Product variation? Think outside the process cell
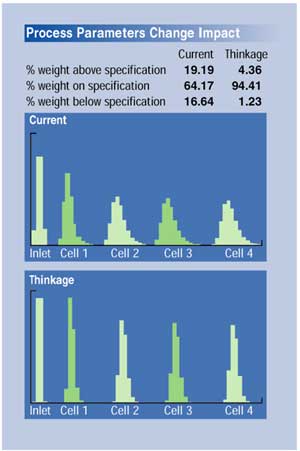
The modeling tool from Thinkage shows how processors can increase product conformity by making changes throughout an entire, linked production network rather than in just one cell. Source: Thinkage.
"Improvement projects only deliver value if the entire process, and not just one cell, is united. When changes or improvements are made, each should be made simultaneously, on each cell in the process," said Mark Grace, president of Thinkage. The company's Think Gates™ service enables processors to monitor and control the state of their food product as it moves from one processing cell to another.
A new modeling tool from Thinkage shows food processors how the Think Gates service manages product variations from cell to cell to produce 30 percent more product within the customer's specifications. A snapshot from a five-cell model, depicted at left, shows the impact that changing one or more parameters has on a typical food product that's marinated, breaded twice, fried and frozen.
"If you make an investment in Cell Two, which reduces variation, but Cell One or Three remains the same, you may lose all the value you created in Cell Two," Grace said.
For more information about the service, contact Thinkage at (908) 253-9550 ext 298.
Looking for a reprint of this article?
From high-res PDFs to custom plaques, order your copy today!