the water conservation and energy recovery aspects, points out NWFPA’s Zepponi. “Budweiser is able to use the productivity improvement as a marketing tool,” which makes it easier to justify shifting money from the marketing budget to additional BERS investments.
A yeast plant in Old Bridge, NJ was the first A-B facility to install BERS 30 years ago. “It worked so well, we said, ‘This is the future,’” recounts John Stier, director of environmental compliance. Ground recently was broken on an anaerobic system at the St. Louis company’s Fairfield, CA plant, which will be the tenth US brewery outfitted with BERS (the Wuhan, China brewery also has BERS). An installation at the company’s Virginia brewery is being evaluated. That would leave the Ft. Collins, CO plant as the only domestic facility without the technology.
An 80% reduction in wastewater is realized, and solid waste is cut in half. The gold is in the gas, however: The methane from digesters meets 10-15% of each brewery’s energy needs. Ten years ago, A-B put the savings from eight BERS-equipped facilities at $40 million annually. Since then, gas prices have more than doubled, pushing current value past $100 million.
When A-B began its BERS journey, about 80% of the off gases were captured. Today, “we’re in the 99%-plus category,” Stier says. “It’s a continuous improvement process. The design refinements in Fairfield will get us closer to 100%.
“BERS is a great match for the food industry because of all the organics in these wastestreams,” he adds. The days of flaring methane are over, he believes. “We’re the world’s largest operators of these systems, and the ultimate compliment is the calls we get from other food companies considering similar investments.” Just as bakers maintain a Mother Sour of complex yeasts to make sourdough bread, the anaerobic bacteria in A-B’s tanks are highly evolved organisms. To help other companies get their systems up and running, Stier says A-B occasionally loads a rail car with starter bugs for their ferment.
One grateful recipient was Gatorade Blue Ridge, the sports drink company’s gold-certified LEED plant in Wytheville, VA (see “Gatorade: Sustainability with attitude,” Food Engineering, October 2007). Methane from the anaerobic digesters fire a boiler used to generate hot water for the plant. BOD discharges are reduced to a tenth of typical levels, and the electrical cost to run blowers and the aeration system in an aerobic treatment system is eliminated.
Blue Ridge’s LEED application won points for the wastewater technology. Water credits also were generated from the selection of nanofiltration from GE Water & Process Technology over R/O, a substitution that will save 50 million gallons of water a year. Another 50 million gallons is saved with an innovative waterless bottle-rinsing system. Arguably the most sustainable improvement comes from volumetric fillers that eliminate 8,000 gallons of spilled product per line per day, an advance that also reduces BOD levels. All told, the plant uses 20% less water per unit of production than comparable hot-fill facilities.
Nestlé SA is another major food company trying to boost its water-use cred with a recovery system that will return up to 100,000 gallons a day from a dairy wastestream at a new $359 million plant in Anderson, IN. The recovered water will be used in the refrigeration system’s cooling towers. Nestlé is seeking LEED certification.
The Swiss food giant began beating the sustainability drum before the term was in vogue. Environmental stewardship was the term of choice several years ago, and Nestlé North America backed up the talk with capital projects like the cascade system using both carbon dioxide and ammonia refrigerants at its Stouffer’s frozen entrees plant in Jonesboro, AR (“Refrigeration, Naturally,” Food Engineering, November 2003). The new Indianapolis area dairy takes advantage of R/O and filtration technology from GE to recover cooling-tower water.
The 880,000-sq.-ft. facility was built by Stellar Group and is expected to begin production in the spring. Five lines will produce the fast-growing Nesquik ready-to-drink and Nestlé Coffee-Mate liquid products.
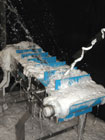
Plants can’t scrimp on sanitation, but equipment designed to make cleaning easier can save millions of gallons of water and hundreds of pounds of chemicals a year. Source: Dorner Manufacturing Corp.
