Flooring Commandment: Know Thy Installer
Polymer science presents food and beverage manufacturers with many floor covering options, but performance often hinges on the expertise of the people installing them.
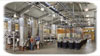
Blues/folk singer Maria Muldaur warbled, “It ain’t the meat, it’s the motion.” The sentiment can be applied to industrial flooring, with seamless toppings serving as meat and the installation crew providing the motion.
Epoxy, resin and urethane-based floor toppings are a growing trend in food and beverage plants, with polymer flooring suppliers launching forays into segments previously considered off limits. A recent trade show for dairy processors attracted a handful of seamless flooring formulators hoping to lure dairies away from tile and acid-resistant brick, at least in nonprocessing areas.
Food companies’ focus on improved sanitation as a fundamental element of food safety has resulted in second and third looks at polymer flooring. Previous experiences soured many manufacturers on these materials, which straddle the science of paint technology and the mason’s craft. “If you don’t have a power trowel, you are a painter, not a flooring installer,” says one cement contractor. The best option is the installer with expertise in both disciplines. That scenario increases the likelihood of material recommendations based on the best solution, not the topping the installer happens to sell.
Proper preparation and application of synthetic materials are vital and must be preceded by careful assessment of the conditions of use. Unfortunately, those steps are not always followed, resulting in premature failure.
“The evaluation step is crucial,” insists Ron Puszynski, president of Chicago area installer Concare Inc. Once a compound is selected, Puszynski advocates securing a letter of certification from the material manufacturer. “If you get the manufacturer involved that way, you can validate the appropriateness of the selection,” he points out.
Unqualified and careless installers have tarnished the image of seamless floor compounds, complains Steven Hess, president of Indianapolis-based Surface Solutions Inc. “You can have the best product in the bucket, but if you don’t put it down right, you’ve got nothing,” says Hess, who winces at the installers’ image of “fat guys with sanders on their belts” who either don’t know or don’t follow proper procedures. For example, some coatings require installers to broadcast 1.5 lbs. of sand per square foot to enhance a coating’s ability to withstand thermal cycles. “Some people don’t want to sweep that much sand off at the end of the day,” he says, and they use less than the specified amount. The difference is invisible to the naked eye, at least until pinholes and other faults appear later.
Industrial clients shoulder some of the blame. As the variety and complexity of flooring options have expanded, food companies and others sometimes fail to establish proper specifications. If all stakeholders in the project are not involved in the inspection and evaluation phases, the likelihood of an unfavorable outcome increases.
Some suppliers tackle installation by training and deploying their own installers. “You’re only as good as the guys who install the floor,” reasons Keith Kwasny, founder and president of Farmington Hills, MI-based Sanicrete. He is gradually adding installation crews, requiring new workers to spend a year as a laborer before serving a one- to two- year apprenticeship.
Some suppliers are instituting more stringent certification programs, often augmented with material-specific training by the formulator. BASF Corp., which pioneered cementitious urethane toppings under its Ucrete brand, established a master contractor program in the early 1970s, when Ucrete first entered the market, according to Ashley Davidson, product marketing manager in the firm’s US headquarters in Cleveland. The program has been beefed up in recent years, says Davidson, and contractors must be certified in order to purchase the company’s floor coatings.

For food and beverage, some installers opt for cementitious urethane, a blend of urethane and cement, over epoxy coatings. The material’s ability to withstand thermal shock as the plant cycles through hot water washdown and refrigerated operating conditions, as well as its abrasion and impact resistance, make it the material of choice in the harshest environment. On the other hand, processing areas for shelf-stable and further-processed foods usually don’t require high-pressure washdown, in which case epoxy may be appropriate. “There are different microbiological requirements for a meat plant than a bakery than a dairy,” points out Paul Brawley, operations manager at Cornerstone Flooring, Indianapolis. Food safety considerations dictate a floor’s performance requirements, and epoxy coatings often provide a cleanable and serviceable alternative. In warehouses and employee welfare areas, polyurethane can be costly overkill.
Time spent coating a substrate and waiting for it to cure is time lost to production. Formulators have responded to manufacturers’ desire to return an area to production as quickly as possible with fast-curing finishes, including a thin film that cures instantly with ultraviolet light (see related story on page 64). Surface Solutions’ Hess says some clients are unwilling to wait the two days necessary to apply and seal a topping like Ucrete HP and opt instead for Ucrete HF, a heavy-duty coating that also allows a one-day turnaround. “It’s more functional than aesthetic,” he says of HF, and the manufacturer’s thermal specs are broader than HP’s.
