It's not just what's inside that counts
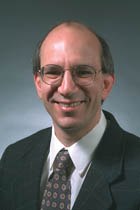
New materials, container sizes and labeling requirements can significantly impact the ability to reconfigure a line.
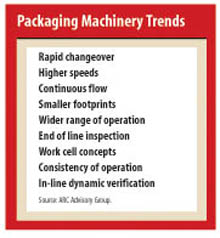
Automation suppliers have responded to these needs with the evolution of 3rd Generation Packaging Controls (3GC) that integrate logic, HMI and motion control functions for packaging machinery. The market is shifting from hardware to software integration and improving the overall reliability and flexibility of solutions. Networking has also increased in importance in machine control architectures as both I/O and servo drives are distributed throughout machinery over high-speed networks. In effect, intelligence is leading to increasingly modular architectures.
There are numerous benefits from network centric mechatronic solutions. Machines are simply safer to operate and provide a greater amount of uptime due to their increased reliability. Footprints have become significantly smaller as electronic motion simplifies many mechanical designs. Users are also finding that there is a much higher return on assets as a result of improved machine reliability and lower maintenance cycles.
The content of digitally controlled subsystems has increased with the integration of servos to replace a myriad of mechanical solutions such as magnetic clutches on bottle cappers or line shafts and gear boxes on flow wrappers and cartoners. End users are seeking to minimize capital costs by purchasing machines that have a wider range of operation. This is critical in reconfiguring machinery for new types of materials used to seal blister packs, tubular packages or bottles. Flexible packaging lines with rapid changeover featuring tool-less changeover technologies are at the heart of this achievement, where the capabilities of electronic servos are being leveraged to accommodate the variability in the process.
The benefits of all electronic machine control are evident in reduced changeover time, cleaner operation, and ease of production data tracking for regulated electronic records. It is a new dimension of flexibility available from electronic machine control that is invading the packaging domain. Machine modularity is allowing manufacturers to configure manufacturing systems based on functional subsystems. It is also driving the inclusion of robotics to allow another dimension of flexibility on the packaging line. Agility versus fixed configurations is becoming a viable alternative that is enabling manufacturers to achieve a greater degree of flexibility and rapid changeover as packaging lines transform.
Sal Spada is research director at ARC Advisory Group. His areas of expertise include real-time, object-oriented software design and development applied to motion control systems. He can be reached at sspada@arcweb.com.
Looking for a reprint of this article?
From high-res PDFs to custom plaques, order your copy today!