Dairy integrates plant intelligence with ERP
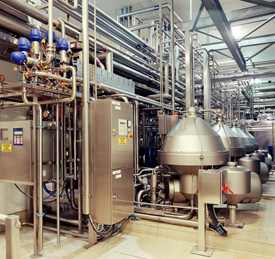
The system provides total traceability from raw goods to final packaging
Dairy Crest’s Severnside dairy in
Working in cooperation with the Severnside team, as well as Dairy Crest’s corporate Oracle integration team, FMA scheduled all work to take place during a series of planned outages to minimize impact on production.
Involving the complete integration of the plant control system with Dairy Crest’s Oracle ERP system, the project has enabled key plant operating data to be automatically provided to the ERP system. The existing FMA-installed plant IT system already had been producing Web-based reports for operations from automatic production data capture.
The integrated IT solution developed by the integrator ensures the regular uploading of dairy production records, plant utilization, ingredients usage, quality information, genealogy data and other production information. Key business-critical elements of this data are now integrated into the Oracle system.
Plant data automatically is recorded in real time to provide a precise, historic record with key data, also now being provided automatically to Dairy Crest’s group-wide Oracle ERP system.
The key benefits of the integration project provide Dairy Crest Severnside with:
- Total traceability from raw goods intake to final product packaging;
- Comprehensive losses tracking, in relation to geography, departments, processes and procedures;
- Rapid batch tracking of all processes and events;
- Fully automated reporting and forward/backward genealogy;
- Transparent auditing and more easily followed audit trails;
- Greater transparency of all production processes.
Integrating production data into the corporate ERP empowers Dairy Crest management with the information necessary to better operate the business in real time, something that simply would not have been achievable with a paper-based system.
“When Severnside was originally commissioned,” comments FMA Managing Director Terry Clough, “there were no Dairy Crest corporate plans for such high levels of automatic data transfer. Through our integration activities, the dairy now benefits from a [capable] information system, one that is sufficiently powerful and versatile to enable operational decisions to be implemented and acted upon in real time.”
For more information, contact FMA Process Engineering.
Looking for a reprint of this article?
From high-res PDFs to custom plaques, order your copy today!