For extreme cold, methylmethacrylate (MMA) is the resin of choice, according to BASF’s Davidson. MMA sets up in less than two hours at temperatures as low as -20°F, though VOCs are an issue. BASF produces MMA and epoxy coatings, but cementitious urethane accounts for 80 percent of the company’s industrial flooring applications, Davidson estimates. The material boasts a coefficient of thermal expansion (CTE) that closely mimics that of concrete.
Coefficient of friction (COF) is another barometer of flooring performance. Though it sounds counterintuitive, John Crowley of Garon Products Inc. says gloss and semi-gloss urethane cements developed by his firm deliver greater COF than the typical matte finish. Another Garon innovation is an epoxy with nanoparticles of less than 0.1 micron that is more resistant to abrasions and increases strength without compromising clarity, according to Crowley, vice president of the Wall, NJ firm.
“Mold won’t feed on the plastic” in seamless floor coating, allows Pat Scudder, president of Protective Industrial Polymers (PIP) in Berea, OH, “but what about a divot or fracture where microbes find a food source?” His firm is introducing a concrete pretreatment with an antimicrobial additive that has been demonstrated to be effective in inhibiting mold and bacteria growth in the substrate. The additive also can be included in the flooring’s top coat to create an antimicrobial system, he says.
PIP developed an epoxy primer to address vapor intrusion from a cement substrate, replacing air in the cement with a colloidal gel. Chemists started experimenting with various antimicrobial additives, gradually increasing the ratio of additive to epoxy until tests could confirm the gel’s effectiveness. The CTE rate increases, which means the concrete doesn’t expand or contract as much as it normally would, helping to extend the floor’s life. While that functional benefit seems compelling by itself, the antimicrobial additive is attracting the most interest, Scudder says.
Describing it as “a belt and suspenders preventative solution,” Concare’s Puszynski says his firm has recommended the material to end users because of its ability to penetrate six inches or more into the substrate, thereby stabilizing the infrastructure.
Additives and pretreatments that improve a floor’s performance have merit, but many within the flooring business itself are skeptical about antimicrobial elements. “To me, this is still a marketing gimmick,” says Klaus Huenermann, technical director for Silikal America, a Carrollton, GA division of a German manufacturer of methacrylate resins that Huenermann describes as “enhanced MMA.” “It’s way beyond epoxy in terms of durability and gripability,” he adds.
Gripability is particularly important on ladders and platforms, two common applications for the plasma stream deposition of metal alloy particles done by Detroit-based SlipNOT Metal Safety Flooring. The difference between “the peaks and valleys” of those particles determines the COF of the slip-resistant coating, says Christina Molnar-Metrose, vice president of business development. For food plants, a Grade 1 coating is recommended for bakeries and other sites where ease of cleaning also is desired, while Grade 2 is appropriate for a packing house where grease and water make a high COF a priority.
Absent a COF standard, comparisons of the traction of different floor coverings are difficult, notes Molnar-Metrose. The type of footwear worn in the plant further complicates the issue, she adds. That said, SlipNOT usually defers to the OSHA 88 standard for quantifying COF. Most of its food application coatings rate 0.85 or greater. No end user has ever disclosed the impact of better traction on slips and falls, but some report productivity improvements when workers are more sure-footed, says Molnar-Metrose.
Installation isn’t an issue for Slipnot, which fabricates plates or coats drain covers and other components in its facility and then ships them to the food company or its equipment fabricator. For many other flooring suppliers, ensuring the integrity of the installation work is an ongoing struggle. “We are selling a capital investment that should last more than five or 10 years, so we don’t sell materials to anyone else,” says Brawley of Cornerstone, which maintains its own installation teams. The oversight is particularly important in food plants, where proper clothing and food safety protocols must be observed. Painters typically bring xylene and other chemical solvents to job sites, but xylene is strictly prohibited in food manufacturing facilities. Ensuring work teams adhere to those restrictions and requirements is almost as important as following the proper installation steps, he says.
Grout in tiles and brick is a breeding ground for bacteria, and many food manufacturers are replacing those durable floor coverings with seamless coatings. Suppliers have differing opinions of whether a seamless topping can be poured over existing brick, or if the old flooring must be removed. But there’s no disagreement on the importance of qualified and conscientious installers. Regardless of the performance requirements or the material type, the service life of a new floor is contingent on the workers who paint or trowel the material.
Installers of industrial flooring are tapping a growing business for cautionary warnings and position markings that are part of a floor’s top coat. “Corporate safety departments drive a lot of it,” acknowledges Ron Puszynski, president of Concare Inc., Melrose Park, IL, but interest in waste elimination is playing an expanding role. As an adjunct to kaisen events and other continuous improvement efforts targeting processes and procedures, lean practitioners are taking a hard look at how housekeeping adds to or reduces waste. The 5S technique lends itself to reevaluation of floor organization.
