Tighter food defense requirements seen by security expert
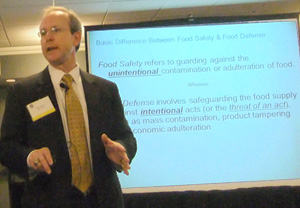
Speaking at an ADT Media Summit on food defense in Chicago May 10, the brewery’s regional security and emergency manager said security officers from a number of food and beverage companies have been working with the Grocery Manufacturers Association to lobby federal regulators to minimize the financial costs of food defense. “The single biggest cost factor to food companies [for FSMA compliance] was going to be food defense,” Powers said, and the industry has pressed hard for workable guidelines that would not turn plants into “
“There is nothing in FSMA that says you have to have electronic systems,” said Powers, “but you can’t [satisfy] FSMA without historical records of CCTV recordings, access card use” and maintenance records of system components.
Installing and maintaining security hardware can add up to significant capital expenditures, he conceded, but Powers said he has documented returns on investment of 10-40 percent on projects. He cited work for a major food company that began with a $1.6 million installation at a single manufacturing site. According to Powers, payback occurred in six months, an ROI of almost 45 percent. Ten distribution centers were equipped with $500,000-$1 million in surveillance equipment and generated returns of 15-25 percent.
Many of the returns were generated by charges assessed to vendors based on video surveillance. In one instance, cameras captured a delivery truck sideswiping a loaded trailer, toppling the trailer and resulting in $150,000 in damages, which the delivery company was forced to pay. Late delivery charges of $50,000 to $100,000 per site were realized by date-stamped video documenting late deliveries. At a
Soft savings from surveillance included the elimination of “contamination pranks” by employees within the plant, the virtual elimination of OSHA recordable injuries on the loading docks of another facility and the eradication of drug dealing and prostitution at a plant’s trailer yard.
For more on plant security, see:
“Plant Security: Access Granted,” FE, JAN 2011.
“National security at the dinner table,” Bill Ramsey, Frank Pisciotta, FE On line.Looking for a reprint of this article?
From high-res PDFs to custom plaques, order your copy today!