Tech Update: Process Control
Citect Ampla MES software allows Ahold Coffee Company to improve overall equipment effectiveness while improving planning and production processes.

Which doesn’t belong in this list: Melamine, Listeria monocytogenes, Salmonella, E. coli, peanuts, OEE, milk, crab, sulfite, soy, wheat, egg? If you have the right process control system in place, your OEE (overall equipment effectiveness) might see a measurable improvement, allowing you to operate more efficiently; and all the others on the list-which have been the subject of nearly endless FDA and voluntary recalls in the last year-would have been flagged by your process control system. Products containing them or with inappropriate labeling wouldn’t get out the door, or if they did, not past the distributor.
Can you afford a recall? Phil Friedman, VP, consumer and life science industries, QAD Inc., has a good friend who worked for FDA, and when he retired, consulted on the Tylenol case for Johnson & Johnson. Friedman’s friend told him, if the Tylenol incident were to happen today (post 9/11), the brand would have gone down. No matter how big the brand, with a major recall, all bets are off, warns Friedman. “Brand loyalty can switch in a heartbeat when it comes to health issues,” he adds.
In a 2008 study AMR Research conducted with 251 food and beverage companies, 63% of respondents increased their brand claims of health and safety and product performance over the past five years. Yet the average company had 178 recalls: 38 for product performance, 36 for allergen-free compliance, 31 for potential contamination, 30 for health and safety, 29 for marketing label issues and 14 for products that don’t perform when aged. Sixty-seven percent of companies with more than $5 billion in revenue had write-offs related to recalls that exceeded $20 million.
According to Vicki Griffith, marketing director, food and beverage, Lawson Software, average processors in the AMR study lose $10 million per year in recalls because they don’t have any proactive mechanisms in place. The average recall takes 34 days for a processor to sense the need for a recall and to act on it (up to 60 days for a health and safety-related recall). By that time, the food has probably left the supply chain. Griffith finds the reason most companies lose this much time and money is that no one person or group is responsible for recalls. Often it’s the marketing department who is responsible for the labels, QA for testing, and so on.
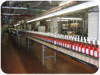
“On process controls,” notes Ed Goldman, senior VP of Foster-Miller, “we’ve been pushing process automation and continuous inspection all through a process. If you can continuously inspect at each step, you can reduce your scrap losses.” Goldman doesn’t consider this rocket science. Instead, he says the pharma industry calls this method process analytical technology (PAT), a method not unlike quality by design. Since most food industry batches are not worth as much money as a drug batch, the stakes aren’t so high. Therefore, it’s tough to sell PAT to the food industry when an analytical instrument costs $10,000-20,000.
“The need to get information from the plant floor on a real-time basis is an important issue,” says George Lipsky, strategic account manager-food and beverage/packaging, Mitsubishi. Processors want to bring key real-time information-not a ton of useless, unprocessed data-from the plant floor into their manufacturing execution system (MES) or ERP system so they can make informed decisions. In the case of a call-back, they need specific batch data so they don’t have to recall everything that was made in the last three months.
Process control is what drives supply chain execution, says Brandon Henning, GE Fanuc Intelligent Platforms food and beverage global industry manager. Most companies in this industry think a reliable supply chain execution strategy is based on a lower-stock inventory and a make-to-demand environment. The problem is, according to Henning, processors can’t achieve this strategy if they can’t count on their operations. Therefore, manufacturers need better process control, higher plant floor visibility and the kind of software systems that will drive their supply chain execution strategy.
For those processors using Windows-based systems, there are some OS-based improvements that will enhance communications between systems and provide new security measures, says Tim Donaldson, director of marketing at Iconics. The new 64-bit OS will provide HMI/SCADA users universal data connectivity through Windows Communication Foundry, enriched user interface with Windows Presentation Foundation, virtual Earth geographical information system (GIS), a Windows Workflow Foundation for secure real-time data communications and a User Account Control (UAC), which prevents unauthorized system changes.

