5th Annual Replacement Parts and Components Survey: Processors Take a Cost-Driven Approach
Real-time
ordering and the growing role of the purchasing department are among the trends
in FE’s annual study.

Call
it collaboration or a greater focus on cost, but the role of purchasing
managers in the spare parts and components process clearly is growing,
according to Food Engineering’s Replacement Parts and Components Trends Survey.
A sample of Food Engineering readers was surveyed earlier this year, marking the fifth year the magazine has taken the measure of MRO automation practices and strategies at North America’s food and beverage companies. The survey provides insight into how food professionals source parts, evaluate suppliers and try to optimize up-time performance at their facilities.
The growing role of financial managers in the parts replenishment process is clear based on responses to a question asking which job functions are involved in various aspects of purchase decisions. When it comes to recommending or evaluating suppliers, brands and models, purchasing was involved at 32 percent of respondents’ plants, up from 18 percent in 2003. In contrast, engineering was involved at 58 percent of plants, down from 68 percent in 2003. Maintenance’s involvement slipped to 66 percent, down from 72 percent.
Purchasing also is more involved in P/O approval, signing off 36 percent of the time, up from 25 percent in 2003. Involvement by both maintenance and engineering declined steadily over the past four years. Engineering also was less likely to have any involvement in parts decisions, with no role at one in five plants, down from one in eight in 2003. Conversely, purchasing was more likely to be involved.
R&D professionals also are becoming more involved in the replacement process, though in different areas than purchasing. At 26 percent of plants, R&D helps determine need, up six points from 2003. R&D also doubled its involvement in order placement, though the input is infrequent (6 percent of plants).
While the IT department is the least likely of nine functional areas to be involved in replacement, the growing use of asset-management systems demands some input from information professionals. Product specification development, needs determination and evaluation/recommendation of models and suppliers involve IT one-sixth of the time, according to respondents.
A cost-driven mindset presumably results in stocking less durable parts and equipment, and there is some evidence of that in the survey. Asked how they reconcile the cost of high-quality parts that may provide longer life than less costly alternatives, 38 percent of respondents checked the option, “Most parts are commodities, with price the determining factor when specifying replacements.” An equal number indicated, “We have quantified the maintenance costs of most machinery parts and are able to calculate ROI in higher quality parts.” Almost one in five checked, “Manpower shortages force us to specify the highest available quality parts to prolong mean time to failure.”
The tradeoffs between quality and price can be complex, and a number of food professionals offered insights to their approach. “Unless the original part failed prematurely, the replacement part is from the original OEM,” one wrote. “Potential loss from failure and time to replace are considered along with costs,” said another. “Minimizing downtime is our driver,” one noted simply.
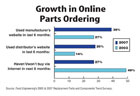
Willingness to purchase from a website is more common among smaller firms: almost two-thirds of respondents from plants with fewer than 100 employees bought parts from a website in the last six months. Workers at facilities with 1,000 or more employees are by far the least likely group to purchase online.
As the Internet grows as a business-to-business tool, the demand for accurate information rises. “Keep their websites up-to-date” was a frequent response to the question, What actions can OEMs take to better satisfy end users? “Make all manuals on CDs or via Internet,” one professional wrote. “Provide more detailed, accurate, up-to-date electronic parts information,” another urged. Exploded-view schematics, preventive/predictive maintenance routines and electronic bill of materials are other point-and-click options with a swelling demand.
Lower prices were easily the most frequently cited customer-satisfaction desire, but higher quality also is in demand. Improved technical and customer support is another area for OEM improvement, along with better parts availability. Domestic sourcing is a particular problem when a machine is made outside the US, one maintenance professional complained. “Make parts interchangeable,” another suggested.
Knowledgeable technical representatives are requested by a respondent who would appreciate an OEM who “understood our application, rather than promising the sky.” Another wants manufacturers to track his purchase records “to prevent mis-purchases and for recommendations for improvements.” One pleads, “Eliminate voice mail.”
Better technical support is a priority for many maintenance professionals, with 82 percent rating it very or extremely important. In fact, it is now more important than company reputation and prior relationships when selecting a parts supplier. The most important supplier characteristics are product quality, on-time delivery, product availability, delivery speed and value for price.
When it comes to maintenance-management strategies, end-user size matters. Parts P/Os are generated automatically at the vast majority of plants with 500 or more employees but at barely one in 10 of those with fewer than 100 workers. In fact, no automation exists at seven out of 10 small plants, while the same is true at only a handful of large plants.
