Trash talking in meat processing
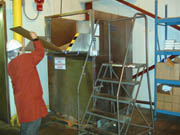
"We had four full-time employees covering two eight-hour shifts every day just to handle our waste," says John Fischer, plant manager for Advance Brands, which is jointly owned by Excel Corporation, Cargill Inc.'s meat business and Advance Food Company. "The debris from unpacking our raw materials filled a trash cart every 20 minutes."
The increased waste, and the manpower required to handle it, reduced the company's efficiency. Three times every hour, a worker had to haul away a full cart of waste and replace it with an empty one. Debris filled the plant. And even with employees exercising care, the waste caused safety concerns. "When all of the steps in the waste process were factored in - shuttling the carts, crushing the debris, dealing with the amount of space all the trash occupied - it was obvious we needed a more cost-effective and labor-saving solution," said Fischer.
To reduce the spread of debris, the company decided collecting the trash at the source of the waste would offer the safest and most cost-effective solution. Advance Brands selected a waste compactor, the KenBay Rotorpac, to help contain the waste in one location.
"We decided to overhaul our plant with a $15 million upgrade," says Tim DeLarm, vice president of engineering, "We can handle 60 million pounds of product annually and like anyone in our business, we generate a lot of waste, but the Rotorpac makes it very manageable."
The Rotorpac's small footprint - it occupies about the same floor space as a standard pallet - enabled the plant to locate it at the start of the production process. Meat is removed from the receiving coolers, checked in, weighed, assigned a barcode, and then unpacked for formulation and blending. The compactor receives the cardboard debris of the boxed meat from a chute at the top of the unit, a feature designed especially for the plant to handle the tremendous amount of cardboard that results from its production process. All four of the plant's compactors are stainless steel to help simplify sanitation and make it easier for the plant to meet food safety requirements.
The KenBay equipment has enhanced the entire Advance Brands operation. "With innovations like this," said Fischer, "it's no wonder we have increased sales more than 20 times in the last decade. We've found the right ingredients."
For more information:
KenBay Rotorpac, 888-353-6229
www.kenbay.com
Looking for a reprint of this article?
From high-res PDFs to custom plaques, order your copy today!