While controls for food processing may not seem as sophisticated as a refinery’s distributed control system (DCS), some of the goals are nevertheless just as critical. According to Charlie Rastle, Rockwell Automation industry manager, controlling the baking of bread through an oven requires achieving specific moisture content and baking temperature for each type of bread and controlling the ambient environmental temperature and humidity as well. Crackers are no different. Their moisture content is a major part of what defines the cracker. Rastle says achieving even finer control of the oven and conveyors while minimizing fluctuations results in more consistent product with less waste.
In Europe, most food and beverage manufacturers use PLCs and are a long way from moving to a DCS, says Nell Burden, industry sales & marketing, Emerson Process Management. She says there are some examples of DeltaV (Emerson’s modular DCS) more frequently in distilleries. “I would have thought that the advantages of the DCS and its batch supervision would have become more attractive, given the need for product security,” says Burden.
But PLCs have been catching up with the DCS in functionality. System and machine builders have been asking PLCs to do more. For example, they handle batching, control robotics, work with vision systems, calculate PID loops, provide motor controls, and have motion/position control capabilities. Thanks to ARC Advisory Group the term, programmable automation controller (PAC), was coined in 2002 to denote a device capable of performing the tasks above, which were normally outside the realm of the PLC. Henning sees PAC as the wave of the future; where it used to take three or four PLCs and other specialized controllers to build a machine or process, now typically one PAC may be needed do the job.
Before PACs became fashionable, most major brand PLCs had plug-in cards for functions like PID or simple motion control, but several PLC vendors have been phasing in PACs. Mitsubishi, according to Lipsky, would rather keep the term PLC, and offer all the functions of a PAC plus a built-in MES capability, which is usually found residing on a higher-level computer. The reason for this is to translate the gobs of data coming from its I/O points into actionable information that can be passed up the ladder to ERP and other MES systems.

“Certainly, OEE is at the forefront of SPC,” says Marianne Steidinger, Wonderware MES/EMI marketing program manager. “OEE has three factors-availability, performance (of equipment/assets) and quality (of product),” she adds. OEE is used by many food manufacturers as a precursor to a “big bang” MES implementation, for it can help them with equipment productivity, product quality and throughput, and equipment availability by eliminating bottlenecks or constraints in the production process.
Advanced process control (APC), once considered as part of a high-end DCS, can be employed with PLCs as well and work in high-value processes such as fermentation. Rockwell recently purchased Pavilion, a provider of APC and model-predictive control (MPC) software. Why use MPC software? Rastle cites dryers as one example. Getting the right final moisture content of a product can be a challenge. Over-drying means selling product with less moisture content (therefore, more product) and wasting energy to boot. Fluidized bed dryers can be tricky to control and operate at maximum efficiency.
Rastle says the difference between the DCS at a chemical plant or refinery and a PLC-based food plant is that once a model is built for a particular DCS process, it doesn’t have to be changed because the product doesn’t often change. At a food plant, recipes are always changing as products are redefined. Therefore, system integrators and suppliers must be available to help with refining or completely redefining process models for manufacturers who may not have qualified people on staff.
ActiveFactory also trends data at Beam’s plant. Trends can be identified and reports can be exported to Microsoft Excel. “In regards to metrics,” says Crosley, “what we’re seeing is a consistency in throughput. Through the trending information, we’re able to tell when problematic areas arise. And by having that information readily available and having it automated, we’re able to take preventative action and maintain a consistent operation.”
When it comes to short batch runs, there can’t be anything much shorter than the specialty candy Mars Direct runs, based on its orders from around the world. People from more than 200 countries have visited www.mymms.com to place orders for personalized M&M candies in quantities as small as 1.5 pounds. According to M&M R&D Director Dan Michael, at times, the company receives more than 1,000 orders per day via the Web site, and each order is a unique batch specified by the customer. The candies can be imprinted with photos uploaded to the Web site, or a special message can be printed on them. After printing, the candies are packaged in any number of options selected by the customer: from small bags with or without ribbons to tins and glass boxes. These M&Ms go through nine inspection steps from the time the candy is produced until it is shipped to the customer.