Inventory dollar value remains the most popular tracking system used in food, with the largest plants most likely to use it. Big facilities also are the most likely to outsource inventory management to local supply houses. Remanufacturing or re-engineering of parts to reduce costs or improve performance remains the most popular MRO inventory practice, particularly at plants with 500-999 workers. Vendor-managed inventory is used at three out of five 1,000-plus employee plants, significantly more than any other category. Consignment is twice as likely to be used at large plants than at smaller facilities.
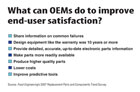
With more maintenance managers saying, “Google me a valve,” it’s not surprising that 43 percent of respondents use web search engines to get parts information, and 51 percent click on supplier websites (45 percent visit distributors’ websites). Supplier literature, on the other hand, has slipped to the fifth most popular information source, down from number one in 2003 and 2004. Only 47 percent of respondents indicate they use supplier literature.
Supplier sales and customer service personnel are the most popular information sources, surpassing even peers within food professionals’ own companies.
FedEx vaulted ahead of UPS as the preferred delivery service for time-critical parts deliveries, with two-thirds indicating they recommend or request FedEx. UPS slipped slightly and is recommended by three-fifths, and DHL plummeted nine points to 13 percent. Other mentions included taxicabs and delivery by a salesperson. U
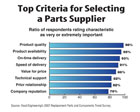
Respondents from plants employing 1,000 or more full- and part-time workers represented 13 percent of the sample. Plants with fewer than 100 employees constituted 12 percent of the base. As in previous surveys, the majority (60 percent) worked at plants with 100-499 employees.
Engineering was the job function of 26 percent of respondents, followed by maintenance (23 percent), plant operations (20 percent), general administration/executive management (19 percent) and purchasing (9 percent). The remainder were in quality assurance, R&D and support roles. No IT professionals participated in the survey.
Processors of meat, poultry and seafood accounted for 24 percent of returned surveys, followed by bakery products and miscellaneous (coffee, snacks, pasta, spices, etc.), both at 12 percent. The rest were scattered over eight categories, including beverages (10 percent) and dairy products (10 percent).

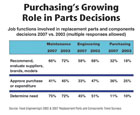
A sample of Food Engineering readers was surveyed earlier this year, marking the fifth year the magazine has taken the measure of MRO automation practices and strategies at North America’s food and beverage companies. The survey provides insight into how food professionals source parts, evaluate suppliers and try to optimize up-time performance at their facilities.
The growing role of financial managers in the parts replenishment process is clear based on responses to a question asking which job functions are involved in various aspects of purchase decisions. When it comes to recommending or evaluating suppliers, brands and models, purchasing was involved at 32 percent of respondents’ plants, up from 18 percent in 2003. In contrast, engineering was involved at 58 percent of plants, down from 68 percent in 2003. Maintenance’s involvement slipped to 66 percent, down from 72 percent.
Purchasing also is more involved in P/O approval, signing off 36 percent of the time, up from 25 percent in 2003. Involvement by both maintenance and engineering declined steadily over the past four years. Engineering also was less likely to have any involvement in parts decisions, with no role at one in five plants, down from one in eight in 2003. Conversely, purchasing was more likely to be involved.
R&D professionals also are becoming more involved in the replacement process, though in different areas than purchasing. At 26 percent of plants, R&D helps determine need, up six points from 2003. R&D also doubled its involvement in order placement, though the input is infrequent (6 percent of plants).
While the IT department is the least likely of nine functional areas to be involved in replacement, the growing use of asset-management systems demands some input from information professionals. Product specification development, needs determination and evaluation/recommendation of models and suppliers involve IT one-sixth of the time, according to respondents.
A cost-driven mindset presumably results in stocking less durable parts and equipment, and there is some evidence of that in the survey. Asked how they reconcile the cost of high-quality parts that may provide longer life than less costly alternatives, 38 percent of respondents checked the option, “Most parts are commodities, with price the determining factor when specifying replacements.” An equal number indicated, “We have quantified the maintenance costs of most machinery parts and are able to calculate ROI in higher quality parts.” Almost one in five checked, “Manpower shortages force us to specify the highest available quality parts to prolong mean time to failure.”
The tradeoffs between quality and price can be complex, and a number of food professionals offered insights to their approach. “Unless the original part failed prematurely, the replacement part is from the original OEM,” one wrote. “Potential loss from failure and time to replace are considered along with costs,” said another. “Minimizing downtime is our driver,” one noted simply.
