Packaging Trends Survey: Priority Shift in Food Packaging Industry
Speed always is a priority in packaging operations, but market realities are elevating other considerations for food and beverage professionals.
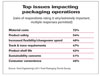
Scrambling to keep up with production, bonuses based on total throughput, dealing with line hiccups: Those were the good old days in food and beverage packaging.
Today’s supervisors, engineers and other packaging professionals have a lot more on their plate as they cope with the sometimes contradictory demands of customers, the supply chain and senior management. Based on reader feedback to Food Engineering’s packaging trends survey, today’s pressures are forcing a reshuffling of priorities and a renewed focus on changes designed to improve overall performance.
An example of the shift in priorities is the ratings of 17 issues and their impact on packaging operations in the next two years. Product safety consistently has ranked second over the years, but the gap between safety and material costs is widening, with barely half the readers believing safety will have a big or great impact, with a comparable number judging machine flexibility and changeover speed to be a big-impact issue. By comparison, 71 percent say material costs will have a big impact.
Asked what actions their companies are pursuing to boost equipment availability, three in five survey respondents cite greater operator involvement in routine maintenance. The second most popular strategy is greater OEM involvement in maintenance training, though only 22 percent are taking that approach. Additional equipment-availability initiatives with similar support are training and education by outside experts and expanded maintenance staffing. Readers volunteer ISO 9000:2008 certification and “implementation of TPM pillars-skills development, focused improvement, autonomous and preventative maintenance, vertical startup, loss analytics, etc.” as elements of improved availability.
Overall equipment efficiency is the metric of choice for evaluating machine performance, not only in production but packaging, as well. Almost half (48 percent) of readers say OEE is driving continuous improvement in packaging. One in five cites increased reliability, and one in 10 focuses on faster changeovers. Improved maintenance procedures are being sought by 8 percent, and another 7 percent are zeroing in on reductions in product giveaway.
Hygienic machine design is a priority throughout today’s food plants, and it’s not surprising that one in four (27 percent) of respondents specifies better hygienic design as the primary area for needed improvement in packaging equipment. Slightly more (28 percent) want equipment that can handle a broader range of container sizes and shapes. Simplified programming (19 percent) and more heavy-duty construction (16 percent) are other needs. Despite the interest in requiring operators to shoulder a bigger share of maintenance responsibilities, only one in 25 readers feels operator safety is an area that needs improvement.
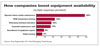
Palletizing is the next most frequently mentioned bottleneck. Seven readers say corrective action is likely, compared to six who say a fix is unlikely. Case packing, sealing and erection follow, with three saying improvements are very likely, and two who rate corrective action as somewhat likely. Two believe a change is somewhat unlikely, and one reader holds scant hope for improvement.
Accumulation systems, labeling operations and capping and sealing are cited as bottlenecks by numerous respondents. Three readers mention slicing. “The slicing area slows us down considerably, before we can get into the boxing of products,” one reader writes. “Cereal bar chokepoint is at the cutting table guillotine, ahead of the in-line wrappers,” writes another. Both indicate improvements are somewhat likely.
As previously noted, material costs, product safety and increased flexibility/changeover speed rank as the top three issues facing packaging operations over the next two years. Little has changed in the rankings of 14 other factors over the last three years, with two exceptions: Consumer convenience has plunged to the seventh rated issue, down from No. 3 in 2008, while faster line speeds rank eighth, down four slots since 2010. Given a general shift from mass-produced products to greater customization, the growing importance of flexibility and a de-emphasis on raw speed are two sides of the same coin.
A connection also can be found in responses to the question, “Where does your company’s packaging effort fall short?” More automation is the prevailing need, but barriers to implementation go beyond financial considerations. Several readers cite lack of space as an impediment to additional equipment. “Room in the plant for additional equipment is very short,” writes one respondent. The versatility vs. high-speed trade-off resurfaced in another written comment: “Automation with more flexibility [is the shortfall]. The big concern is, when you automate, you give up flexibility. We fall short in both categories at the moment.”