The Ahold Coffee Company (ACC) is the largest private label coffee roaster in the Netherlands with revenues over 41 billion euros and employees numbering 247,000 globally. With a goal of decreasing the amount and duration of line stoppages without making operational or equipment changes and improving OEE, ACC decided to implement an MES system. The processor wanted to track real-time key performance indicators (KPIs), but it also wanted a system that would easily integrate with its ERP system.
ACC selected Ampla, Citect’s MES solution because its modular architecture provides flexibility and scalability. The project included the installation of planner, downtime, production and metrics modules. The modules seamlessly connected via B2MML (business to manufacturing mark-up language) to ACC’s existing FlexProcess ERP system. The MES software supports the ISA-95 compliant equipment hierarchy tree, a key object on which Level 3 manufacturing operations management activities are applied and from which information flows.
After implementing the MES, Operations Manager Jeroen de Jager objectively identified the goals (“low-hanging fruit”) that should receive the highest priority for eliminating waste and stoppages more efficiently. He addressed the major issues first and then assigned improvement teams to identify and remedy other performance issues. The software allows de Jager to define the relative profitability of the various products ACC produces. For example, some products are relatively inefficient to produce and carry higher labor and downtime costs due to factors such as packaging. By identifying the poorer performers, ACC can more accurately determine actual production costs.
The maintenance staff has been able to confirm that preventative maintenance, in line with packaging equipment vendors’ recommendations, does actually increase the overall equipment availability and, therefore, is worth scheduling. In addition, the number of maintenance staff required to service the lines is more visible as the system records the amount of time the maintenance staff spends on the line. A log of the activities the maintenance staff performs on the line is also stored in the system.
By systematically applying a manufacturing model based on business logic, Steidinger adds, manufacturers can implement a track and trace system that not only tracks raw materials to finished goods, but can add indications such as quality, maintenance/uptime, inventory management, ERP integration for quicker quote to cash cycles, visibility of the manufacturing process for better customer management and order control. And in case of quality issues, faster remediation of quality breaches with a systematic method for capturing data, making decisions, and implementing changes that become part of the genealogy (or record) of the batch can be achieved.
According to Rastle, processors are putting in sensors and data acquisition/logging software products to have the process information necessary to plug into a track and trace system. It’s the critical control points that especially need monitoring, such as cook temperatures and times and CIP parameters.
Henning says new technologies are coming that will further enable track and trace. These include RFID for tracking products once they leave the plant and vision systems used in conjunction with labeling systems to make sure the correct label is on the product with the right identification numbers and/or barcodes.
Finally, the label printing companies are involved as well to make traceability from the farm to the consumer possible. According to Videojet’s Business Unit Manager, Brand Protection Solutions Bob Neagle, software can be used to assign unique numbers that tie a product back to a processor’s database to show where a specific lot of tomatoes originated, and also track them to their final destination.
The tracking software can generate fully random codes, create derived codes and incorporate electronic product code structures, or administer codes pre-generated from outside sources. The software links the codes to intended shipment destinations. The tracking mechanism is crucial as pallets are de-aggregated at remote distribution centers, becoming smaller shipments to the ultimate retail outlet.
With technology increasing in performance and providing more process control capability than ever before, the question is not whether you can afford it. The question is, can you afford a recall? With the right technology in place, you may be able to stop a bad product before it gets out the door. Think of process control as insurance. Can you afford not to have it?
For more information:
Vicki Griffith, Lawson Software, 517-339-8188, vicki.griffith@us.lawson.com
Phil Friedman, QAD Inc., 631-474-2055, phf@qad.com
Ed Goldman, Foster-Miller, 781-684-4145, egoldman@foster-miller.com
Brandon Henning, GE, 434-978-6139, brandon.henning@ge.com
Charlie Rastle, Rockwell, 303-517-8914, cmrastle@ra.rockwell.com
Nell Burden, Emerson Process, +44 7920 587263, nell.burden@emersonprocess.com
George Lipsky, Mitsubishi, 678-963-0893, george.lipsky@meau.com
Maryanne Steidinger, Wonderware, 949-639-8713, maryanne.steidinger@wonderware.com
Tim Donaldson, Iconics, 508-543-8600, timd@iconics.com
Bob Neagle, Videojet, 800-992-2102, x2448, bob.neagle@videojet.com

Citect Ampla MES software allows Ahold Coffee Company to improve overall equipment effectiveness while improving planning and production processes.
