Wastewater Treatment
How the bottom line is tied to wastewater treatment
Insight into some real-world, win-win situations for treating wastewater.

J.R. Simplot’s process water treatment and return plant in Caldwell, ID, designed and built by CDM Smith, treats an average of 2.3 million gallons per day of high-strength potato processing wastewater. Source: CDM Smith.

The total plant layout at Frito-Lay’s Casa Grande system includes steps from fine screening and primary clarification to MBR, followed by carbon filtration, ultraviolet sterilization, RO and stabilization and chlorination. Source: GE Water.

Frito-Lay’s Casa Grande MBR water recovery and reuse plant processes up to 645,000 gallons per day from the potato chip manufacturing process. Source: GE Water.

The Probst Group worked with Excel Engineering and CDM Smith to provide Baker Cheese a wastewater treatment plant that could achieve phosphorous concentrations less than 0.4 mg/l. Source: The Probst Group.

Instead of a new building, DAS EE specialists extended Friweika’s wastewater treatment facility by installing four TFRs (trickle-flow reactors) with dimensions of 3 m dia. and 8 m tall. Source: DAS.

Stonyfield’s wastewater system is designed to pretreat equalized raw process wastewater with COD, TSS and FOG levels up to 5,000 mg/l, 550 mg/l and 500 mg/l, respectively. It also produces biogas, which is recovered and used to heat the anaerobic reactor. Source: ADI Systems.






There are several reasons to treat your wastewater, but when you stop and think about it, only one thing matters—the bottom line. Sure, you want to be “green” in the eyes of your community and customers, but think of the economic pluses to treating your wastewater.
At the most basic level, there are surcharges from the POTW (publicly owned treatment works) for excessive BOD (biological oxygen demand) and COD (chemical oxygen demand) levels that can be cut. If you are trucking wastewater offsite, that could be an extra expense. Also, if your plant’s energy costs are high, you might be able to capitalize on energy in your wastewater. Or if you’re located in a geographical area where water is scarce, there could be strict regulations on usage amounts.
Article Index:
- Scarcity of water
- Cutting transportation costs for wastewater
- Water reuse pick of the year
- Increasing amounts of potato wastewater = more energy
- Keeping the “green” image
- Sidebar: Floating wetlands, clean waterways
Speaking about regulations, perhaps the EPA says you’re releasing far too many nutrients, such as nitrogen and potassium, into the local aquifers, and you may be fined. This also doesn’t help your community image, and you might want your customers to perceive that you are actually green.
The remainder of this article looks at some real-world, win-win situations for treating wastewater where at least one or more of the above were compelling reasons for food and beverage processors to make some changes in the way they handled their wastewater. (For a detailed look at wastewater technologies, visit FE, September 2015.)
Scarcity of water
The availability of freshwater is limited, and it is increasingly difficult to find adequate sources to meet future demand requirements.
“It is projected that global demand will outpace supply of freshwater by 38 percent by 2025, and in regions without extended drought conditions, the situation is even worse,” says Brian Arntsen, global domain leader, UF/MBR, GE Water & Process Technologies. “Reuse of wastewater comes in many forms, and the reasons for reuse are related to the existence of local conditions, such as accessibility to freshwater in the environment, population, climate, and industry and agriculture needs.”
Membrane bioreactor (MBR) technology combines biological, secondary and tertiary wastewater treatment in one step and has been used not only to treat wastewater to high effluent quality standards for over 25 years, but is also a well-established means of enabling the reuse of wastewater, says Arntsen. The MBR process can generate a solids-free wastewater effluent extremely low in BOD (less than 3 mg/l) and nutrient removal (N and P), producing a permeate water quality good for recreational use. For reuse flow sheets that incorporate reverse osmosis (RO) to achieve more stringent limits, MBR provides feed or product water as it achieves SDI (silt density index) values less than three on a constant basis. Literature shows the log reduction of indigenous virus/coliphage in the range of 2.6 to 3.2, and it’s expected that MBR will remove greater amounts, says Arntsen.
“It is projected that global demand will outpace supply of freshwater by 38 percent by 2025, and in regions without extended drought conditions, the situation is even worse.”
– Brian Arntsen
Frito-Lay has a 160,000-sq.-ft. facility in Casa Grande, AZ that was built in 1984. Because this area is now water scarce, the company has made significant investments and technology upgrades with the goal to make the facility “near net zero,” running primarily on renewable energy sources and recycled water, while producing nearly zero landfill waste, reports Arntsen.
The facility recycles up to 75 percent of production water back into the facility, has a 36-acre solar field that generates 10 million kWh of electrical power, has reduced its natural gas consumption by 80 percent with biomass boilers (which use recovered wood and agricultural waste for combustion) and sends less than 1 percent to landfill by recycling and alternative uses, such as cattle feed. This ambitious environmental sustainability project won gold LEED certification.
The water recovery and reuse plant is designed to treat and recycle up to 645,000 gallons per day of processing water from the potato chip and snack manufacturing process for rinse and wash water for landscape irrigation. Using a process that incorporates clarification, MBR, activated carbon, disinfection and RO, the final product water meets or exceeds EPA primary and secondary drinking water standards. See the table for the results.

