Navigating the Data Sea
Food and beverage processors are striving to collect more and better data. But is your data gathering system doing the job you need?
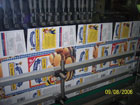
If your house was on fire, you'd need water to put it out. Would your garden hose solve the problem? Not likely. Would a tsunami help? Well, the fire would be out but you'd have a whole other problem. And so it is with data gathering. You don't need sky-high reams of data. You need the right data at the right time to make the best decisions. And, perhaps even more importantly, you need to be able to trust the data you receive.
The push to collect data is on. We see it in all forms of food and beverage processing and at plants all over the world. "Regulations on traceability and food safety are driving US and European food companies toward automation and control networked systems," says Jonas Westlund, a Frost & Sullivan industry analyst.
Food safety, global competition, customer demands for lower prices and on-time delivery are among the ongoing pressures on processing facilities. Hard work is not enough, operations need to be managed more effectively and that requires more and better information-hence the advent of data gathering, correlation and analysis.
Westlund sees a number of drivers behind these trends. "Traceability requires significant information to be effective and the cost and the possible disruption to production processes of collecting this data makes data collection an attractive investment. Rising raw material costs and increased competition from low-cost manufacturing regions such as China are pushing manufacturers to examine their operational efficiency."
Increasing efficiency requires information to pinpoint areas for improvement, evaluate potential benefits and track improvements. Customer consolidation is resulting in near non-negotiable demands for product variation, resulting in increased production complexity, improvements in on-time deliveries and lower costs.
"The net effect has seen food processors being put under considerable pressure to streamline their production processes in order to reduce costs, maintain efficiency and ensure profitability," says Westlund. "As a result, this is expected to drive investment in data collection, supervisory control and data acquisition (SCADA) and distributed control systems (DCS), which in the long term is anticipated to contribute to improved margins among food processing companies."
And yet, data costs money. It may be labor dollars, a negative impact on production, capital and maintenance costs or all of the above. No one method is best for all situations or all types of data.
Manual and automated data collection can live in the same house. An operator or warehouse person, for example, can collect and record data using automated devices like bar code or RFID readers, data terminals on the floor or handheld computers.
Bar coders were particularly effective for Berner Foods, a contract manufacturer of Swiss cheese for companies like Alpine Lace. A data collection system from Ross Systems helped Berner increase inventory visibility and accuracy and improved inventory tracking. By automating manual operations with bar code scanning, the company went from having a 14-hour lag time between completing a production cycle and updating the inventory, to a real-time process, enabling product to get to customers faster and more efficiently. In addition, Berner can now locate product in its warehouse in real-time, compared to the 30-minute to one hour window previously required.
Other food manufacturers are combining various technologies for an all-inclusive approach to data gathering. Sausage maker Odom's Tennessee Pride processes 76 million pounds of product per year and combines data gathering technologies to improve efficiencies. A recent upgrade to its Dixon, TN, plant included an expansion from four semi-automated packing lines to 10 fully automated lines. The project included data collection and analysis investments, which "allow us to increase the turns in our supply chain," says Mike Hader, Odom's director of IT.
At the Dixon plant, automated controls, including Rockwell PLCs, feed run rates and downtime data in real time. Production management uses this data for real time decision-making and analysis of history and trends. At casing and palletizing, carton and pallet identification is added and also tracked in real-time. When picking up product from the palletizer, forklift drivers read the pallet ID using Symbol Technology handheld readers. Since Odom's ships 50 percent of its cases directly from the palletizer, the forklift driver gets real-time delivery instructions. Production reporting is automated from the palletizer.
"Real-time data is a big plus but you need to plan for times when automation fails," says Hader. "Our people rely on the real-time data for real-time decision-making. You need definite plans to keep product flowing out the door."
Yet technical barriers can exist in data gathering. "We see three key issues. First, the automation level consists of a fire hose of data. It can easily overwhelm the systems that collect it. Second, the different systems talk in different languages. And third, we cannot assume that just because the numbers came from sensors or other automation equipment that they are correct. They must be validated in some way," says Gregg La Blanc, OSIsoft's technical director.
