Tech Update
Reduce Your Energy Usage, but Know Where to Start
There may be some energy-savings steps you haven’t yet taken.

This motor control center (MCC) consists of a bank of variable speed motor drives that are responsible for controlling motor speeds in a portion of the plant. Just beyond the MCC is a local network cabinet, which connects the drives with various controls in the facility. Photo courtesy of Ross Van Pelt, RVP Photography
The problem with a single article describing what’s new in saving energy is that by now we know where most of the energy waste is, and we’ve probably already fixed those issues—picked the low-hanging fruit. For example, the leaky air hoses and fittings, the lights left on 24 hours a day in the plant and the cooler when no one is there, running empty conveyors, wasted water rinses, etc.—and the list goes on.
Other energy savings opportunities may be hiding in plain sight. Without some measurements and monitoring, it will take a little work to find out what’s going on. In fact, Grainger’s editorial staff recently put out a list of six tips for reducing energy consumption in food manufacturing. First on the list is to automate, monitor and control.
Monitoring & Controlling Energy—Your First Step to Lowering Bills
The good news on monitoring and controlling energy usage is there’s plenty of technology out there, and if you need help, most automation suppliers and system integrators have plenty of experience with this equipment. Perhaps a little more difficult is that clear goals need to be set before actually applying any technology to monitor energy usage.
New energy monitoring technology is often easy to apply, and some of it may be already installed, though underused or not at all. Monitoring kilowatt consumption, optimizing equipment utilization and building a robust control process will help synchronize the system with facility operations.
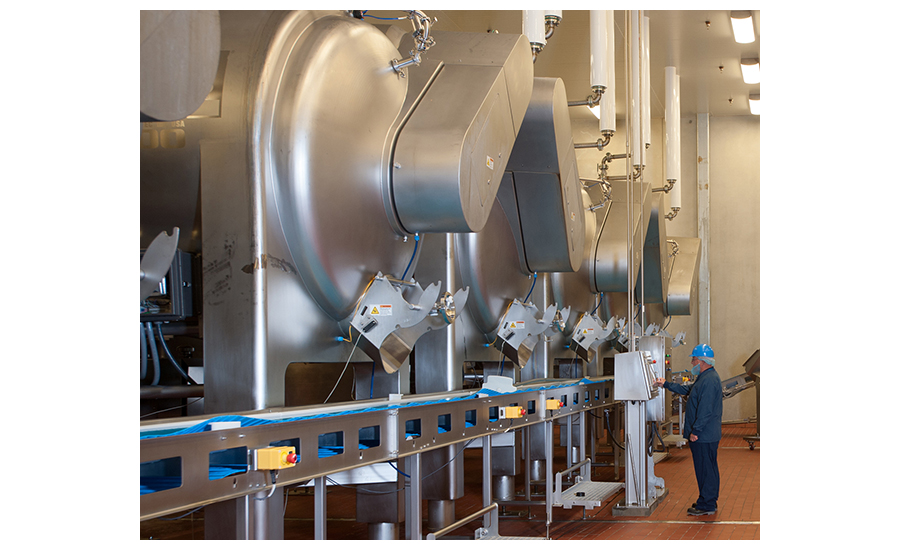
Today, energy dashboards let operators access automation usage and energy monitoring systems from anywhere with smartphones or tablets, making it possible for operators to get a grip on areas and equipment in the plant using energy. The meat industry is a large user of resources and energy, and plant equipment tends to use a lot of electricity, for example, in processing equipment, refrigeration, pumping water and waste removal.
George Walker, managing director of Novotek UK and Ireland, a food control system provider, set out to design a monitoring system for his meat processing clients. “Meat processing requires a lot of heavy machinery, each with associated electrical components such as motors and drives that will have varying standards of electrical efficiency. These devices begin to draw more energy as they age, often indicating a need for maintenance.”
“The most efficient way of recognizing and addressing these problems is with industrial control systems, such as modern HMI/SCADA,” says Walker. For example, GE Digital’s iFix 2022 (v. 6.8) provides fast connectivity with systems and enhanced visualization of data through a HTML5 user interface and responsive web design.
“What this means for food engineers and plant managers is that the data collected by these systems helps to paint an easily understandable, data-driven picture of your plant, equipment and processes,” says Walker. “Using this, it becomes easy to identify systems that are particularly energy intensive and identify the causes.”