The Frito-Lay Casa Grande facility is an excellent example of how a food plant in the desert furthers sustainability by treating and recycling its process water.
Cutting transportation costs for wastewater
Baker Cheese has been producing cheese in St. Cloud, WI since 1916. In the 1950s, the decision was made to produce only mozzarella cheese and, through customer demand, created its Original Baker String Cheese. Today, the cheese maker uses about 2 million pounds of milk per day to make string cheese. Baker needed a change in the way it handled its wastewater.
Historically, all process wastewater had been hauled offsite to local municipalities, leading to high and increasing disposal costs. On average, at least 10 trucks hauled off wastewater every day. In addition to high costs, hauling the wastewater greatly limited the facility’s ability to increase production and reduce whey transportation costs. The problem with whey processing is that it generates three times more wastewater than current cheese processing flows. Building its own wastewater treatment plant (WWTP) seemed to be the only viable solution, but brought other challenges, such as complying with very stringent phosphorous limits and aesthetic concerns.
To meet the current and future needs of the facility, the Probst Group worked with Excel Engineering and CDM Smith to provide a WWTP that could achieve phosphorous effluent concentrations to less than 0.4 mg/l. The WWTP includes expandable ultra-filtration (UF) membranes and an anoxic selector tank used for nutrient control (enhanced biological phosphorous removal). The external UF membranes create a physical barrier that provides reliable low solids effluent for total suspended solids (TSS), compared to conventional solids-liquid separation technologies like clarification or dissolved air flotation (DAF).
Reliable solids removal is imperative for ultra-low phosphorus limits, as biological solids contain 3-7 percent phosphorous. A sludge digester was also installed, reducing typical sludge yields by 30-50 percent. To further reduce phosphorous and meet compliance requirements, Baker utilized a water quality trade (WQT), the first approved in the state of Wisconsin. To address the aesthetic concerns of Baker, a square concrete sludge tank was designed to block a circular concrete aeration basin, and a silo was used as a selector tank, allowing the WWTP to appear as part of the cheese plant.
The new WWTP and the WQT allowed the St. Cloud plant to handle its own wastewater and plan for production expansion. Operational costs are significantly lower than hauling costs had been. For the local community, these changes mean 90 percent less truck traffic on local roads and increased employment opportunities and local milk demand as production increases.
The WQT has numerous benefits in conjunction with the new WWTP. Currently, the facility is achieving phosphorous levels of less than 0.3 mg/l. And the 20 acres of prairie grass and native flowers that were planted as part of the WQT is helping to protect the local watershed and create a permanent conservation easement that will attract wildlife.
Water reuse pick of the year
CDM Smith announced that J.R. Simplot Company’s process water treatment and return plant (PWTRP) in Caldwell, ID (which CDM Smith designed and built) was recognized by the WateReuse Association as its 2016 Industrial Project of the Year.
Simplot, a producer of potato products, set an ambitious goal for the PWTRP, which was part of a major expansion to consolidate the company’s French fry production for major customers into a single facility: create a zero-liquid discharge facility and produce effluent suitable for reuse in production. The PWTRP accomplished Simplot’s challenging objectives through an innovative treatment system including primary clarification, anaerobic fermentation, enhanced biological nutrient removal for nitrogen and phosphorous, and activated sludge with membrane bioreactors followed by RO and chlorine disinfection. All RO brine is evaporated onsite in an innovative enhanced evaporation system.
The state-of-the-art PWTRP was completed in January 2014, and treats an average of 2.3 million gallons/day (mgd) of high-strength potato processing wastewater with a maximum capacity of 3.2 mgd. Approximately 1.7 mgd of water, equivalent to drinking water standards, is reclaimed and returned for reuse safely in the production process. An innovative spray evaporation technology disposes of up to 320,000 gallons per day of brine reject from the RO system. All remaining effluent is used for the irrigation of forage crops. Common-wall construction minimized capital costs and consolidated piping needs, minimizing operating labor and lowering the plant’s overall footprint.
“By working collaboratively throughout the design-build process, we were able to deliver the project on budget and against an aggressive schedule since the PWTRP had to be operational before the new production facility went online,” says Al Goodman, CDM Smith’s client service leader for Simplot. “Several treatment innovations are helping Simplot optimize their water management, meet recycling water quality goals equivalent to drinking water and advance Simplot’s sustainability mission. This creates what is truly a zero liquid discharge facility for Simplot and a flagship project that raises the bar for water reuse in food industries.”
Increasing amounts of potato wastewater = more energy