When asked how a food manufacturer should address these three issues, Blanc says, "That fire hose needs to be connected to real-time systems that can keep up. It needs to be designed to store data quickly, in a meaningful way. Typically, the data has to be stored with time being a key factor and the language issue requires some translation. For example, data from one source must be mapped to the needs of a receiving system. It may need summarization, for example, flow rates from a meter need to be translated into pounds for the ERP system. Finally, we need to validate the data from the floor. What if a meter fails or a float in a tank gets stuck. Previous readings and other run-related information must be used to test new readings to see if they appear to be correct."
Cargill implemented OSIsoft's PI product at its plants and, according to OSIsoft, the PI system solves the fundamental problem of getting access to all the data available in manufacturing operations. OSIsoft says PI can be extended to PI systems to meet supervisory, optimization and visibility type projects easily because the data is available online for years and years in common, intuitive tools. This makes historical analysis easy and helps illustrate long-term patterns that would otherwise be undetected as well as real-time process monitoring. "We continuously hear from our plant managers that PI enables a more intelligent use of people's time and resources. It is truly a powerful advantage when people have insight into operational information and can quickly make the right decisions," says Ron Christenson, corporate vice president and chief technology officer, Cargill.
In addition, Cargill is using OSIsoft's RtPM platform to combine multiple data sources and monitor critical systems, ensure that compliance standards are met and optimize resources. According to Christenson, the technology also helps sites identify and stay on target within various key performance indicators. For example, the information from various sources can be used to calculate materials, temperature and other factors against product produced to determine exact efficiency in a given batch or process.
Recently, Cargill announced that it would use RtPM to deliver real-time operational performance metrics across its enterprise. Cargill will look across multiple plants and production lines to benchmark equipment reliability, efficiencies and ultimately identify and expand deployment of those techniques and applications that deliver operational performance gains.
Whether you are using manual or automated data collection-or some combination of the two-it's vital that the data you receive be accurate and worthwhile.
Paul Moylan, Rockwell Automation, 919-465-1741 x 334, pemoylan@ra.rockwell.com
Kevin Prouty, Symbol Technologies, 781-334-5059, kevin.prouty@symbol.com
Mark Beatty, Steton, 435-627-5094, mark.beatty@steton.com
Ron Kolz, OSIsoft, 440-720-3670, rkolz@osisoft.com, 440-720-3670
Michael Putnam, MARKEM, 781-891-3279 x 3201, mputnam@markem.com
Mark Dessommes, LXE, 770-729-6643, dessommes.m@lxe.com

"Campina is saving money across six production plants and four co-packing sites," says Huub Buckx, head of Campina data & systems management. "We are also saving money for our third-party logistics suppliers because the automated labeling and tracking system information has helped them simplify their inbound and outbound operations." The system helped to improve on-time delivery, shorten delivery times and improve customer satisfaction. There are fewer mistakes in palletizing, picking and shipping. There are fewer customer returns due to incorrect product or expiration date and line downtime has been reduced. The system also provided more reliable data to the SAP system that allowed Campina to shorten planning cycles and provide more accurate and timely customer billing.
The new system has automated many traditionally manual tasks. The heart of the system is the MARKEM CoLOS software, which provides integration, product traceability and packaging line management. Each day, or as required, the SAP system transmits customer order information, such as lot number, product number and proposed ingredients to use for each order, to the CoLOS software. Using CoLOS, the supervisor can determine the actual ingredients to be used for each order, which matches ingredient lot numbers with product lot numbers. The supervisor can then plan and prioritize the orders for daily production and transmit this information to CoLOS for use by the shift operator. If necessary, the shift operator has the flexibility to further prioritize these orders to ensure maximum throughput. When the operator selects an order to run, the system prompts the operator to run a test label and confirm its accuracy and readability before actual product is labeled.
