ENERGY EXCLUSIVE: Powering Your Bottom Line

Of all the energy consumed in US food and beverage plants, corn milling, beet sugar, soybean oil, brewing, and canned food operations use the largest share. Everywhere you look, companies are trying to reduce energy costs and improve their bottom lines. Nestlé, for example, reported to its investors that its energy and efficiency programs targeted savings of hundreds of millions of dollars over a six-year period. Other major food processors have similar initiatives, many of which were re-energized by the rapid rise in natural gas prices. Energy prices have risen so rapidly during the past three years that even ambitious dollar savings targets need to be revised upward.
Been there, done that
Rising energy prices, tight supplies, and an uncertain future: sound familiar? Yes, but this time things are different. "In past energy crises, by the time we had an energy reduction solution deployed, the crisis was over," says Karen Balentine, business development specialist for Emerson's food and beverage unit. She's not betting on that happening again. The energy crises of the 1970s and 1980s were caused by disruptions in oil imports. While supply disruptions can still have an impact (as shown by the chaos in the US Gulf Coast from hurricanes Katrina and Rita), the demand side of the energy equation has changed. This time, there may be no return to the lower prices of the past.One major structural change in energy markets is electric power generation, which requires far more natural gas than ever before. Since the 1980s, gas-fired electric plants have become larger, more efficient, and very clean burning. As a result, more than 95 percent of the new power plants built during the last ten years in the US use gas for fuel. This has reduced the huge seasonal variations formerly seen in gas demand. Furthermore, the supply side has tightened as producers struggle to increase production and more imports of liquefied natural gas (LNG) are delayed because of the time required to develop LNG terminals and concerns about LNG becoming a target for terrorists. LNG can be transported anywhere, so the North American market must compete for it against the rapidly developing economies in Asia.
Deregulation of electric power markets has a checkered history after the California debacle of 2000-2001. Where deregulation has occurred, its effect has been to link the energy prices of electricity and gas, since suppliers to new regional power markets have large numbers of gas-fired plants. In daily power auctions, the price of gas determines how these suppliers price their power. With gas prices high, their gas-fired plants are setting the market price for power in many parts of the US. New coal-fired electric plants are on the drawing board, but they will not be running in large numbers for another five to ten years. As a result, power and gas prices will be tied together in the US for years. With so much of food processors' energy depending upon gas and electricity in increasingly tight energy markets, the energy crisis has become a permanent feature of business.
Production & energy
Food plant utility systems are tied into every production operation, but most of the human resources in a plant focus on producing product rather than monitoring utilities. "Plant managers generally do not have knowledge and experience in energy," says Al Hamdan marketing manager, PEMS, with Rockwell Automation. The same is true for most plant engineers. "Energy management has been a side business for food plant engineers," adds Don Lovell, senior consultant with Rockwell. "It is not what they mainly spend their time doing." It helps if plant operators can engage a trusted partner before they make a big push to save energy. Even then, cautions Hamdan, there may not be enough information to quantify the relationship between production and utilities. Hamdan has found plants where energy consumption ran 20 percent over historical plan, yet there was no identifiable cause. "Many food plants do not have the infrastructure installed to be able to understand their energy cost behavior," says Hamdan. He recommends that plants add new power measurements that connect utility consumption to individual production lines. If that seems too expensive, he says they should at least develop the next level of detail in their monitoring capability. "I tell customers to think of the first step as an ante that will give them additional information so that they can see and understand more as energy prices rise," he says. "Energy prices are not going down in my view, so the ROI on today's energy investment will improve with time. At some point, the ROI will be high enough to meet the manufacturer's hurdle for approval."