Benefits often classified as soft paybacks are cited by one reader as a justification for committing capital to address a specific automation shortfall. “We could improve costs and product quality, reduce consumer complaints and possibly reduce overfill by replacing some manual pick-and-place efforts with more reliable vision-controlled pick-and-place robotics,” this individual notes.
Changeovers, maintenance and operator training are other frequently cited shortfalls. “We need better-trained operators to step up to the plate,” a packaging professional writes. “Maintenance is called on [to make] quick fixes that operations is responsible for.” Material waste is an area several readers would like to see their organizations tackle.
Waste reduction programs often are cast as elements of sustainable manufacturing, though they just as easily could be considered an outcome of lean manufacturing and efficiency initiatives. A question on sustainable practices was recast this year as efficiency practices, and half the respondents indicate their companies have taken action to reduce waste streams, the same proportion as a year ago. Efforts to reduce energy use are underway at three out of five plants, making it the most common efficiency effort. Efforts to reduce transportation costs and cut back on the amount of material used for secondary packaging grew in popularity.
Pressure is building to slash supply-chain costs, and two out of five readers say their organizations redesigned primary packages or shipping materials to drive down costs. “We streamlined our packages and eliminated smaller, less profitable items and tried to increase our throughput and lower man-hour costs per lb.” of finished goods, a packaging professional writes. “Tracking of all waste material to reduce any losses” is another firm’s tactic.
Others cite conversions to smaller carton sizes, reductions in the size and weight of primary and secondary packaging, less stretch wrap, thinner gauges of film, substitution of bag-in-box for rigid containers and a host of other tactics. The most frequently mentioned effort, however, is forging relationships with new suppliers. “More supply chain competition,” one writes, “by searching for more suppliers.”

Change is easier to rationalize if it serves a business objective such as decreasing the amount of time needed to get a new product to market. Existing-equipment modification was the most popular tactic to speed market entry, with two in five taking that route. More automation and the addition of modular lines also were cited. Only one in eight turned to a contract packaging firm, down from one in five in last year’s study.
Compared to last year’s study, this year’s respondents are less apt to implement supply-chain programs to reduce damage in transit, monitor shipment locations or control the distribution process better. The one area where there was an uptick in activity was temperature monitoring of shipments, with one in four indicating a system was in place.
Similarly, the proportion of readers focusing on projects such as adapting lines to handle different package types, installing new lines and investing in material-handling equipment is static or declining, compared to last year. The lone exception is an increase in firms who are reducing expenditures for capital projects: 27 percent say spending will be down this year, identical to the number who say they will increase capital spending.
Greater diversity in employment responsibilities is reflected, with 28 percent of the sample responsible for engineering and 20 percent charged with operations or production management. Administrators and general management represent another 17 percent, while the proportion of R&D professionals has increased to 8 percent. The largest change is in QA/QC respondents, which doubled to 10 percent. Purchasing, maintenance, logistics planners and owners and CEOs also provided input.
Survey participants represent food and beverage plants that are slightly smaller than last year’s sample and noticeably smaller than in 2009’s survey. The majority work at sites with fewer than 100 workers and smaller budgets, with 56 percent spending less than $100,000 on new packaging equipment and 53 percent spending less than $500,000 on packaging materials. By comparison, three in five answering the 2009 survey had material budgets exceeding $500,000.
A diversified manufacturing base is reflected, with processed meat, poultry and seafood products representing the largest segment at 17 percent. Other well-represented categories are beverages (14 percent), supplements and ingredients (12 percent), baking and snack foods (10 percent) and dairy/frozen novelties and cereal/grain-based products (each 8 percent).
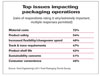
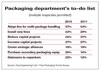
Today’s supervisors, engineers and other packaging professionals have a lot more on their plate as they cope with the sometimes contradictory demands of customers, the supply chain and senior management. Based on reader feedback to Food Engineering’s packaging trends survey, today’s pressures are forcing a reshuffling of priorities and a renewed focus on changes designed to improve overall performance.