Based upon the order information from SAP and the in-line Mettler Toledo weigh scale, the correct labels for the product and/or box are automatically printed and applied by MARKEM printer/applicators. The applied labels are then verified accurate and readable by in-line bar code scanners. If they are not readable the system automatically stops the packaging line so that the operator can take appropriate action. The boxes continue on to the automated palletizer, which receives pallet loading instructions (the stacking pattern) from the order information in CoLOS Manager or it can be manually entered.
MARKEM CoLOS software automatically determines when the correct number of boxes of product has been stacked. The system automatically generates, stores and prints pallet labels with all the necessary product information and the pallet SSCC (serial shipping container code) number. After the pallet labels are applied, the operator uses a radio frequency wireless LXE handheld scanner to scan the pallet label and identify whether the pallet is going to shipping or warehousing. Using wireless handheld scanners CoLOS Ship keeps track of the progress of each order and provides SAP with order completion confirmation and warehouse and shipping information.
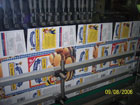
Odom's Tennessee Pride processes 76 million pounds of sausage products per year and combines data gathering technologies to improve efficiencies. A recent upgrade at its Dixon, Tennessee, plant included an expansion from four semi-automated packing lines to 10 fully automated lines.
If your house was on fire, you'd need water to put it out. Would your garden hose solve the problem? Not likely. Would a tsunami help? Well, the fire would be out but you'd have a whole other problem. And so it is with data gathering. You don't need sky-high reams of data. You need the right data at the right time to make the best decisions. And, perhaps even more importantly, you need to be able to trust the data you receive.
The push to collect data is on. We see it in all forms of food and beverage processing and at plants all over the world. "Regulations on traceability and food safety are driving US and European food companies toward automation and control networked systems," says Jonas Westlund, a Frost & Sullivan industry analyst.
Food safety, global competition, customer demands for lower prices and on-time delivery are among the ongoing pressures on processing facilities. Hard work is not enough, operations need to be managed more effectively and that requires more and better information-hence the advent of data gathering, correlation and analysis.
Westlund sees a number of drivers behind these trends. "Traceability requires significant information to be effective and the cost and the possible disruption to production processes of collecting this data makes data collection an attractive investment. Rising raw material costs and increased competition from low-cost manufacturing regions such as China are pushing manufacturers to examine their operational efficiency."
Increasing efficiency requires information to pinpoint areas for improvement, evaluate potential benefits and track improvements. Customer consolidation is resulting in near non-negotiable demands for product variation, resulting in increased production complexity, improvements in on-time deliveries and lower costs.
"The net effect has seen food processors being put under considerable pressure to streamline their production processes in order to reduce costs, maintain efficiency and ensure profitability," says Westlund. "As a result, this is expected to drive investment in data collection, supervisory control and data acquisition (SCADA) and distributed control systems (DCS), which in the long term is anticipated to contribute to improved margins among food processing companies."
And yet, data costs money. It may be labor dollars, a negative impact on production, capital and maintenance costs or all of the above. No one method is best for all situations or all types of data.
Clipboard is not dead
For short duration studies, situations where a minimum amount of data is infrequently recorded, or when a time delay does not rob us of the value of the information, manual collection (a pencil and a clipboard) may be the best method available. But the real problem with manual data collection is accuracy. One study found an error rate of one in 300 numbers being read and recorded accurately (as compared to one in more than 3 million by bar code readers). Forms can help by simplifying the task and thus helping to ensure consistency and accuracy. They can be preprinted or, even better, computer generated with key data completed in advance.Manual and automated data collection can live in the same house. An operator or warehouse person, for example, can collect and record data using automated devices like bar code or RFID readers, data terminals on the floor or handheld computers.
Bar coders were particularly effective for Berner Foods, a contract manufacturer of Swiss cheese for companies like Alpine Lace. A data collection system from Ross Systems helped Berner increase inventory visibility and accuracy and improved inventory tracking. By automating manual operations with bar code scanning, the company went from having a 14-hour lag time between completing a production cycle and updating the inventory, to a real-time process, enabling product to get to customers faster and more efficiently. In addition, Berner can now locate product in its warehouse in real-time, compared to the 30-minute to one hour window previously required.
