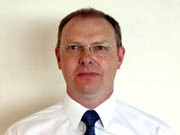
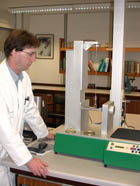
Although Crown introduced an easy-open lid in 1990, the package often failed to live up to its name. Research on the ergonomics of lifting a tab and peeling back a lid continued, and a second-generation end followed. Terry Benge participated in that project, and in 1996 he was asked to spearhead a team of 16 engineers and technicians who refined the design and transferred the technology to produce those lids at Crown plants around the world.
A physics graduate of the University of Manchester's Institute of Science and Technology with an honors degree in polymer science and technology, Benge joined the British firm Metalbox in 1976. Through a series of mergers, he became a Crown researcher in 1994, spending two years in the specialty packaging business in Rouen, France, before returning to the R&D center in Wantage, in the English countryside. He now serves as R&D director for Crown's food division.
FE: What shortcomings of the earlier versions of the easy-open end did your development team address?
Benge: Before the 1990s, "easy open" was a misnomer. Quite frankly, the early ends were not very suitable for consumers. The ergonomics were still difficult when I took over the project in 1996.
Beverage guys will throw their hands up in horror, but sanitary food ends are much more difficult to manufacture than ends for aluminum cans. Ends are stamped out of very wide sheets of metal, and any variations in thickness can result in unacceptable failure rates. Development of the third generation, which we dubbed Lift Off, was made possible by the introduction of DR (double reduced) steel and tighter manufacturing controls in five plants.
FE: What's the significance of DR steel?
Benge: DR steel results in ends that are both harder and thinner than conventional steel. Typically, steel can be elongated three percent at best before rupturing. We had to expand it 30 percent to hold the rivet. That took five years to master on our existing 100-ton conversion presses. Each press performs 12 tab processes and eight end-making processes. The ends have to be strong enough to tolerate retorting and seaming and still require less hand strength to remove once the score has been pierced.
The steel spec we created for the original easy-open end didn't exist before, and we maintained that standard when we moved to high-nitrogen steel, which gives more elongation to make rivet-forming easier. The press stretches the metal to create a top hat, then hits it to produce a rivet to hold the tab while creating the tab from another piece of steel simultaneously. All this is taking place at rates of up to 1,800 ends per minute. Very important enabling technology was transferred from beverage processes, such as plastic belts that transfer lids from station to station at a rate of 600 per minute per lane.
FE: Describe the laboratory aspects of the project.
Benge: It's a quite interesting engineering problem to design an end with the optimum initial pop, tear force and peel strength. We made substantial investments in people and technology, including precision robotic instrumentation and analytical equipment. At the outset, we had to design and build a measurement machine that mimics, as much as possible, the motions and force exerted by the consumer when opening a can. Tearing, the initiation of the pulling back of the lid after the initial pop, always has been the highest and most difficult force to control. The target was maximum 10 pounds of force, which represented a 20 percent improvement over previous generations. In 1996, tear force variability was the number one complaint we received. With the third generation, those complaints virtually have been eliminated; the force required to lift the tab is the biggest complaint now. That's a function of tab access, how much room there is between the tab and the end. It's a geometric problem: how to provide access while manufacturing at high speeds and stacking and handling the finished ends.
FE: Tearability is a function of score depth. How tight are those tolerances?
Benge: Lacquers on the metal and vagaries in the steel depth result in variances in the score, but we've significantly improved tolerances. In the first generation, we scored within a range of 20 microns. We're now able to produce within a 10-micron ban, or a score depth of plus or minus 5 microns.
Every plant has equipment to measure score depth, and people have talked for years about using lasers, but when you tell the makers of laser machines what the tolerances are, they go pale. Instead, we put sample ends on an anvil and use optics kits to determine score depth. Because the tests are destructive, any anomalies have to be explained in the context of new samples.
We work with a safety margin that is above minimum performance because scoring is a particularly critical aspect. This is one of the few zero defects products I've ever encountered. Irregularities in the steel can produce microscopic holes along the score, and that is totally unacceptable.
FE: How was the transition from lab to full-scale production equipment accomplished?
Benge: Development required near full-scale production equipment. And it was augmented by 2,000 hours of line monitoring at the first plant before commercial production could begin. We had lots of standards, but we didn't really understand how the process worked until we watched how the line functioned and understood where variation occurred.
For example, the knife that scores the lids dulls over time, and how the dies wore varied from one knife manufacturer to another. That had to be carefully monitored to ensure that we manufactured with a safety margin. Photos from an electron microscope helped in that understanding.
Details of what the operating engineers did had to be captured. The engineers have to adjust the scoring die to within 2.5 microns, with grease up to their elbows in a 100-ton press. They have to profile the die slightly, deeper at the tab end than the back end. As we implemented the process from one plant to the next, we would explain what the other plants did, the engineers would express their reservations, and then we would generate rules they felt comfortable with.
FE: Couldn't some of those functions be automated?
Benge: We found great difficulty in automating the process, but we found ways to help the engineers understand and do things better.
Our plants use three different types of forming presses, and they use significantly different processes. As the metal gets thinner and harder, it tends to split more readily. Engineers had to understand how to prevent that on their particular press. One of our young engineers suggested creating forming-limit diagrams. We etched a lattice on the metal to see which bits expanded and contracted during the process, then related that to how close we were to the rupture limits and rivet failures. Those diagrams enabled us to produce a process that is more robust.
FE: Continuous improvement or cost reduction is the name of the packaging game. Where is your current focus?
Benge: We've spent a lot of time helping end users-the canners-adapt their older seamers to the new ends. Customers are there to fill cans, not to close them, so it's our job to make the seaming process a nonissue. Wrinkles compromise the hermetic properties of a can, so we provide our expertise and sometimes alternate tooling to eliminate those types of problems.
We're not only involved in continuous improvement, we're also looking for a replacement to the easy-open end. Peelable foil ends will be the next generation. Our challenge is to design a process to reliably and efficiently mass produce those ends, just as we do with 5 billion easy-open steel ends each year.