The French fry connection
With more than 55 production facilities on six continents, McCain Foods in Florenceville, NB, is the world's largest manufacturer of frozen French fries, selling its products in more than 110 countries. Production quantities are measured in tons per hour, yet quality is paramount.
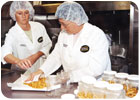
To ensure efficiency of its production line, McCain developed an internal key performance indicator (KPI), called Recovery, which calculates the yield from a quantity of raw material. The metric results are intended to help managers determine what modifications are needed to increase line production.
McCain plant managers initially maintained the Recovery KPI in a static database application that was difficult to access and only yielded results in hourly time increments. As a result, managers weren't able to identify and fix problems in real-time.
For this reason, McCain decided to deploy enterprise manufacturing intelligence software from Activplant Corporation. On a trial basis, the software was installed in the company's Easton, ME, plant, which is one of its largest facilities. More than fifty machines and stations are involved in the French fry production process, performing every task from peeling and cutting to frying and freezing. The machines run 24/7. In one hour, the largest production lines can produce 25 tons of finished product.
With Activplant in place, information is readily accessible and real-time metrics can be used to drive operational excellence and continuous improvement.
"By producing real-time results, engineers no longer have to wait to see if there's a production problem," says Guy Metivier, manager of manufacturing execution systems at McCain's Global Technology Center. "Plant personnel can now get up-to-the-minute results and make corrections immediately with a resulting improvement in the Recovery KPI."
Unlike McCain's earlier system, the Activplant solution is dynamic, controllable and maintainable by each plant. McCain expects greatly reduced application maintenance costs, as existing plant resources will maintain and modify the Activplant solution without having to hire expensive IT or consulting resources.
Based on the success in the Easton facility, McCain is ready to implement the software throughout its facilities worldwide. "We will use Activplant anywhere our manufacturing technology permits," says Metivier.
For more information: Kyle Solomon, Activplant Corp.;
519-668-7336; ksolomon@activplant.com
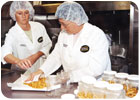
Enterprise manufacturing intelligence software from Activplant helps McCain obtain real-time metrics that can be used to drive operational excellence and continuous improvement in its French fry producing operations. Source: McCain.
To ensure efficiency of its production line, McCain developed an internal key performance indicator (KPI), called Recovery, which calculates the yield from a quantity of raw material. The metric results are intended to help managers determine what modifications are needed to increase line production.
McCain plant managers initially maintained the Recovery KPI in a static database application that was difficult to access and only yielded results in hourly time increments. As a result, managers weren't able to identify and fix problems in real-time.
For this reason, McCain decided to deploy enterprise manufacturing intelligence software from Activplant Corporation. On a trial basis, the software was installed in the company's Easton, ME, plant, which is one of its largest facilities. More than fifty machines and stations are involved in the French fry production process, performing every task from peeling and cutting to frying and freezing. The machines run 24/7. In one hour, the largest production lines can produce 25 tons of finished product.
With Activplant in place, information is readily accessible and real-time metrics can be used to drive operational excellence and continuous improvement.
"By producing real-time results, engineers no longer have to wait to see if there's a production problem," says Guy Metivier, manager of manufacturing execution systems at McCain's Global Technology Center. "Plant personnel can now get up-to-the-minute results and make corrections immediately with a resulting improvement in the Recovery KPI."
Unlike McCain's earlier system, the Activplant solution is dynamic, controllable and maintainable by each plant. McCain expects greatly reduced application maintenance costs, as existing plant resources will maintain and modify the Activplant solution without having to hire expensive IT or consulting resources.
Based on the success in the Easton facility, McCain is ready to implement the software throughout its facilities worldwide. "We will use Activplant anywhere our manufacturing technology permits," says Metivier.
For more information: Kyle Solomon, Activplant Corp.;
519-668-7336; ksolomon@activplant.com
Looking for a reprint of this article?
From high-res PDFs to custom plaques, order your copy today!