Other food manufacturers are combining various technologies for an all-inclusive approach to data gathering. Sausage maker Odom's Tennessee Pride processes 76 million pounds of product per year and combines data gathering technologies to improve efficiencies. A recent upgrade to its Dixon, TN, plant included an expansion from four semi-automated packing lines to 10 fully automated lines. The project included data collection and analysis investments, which "allow us to increase the turns in our supply chain," says Mike Hader, Odom's director of IT.
At the Dixon plant, automated controls, including Rockwell PLCs, feed run rates and downtime data in real time. Production management uses this data for real time decision-making and analysis of history and trends. At casing and palletizing, carton and pallet identification is added and also tracked in real-time. When picking up product from the palletizer, forklift drivers read the pallet ID using Symbol Technology handheld readers. Since Odom's ships 50 percent of its cases directly from the palletizer, the forklift driver gets real-time delivery instructions. Production reporting is automated from the palletizer.
"Real-time data is a big plus but you need to plan for times when automation fails," says Hader. "Our people rely on the real-time data for real-time decision-making. You need definite plans to keep product flowing out the door."
Instant notification
A major advantage of real-time data gathering and analysis is instant operator notification of problems, whether they are simple data accuracy problems or operational issues. A provider of value-added egg products, Cargill's Sunny Fresh uses Steton's Quality Suite, which includes both data collection and analysis software to support quality assurance. "It was essential for the inspectors at Sunny Fresh to be immediately notified of out-of-compliant issues," says Karla Lombard, Sunny Fresh's quality assurance specialist. "With Steton Quality Suite, a pop-up window appears on the inspector's screen notifying him instantly when there are non-compliant issues, which enables us to assign corrective actions right away."Yet technical barriers can exist in data gathering. "We see three key issues. First, the automation level consists of a fire hose of data. It can easily overwhelm the systems that collect it. Second, the different systems talk in different languages. And third, we cannot assume that just because the numbers came from sensors or other automation equipment that they are correct. They must be validated in some way," says Gregg La Blanc, OSIsoft's technical director.
When asked how a food manufacturer should address these three issues, Blanc says, "That fire hose needs to be connected to real-time systems that can keep up. It needs to be designed to store data quickly, in a meaningful way. Typically, the data has to be stored with time being a key factor and the language issue requires some translation. For example, data from one source must be mapped to the needs of a receiving system. It may need summarization, for example, flow rates from a meter need to be translated into pounds for the ERP system. Finally, we need to validate the data from the floor. What if a meter fails or a float in a tank gets stuck. Previous readings and other run-related information must be used to test new readings to see if they appear to be correct."
Cargill implemented OSIsoft's PI product at its plants and, according to OSIsoft, the PI system solves the fundamental problem of getting access to all the data available in manufacturing operations. OSIsoft says PI can be extended to PI systems to meet supervisory, optimization and visibility type projects easily because the data is available online for years and years in common, intuitive tools. This makes historical analysis easy and helps illustrate long-term patterns that would otherwise be undetected as well as real-time process monitoring. "We continuously hear from our plant managers that PI enables a more intelligent use of people's time and resources. It is truly a powerful advantage when people have insight into operational information and can quickly make the right decisions," says Ron Christenson, corporate vice president and chief technology officer, Cargill.
In addition, Cargill is using OSIsoft's RtPM platform to combine multiple data sources and monitor critical systems, ensure that compliance standards are met and optimize resources. According to Christenson, the technology also helps sites identify and stay on target within various key performance indicators. For example, the information from various sources can be used to calculate materials, temperature and other factors against product produced to determine exact efficiency in a given batch or process.
Recently, Cargill announced that it would use RtPM to deliver real-time operational performance metrics across its enterprise. Cargill will look across multiple plants and production lines to benchmark equipment reliability, efficiencies and ultimately identify and expand deployment of those techniques and applications that deliver operational performance gains.