A manufacturing best practice from Japan, 5S is awkwardly translated into English as sort, set in order, shine, standardize and sustain. Masking tape can suffice for entry-level directionals, but many firms are taking the concept well beyond. “They’ll mark where a sanitation cart goes, where the pallet goes,” says Puszynski. “The objective is creating an automated process for the people in the plant.”
Permanent markings might not be an option if it means taking an area out of production. However, advances in material science are removing that obstacle. For example, a thin-film coating from the Netherlands cures instantly with the help of a machine resembling a lawnmower that brings UV light close enough to the film to be effective. The coating, developed by Royal DSM N.V., emits near-zero levels of volatile organic compounds.
“Thin film isn’t for everything,” Puszynski cautions, “but it can be helpful to lean teams seeking improved factory flow and worker safety.”
1227 Valley Rd., P.O. Box 38
Mertztown, PA 19539
800-523-8269
www.atlasmin.com
BASF Construction Chemicals-Building Systems
889 Valley Park Dr.
Shakopee, MN 55379
952-496-6000
www.buildingsystems.basf.com
Blome International Inc.
1450 Hoff Industrial Dr.
O’Fallon, MO 63366
636-379-9119
www.blome.com
ChemMasters
300 Edwards St., Madison, OH 44057
800-486-7866
www.chemmasters.net
Concare
2081 North 15th Avenue
Melrose Park, Illinois 60160
708-681-8800; 866-CONCARE
www.concare.com
Cornerstone Flooring
750 Patrick Place, Brownsburg, IN 46112
800-659-7699
www.cornerstoneflooring.com
Corro-Shield International Inc.
7059 Barry St., Rosemont, IL 60018
847-298-7770
www.corroshield.com
Crossfield Products Corp.
3000 E. Harcourt St.
Rancho Dominguez, CA 90221
310-886-9100
www.crossfieldproducts.com
Dur-A-Flex, Inc.
95 Goodwin St.
East Hartford, CT 06108
860-528-9838
www.dur-a-flex.com
Fortified Systems Inc.
126 Eisenhower Ln. N.
Lombard, IL 60148
630-916-0438
www.fortifiedsystems.com
Garon Products Inc.
P.O. Box 1924, Wall, NJ 07719
732-223-2500
www.garonproducts.com
High Performance Systems
22 Hillcrest Blvd.
Warren, NJ 07059
800-928-7220
www.highperfsystems.com
Protective Industrial Polymers
140 Sheldon Road, Berea, OH 44017
440-243-4560
www.protectiveindustrialpolymers.com
Kagetec Industrial Flooring Systems
309 Elm Ave. SW, Montgomery, MN 56069
612-435-7642
www.kagetecusa.com
SaniCrete
24535 Hallwood Court
Farmington Hills, MI 48335
248-893-1000
www.sanicrete.com
Sherwin-Williams Protective
& Marine Coatings
101 Prospect Ave.
Cleveland, OH 44115
800-524-5979
www.sherwin-williams.com
Sika Industrial Flooring
Division of Sika Corp.
201 Polito Ave., Lyndhurst, NJ 07071
800-637-7793
www.sikafloorusa.com
Silikal
609-B Fertilla Street, Carrollton, GA 30117
888-830-1404
www.silikalamerica.com
SlipNOT Metal Safety Flooring
2545 Beaufait St., Detroit, MI 48207
800-754-7668
www.slipnot.com
Stonhard Inc.
One Park Ave., Maple Shade, NJ 08052
800-257-7953
www.stonhard.com
Surface Solutions Inc.
5689 W. 73rd St.
Indianapolis, IN 46278
866-858-4080; 317-388-8000
www.surfacesolutionsusa.com
Tennant Company
701 N. Lilac
Minneapolis, MN 55440
763-540-1200
www.tennantco.com
Tnemec Co. Inc.
P.O. Box 165770, Kansas City, MO 64116
800-Tnemec-1, 816-326-4254
www.tnemec.com
For a complete of flooring suppliers, see Food Master or visit.
www.foodmaster.com
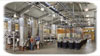
Sanitation routines and other factors dictate the type of flooring used in food and beverage plants, though increasingly the choice is seamless coatings. Source: Cornerstone Flooring.

An installer spreads sand while his coworkers continue to spread a cementitious urethane compound on top of a concrete floor. If insufficient sand is deposited, long-term failure is likely. Source: Surface Solutions Inc.
Epoxy, resin and urethane-based floor toppings are a growing trend in food and beverage plants, with polymer flooring suppliers launching forays into segments previously considered off limits. A recent trade show for dairy processors attracted a handful of seamless flooring formulators hoping to lure dairies away from tile and acid-resistant brick, at least in nonprocessing areas.