Source: Citect.
Source: Citect.
Which doesn’t belong in this list: Melamine, Listeria monocytogenes, Salmonella, E. coli, peanuts, OEE, milk, crab, sulfite, soy, wheat, egg? If you have the right process control system in place, your OEE (overall equipment effectiveness) might see a measurable improvement, allowing you to operate more efficiently; and all the others on the list-which have been the subject of nearly endless FDA and voluntary recalls in the last year-would have been flagged by your process control system. Products containing them or with inappropriate labeling wouldn’t get out the door, or if they did, not past the distributor.
Can you afford a recall? Phil Friedman, VP, consumer and life science industries, QAD Inc., has a good friend who worked for FDA, and when he retired, consulted on the Tylenol case for Johnson & Johnson. Friedman’s friend told him, if the Tylenol incident were to happen today (post 9/11), the brand would have gone down. No matter how big the brand, with a major recall, all bets are off, warns Friedman. “Brand loyalty can switch in a heartbeat when it comes to health issues,” he adds.
In a 2008 study AMR Research conducted with 251 food and beverage companies, 63% of respondents increased their brand claims of health and safety and product performance over the past five years. Yet the average company had 178 recalls: 38 for product performance, 36 for allergen-free compliance, 31 for potential contamination, 30 for health and safety, 29 for marketing label issues and 14 for products that don’t perform when aged. Sixty-seven percent of companies with more than $5 billion in revenue had write-offs related to recalls that exceeded $20 million.
According to Vicki Griffith, marketing director, food and beverage, Lawson Software, average processors in the AMR study lose $10 million per year in recalls because they don’t have any proactive mechanisms in place. The average recall takes 34 days for a processor to sense the need for a recall and to act on it (up to 60 days for a health and safety-related recall). By that time, the food has probably left the supply chain. Griffith finds the reason most companies lose this much time and money is that no one person or group is responsible for recalls. Often it’s the marketing department who is responsible for the labels, QA for testing, and so on.
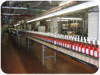
Filled and capped Jim Beam bottles head toward cartoning operations. Wonderware HMI, Historian, InBatch and ActiveFactory allow Jim Beam personnel to control processes consistently and view plant operations in real time. Source: Wonderware.
Defining process control
If you think process control is a closed-loop PID controller or a collection of them, or a PLC running a machine, you need to expand your horizons. “Process control doesn’t necessarily mean it’s about manufacturing,” says Friedman. “Process control is an electronic traceability process to address issues of quality, reliability, quantity, management, etc. I call process control a component of what I describe as a sensor-based computing architecture, which drives every part of a business,” adds Friedman.“On process controls,” notes Ed Goldman, senior VP of Foster-Miller, “we’ve been pushing process automation and continuous inspection all through a process. If you can continuously inspect at each step, you can reduce your scrap losses.” Goldman doesn’t consider this rocket science. Instead, he says the pharma industry calls this method process analytical technology (PAT), a method not unlike quality by design. Since most food industry batches are not worth as much money as a drug batch, the stakes aren’t so high. Therefore, it’s tough to sell PAT to the food industry when an analytical instrument costs $10,000-20,000.
“The need to get information from the plant floor on a real-time basis is an important issue,” says George Lipsky, strategic account manager-food and beverage/packaging, Mitsubishi. Processors want to bring key real-time information-not a ton of useless, unprocessed data-from the plant floor into their manufacturing execution system (MES) or ERP system so they can make informed decisions. In the case of a call-back, they need specific batch data so they don’t have to recall everything that was made in the last three months.