Whether you are using manual or automated data collection-or some combination of the two-it's vital that the data you receive be accurate and worthwhile.
For more information
Mike Mitchell, Ross Systems, 770-351-9600, michaelmitchell@cdcsoftware.comPaul Moylan, Rockwell Automation, 919-465-1741 x 334, pemoylan@ra.rockwell.com
Kevin Prouty, Symbol Technologies, 781-334-5059, kevin.prouty@symbol.com
Mark Beatty, Steton, 435-627-5094, mark.beatty@steton.com
Ron Kolz, OSIsoft, 440-720-3670, rkolz@osisoft.com, 440-720-3670
Michael Putnam, MARKEM, 781-891-3279 x 3201, mputnam@markem.com
Mark Dessommes, LXE, 770-729-6643, dessommes.m@lxe.com

An operator controls the MARKEM CoLOS station on the packaging line at Campina's dairy processing plant. CoLOS software provides integration, product traceability and packaging line management. Source: ARC Advisory Group.
Sidebar: Automating traditionally manual tasks
With thirty food processing facilities across Europe, Campina, a dairy processor, needs to have data it can trust. After examining areas where improvements could be made, the company concluded that it had inefficient logistics processes. The current processes had little uniformity from plant to plant, produced a variety of clerical mistakes and labeling errors, and would not be able to meet increasing regulatory and customer requirements. Campina decided that a new product and pallet labeling system would be required. The new system needed to handle both fixed and variable weight cheese and butter products, ensure improvements in logistical operations and improve product tracking and tracing. This would also require the system to provide automatic data exchange to and from the SAP system, as well as a straightforward way for future interface to the production system."Campina is saving money across six production plants and four co-packing sites," says Huub Buckx, head of Campina data & systems management. "We are also saving money for our third-party logistics suppliers because the automated labeling and tracking system information has helped them simplify their inbound and outbound operations." The system helped to improve on-time delivery, shorten delivery times and improve customer satisfaction. There are fewer mistakes in palletizing, picking and shipping. There are fewer customer returns due to incorrect product or expiration date and line downtime has been reduced. The system also provided more reliable data to the SAP system that allowed Campina to shorten planning cycles and provide more accurate and timely customer billing.
The new system has automated many traditionally manual tasks. The heart of the system is the MARKEM CoLOS software, which provides integration, product traceability and packaging line management. Each day, or as required, the SAP system transmits customer order information, such as lot number, product number and proposed ingredients to use for each order, to the CoLOS software. Using CoLOS, the supervisor can determine the actual ingredients to be used for each order, which matches ingredient lot numbers with product lot numbers. The supervisor can then plan and prioritize the orders for daily production and transmit this information to CoLOS for use by the shift operator. If necessary, the shift operator has the flexibility to further prioritize these orders to ensure maximum throughput. When the operator selects an order to run, the system prompts the operator to run a test label and confirm its accuracy and readability before actual product is labeled.
Based upon the order information from SAP and the in-line Mettler Toledo weigh scale, the correct labels for the product and/or box are automatically printed and applied by MARKEM printer/applicators. The applied labels are then verified accurate and readable by in-line bar code scanners. If they are not readable the system automatically stops the packaging line so that the operator can take appropriate action. The boxes continue on to the automated palletizer, which receives pallet loading instructions (the stacking pattern) from the order information in CoLOS Manager or it can be manually entered.
MARKEM CoLOS software automatically determines when the correct number of boxes of product has been stacked. The system automatically generates, stores and prints pallet labels with all the necessary product information and the pallet SSCC (serial shipping container code) number. After the pallet labels are applied, the operator uses a radio frequency wireless LXE handheld scanner to scan the pallet label and identify whether the pallet is going to shipping or warehousing. Using wireless handheld scanners CoLOS Ship keeps track of the progress of each order and provides SAP with order completion confirmation and warehouse and shipping information.
Links
Looking for a reprint of this article?
From high-res PDFs to custom plaques, order your copy today!