“For example, if iFix pinpoints that a motor in a refrigeration unit is drawing significantly more electricity from the mains than it should for its speed, then this highlights that it may be time to swap to a premium efficiency—IE3 or higher—motor,” adds Walker. “Making this change alone will lead to a significant reduction in energy usage from this process, in turn highlighting the value of industrial data visualization.”
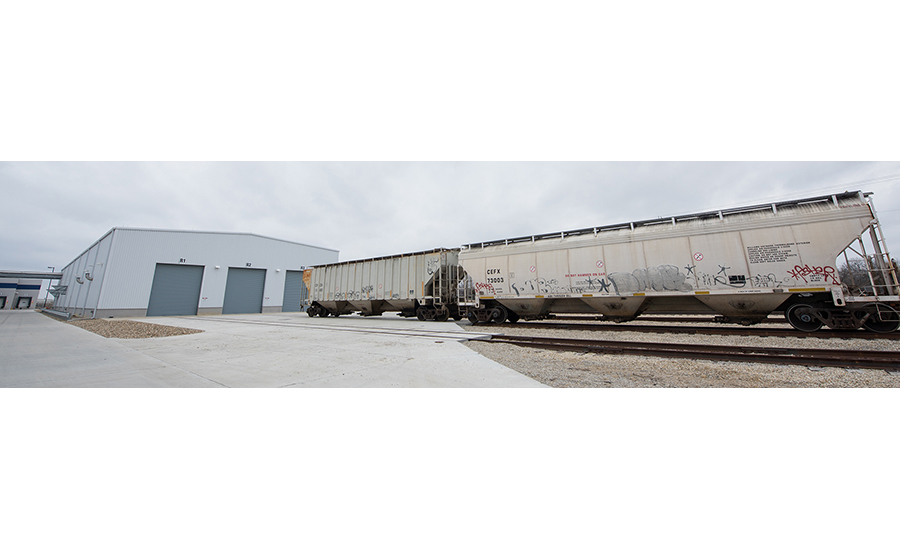
“The most efficient way of recognizing and addressing these problems is with industrial control systems, such as modern HMI/SCADA,” says Walker. For example, GE Digital’s iFix 2022 (v. 6.8) provides fast connectivity with systems and enhanced visualization of data through a HTML5 user interface and responsive web design.
“What this means for food engineers and plant managers is that the data collected by these systems helps to paint an easily understandable, data-driven picture of your plant, equipment and processes,” says Walker. “Using this, it becomes easy to identify systems that are particularly energy intensive and identify the causes.”
“For example, if iFix pinpoints that a motor in a refrigeration unit is drawing significantly more electricity from the mains than it should for its speed, then this highlights that it may be time to swap to a premium efficiency—IE3 or higher—motor,” adds Walker. “Making this change alone will lead to a significant reduction in energy usage from this process, in turn highlighting the value of industrial data visualization.”
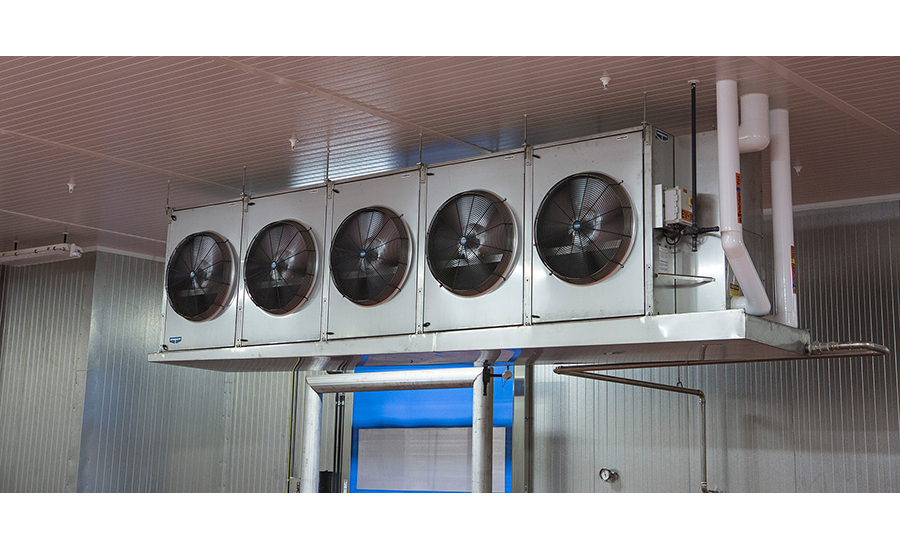
Higher efficiency motors are becoming the norm with equipment suppliers for several reasons, according to Andrew Hager, senior mechanical engineer, central region discipline lead for CRB. Equipment vendors are providing higher efficiency motors with their standard offerings, primarily due to the increased efficiency from implementing codes and standards, but also because manufacturers want better efficiency to lower energy consumption and reduce energy losses through heat buildup.
