Still entering your production data on clipboards? Still hoarding away chart recorder output in shoeboxes? Still transferring your data into Microsoft Excel spreadsheets? Want to “upgrade” your manual system? Behold, the auditor stands at your door and knocks. Will you be ready?
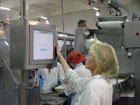
MES software should give operators the tools to do their job, not complicate matters with overly complex screens and confusing information. Source: CDC Software.
The real world
I received a phone call from a processor a few months ago, and had it not ended by the caller saying, “Whoops, the auditors are here; I gotta go,” I might not have given it a second thought. Seems he, like other manufacturers, is still managing his processes the old-fashioned way: clipboards, spreadsheets, charts, paper and pen. When the auditor shows up, he scrambles to find needed records. The caller (from a small company that employs 100 people) and I spent 30 minutes discussing software options to automate the process, keep track of batches and track and trace.Unfortunately, the first complaint that many small processors have is “Software is just too expensive,” and the second, “It will cause people to have to relearn their jobs.” While the first issue may be true and a hard pill to swallow, the second complaint about relearning jobs may be the most important. Manufacturing execution system (MES) software, sometimes known as “shop floor” software offers modular products and solutions without a plethora of expensive tools that will never be used. In many cases, software developers who write products specifically geared to the food and beverage industry will understand a processor’s needs and its ability to pay for software. And in some cases, the use of this software will transform people and the way they do their jobs-which is good!
Marsan Foods (Scarborough, ON) employs 100 people in two facilities and provides frozen prepared entrees, soups and sauces to national brands, store brands and club stores as well as restaurants and hospitals.
Faced with significant growth, Marsan built a new plant in 2000 and installed high-speed production lines. Although one line is capable of producing 125 meals per minute (60,000 meals per shift), Kristoffer Soderlind, director of operations, says the company could run just 30,000 to 36,000 meals on a good day. He expected better numbers, and he needed to know why he wasn’t getting them. Old methods of logging shift and manufacturing data on clipboards weren’t getting the job done.
“You need information to be able to solve your problems. Using clipboards is just wasting your time,” Soderlind says. He needed to get hold of downtime, machine yield and weights. On a suggestion from an equipment supplier, he and the company’s president looked at CDC Software’s CDC Factory.
Marsan’s president visited two up-and-running applications in England and thought the system would provide value to his company. Soderlind was looking for a solution that used good manufacturing practices, but he didn’t have the time to program software or learn the complex nuances of different manufacturing theories, and he wanted something plant floor operators could understand.
The solution worked. On the one large line, he has seen overall equipment effectiveness (OEE) increase from 65 to 74%, and he reports figures of close to 80% in the last three months. The software shows what’s causing downtime and allows staff to find new ways to fix problems. In fact, by adding an extra sauce pump in a line and cleaning a sauce hopper for each SKU, he was able to reduce downtime due to product changeovers from 50 minutes to 30 minutes
“Before [using MES], we always said that continuous improvement is important for us, but it was primarily at the management level,” Soderlind states. “Now when the operators on the shop floor can be part of this, there is more accountability, and they enjoy coming to work.” And, yes, MES has justified its cost a couple or more times over.

Chocolate Potpourri, a small specialty company with 20 employees, uses SYSPRO ERP software to gain the efficiencies of an integrated, real-time database. In the past, the processor had several non-connected databases and applications and no quick way to make important decisions. Source: SYSPRO.
MES ill-defined
The foregoing example shows how MES can benefit processors. But one of the problems hindering its widespread acceptance is that MES has not been clearly defined, although it would seem MES should at least be capable of downtime monitoring, batch records, track-and-trace, quality, OEE and SPC-to name a few. Over the years, ERP software, traditionally steeped in accounting functionality, has been extending its functionality toward the plant floor, providing some or all of these capabilities.Meanwhile, process control software has added many of these functions, working its way up the enterprise hierarchy. MES software was supposed to be the missing link between enterprise and process control system. Should it inherit ERP functionality? Should it perform data acquisition and PID control? What modules should it have? In many cases, MES has had too much complexity and in other cases, not enough to be useful.
Trying to categorize what MES is and where it fits in may be part of the problem. According to Terry McCorriston, director, CSB-System International, “I think the small guys make a huge mistake by thinking in categories like MES, ERP, SCM, SCADA, etc. Historically these multiple systems loosely connected to each other have never worked, not for the small guys and very limited for the big guys. What [the small guys] need to focus on are the business processes and how to collect or record the data once, for all areas to use.”
In the food industry, Microsoft Excel may be the logical next step from paper records. Claus Abildgren, Wonderware marketing program manager, laughingly defines MES as “Microsoft Excel Spreadsheets.” According to Siemens Energy and Automation’s US MES Marketing Director, Maryanne Steidinger, “The two products we see that are used for tracking and tracing of lots are typically Excel or Access. We laugh and say that Microsoft is our biggest competitor.”
