You think your dairy processing plant is efficient, but when you do the math, you can’t account for 7 million pounds of lost milk per year. That’s a loss of more than $1 million. In addition, your POTW is billing you more than $80,000 annually for exceeding the maximum permitted levels of fats, oils and greases (FOG) in your wastewater. What’s going on? Seems like money down the drain, doesn’t it?
Unfortunately, stories like this are not uncommon, especially when you don’t know what’s going on in your process. And, as Murphy’s Law’s first corollary states, “Left to themselves, things tend to go from bad to worse.” Most likely, without intervention, this dairy facility would have seen even worse numbers as time went on. Fortunately, this story has a happy ending. Vigilistics, Inc. (now part of SafetyChain Software) production management software was employed to get a handle on what was happening to the “spilt milk.”
The advanced controls software includes real-time data collection from the plant floor. To get started, engineers segmented the plant into key performance areas. Then, key performance metrics were established using the data collection engine for each key step. Up and running, the system revealed a measurable shrink, and the dairy was able to reduce the shrink from 2.5 percent to less than 1 percent the first year, translating to an annualized savings of $600,000. The dairy was able to stop the FOG from going to the POTW and realized an additional $80,000 savings the first year.
The Vigilistics system includes real-time variance reporting and collaboration, which highlight variations from the key performance metrics. Operators are alerted to problems before they expand to become significant issues. In addition, milk receiving and cream load out procedures were adjusted, and operators were retrained as needed to understand procedures. Production planning adjustments were made to avoid unnecessary product changeovers and minimize recycle time on the pasteurizer—the time to change from product to water and water to product was reduced to an acceptable level. Filler loss and overfills were reduced, and the production of unsalable product was reduced. Waste stream FOG levels were monitored and managed.
Advanced process control and suitable applications
While you might think of advanced process control (APC) as sophisticated model predictive control (MPC) systems, neural networks or advanced regulatory control (ARC), even data historians coupled with SPC (statistical process control) may actually be more “advanced” than what some processors are using.
“A production historian is a must-have for processors to improve process efficiency,” says John Tertin, director of manufacturing information systems, ESE Inc., a member of the Control System Integrators Association (CSIA). “While food processors are starting to adopt this technology, the number of major processors that haven’t yet is astounding.”
While installing a data historian is a good first step, processors need to consider how to present the data so users are able to visualize problems and make corrections. For example, Peco Foods, which makes boneless breast products for retail and foodservice markets, found itself with problems faced by many processors: manually entered data filled with errors and no way for operators to view failures or an out-of-control process. The processor wanted a solution that would provide:
- Reliable electronic data collection with threshold alarms that could instantly notify key personnel of problems
- Easily visible scoreboards to keep everyone on the plant floor fully informed
- Real-time reporting with SPC analysis capabilities
- 100 percent ROI in less than a year.
Peco found a solution that fit its needs in CAT Squared’s (CAT2) Food Safety and Quality Management (HAT) and SPC Charting software. Peco also installed 55-in. flat-screen monitors encased in IP69K-rated enclosures and used CAT Squared’s Professional Services. Peco is now able to analyze extensive quality and production data in real time and respond as problems occur, changing its business practices from reactive to proactive.
“Before HAT, it was like playing a basketball game and telling your team, ‘Push hard! We can win!’ but never keeping score,” says Tony Pierce, Canton, MO plant manager. “Now we keep score from the beginning of the game.”
It’s no surprise that properly applied controls can save money and product, as in the previous dairy processing plant example. The point is, often a little change can make a big difference, and the challenge can be in knowing what and where to look for improvements.
“Plant mass balance and product loss reductions can be a real challenge for food plants,” says Ola Wesstrom, Endress+Hauser USA senior industry manager, food and beverage. “The variability in raw ingredients needs to be accounted for, as well as real losses from changeovers and cleaning. There is also what I consider accounting losses, which can be much harder to identify. What I mean by this is the possible impact of measurement[s] tolerances, temperature influence of volume and mass, etc. Virtual process valves can sometimes be applied to APC, but need to be validated carefully to ensure correct information is used.”
“One of the most costly issues for food and beverage processors is overfill, or giveaway,” says Steven Voight, InfinityQS International client solution engineering manager. “This happens because producers tend to add extra product—creating excessive variation in the filling/product sizing process—to ensure that average fills and individual package fills meet or exceed the minimum regulatory standards. As a result, these companies use more ingredients than necessary in production.”
By implementing SPC methodologies, as well as APC, manufacturers can minimize these variations and set their overfill volume to the lowest possible level, while still ensuring regulatory compliance. InfinityQS has performed analyses for numerous food and beverage processors on this issue and determined, especially when premium ingredients are used, that overall reduction in overfill amounts can save millions of dollars each year, adds Voight.