An example of the shift in priorities is the ratings of 17 issues and their impact on packaging operations in the next two years. Product safety consistently has ranked second over the years, but the gap between safety and material costs is widening, with barely half the readers believing safety will have a big or great impact, with a comparable number judging machine flexibility and changeover speed to be a big-impact issue. By comparison, 71 percent say material costs will have a big impact.
Asked what actions their companies are pursuing to boost equipment availability, three in five survey respondents cite greater operator involvement in routine maintenance. The second most popular strategy is greater OEM involvement in maintenance training, though only 22 percent are taking that approach. Additional equipment-availability initiatives with similar support are training and education by outside experts and expanded maintenance staffing. Readers volunteer ISO 9000:2008 certification and “implementation of TPM pillars-skills development, focused improvement, autonomous and preventative maintenance, vertical startup, loss analytics, etc.” as elements of improved availability.
Overall equipment efficiency is the metric of choice for evaluating machine performance, not only in production but packaging, as well. Almost half (48 percent) of readers say OEE is driving continuous improvement in packaging. One in five cites increased reliability, and one in 10 focuses on faster changeovers. Improved maintenance procedures are being sought by 8 percent, and another 7 percent are zeroing in on reductions in product giveaway.
Hygienic machine design is a priority throughout today’s food plants, and it’s not surprising that one in four (27 percent) of respondents specifies better hygienic design as the primary area for needed improvement in packaging equipment. Slightly more (28 percent) want equipment that can handle a broader range of container sizes and shapes. Simplified programming (19 percent) and more heavy-duty construction (16 percent) are other needs. Despite the interest in requiring operators to shoulder a bigger share of maintenance responsibilities, only one in 25 readers feels operator safety is an area that needs improvement.
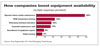
Unclogging chokepoints
Respondents were asked to identify the biggest bottleneck in their packaging line and to indicate the likelihood it would be cleared in the next year. Unsurprisingly, filling operations are the most frequently cited chokepoint, and 14 readers say their organizations are very or somewhat likely to take corrective action. Eight others say their firms are unlikely to fix the problem, including three who indicate action is very unlikely.Palletizing is the next most frequently mentioned bottleneck. Seven readers say corrective action is likely, compared to six who say a fix is unlikely. Case packing, sealing and erection follow, with three saying improvements are very likely, and two who rate corrective action as somewhat likely. Two believe a change is somewhat unlikely, and one reader holds scant hope for improvement.
Accumulation systems, labeling operations and capping and sealing are cited as bottlenecks by numerous respondents. Three readers mention slicing. “The slicing area slows us down considerably, before we can get into the boxing of products,” one reader writes. “Cereal bar chokepoint is at the cutting table guillotine, ahead of the in-line wrappers,” writes another. Both indicate improvements are somewhat likely.
As previously noted, material costs, product safety and increased flexibility/changeover speed rank as the top three issues facing packaging operations over the next two years. Little has changed in the rankings of 14 other factors over the last three years, with two exceptions: Consumer convenience has plunged to the seventh rated issue, down from No. 3 in 2008, while faster line speeds rank eighth, down four slots since 2010. Given a general shift from mass-produced products to greater customization, the growing importance of flexibility and a de-emphasis on raw speed are two sides of the same coin.
A connection also can be found in responses to the question, “Where does your company’s packaging effort fall short?” More automation is the prevailing need, but barriers to implementation go beyond financial considerations. Several readers cite lack of space as an impediment to additional equipment. “Room in the plant for additional equipment is very short,” writes one respondent. The versatility vs. high-speed trade-off resurfaced in another written comment: “Automation with more flexibility [is the shortfall]. The big concern is, when you automate, you give up flexibility. We fall short in both categories at the moment.”
Benefits often classified as soft paybacks are cited by one reader as a justification for committing capital to address a specific automation shortfall. “We could improve costs and product quality, reduce consumer complaints and possibly reduce overfill by replacing some manual pick-and-place efforts with more reliable vision-controlled pick-and-place robotics,” this individual notes.