“Considering new systems, we are designing and installing variable speed air compressor(s) with a constant speed air compressor(s) in most cases for large, compressed air systems,” says Hager. The constant speed compressor is designed to maintain the baseline compressed air demands and the variable speed air compressors handle the peak loads. As the load falls below the capacity of the constant speed compressor, the variable speed compressor takes over and manages the low load conditions. In respect to pumping systems, all new systems are variable speed systems. It is important to consider the operational requirements of the systems, and whether or not the systems can turn down the speed based on the demands for pressure/flow.
A recent set of case studies from a system integrator, EDC Scotland (Electronic Drives & Controls), points out several wins when food processors added VSDs to motors on fans and compressors. For example, Cherry Valley Farms processes 45,000 Pekin ducks per day using air blown over coils of ammonia refrigerant to produce blasts of very cold air. Twenty ABB HVAC drives were added to the cooling process (two drives per chill bay), which resulted in a 25% energy savings during production (by running the motors at 45 Hz). Outside operating hours, when the motors were slowed to 30 Hz, a 60%-70% savings was realized. These fans can’t be switched off completely or they would ice up.
Pizza Hut saw an 85% savings in energy when it installed ABB component drives on an extractor fan motor and supply fan on its cooker heads at its UK Watford Dome branch facility. When running the fans at full speeds for 13 hours a day, they consumed 35-45 kWh, according to EDC.
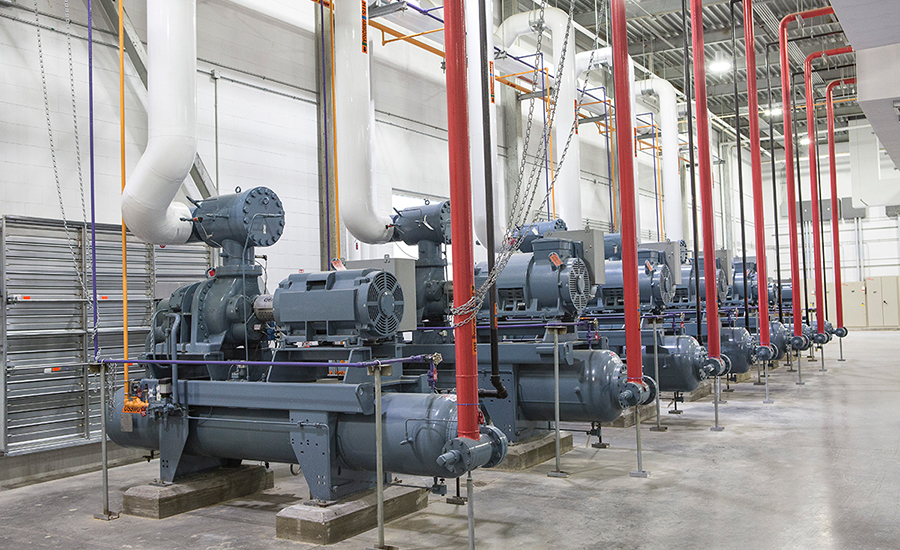
Heinz’s facility in Wigan, UK uses 100 metric tons of steam every hour to process 1.3 billion cans of food every year. The steam is used for both space heating and the sterilization of canned foods. Four boilers are each fitted with two gas-fired burners with fans to push air into the frame. Eight ABB VSDs rated to 55 kW were installed on the production line, varying the speed of the fans to control the amount of air injected into the process and altering the flame level to match steam demand. Previously, the demand for steam had ramped up and down slowly over several days and varied seasonally. According to EDC, the energy center is now 14% more efficient, the drives are more responsive than the mechanical dampers (which introduced a time lag), and reducing the energy consumption also decreases nitrous oxide emissions.