“In all honesty,” she adds, “processors have to start somewhere, and depending on a processor’s size, a paper-based system will work fine for a number of years.” But when sales really take off, output and growth will be more than paper systems and Excel can handle.
Another problem for its acceptance has been the way MES is sold. Because it occupies the “middle” space between ERP and process control, many MES suppliers have duplicated much of ERP and process control functionality without really providing users what they need on the shop floor. It’s no wonder that this shovel-ware attitude is not the right approach. “The last thing you want to do with a mom-and-pop company is to sell them 25 modules they won’t need,” says Martin Michael, Advanced Automation’s VP business solutions. Food processors know they need to improve their business; that’s why they start with Excel. “In my opinion,” says Michael, “if you’re using Excel and its power, you are to some degree getting MES. The thing you don’t get with Excel is organized data-it’s often fragmented.”
But many MES products are just as fragmented. According to Mark Sutcliffe, general manager for CDC Factory, the reason MES hasn’t taken off is because it’s still a scrambled, piecemeal sector with lots of design and build solutions, which are more programming-like, rather than business solutions. “I think that’s because it’s been built out from engineering and controls and not from the organizational and results perspective of the business,” Sutcliffe says.

Today’s MES software can locate recurring problems and calculate OEE. It’s important to have the hardware and communications architecture in place so MES can collect data automatically and find problems in real time. Source: Schneider Automation.
ERP can also deliver MES
MES-like tools, however, are not mutually exclusive to ERP systems. “Batch processing, lot tracking and traceability, downtime monitoring, etc. are all covered in a quality ERP program,” says Rebecca Gill, vice president, Technology Group International. ERP packages, says Gill, will have readily available the vast majority of food-based manufacturing requirements if the processor is looking at a package geared toward small- to medium-size businesses (SMBs). These include production planning and forecasting, scheduling, recording and full lot control capabilities. What will differentiate these ERP products is the software vendor’s knowledge of the food and beverage industry. Gill asks, “Do they understand batches and scalable formulas, ingredients, substitutions, etc.?”An example of ERP vendors offering MES-like functionality comes from Lawson’s QuickStep product, which now offers asset management. According to Rob Wiersma, director of industry strategy, food and beverage, “ERP functionality today includes capabilities such as inventory management, traceability and asset management.” He adds, “With QuickStep, we can get a smaller but growing company up and running in a shorter period of time with standard business processes already defined for the food industry.” Wiersma says his company can help processors focus on planning, analysis and inventory management.
ERP vendors that focus on small- to medium-size food processors tend to develop industry-specific modules. Rene Inzana, SYSPRO product marketing manager, lists some of them: goods in transit, lot traceability, finite scheduling, landed cost tracking, quality data collection (warns of out-of-tolerance conditions), engineering change control, material variability and dynamic formula adjustment, inventory management (multiple units of measure and variable or catch weights), low-cost manufacturing (keeps finished goods inventory at a minimum), shop clock (monitors employees’ time, attendance, time spent on jobs and operations), customer service management, trade promotion and deduction management system.
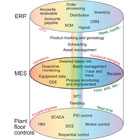
MES software allows operations and functional managers to get an overall view of the plant. MES functionality has always included traditional shop floor functions (e.g., scheduling, asset management and product tracking), but many ERP systems duplicate these modules. Today, MES software often duplicates some plant floor functionality such as SPC and trending.
Getting started
Advanced Automation’s Michael says that while it would be possible to take the processor’s existing spreadsheets and make a custom MES product, it may not be the most cost-effective option. This is when it’s a good idea to enlist the help of an independent system integrator (SI) to assist in a “make or buy” decision on software. The SI can help define the processor’s business objectives and priorities and map a strategy for the next several years. Michael provides some basic tips for small processors just getting started:Unfortunately many processors are still suffering the “islands of automation” syndrome and need some basic architecture, says Schneider Electric Food Processing Development Manager, Rusty Steele. In many cases, automation providers and SIs can do this. He recommends a three-step process:
1. Make sure there is a control layer (at least sensors, e.g., temperature, weigh scales, pH, etc.) for the collection of data and a network to support it.
2. Add a repository layer. A SCADA system and or data server to connect to MES and ERP systems through ODBC or through OPC servers (a slightly higher investment).
3. Implement MES modules necessary to the operation of the plant: e.g., SPC, OEE, monitoring KPIs, downtime monitoring, etc. Don’t implement modules that will have no benefit.