ICONICS implemented a solution for a confectionery processor where yield was improved by monitoring turn of scale (TOS), the percentage that the processor gives away to the consumer.
“Using a data historian [utilizing big data] and the addition of performance calculations, we helped to monitor, manage and reduce this loss,” says Adam Meunier, ICONICS product marketing manager. “Implementing simple systems, such as performing scrap/rework reason collection via handheld devices, allows insight into the plant’s biggest issues.”
The continuous monitoring of weights and temperatures using SPC allows for real-time monitoring and alerting. Rules can be configured and monitored for control limits, adherence to specifications and trends within the data. Real-time monitoring also paves the way for users to implement a closed loop-back scenario that allows the APC software to take action, adds Meunier.
For F&N Dairies in Thailand, overfill was an issue until the company used Schneider Electric’s Wonderware Line Performance Suite software to create its Process Nexus II system to monitor and record net control, which measures product net weight and product loss during the manufacturing process. The captured net weight is plotted to show its trend; from there, the operators are able to calculate overfill in real time and react immediately to address overfill issues to minimize loss.
“Imagine manufacturing 3 million cans per day: How do you control each can’s net weight to ensure it is properly filled with little to no overfill?” asks Somchai Khwahan, F&N Dairies production manager. “This was an issue which our team faced daily, and eventually, the paper-based recordkeeping processes were not able to keep up with our rapid production, so we developed Process Nexus II to capture this information.”
“There are many applications that benefit from APC technology,” says Michael Tay, Pavilion product manager for Rockwell Automation. “However, some more frequent applications to which the technology is applied include most drying processes, evaporation, standardization and line optimization on integrated processing, such as French fry or cereal production.”
One advantage we have today—if sensors are in place—is a large amount of data, or “big data.” “A key advantage in working with big data is that it enables predictive advanced monitoring,” says ICONICS’ Meunier. “This involves running simulations and calculations to predict scenarios based on the outcome of altering variables in huge datasets. For example, if a company’s production is affected by weather conditions, a prediction can be made as to what quality and amount of product can be produced based on various specified criteria. This can then be correlated with budget forecasting. It can even allow for production schedulers to alter production schedules based on such models. The more comprehensive the data, the more accurate the model of how weather affects production is likely to be. Of course, there are other factors that can also influence the variable you are trying to predict.”
Model predictive control (MPC) is one form of APC that can be applied to a few specific food and beverage applications, but when it is applied can make a real difference. (For more details on MPC, visit “Predict the future: Get control of your process,” FE, April 2015.) Some specific applications geared to MPC include distillation, drying, evaporation—and perhaps others such as crystallization, mashing, fermentation, etc., says Lou Heavner, Emerson consultant.
Narrowing down where yield losses occur
Processors usually know where their losses are happening, says Wesstrom. However, the key is to determine whether this loss is real or accounting.
“Then narrow down to specific areas to evaluate what can be done to address the situation and determine ROI,” he says.
For those that already have good loss tracking and a fairly good handle on sources of yield losses, Rockwell’s Tay says there can be unit challenges.
“Fewer customers have these losses pulled together on common engineering units,” he says, which makes it “easy to rank where the largest challenges are and which losses show the largest variation over time.”
“Most problems that are amenable to process control improvements come down to variability,” says Emerson’s Heavner. “We look for variability and for ways to attenuate it. With a reduction in variability comes an opportunity to push the process closer to constraint limits, which leads to many economic improvements.”
Often, it’s a matter of talking to the right people and asking the right questions, says InfinityQS’s Voight. He suggests asking for insight on a yield problem from an experienced line operator rather than a quality manager.
“One issue we encounter regularly when implementing our software solutions is the lack of standardization of processes between different sites, departments, shifts or even individual operators in the same company,” says Voight. “Management will naturally assume that all operators follow the established ‘official’ documentation when that’s not often the case. The extent of processing variation typically lies undiscovered until we help the manufacturer develop and implement standard data collection and analysis protocols for the enterprise.”
With the right software tools, operators who’ve experienced ongoing problems are keyed in to solve problems. For example, Country Maid was having problems with dough consistency at its bakery and was unable to resolve them until a Rockwell Automation PlantPAx system was installed. With the new software, operators were able to determine that the problem was related to changing climatic conditions in the facility’s flour storage silos located outside the building, the company took action to correct the silo climate conditions, and the dough consistency problems were gone. (For more on this story, visit “System integration: Tales from the trenches,” FE, Nov. 2014.)