Speaking of large boilers, boiler stack recovery systems are becoming more readily packaged by manufacturers and vendors to make them easier to sell and install, says CRB’s Hager. “We are seeing more recovery systems being included with new installations. For existing systems, it comes down a cost/benefit evaluation of variables such as the age of the existing system, operational set points of the system, and the cost associated with the downtime to implement the change.”
Energy-Efficient Boilers Help Lower Water Heating Bills
Not every application requires huge boilers eating up a lot of floor space. In certain situations, smaller boilers with fast heating capabilities are what’s needed—in other words, supply the right amount of hot water when called upon.
Imagine a poultry egg operation where you need to wash and sanitize 600 cases of eggs an hour. When I was a kid on the farm, the standard case size was 30 dozen or 360 eggs. In any case, Pine Valley Ranch in Spencerville, Ohio—an egg breaking facility—turned to Consolidated Hunter, a local heating contractor, and Pickrel Brothers, a provider of industrial heating supplies, to present the options. Their recommendation was to install six Weil-McLain SlimFit 750 commercial, high-efficiency hot water boilers.
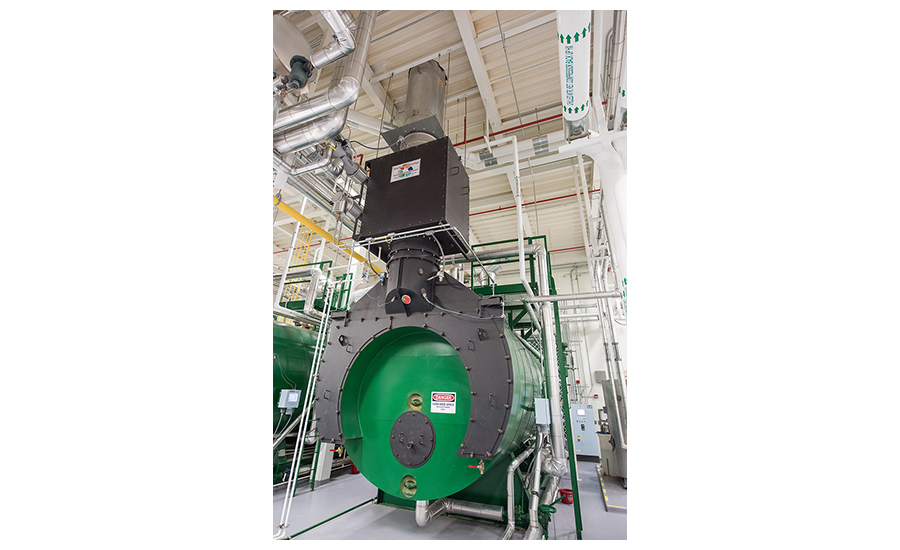
“We’re an egg-breaking plant,” says Evan Fleck, an owner of Pine Valley Ranch. “Our eggs come straight from the barn and are immediately washed. Then they are broken, separated and chilled. Once this is done, they are loaded into liquid tankers and shipped to be pasteurized. Every step of the process is important, especially the washing of the eggs. We need plenty of hot water for that, as well as for other daily operations.”
The 4.5 million BTU/hr heating system installed at Pine Valley supports seven individual heating zones. The first three are dedicated to the egg washing machines and supported with the 750 BTU/hr boilers. The fourth and fifth zones support the CIP equipment (990,000 BTU/hr heat exchangers) while the two remaining zones are for the indirect fired water heater and the onsite mixing station.
“Every zone is critical to ensuring a high-quality, efficient production process,” says Fleck. “We have more than 900,000 chickens at this facility and they produce a lot of eggs. The Weil-McLain boiler system provides a consistent source of hot water to accommodate this large number.”
SlimFit boilers have rugged, cast horizontal heat exchanger sections that provide thermal efficiencies up to 95.8% for 1000 and 1500 models. The boilers feature a low pressure drop design, with large water passageways to accommodate a wide range of commercial installations, including retrofit and replacement applications with older water systems.