For Friweika eG, a potato processing facility in Weidensdorg (Germany), business was mushrooming, causing a serious problem for its WWTP. The WWTP needed to be expanded, but there was very little room to install more equipment. Besides meeting wastewater specifications, the facility uses the WWTP to produce biogas, which makes a significant dent in the facility’s energy bills.
Since its commissioning nine years ago, the aerobic biological stage of the wastewater treatment had been expanded several times, due to continuous increases in production and a related surge in pollution levels of wastewaters. However, after increasing aeration, expanding the hydraulic capacity and increasing its overall automation level, the original four-step combination compact system, with each step consisting of a sludge tank with a plunged packed bed and integrated secondary sedimentation basin, reached its capacity.
Considering the production expansion and the expected increase in the organic load also in the discharge water, Friweika needed to extend the aerobic treatment by adding a new system. The old system was designed to handle COD loads of 560 kg/d and was filled far beyond its capacity, reaching at times loads of 1,260 kg/d. But where to put the additional system? A new plant would have required a second “compact” round tank with dimensions of 22 m in diameter, and 6 m high—for which there was no space.
DAS Environmental Expert GmbH (Dresden) specialists were called in and worked out an innovative and effective solution. Instead of adding another “compact” system, DAS EE integrated a TFR (trickle flow reactor) into the plant design and achieved a reduction of special requirements by nearly 50 percent, compared to a classic compact system. Instead of a new building, DAS extended the old system by adding four TFRs, each three meters in diameter and eight meters high. In each reactor, the wastewater trickles down as a liquid film, and ventilators push air in the opposite direction, ensuring the continuous supply of oxygen necessary for the microorganisms in the biofilm as they perform the aerobic degradation.
The wastewater stream is separated into two parts, with one being treated by the old system and the other in the TFRs. Together, the two systems have a treatment power that has not yet reached its capacity, even during production expansions. The wastewater with inflow COD loads of about 3,500 mg/l (85 percentile) was cleaned to indirect discharger quality with TFR outlets containing less than 1,000 mg/l COD.
Keeping the “green” image
Stonyfield has always been dedicated to a “healthy planet” and educating its consumers and producers about the value of protecting the environment. So, it’s not surprising that its Londonderry, NH plant engineers work hard to reduce the water and energy used to make yogurt and reduce and recycle waste as much as possible. With this in mind, engineers reviewed a number of different wastewater treatment technologies, vendors and full-scale treatment options. Stonyfield selected ADI Systems to design and build a wastewater treatment system to meet newly mandated local effluent discharge limits.
The system is designed to pretreat equalized raw process wastewater with COD, TSS and fat-oil-grease (FOG) levels up to 5,000 mg/l, 550 mg/l and 500 mg/l, respectively. It consists of two stages: a proprietary Type S low-rate anaerobic ADI-BVF reactor, followed by an ADI-SBR aerobic polishing system. ADI Systems also installed a simple, natural and robust odor control system to purify the off-gas from the equalization tanks.
This combination of unit processes readily treats the high-strength, high-solids, high-FOG wastewater. The treatment facility produces minimal waste sludge for disposal, as well as a substantial quantity of biogas, which is recovered and used to heat the anaerobic reactor, improving performance and minimizing overall electrical energy needs for waste treatment.
The wastewater treatment system and waste-to-energy system allow Stonyfield to meet or exceed mandated effluent limits, so it can produce yogurt products without regulatory penalties. It also shows Stonyfield’s commitment to sustainable agricultural practices.
Sidebar: Floating wetlands, clean waterways
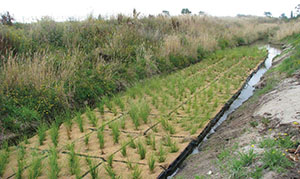
Could floating wetlands work in areas in the US where nutrient levels are too high?
Source: Fonterra/Living Water.
Developed by New Zealand’s Massey University and adopted by dairy producer, Fonterra, and the New Zealand Department of Conservation’s (DOC) partnership, Living Water, floating wetlands consist of native New Zealand wetland plants, tethered to buoyant mats or “rafts” that sit on the water surface. Capable of removing large amounts of nutrients, the rafts filter water in drains and runoffs before it reaches waterways.
“The floating treatment wetlands have only been installed for a relatively short time, but initial tests and the rapid plant growth indicate that they are doing a good job removing nutrients from the water,” says Michael Paviour, DOC community ranger. “The floating wetlands are by no means a silver bullet for solving water quality [problems], but when used alongside other activity, such as silt traps and riparian planting, they are proving to be a practical and effective method for improving water quality.”
For more information:
GE Water: www.gewater.com
The Probst Group: www.probstgroup.com
CDM Smith: www.cdmsmith.com
DAS Environmental Expert: www.das-ee.com; (USA): www.das-usa.com
ADI Systems: www.adisystemsinc.com
Looking for a reprint of this article?
From high-res PDFs to custom plaques, order your copy today!