APC tools
APC tools can include MPC, SPC, advanced regulatory controls (ARC) and others. ICONICS’ Meunier adds to the mix Six Sigma, Kaizen and TPM initiatives.
So what can you expect from APC or ARC? When a yield problem exists, should you look at APC first? It depends.
“Advanced regulatory control using regulatory techniques is a common starting point,” says Emerson’s Heavner. “Control performance services should not be overlooked, even if it isn’t a product per se.”
Most processes benefit from a good analysis and improvement of the basic regulatory controls. “Inferential sensors can be a part of this, and we use neural nets in some cases,” adds Heavner. MPC is an excellent approach for dead-time dominant processes like evaporators, interactive processes like distillation and anywhere there is an opportunity for constraint optimization. “Most of these APC solutions have a typical simple payback of approximately six months, but vary from two to 14 months,” adds Heavner.
Yield improvements often have the best return on investment compared to energy savings and increased production, but many projects benefit from a combination of yield, energy savings and increased production. Inferential sensors (aka soft sensors) may not have a payback per se, but when considering the cost of an online analyzer, they can be quite attractive as an investment, says Heavner.
What about SPC?
“SPC can help resolve yield problems,” says InfinityQS’s Voight. “However, this methodology is most effective when applied to process input rather than outputs, since it’s more valuable to control variation before a product is manufactured.”
This requires the ability to automatically capture and analyze process inputs, as opposed to waiting for an operator to read and manually enter values. Often, however, these machine outputs do not by themselves contain all the information required to make accurate processing decisions, says Voight.
“For example, a continuous oven may output temperature and belt speed, but not important parameters like product or lot number, which might be available from an MES or ERP system,” adds Voight. “A truly flexible, automated data capture solution [like InfinityQS’s Data Management System] can combine inputs from multiple sources to produce powerful and actionable quality data.”
Batch and APC
Most food and beverage processors have manual batch systems in place. So is it a good idea to use APC to augment batch, or does it make more sense to replace it—and if so, with what?
“Advanced processes within a control system are intended to supplement existing batch system controls by offering advanced features that do not directly control the process, but rather augment the process,” says Meunier. “Features that analyze historian data, ARC, MPC, inferential control and sequential control can all be combined to provide advanced, hyper-efficient process abilities.”
While these features do not necessarily run the basic processes themselves, the features may become more critical and eventually the base of food and beverage manufacturing, says Meunier.
For example, Meunier notes that a food processing customer was dealing with products that were overweight, and the processor seemingly had no control of the involved process. Products were returned due to poor quality. After implementing the ICONICS solution, the process could be controlled, and weights were brought in line with the correct SKU information. Product quality improved, and first-time pass rate increased by 45 percent. Following the software implementation, an ROI was achieved within one year. More significant, in this application, no hardware changes were necessary for the software implementation.
Some food and beverage batch applications might be better controlled as a continuous process, but this will mean adding sensors that are up to the task.
“Eliminating or augmenting the manual batching control with accurate metering instrumentation can greatly improve product quality and reduce losses,” says E+H’s Wesstrom. “Inline quality monitoring of viscosity, Brix, dissolved oxygen, color or other relevant parameters can enable the conversion of a batch to a continuous approach.”
“APC can be used on a batch system, but it would focus more heavily on things like startup/shutdown practices, preheats, ingredient measuring, etc. than a continuous process system would,” says Voight. “If feasible, the migration from a batch to continuous processing model could certainly result in lower variability, but increasing throughput would likely be the predominant motivation.”
“Batch processes aren’t the most attractive candidate for APC and may require a significant process redesign to convert the process to continuous,” says Emerson’s Heavner.
The pharmaceutical industry is wrestling with this as it looks to adopt more continuous manufacturing. Most batch processes have some continuous processing unit ops in the facility. These would be obvious candidates. Blending is a good application where sequential blending can be easily and economically replaced with continuous parallel metering. Batch operations with long phases or steps are also good candidates. Inferential sensors can be beneficial for both batch and continuous processes, adds Heavner.
Some batch processes gain from a distributed control system (DCS) implementation, which is typically used for continuous processes. For example, Carlton and United Breweries (Australia) was being stretched too thin—even with eight packaging lines that typically ran 24 hours a day.
“We just couldn’t manage the number of brands we were being asked to make. So we had to increase our plant flexibility from both a technological point of view and to make our people more efficient and flexible as well,” says Matthew Anderson, plant manager.
To retain its competitive edge, the company replaced the control system for the filtration room—the plant’s nerve center—in the Abbotsford brewery. The new system centers on Emerson’s DeltaV distributed control system; digital valve controllers; and pressure, temperature, conductivity and flow measurement instrumentation.
