Embrace both architectures
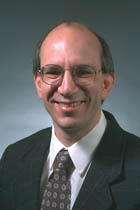

OEMs must identify an architecture that integrates a variety of actuators and sensors from a host of suppliers while also considering integration with the entire information layer in an organization. The benefits of an open modular architecture in automation systems allow new technologies to be incrementally introduced or existing systems to be selectively enhanced rather than replaced completely. Well-defined machine control architectures can significantly lower the cost of business for OEMs designing and building production machinery. Long ago, OEMs identified the benefits of using component architectures whether in electronic hardware systems, software development, or mechanical subsystems. Modularity and reusability have been a long standing practice in the OEM community.
Machine builders should create a selection matrix that helps to objectively compare and contrast the benefits of specific system architectures, as the optimized machine control architecture selection for production machinery is greatly influenced by machine construction and performance requirements. Sometimes these factors are ignored and strong statements are made today in the market in favor of distributed architecture as being the architecture of the future, almost pointing to a demise of centralized architecture.
An overall machine control architecture can be more complex to achieve a desired performance. For example, centralized architecture within distributed architecture may be the most optimized solution for some machine configurations where part of a machine section must be tightly coordinated, requiring centralized motion control. In many motion control applications, an important aspect is to determine a level at which decentralization must occur for optimization, for example at the motion controller level or servo drive level.
Embracing both architectures can create optimum solutions. Consequently, both centralized and distributed architectures will continue to exist for motion control solutions. Many distributed solutions seek the obvious benefit of putting intelligence closer to where the actuation occurs, thereby reducing cabling, minimizing the overall size of the electrical cabinets, and enabling the machinery to be more modular. Thus, many solutions characterized as distributed are really centralized in disguise. A truly distributed system allows for each intelligent device to initiate an action or simply send out an unsolicited message. These types of distributed architectures leverage multi-master networking capabilities. However, the current state of the technology in motion control networks has not adequately addressed the multi-master configuration as an alternative. The multi-master capabilities will simply make a distributed architecture more robust by adding another dimension which will simplify the overall machine control problem by ensuring that distributed devices will play a more active role in machine control.
The discussion about whether to adopt centralized or distributed architectures for motion control solutions continues to be debated. The truth, as usual, is it depends.
Sal Spada is Research Director at ARC Advisory Group. His areas of expertise include real-time, object-oriented software design and development applied to motion control systems. He can be reached at sspada@arcweb.com.
Looking for a reprint of this article?
From high-res PDFs to custom plaques, order your copy today!