Changeovers, maintenance and operator training are other frequently cited shortfalls. “We need better-trained operators to step up to the plate,” a packaging professional writes. “Maintenance is called on [to make] quick fixes that operations is responsible for.” Material waste is an area several readers would like to see their organizations tackle.
Waste reduction programs often are cast as elements of sustainable manufacturing, though they just as easily could be considered an outcome of lean manufacturing and efficiency initiatives. A question on sustainable practices was recast this year as efficiency practices, and half the respondents indicate their companies have taken action to reduce waste streams, the same proportion as a year ago. Efforts to reduce energy use are underway at three out of five plants, making it the most common efficiency effort. Efforts to reduce transportation costs and cut back on the amount of material used for secondary packaging grew in popularity.
Pressure is building to slash supply-chain costs, and two out of five readers say their organizations redesigned primary packages or shipping materials to drive down costs. “We streamlined our packages and eliminated smaller, less profitable items and tried to increase our throughput and lower man-hour costs per lb.” of finished goods, a packaging professional writes. “Tracking of all waste material to reduce any losses” is another firm’s tactic.
Others cite conversions to smaller carton sizes, reductions in the size and weight of primary and secondary packaging, less stretch wrap, thinner gauges of film, substitution of bag-in-box for rigid containers and a host of other tactics. The most frequently mentioned effort, however, is forging relationships with new suppliers. “More supply chain competition,” one writes, “by searching for more suppliers.”

Leave well enough alone
Not everyone is sold on the need for changing materials, packaging systems or suppliers, of course. In fact, slightly more than half say their firms have stuck with the tried and true in recent years. The cost of change and existing equipment investments are the primary reasons for standing pat, but one quarter of the sample cites uncertainty about how customers would react to change as the reason they haven’t taken any action. “Overwhelming number of customers prefer to leave our packaging as is,” one reader comments. Several indicate there simply is no need to change.Change is easier to rationalize if it serves a business objective such as decreasing the amount of time needed to get a new product to market. Existing-equipment modification was the most popular tactic to speed market entry, with two in five taking that route. More automation and the addition of modular lines also were cited. Only one in eight turned to a contract packaging firm, down from one in five in last year’s study.
Compared to last year’s study, this year’s respondents are less apt to implement supply-chain programs to reduce damage in transit, monitor shipment locations or control the distribution process better. The one area where there was an uptick in activity was temperature monitoring of shipments, with one in four indicating a system was in place.
Similarly, the proportion of readers focusing on projects such as adapting lines to handle different package types, installing new lines and investing in material-handling equipment is static or declining, compared to last year. The lone exception is an increase in firms who are reducing expenditures for capital projects: 27 percent say spending will be down this year, identical to the number who say they will increase capital spending.
Who answered the survey?
Statistics and industry feedback to the 26th annual Food Packaging Trends survey were gleaned from 147 responses to a Web-based questionnaire.Greater diversity in employment responsibilities is reflected, with 28 percent of the sample responsible for engineering and 20 percent charged with operations or production management. Administrators and general management represent another 17 percent, while the proportion of R&D professionals has increased to 8 percent. The largest change is in QA/QC respondents, which doubled to 10 percent. Purchasing, maintenance, logistics planners and owners and CEOs also provided input.
Survey participants represent food and beverage plants that are slightly smaller than last year’s sample and noticeably smaller than in 2009’s survey. The majority work at sites with fewer than 100 workers and smaller budgets, with 56 percent spending less than $100,000 on new packaging equipment and 53 percent spending less than $500,000 on packaging materials. By comparison, three in five answering the 2009 survey had material budgets exceeding $500,000.
A diversified manufacturing base is reflected, with processed meat, poultry and seafood products representing the largest segment at 17 percent. Other well-represented categories are beverages (14 percent), supplements and ingredients (12 percent), baking and snack foods (10 percent) and dairy/frozen novelties and cereal/grain-based products (each 8 percent).
Looking for a reprint of this article?
From high-res PDFs to custom plaques, order your copy today!