The new system provides many improvements including increased product capacity, on-spec product, production flexibility, operator capabilities and troubleshooting capacity; reduced unplanned shutdowns and maintenance costs; and faster product-to-market response time.
“If we had major breakdowns in the past, we had to shut the whole plant down,” says Rob Glastonbury, project manager. “With this new system, we’ve got a window on what’s actually happening in the plant, and we now feel we can get to problems before they are breakdowns.”
For more information:
Steven Voight, InfinityQS International, 703-961-0200,
svoight@infinityqs.com, www.infinityqs.com
Ola Wesstrom, Endress+Hauser, USA, 317-535-2134,
ola.wesstrom@us.endress.com, www.us.endress.com
Adam Meunier, ICONICS, 508-543-8600,
adam@iconics.com, www.iconics.com
John Tertin, ESE Inc., 715-387-4778,
tertinj@ese1.com, www.ese1.com
Michael Tay, Pavilion Technologies (Rockwell Automation), 512-438-1482,
www.pavtech.com
Lou Heavner, Emerson, 512-834-7262,
lou.heavner@emerson.com, www.emerson.com
Sidebar: Integrated automation system yields optimized production
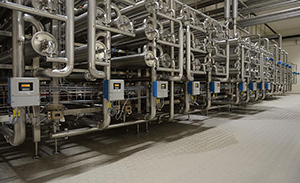
Fonterra was able to deploy a completely integrated control solution from Rockwell Automation, which offers advanced controls over a plant-wide network, offering communications from the shop floor to the top floor. Source: Rockwell Automation.
Fonterra Co-operative Group Ltd recently built a new dairy ingredients plant in Heerenveen, the Netherlands. The facility produces three variants of lactose powder and a range of protein products including whey protein concentrate and isolate and a lipid-rich whey protein concentrate, as well as several functional protein powders. Fonterra, which uses Rockwell Automation platforms in its home country of New Zealand, worked with Beenen B.V, a Rockwell Automation Recognized System Integrator to design the plant’s controls.
Fonterra was able to deploy a completely integrated solution from a single supplier that also offers effective communication from the shop floor to the top floor. Production data can be captured, collated and analyzed to improve processes, and Fonterra can share vital manufacturing information with a variety of disciplines both inside and outside the plant.
The entire software system provides advanced controls capability over all plant processes. FactoryTalk View offers overall visibility into the processes and interfaces with the ERP and process control systems. FactoryTalk Historian is used for data collection, and FactoryTalk VantagePoint is used for information, visualization and dissemination. By making data freely available in an easy-to-read format, operators and managers are able to make much more informed decisions, much more quickly and with greater positive effects on the line optimization.
“We knew from the start that we wanted to use Allen-Bradley PACs and control solutions,” says Hans Berghorst, operations director at Fonterra. “We do a lot of joint development with Rockwell Automation back in New Zealand, so it is easy to copy and paste routines and programs. In addition, we have specialists in our process control department in New Zealand who know and understand Rockwell Automation solutions very well. Also, from a support point of view, it’s always better when you have a standardized solution.”
Sidebar: APC and ERP
How should APC connect to MES or ERP systems to help processors achieve their desired cost containment calls?
“ESE provides two-way communications with MES and ERP systems for two main applications: production scheduling and paperless recordkeeping,” says John Tertin of ESE Inc.
When an order is received and entered into a processor’s ERP system, it is typically broken into several production runs by the production manager and delivered to the plant floor where an operator(s) configures the control system (batch size, formula, etc.) to run one or more batches to fill the work order. This method of production is both inefficient and prone to error. Scheduling production runs to minimize equipment changes or overlap is time consuming, configuration of recipes and formulations by operators on the plant floor can introduce error, and making changes to a schedule is difficult since it is largely a manual process of printing and delivering new copies of a paper production schedule, says Tertin.
Production systems can suffer from the lack of an ERP system fine-tuned to manage inventories for food processors. With 20 percent growth per year, Savoury Systems International tried to manage inventory and wound up typically with overstocks to compensate for orders. Without inventory management and forecasting tools, the company typically had $2 million in extra inventory that was eliminated when it added Sage ERP X3 with Sage Inventory Advisor and Sage Enterprise Intelligence. Since installing Inventory Advisor, stock-outs are at all-time low, and orders are filled on time.
The preconfigured KPIs in Enterprise Intelligence provide the processor with an instant way to measure the performance of every department.
“Previously, department managers lacked the measurement tools they needed to maintain the continuous improvement we strive for,” says David Adams, Savoury Systems president. “Now, they have the KPIs that enable them to head off problems and nimbly respond to changes.”
In addition, the traceability features in the ERP system help the processor maintain quality control, product consistency and food safety.