Palletizing solution encourages flexibility
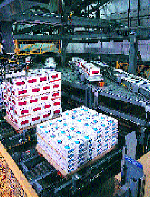
When a large gum manufacturer recently decided to automate its manufacturing and distribution center, it called on Alvey Systems, Inc., for help in designing a system that is sufficiently flexible to keep up with an explosion in stock keeping units (SKU) resulting from the introduction of new case sizes and weights.
At the time the manufacturer produced some 96 different SKUs, with cases ranging in weight from four to 50 pounds. Increased efficiency and improved ergonomics were key requirements of the system.
Flexible programming is key to the gantry palletizing system's ability to handle a variety of case sizes and weights. Each of five gantries can handle a variety of product with minimal changeover. A five-axis configuration -- which includes the X, Y, and Z axes plus rotation and tilt -- allows cases, particularly smaller ones, to be placed in a tight pattern that enhances load stability.
After installing the system, the company found it could produce a smaller case. Although the smaller cases didn't exist when the system was first specified, the flexible programming allowed workers to quickly and easily introduce the new case size into two gantry systems, which continue to handle the larger case sizes as well.
Looking for a reprint of this article?
From high-res PDFs to custom plaques, order your copy today!