Arming with information
Wonderware’s Abildgren points out the value of information SMBs will find with monitoring the data. Once a processor gets started with automatic data collection, it realizes the value of a report is increasing the understanding of the process. In addition, the report can compare current results of the process with results that are two weeks old, providing valuable troubleshooting information. This, he believes, is where purchased software may be able to better grow with a processor’s needs because a custom-built system may require more frequent attention from a programmer.Sutcliffe says that it’s not only management that needs access to the information. “People on the shop floor should be counted as assets.” He adds that operators should have actionable information; they shouldn’t have to crunch numbers or rely on paper records. When operators can make intelligent choices, they can be part of the change process.
Therefore, says Abildgren, give operators the information they need to set up a machine for the next batch based on the information collected from the last time the same recipe was run. It might be a Pareto chart of the most frequent reason codes for machine stops. A central definition for the sequence of operations should be available for setting up the machine, and setpoints and data should be downloaded to the machine. Abildgren calls this part of operational discipline, and this discipline should be taken away from supervisors and given directly to the operators.
Can I afford it?
Fortunately, most vendors offering MES capabilities realize there are simply many more SMBs than there are Fortune 500 companies, and they have tailored their pricing structures to make sure an SMB can get started with MES, which can provide both automated production and performance systems.Some vendors now offer pricing based on number of transactions processed (the smaller the company, the fewer the transactions). Another pricing method includes base cost of packaged software plus the actual modules used, which allows the user to pay for exactly what is needed and no more. Another method is based on dollar volume of sales, which works on a percentage of sales with different sliding factors.
Yet another method, which Gill’s company makes available in addition to its regular packages, is the ASP model (application service provider), sometimes known as subscription. This is a completely Web-based solution, where the server, application(s) and user data reside at a third-party site. This subscription-based system is the least expensive to use, but hasn’t caught on. Microsoft has tried this with Office with very limited success. Most users want their data on site because they know it’s secure, and should there be a connectivity problem, their data will still be accessible.
Whatever product you choose, it’s time to put away the clipboards, put digital outputs in the chart recorders and graduate from “MES” (Microsoft Excel Spreadsheets) to software systems that can improve your business.
For more information:
Claus Abildgren, Wonderware, claus.abildgren@wonderware.com, 949-727-3200
Rebecca Gill, Technology Group International, rgill@tgiltd.com, 800-837-0028
Rene Inzana, SYSPRO, rene.inzana@us.syspro.com, 714-437-1000
Terry McCorriston, CSB-System International, mccorriston@csb.com, 519-579-7272, ext. 203
Mark Sutcliffe, CDC Software, msutcliffe@cdcsoftware.com, 786-235-0682
Martin Michael, Advanced Automation, mmichael@advancedautomation.com, 610-458-8700, ext. 257
Rusty Steele, Schneider Electric, rusty.steele@us.schneider-electric.com, 317-306-5564
Maryanne Steidinger, Siemens, maryanne.steidinger@siemens.com, 215-646-7400, ext. 2210
Cevn Vibert, Silchester Control Systems Ltd., cvibert@silchester.co.uk, +44 (0) 1420 561902
Rob Wiersma, Lawson, rob.wiersma@lawson.com, 905-592-1473

The Ryvita control room includes several PC-based windows into its operation, including MES and ERP functionality. Tools include Schneider I/O system, Citect SCADA and Ampla (MES) software plus Microsoft Dynamics NAV (ERP) software. Source: Silchester Controls.
Building MES from Excel
UK-based Ryvita, located in Poole, Dorset, is part of the ABF Group and has been making crsipbread since 1925. It recently began a total quality management (TQM) and best practices program to improve system efficiencies, monitor downtime, track products and react dynamically to changes in the business. Silchester Control Systems (SI) was hired to revamp Ryvita’s mostly manual system into a competitive tool with the latest MES and ERP systems. Weeks were spent in scoping out the project, interviewing users/operators, capturing requirements and writing a user requirements specification.Since most of the equipment in use was Schneider, Silchester implemented a Schneider OPC server, Citect SCADA, Citect Ampla (MES), Microsoft SQL and Reporting Services. Ryvita operators originally entered data into a 40 MB Excel spreadsheet file, which contained thousands of separate calculations taken from hundreds of manual entries. All the data in the Excel file was recreated from SCADA data and manual entries within the SCADA system. Manual data entry used to take many hours per week; now entries are only a few short minutes per shift. The accuracy is unquestioned, and the repeatability is perfect. Trends are now based on actual machine data instead of personal interpretation.

Dashboards at Ryvita give operators key performance indicators at a quick glance and allow them make the appropriate actions based on the information they see. Source: Silchester Controls.
“This is a major step forward in terms of information accessibility for the site,” Mark Chesworth, supply chain director for Ryvita, reports. “It allows live data to be used by the teams in the factory to drive and improve business performance without time being wasted trying to collate vast quantities of information. It also enables the teams to assume real-time responsibility for driving their KPIs and to witness the results of their efforts. We believe this evolution will prove to be truly empowering for our production staff.”