Process control is what drives supply chain execution, says Brandon Henning, GE Fanuc Intelligent Platforms food and beverage global industry manager. Most companies in this industry think a reliable supply chain execution strategy is based on a lower-stock inventory and a make-to-demand environment. The problem is, according to Henning, processors can’t achieve this strategy if they can’t count on their operations. Therefore, manufacturers need better process control, higher plant floor visibility and the kind of software systems that will drive their supply chain execution strategy.
For those processors using Windows-based systems, there are some OS-based improvements that will enhance communications between systems and provide new security measures, says Tim Donaldson, director of marketing at Iconics. The new 64-bit OS will provide HMI/SCADA users universal data connectivity through Windows Communication Foundry, enriched user interface with Windows Presentation Foundation, virtual Earth geographical information system (GIS), a Windows Workflow Foundation for secure real-time data communications and a User Account Control (UAC), which prevents unauthorized system changes.

Autobake, manufacturer of automated baking ovens, uses Rockwell and Siemens PLCs and Wonderware software to create automated baking systems for their food manufacturing customers. The ovens provide data logging of process values and a historical audit trail of alarms and events. Source: Wonderware.
Improve the process
Processors who begin to automate or think about automating using software like Wonderware find themselves putting in equipment like valve actuators and sensors to work with the software. Beam Global Spirits and Wine began upgrading its Clermont, KY plant in 1992 with Wonderware software, based on its ability to work with existing PLCs, and it is still upgrading to new functionality. “Prior to Wonderware, a lot of the processes were manual,” says Nathan Crosley, operations manager. “We would have to manually turn on valves, switches and pumps. The software allows the operators to control the process from one location. And that gives us a lot of consistency.”While controls for food processing may not seem as sophisticated as a refinery’s distributed control system (DCS), some of the goals are nevertheless just as critical. According to Charlie Rastle, Rockwell Automation industry manager, controlling the baking of bread through an oven requires achieving specific moisture content and baking temperature for each type of bread and controlling the ambient environmental temperature and humidity as well. Crackers are no different. Their moisture content is a major part of what defines the cracker. Rastle says achieving even finer control of the oven and conveyors while minimizing fluctuations results in more consistent product with less waste.
In Europe, most food and beverage manufacturers use PLCs and are a long way from moving to a DCS, says Nell Burden, industry sales & marketing, Emerson Process Management. She says there are some examples of DeltaV (Emerson’s modular DCS) more frequently in distilleries. “I would have thought that the advantages of the DCS and its batch supervision would have become more attractive, given the need for product security,” says Burden.
But PLCs have been catching up with the DCS in functionality. System and machine builders have been asking PLCs to do more. For example, they handle batching, control robotics, work with vision systems, calculate PID loops, provide motor controls, and have motion/position control capabilities. Thanks to ARC Advisory Group the term, programmable automation controller (PAC), was coined in 2002 to denote a device capable of performing the tasks above, which were normally outside the realm of the PLC. Henning sees PAC as the wave of the future; where it used to take three or four PLCs and other specialized controllers to build a machine or process, now typically one PAC may be needed do the job.
Before PACs became fashionable, most major brand PLCs had plug-in cards for functions like PID or simple motion control, but several PLC vendors have been phasing in PACs. Mitsubishi, according to Lipsky, would rather keep the term PLC, and offer all the functions of a PAC plus a built-in MES capability, which is usually found residing on a higher-level computer. The reason for this is to translate the gobs of data coming from its I/O points into actionable information that can be passed up the ladder to ERP and other MES systems.

You are the customer with Mars’ MyM&Ms (www.mymms.com). You create a batch to your specifications with art and text, pick the colors, and choose the packaging. Mars picks and prints your candy, then packages and ships your order. Source: Mars Inc.