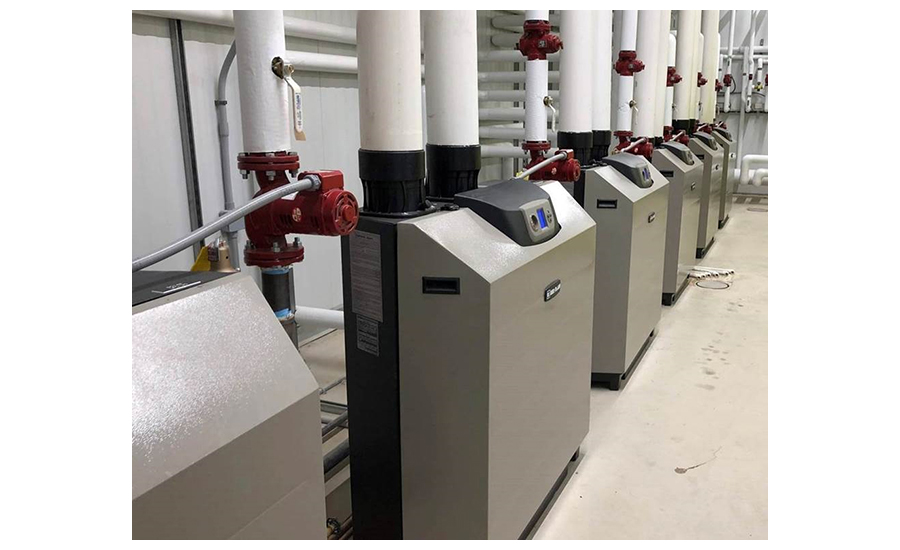
Control features include a setup wizard that guides the installer through the startup process and 10 preset typical heating operation conditions. The SlimFit also features zone stacking up to 24 programmable zones without the need for additional external panels and 0-10 VDC analog output signal for easy integration with a lag boiler in a hybrid system.
“We really appreciate how the Weil-McLain boiler-system enhances our operation,” says Fleck. “The equipment was installed when the facility was built so they’ve been part of our production process from the beginning. Running a plant of this size always presents challenges, but our hot water needs are not one of them.”
Alternative Energy Systems—Depends On The Application
Number four on the Grainger list is the use of alternative energy sources. Depending on location and application, there may be options that can make a difference in your energy bills. For example, Smithfield has had an ongoing program working with Monarch Bioenergy to convert manure and industrial waste at its facilities to electrical energy (cogeneration) and biogas to be used on premises or to sell to the natural gas grid. FE has covered Smithfield extensively on the subject, and Smithfield was named a “Sustainable Processor of the Year” in 2014.
Food distribution centers are also finding ways to decrease energy usage—and even create alternative sources of energy. For example, US Foods recently announced the opening of its 355,000-sq.-ft. distribution center in Sacramento. The facility houses foodservice products, fleet maintenance operations, a full-service demonstration kitchen and a training center for customer product demonstrations and recipe innovation.
According to Dan Geissbuhler, US Foods area president, the new building and fleet operations include innovative sustainability attributes aimed at supporting the company’s commitment to reducing the environmental impact of its operations. Key sustainability highlights include:
- A forthcoming Leadership in Energy and Environmental Design (LEED) Silver certification for building design and construction.
- Solar array installations to be installed later this year expected to generate between 40% to 50% of the building’s energy needs.
- Energy-saving LED lighting, environmentally optimized HVAC systems, refrigeration systems that do not utilize water for evaporative cooling, and water-saving landscaping.
- A fleet of 27 compressed natural gas (CNG) trucks fueled by renewable natural gas, a carbon-neutral biogas produced from the decomposition of organic matter. With the addition of the new Sacramento-based CNG trucks, US Foods will have more than 75 active CNG trucks in its fleet.
- An onsite fueling station that will provide renewable diesel (RD) fuel to the facility’s fleet. US Foods is one of the early-adopters of RD fuel use within the foodservice industry, successfully converting 100% of the fleet fuel used at its Vista, Corona, Livermore and La Mirada, Calif., locations to RD fuel earlier this year. RD fuel is a more sustainable alternative to traditional diesel with a more-than-65% lower carbon intensity rating—based on California Air Resources Board’s lifecycle analysis of carbon intensities using the CA-GREET model.