Small is good
Space is the deal killer for many plant improvement projects, and the same holds for water-related efforts. Minneapolis-based World Water Works engineered a batch treatment for wastewater using three equalization tanks for Ken’s Foods, a salad dressing manufacturer that built a 185,000-sq.-ft. plant in Las Vegas in 2002. The 24-ft.-tall tanks require minimal space while meeting clarification and filtration requirements to remove oil and food solids.Engineer Kyle Booth designed the system. In minimizing the footprint, Booth had to deal with tank configurations that require a lot of suction to discharge. He opted for five Gorman-Rupp centrifugal pumps that move 180 gallons a minute. “Trying to save money in the short term with less expensive solutions can lead to increased costs, lost time and bad publicity in the long run,” maintains Booth. A robust treatment system helps minimize fines from municipal sewer authorities.
Biology is at least as important as engineering when dealing with wastewater. Aerobic treatment systems are susceptible to BOD surcharges when volumes surge and water can’t be held long enough at times to allow dry bacteria to become active. Two years ago, Irving, TX-based EcoBionics developed a compact cabinet with a 3-liter container that acts as an on-site fermenter of Pseudomonas and bacillus bacteria strains to treat sugars, animal fats, proteins and carbohydrates. The fermenter produces 31 trillion bacteria a day, the equivalent of 17-25 lbs. of dry bacteria. More importantly, they begin their conversion work as soon as they hit the waste soup.
Eight incubators were installed at a Texas facility producing 600 million lbs. of sauces, dressings and other products. BOD effluency overages were exceeding $600,000 a year, according to Tom Schroeder, EcoBionics’ business development manager. Average BOD levels were cut 42%, and variability was reduced by 65%. The plant, owned by one of the world’s largest food companies, realized net savings of $256,000 and recently received an environmental quality award from the state.
Rugged construction and simplicity of design are the keys to any waste treatment or water re-use system, concludes Hixson’s Green. Steam condensate return units are probably the most widely used recovery systems, and materials of construction are pipes, a condensate receiver tank with level control, pumps, starter motors and a simple control panel.
Pegging the total cost of 1,000 gallons of potable water at $4.50, he says the ROI from a simple re-use system from a single dairy homogenizer to a cooling water application is less than one year. Such a system can be installed for about $7,500 and operates on $250 worth of electricity a year. At a flow rate of 5 gallons a minute, the savings would be almost $8,500.
Opportunities like that have existed all along, of course, but efficiency is a tough sell, particularly when it involves an inexpensive commodity. The moral dimension of water stewardship never has played well, but thanks to sustainability programs, this commodity has been elevated to the status of valued resource. The time may never be better to capitalize on food manufacturing’s water re-use and treatment opportunities while embellishing the organization’s sustainability reputation. For more information:
Tom Schroeder, Ecobionics,
972-438-0694,
tom.schroeder@nch.com
Ellen Mellody,
GE Water & Process
Technologies, 215-942-3307, ellen.mellody@ge.com
Warren Green, Hixson Inc.,
513-241-1230,
wgreen@hixson-inc.com
Barry Whitman, Mol Industries, 616-453-2484
Ed Binot, Nalco Co.,
630-305-1000, ebinot@nalco.com
Jud Walker, Stellar Group,
904-899-9275,
jwalker@stellar.net
Benchmarking water use in food production
Manufacturers need to know where they are before they can figure out where they’re going. Based on decades of work with various types of food plants, engineers at Cincinnati’s Hixson Inc. determined average water use for various types of products. To make the averages comparable, usage is based on 1,000 lbs. of product produced. (A gallon of water weighs 8.34 lbs. at 4°C; therefore 1,000 lbs. of bottled water equals 120 gallons.)Category Gallons used
Soft drinks 185
Fruit drinks 310
Fresh bakery products 210
Frozen bakery (pies, pizza) 320
Fluid dairy 200
Cheese 330
Ice cream 380
Processed meat 1,500
Looking for a reprint of this article?
From high-res PDFs to custom plaques, order your copy today!