SPC and APC
Statistical process control (SPC) is perhaps best known for controlling give-aways, i.e., monitoring product weights. According to Richard K. Morris, Zontec Inc. marketing manager, SPC can help processors reduce costs, increase yields and achieve parts-per-million quality to raise overall corporate profitability. SPC modules provide real-time dashboard views of global processes for decision support at both production and executive levels. SPC systems can usually be integrated with external systems such as SCADA, ERP, LIMS and OPC servers.“Certainly, OEE is at the forefront of SPC,” says Marianne Steidinger, Wonderware MES/EMI marketing program manager. “OEE has three factors-availability, performance (of equipment/assets) and quality (of product),” she adds. OEE is used by many food manufacturers as a precursor to a “big bang” MES implementation, for it can help them with equipment productivity, product quality and throughput, and equipment availability by eliminating bottlenecks or constraints in the production process.
Advanced process control (APC), once considered as part of a high-end DCS, can be employed with PLCs as well and work in high-value processes such as fermentation. Rockwell recently purchased Pavilion, a provider of APC and model-predictive control (MPC) software. Why use MPC software? Rastle cites dryers as one example. Getting the right final moisture content of a product can be a challenge. Over-drying means selling product with less moisture content (therefore, more product) and wasting energy to boot. Fluidized bed dryers can be tricky to control and operate at maximum efficiency.
Rastle says the difference between the DCS at a chemical plant or refinery and a PLC-based food plant is that once a model is built for a particular DCS process, it doesn’t have to be changed because the product doesn’t often change. At a food plant, recipes are always changing as products are redefined. Therefore, system integrators and suppliers must be available to help with refining or completely redefining process models for manufacturers who may not have qualified people on staff.
Batch processes
Batching capabilities, once routinely handled by a DCS, are handled by PLCs in software. At Beam, Wonderware’s InBatch batch management software is a key component for reliable product quality. Before the bourbon is distilled and bottled, the software enforces recipe procedures and verifies that operators execute activities in the proper sequence, such as sending the correct measures of grains to specific silos, adding water to form a mash and introducing yeast as well as cooking and fermenting.ActiveFactory also trends data at Beam’s plant. Trends can be identified and reports can be exported to Microsoft Excel. “In regards to metrics,” says Crosley, “what we’re seeing is a consistency in throughput. Through the trending information, we’re able to tell when problematic areas arise. And by having that information readily available and having it automated, we’re able to take preventative action and maintain a consistent operation.”
When it comes to short batch runs, there can’t be anything much shorter than the specialty candy Mars Direct runs, based on its orders from around the world. People from more than 200 countries have visited www.mymms.com to place orders for personalized M&M candies in quantities as small as 1.5 pounds. According to M&M R&D Director Dan Michael, at times, the company receives more than 1,000 orders per day via the Web site, and each order is a unique batch specified by the customer. The candies can be imprinted with photos uploaded to the Web site, or a special message can be printed on them. After printing, the candies are packaged in any number of options selected by the customer: from small bags with or without ribbons to tins and glass boxes. These M&Ms go through nine inspection steps from the time the candy is produced until it is shipped to the customer.
Managing it all
According to Steidinger, “Processors are realizing that they must do more with less. Rather than build another plant, manufacturers are looking at their existing equipment to determine if they can increase productivity of a line or plant.” By using software that provides OEE measurements, processors not only gain more productivity, they also start to understand where the weaknesses and bottlenecks are in their plant. They learn where improvements can be made in a focused manner and to use their capital equipment funds in a way that ensures faster ROI.The Ahold Coffee Company (ACC) is the largest private label coffee roaster in the Netherlands with revenues over 41 billion euros and employees numbering 247,000 globally. With a goal of decreasing the amount and duration of line stoppages without making operational or equipment changes and improving OEE, ACC decided to implement an MES system. The processor wanted to track real-time key performance indicators (KPIs), but it also wanted a system that would easily integrate with its ERP system.
ACC selected Ampla, Citect’s MES solution because its modular architecture provides flexibility and scalability. The project included the installation of planner, downtime, production and metrics modules. The modules seamlessly connected via B2MML (business to manufacturing mark-up language) to ACC’s existing FlexProcess ERP system. The MES software supports the ISA-95 compliant equipment hierarchy tree, a key object on which Level 3 manufacturing operations management activities are applied and from which information flows.