Reducing information cost
Obtaining more detailed information about electric power use in the plant costs money. Power distribution systems were designed at a time when power was cheap and metering was expensive. As plants evolve over time, the power distribution network morphs to serve changing plant operations. After many years, the result is that the usefulness of meter information varies all over the map. "We do not have a uniform electric metering infrastructure across all plants," admits SABMiller's Melinda DeLuca, manager of energy and utilities. Instead, it becomes the energy champion's task to make the most of what metering is installed and calculate the plant energy performance.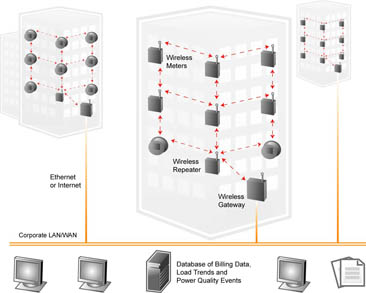
The advantage of a wireless sensor network is not its reliability, but its much lower installation cost when compared to an equivalent wired system. "The actual meters are often only a small percentage of the overall cost of the project," says Hugh Lindsay market manager with Power Measurement Corporation. The bulk of the cost goes toward installing new meter panels and new wiring for data collection. By minimizing the use of new electrical enclosures and eliminating the wiring for data collection, a wireless sensor network can cost 50-70 percent less to install. The meters get their own power from the circuits that they monitor and come complete with their own enclosure.
Wireless power meters were developed for "sub-metering" in large commercial and residential buildings, but industrial suppliers are now offering them to manufacturing plants as well. For example, both Siemens and Power Measurement Corporation now offer wireless meters and integrate both wired and wireless meters into their energy monitoring software. Wireless power meters may be the key to affording the more granular information about power consumption that food processors need.
Measuring your consumption
With energy measurement, though, comes some degree of difficulty. The data needs to be collected and organized so that it can support an analysis of the operation. And the analysis must go deeper than just technical matters. "You have to understand more than just raw energy consumption and demand," says Hamdan. "Manufacturers really need to consider what concrete steps they are willing to take in their operations, too. How are they willing to shift around their production schedule to move certain operations to off-peak hours? Will they install new equipment? Would they be willing to shutdown some operations temporarily to lower their purchased power cost?" Hamdan says that a clear energy plan needs to include a definition of the operational changes that plants are willing to consider.
Optimizing your equipment
While food processors are very secretive about their own energy targets, there is no secret recipe for optimizing energy equipment. The efficiency of various energy conversion processes is governed by thermodynamics, which is a rare field of expertise but not a secret one. This means that operating energy conversion equipment optimally is a major part of success. "In most plants if you want to find the major potential ROI, go to where fuel is burning," says Jim Payne, senior consultant with Emerson Performance Managment. Payne will collect and compare current data based on actual trial runs with equipment design data. "Often we find that either something has drifted out of tolerance or perhaps was not maintained correctly over time," he says. "Improvements to boiler mechanical equipment, instruments, regulatory controls, or advanced controls can be the highest ROI investment in the plant, provided that operating practices improve as well. "Progress can be made with the right attitude and focus, but you have to provide complete training for all involved."
Refrigeration systems are another conversion system that benefits from thoughtful and periodic attention. Both control systems and operating points need to be evaluated. Since plants may have several generations of equipment, some of it far older than others, it makes sense to see that the unit control systems are optimized for energy efficiency. For example, older chilled water control systems may enforce operating points where heat exchanger tubes are not fully immersed in liquid refrigerant. Condenser controls may not respond to colder ambient temperatures that allow them to reduce or eliminate fan horsepower. Machine automation systems that were designed in the era of cheap energy did not need to take these factors into consideration, but today's wise operating companies do. Ice water storage units also offer another easy way to shift power consumption off-peak. These should be automated to charge fully using cheaper off-peak electric power and to exhaust fully during on-peak hours so that their full capacity is used daily to replace more expensive on-peak power.
Awareness is, of course, a fundamental element of efficient energy consumption. "When people recognize that there is a metric and an objective, their behavior will change," says Lovell. "Energy measurements that people trust will cause behaviors that push the meter in the right direction."
The rise in US energy prices has been relentless. For food processors, today's higher prices are not just a fluke, but rather a sign that the industry has entered a new era of more expensive energy. While energy prices do not have the same impact on all manufacturers, they have renewed prominence in operations and planning. From now on, managing energy well will be an important part of achieving excellence in food manufacturing.
For more information:
Karen Balentine, Emerson Process Management,
512-835-2190,
karen.balentine@emersonprocess.com
Hugh Lindsay, Power Measurement,
250-652-7100,
hugh.lindsay@pwrm.com
Al Hamdan, Rockwell Automation,
414-382-1085,
ahhamdan@ra.rockwell.com
Looking for a reprint of this article?
From high-res PDFs to custom plaques, order your copy today!