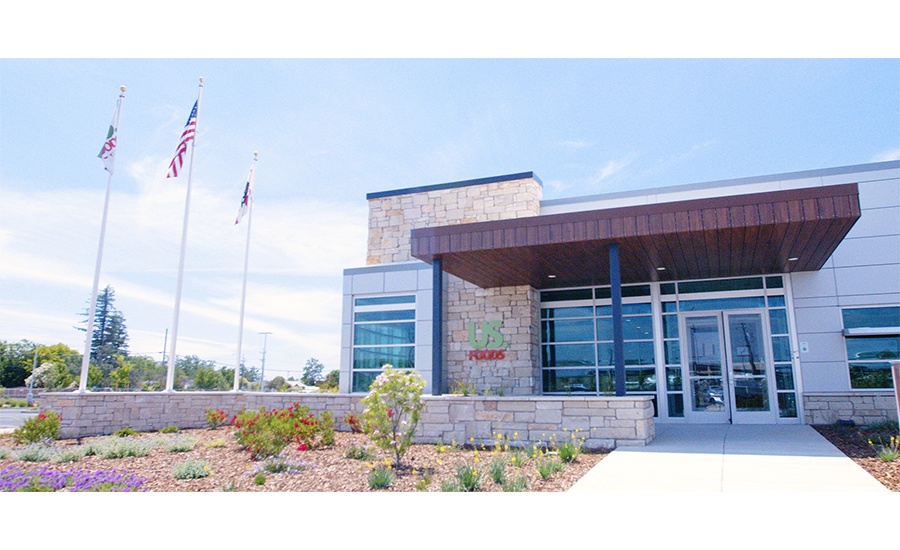
What about Motion Sensors for Controlling Lighting?
Number five on the Grainger list: energy-efficient lighting systems, which US Foods has employed. Do motion sensors and LED lighting make sense? Simple question—but not so simple an answer, according to Hager. Motion sensors certainly make sense in the simplistic form of, “shut off the lights if you’re not in the room” and “turn off the machine if you are not using it.” That might be okay for small or simplistic systems, however some systems may require continuous power for safety and upstream or downstream operations, including monitoring and communicating of data. The division or separation of power sources to stop a conveyor but keep the safety and control equipment powered must be integrated into the design, construction and operation of the equipment as a whole. Processors should be asking, “Is there a standby, ready-to-run or low-power operational mode, and how does that affect safety and upstream and downstream operations?”
High-efficiency lighting systems and lighting controls are expensive, adds Hager. Processors should be evaluating the amount of downtime the lighting system endures to offset the costs of these controls. With the use of high-efficiency lighting, a downtime of minutes will not matter as much as downtime lasting hours. So the question is: How much time translates to the right time for making an investment? That’s where an experienced team can help complete an evaluation that considers the cost of control systems and their installation, the potential savings and the cost of production loss due to downtime for installation. Only then can processors make an informed decision.
One final note on LED lighting—maintenance. If you’re constantly struggling to replace conventional lighting in high ceilings or hard-to-reach locations, which may require setting up special equipment (ladders and scissors lifts) to reach it, LED lighting with its longer lifetime—though a more expensive initial investment—may pay for itself in the long run with less time spent on maintenance and less plant downtime while changing key overhead lighting. Another point on maintenance: I remember one shop floor manager describing another hidden benefit of LED lighting on the plant floor. With LED lighting’s higher intensity and better color-rendering quality, workers are able to spot machine problems much faster, catching potential faults before turning into machine failure and downtime. How do you put a price tag on that?
A Culture of Energy Management
This subject, number six on the Grainger list, could be an article unto itself. Companies like Smithfield and US Foods see the value of getting all employees onboard with saving energy. Whether or not a team member participates directly in an energy-saving function, once they have understood the virtues and potential bottom-line improvements with saving energy, they will find new ways and propose new methods to save more energy. All that’s required to find hidden energy savings is to listen to those people who are close to the process and hear what they have to say.
Resources:
“Six Tips for Reducing Energy Consumption in Food Manufacturing,” Grainger Editorial Staff, Grainger KnowHow web page.
“Case Studies: Food & Beverage,” EDC Scotland, Web page: https://www.edcscotland.co.uk/pages/case-studies-food-beverage
Looking for a reprint of this article?
From high-res PDFs to custom plaques, order your copy today!