After implementing the MES, Operations Manager Jeroen de Jager objectively identified the goals (“low-hanging fruit”) that should receive the highest priority for eliminating waste and stoppages more efficiently. He addressed the major issues first and then assigned improvement teams to identify and remedy other performance issues. The software allows de Jager to define the relative profitability of the various products ACC produces. For example, some products are relatively inefficient to produce and carry higher labor and downtime costs due to factors such as packaging. By identifying the poorer performers, ACC can more accurately determine actual production costs.
The maintenance staff has been able to confirm that preventative maintenance, in line with packaging equipment vendors’ recommendations, does actually increase the overall equipment availability and, therefore, is worth scheduling. In addition, the number of maintenance staff required to service the lines is more visible as the system records the amount of time the maintenance staff spends on the line. A log of the activities the maintenance staff performs on the line is also stored in the system.
Track and trace
Recalls can put a real dent on a processor’s profit. But the same software that helps with track and trace provides other business benefits. Griffith says many of Lawson’s food and beverage customers who are using the M3 Trace Engine also use it to set up production lines to manage quality processes across the entire chain. Processors are able to see if there is a change in a process or a forgotten step in a batch sequence. The software can also be used to compare one line or plant against another, or it can be used to determine what procedures and ingredients made the best batch.By systematically applying a manufacturing model based on business logic, Steidinger adds, manufacturers can implement a track and trace system that not only tracks raw materials to finished goods, but can add indications such as quality, maintenance/uptime, inventory management, ERP integration for quicker quote to cash cycles, visibility of the manufacturing process for better customer management and order control. And in case of quality issues, faster remediation of quality breaches with a systematic method for capturing data, making decisions, and implementing changes that become part of the genealogy (or record) of the batch can be achieved.
According to Rastle, processors are putting in sensors and data acquisition/logging software products to have the process information necessary to plug into a track and trace system. It’s the critical control points that especially need monitoring, such as cook temperatures and times and CIP parameters.
Henning says new technologies are coming that will further enable track and trace. These include RFID for tracking products once they leave the plant and vision systems used in conjunction with labeling systems to make sure the correct label is on the product with the right identification numbers and/or barcodes.
Finally, the label printing companies are involved as well to make traceability from the farm to the consumer possible. According to Videojet’s Business Unit Manager, Brand Protection Solutions Bob Neagle, software can be used to assign unique numbers that tie a product back to a processor’s database to show where a specific lot of tomatoes originated, and also track them to their final destination.
The tracking software can generate fully random codes, create derived codes and incorporate electronic product code structures, or administer codes pre-generated from outside sources. The software links the codes to intended shipment destinations. The tracking mechanism is crucial as pallets are de-aggregated at remote distribution centers, becoming smaller shipments to the ultimate retail outlet.
With technology increasing in performance and providing more process control capability than ever before, the question is not whether you can afford it. The question is, can you afford a recall? With the right technology in place, you may be able to stop a bad product before it gets out the door. Think of process control as insurance. Can you afford not to have it?
For more information:
Vicki Griffith, Lawson Software, 517-339-8188, vicki.griffith@us.lawson.com
Phil Friedman, QAD Inc., 631-474-2055, phf@qad.com
Ed Goldman, Foster-Miller, 781-684-4145, egoldman@foster-miller.com
Brandon Henning, GE, 434-978-6139, brandon.henning@ge.com
Charlie Rastle, Rockwell, 303-517-8914, cmrastle@ra.rockwell.com
Nell Burden, Emerson Process, +44 7920 587263, nell.burden@emersonprocess.com
George Lipsky, Mitsubishi, 678-963-0893, george.lipsky@meau.com
Maryanne Steidinger, Wonderware, 949-639-8713, maryanne.steidinger@wonderware.com
Tim Donaldson, Iconics, 508-543-8600, timd@iconics.com
Bob Neagle, Videojet, 800-992-2102, x2448, bob.neagle@videojet.com
Looking for a reprint of this article?
From high-res PDFs to custom plaques, order your copy today!