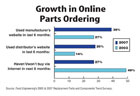
Web is the way
There’s something to this newfangled World Wide Web, the survey demonstrates. Parts purchases from manufacturers’ and distributors’ websites have steadily increased since 2003, with 39 percent of companies buying from OEM sites and 28 percent from distributor sites in the last six months. The comparable numbers four years ago were 27 percent and 14 percent. Conversely, those that haven’t and don’t intend to buy on-line is down to a quarter of respondents, half the proportion four years ago.Willingness to purchase from a website is more common among smaller firms: almost two-thirds of respondents from plants with fewer than 100 employees bought parts from a website in the last six months. Workers at facilities with 1,000 or more employees are by far the least likely group to purchase online.
As the Internet grows as a business-to-business tool, the demand for accurate information rises. “Keep their websites up-to-date” was a frequent response to the question, What actions can OEMs take to better satisfy end users? “Make all manuals on CDs or via Internet,” one professional wrote. “Provide more detailed, accurate, up-to-date electronic parts information,” another urged. Exploded-view schematics, preventive/predictive maintenance routines and electronic bill of materials are other point-and-click options with a swelling demand.
Lower prices were easily the most frequently cited customer-satisfaction desire, but higher quality also is in demand. Improved technical and customer support is another area for OEM improvement, along with better parts availability. Domestic sourcing is a particular problem when a machine is made outside the US, one maintenance professional complained. “Make parts interchangeable,” another suggested.
Knowledgeable technical representatives are requested by a respondent who would appreciate an OEM who “understood our application, rather than promising the sky.” Another wants manufacturers to track his purchase records “to prevent mis-purchases and for recommendations for improvements.” One pleads, “Eliminate voice mail.”
Better technical support is a priority for many maintenance professionals, with 82 percent rating it very or extremely important. In fact, it is now more important than company reputation and prior relationships when selecting a parts supplier. The most important supplier characteristics are product quality, on-time delivery, product availability, delivery speed and value for price.
When it comes to maintenance-management strategies, end-user size matters. Parts P/Os are generated automatically at the vast majority of plants with 500 or more employees but at barely one in 10 of those with fewer than 100 workers. In fact, no automation exists at seven out of 10 small plants, while the same is true at only a handful of large plants.
Inventory dollar value remains the most popular tracking system used in food, with the largest plants most likely to use it. Big facilities also are the most likely to outsource inventory management to local supply houses. Remanufacturing or re-engineering of parts to reduce costs or improve performance remains the most popular MRO inventory practice, particularly at plants with 500-999 workers. Vendor-managed inventory is used at three out of five 1,000-plus employee plants, significantly more than any other category. Consignment is twice as likely to be used at large plants than at smaller facilities.
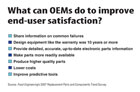
Size-driven strategies
Replacement strategies also show a plant-size bias. Regularly scheduled visual inspections determine when worn parts are replaced at 53 percent of all plants, but only a third of the biggest facilities use this method: at those plants, automated monitoring of parts and components is making inroads, though still at only a small minority. Run to failure remains the maintenance philosophy at one quarter of small and mid-sized plants.With more maintenance managers saying, “Google me a valve,” it’s not surprising that 43 percent of respondents use web search engines to get parts information, and 51 percent click on supplier websites (45 percent visit distributors’ websites). Supplier literature, on the other hand, has slipped to the fifth most popular information source, down from number one in 2003 and 2004. Only 47 percent of respondents indicate they use supplier literature.
Supplier sales and customer service personnel are the most popular information sources, surpassing even peers within food professionals’ own companies.
FedEx vaulted ahead of UPS as the preferred delivery service for time-critical parts deliveries, with two-thirds indicating they recommend or request FedEx. UPS slipped slightly and is recommended by three-fifths, and DHL plummeted nine points to 13 percent. Other mentions included taxicabs and delivery by a salesperson. U
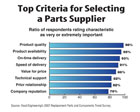
Sidebar
Survey responses were received from 235 food manufacturing professionals earlier this year. Respondents were involved in $480 million worth of replacement parts and components purchases in 2006.Respondents from plants employing 1,000 or more full- and part-time workers represented 13 percent of the sample. Plants with fewer than 100 employees constituted 12 percent of the base. As in previous surveys, the majority (60 percent) worked at plants with 100-499 employees.
Engineering was the job function of 26 percent of respondents, followed by maintenance (23 percent), plant operations (20 percent), general administration/executive management (19 percent) and purchasing (9 percent). The remainder were in quality assurance, R&D and support roles. No IT professionals participated in the survey.
Processors of meat, poultry and seafood accounted for 24 percent of returned surveys, followed by bakery products and miscellaneous (coffee, snacks, pasta, spices, etc.), both at 12 percent. The rest were scattered over eight categories, including beverages (10 percent) and dairy products (10 percent).
Looking for a reprint of this article?
From high-res PDFs to custom plaques, order your copy today!