Food companies’ focus on improved sanitation as a fundamental element of food safety has resulted in second and third looks at polymer flooring. Previous experiences soured many manufacturers on these materials, which straddle the science of paint technology and the mason’s craft. “If you don’t have a power trowel, you are a painter, not a flooring installer,” says one cement contractor. The best option is the installer with expertise in both disciplines. That scenario increases the likelihood of material recommendations based on the best solution, not the topping the installer happens to sell.
Proper preparation and application of synthetic materials are vital and must be preceded by careful assessment of the conditions of use. Unfortunately, those steps are not always followed, resulting in premature failure.

Concrete is the preferred substrate for seamless coatings, though other flooring can be coated. A deteriorated acid brick floor (above) was coated with cementitious urethane (below) to produce a more sanitary appearance. Source: Sherwin-Williams.
Unqualified and careless installers have tarnished the image of seamless floor compounds, complains Steven Hess, president of Indianapolis-based Surface Solutions Inc. “You can have the best product in the bucket, but if you don’t put it down right, you’ve got nothing,” says Hess, who winces at the installers’ image of “fat guys with sanders on their belts” who either don’t know or don’t follow proper procedures. For example, some coatings require installers to broadcast 1.5 lbs. of sand per square foot to enhance a coating’s ability to withstand thermal cycles. “Some people don’t want to sweep that much sand off at the end of the day,” he says, and they use less than the specified amount. The difference is invisible to the naked eye, at least until pinholes and other faults appear later.

Some suppliers tackle installation by training and deploying their own installers. “You’re only as good as the guys who install the floor,” reasons Keith Kwasny, founder and president of Farmington Hills, MI-based Sanicrete. He is gradually adding installation crews, requiring new workers to spend a year as a laborer before serving a one- to two- year apprenticeship.
Some suppliers are instituting more stringent certification programs, often augmented with material-specific training by the formulator. BASF Corp., which pioneered cementitious urethane toppings under its Ucrete brand, established a master contractor program in the early 1970s, when Ucrete first entered the market, according to Ashley Davidson, product marketing manager in the firm’s US headquarters in Cleveland. The program has been beefed up in recent years, says Davidson, and contractors must be certified in order to purchase the company’s floor coatings.

Projects that take a line out of production cause manufacturers to cringe and make the decision to install fast-curing floors easier. Source: SaniCrete.
Best-fit materials
If Know Thy Installer is the first commandment of industrial flooring, Know Thy Application surely is the second. Performance expectations and operating conditions dictate material selection, and the number of options is increasing.For food and beverage, some installers opt for cementitious urethane, a blend of urethane and cement, over epoxy coatings. The material’s ability to withstand thermal shock as the plant cycles through hot water washdown and refrigerated operating conditions, as well as its abrasion and impact resistance, make it the material of choice in the harshest environment. On the other hand, processing areas for shelf-stable and further-processed foods usually don’t require high-pressure washdown, in which case epoxy may be appropriate. “There are different microbiological requirements for a meat plant than a bakery than a dairy,” points out Paul Brawley, operations manager at Cornerstone Flooring, Indianapolis. Food safety considerations dictate a floor’s performance requirements, and epoxy coatings often provide a cleanable and serviceable alternative. In warehouses and employee welfare areas, polyurethane can be costly overkill.
Time spent coating a substrate and waiting for it to cure is time lost to production. Formulators have responded to manufacturers’ desire to return an area to production as quickly as possible with fast-curing finishes, including a thin film that cures instantly with ultraviolet light (see related story on page 64). Surface Solutions’ Hess says some clients are unwilling to wait the two days necessary to apply and seal a topping like Ucrete HP and opt instead for Ucrete HF, a heavy-duty coating that also allows a one-day turnaround. “It’s more functional than aesthetic,” he says of HF, and the manufacturer’s thermal specs are broader than HP’s.
For extreme cold, methylmethacrylate (MMA) is the resin of choice, according to BASF’s Davidson. MMA sets up in less than two hours at temperatures as low as -20°F, though VOCs are an issue. BASF produces MMA and epoxy coatings, but cementitious urethane accounts for 80 percent of the company’s industrial flooring applications, Davidson estimates. The material boasts a coefficient of thermal expansion (CTE) that closely mimics that of concrete.
Coefficient of friction (COF) is another barometer of flooring performance. Though it sounds counterintuitive, John Crowley of Garon Products Inc. says gloss and semi-gloss urethane cements developed by his firm deliver greater COF than the typical matte finish. Another Garon innovation is an epoxy with nanoparticles of less than 0.1 micron that is more resistant to abrasions and increases strength without compromising clarity, according to Crowley, vice president of the Wall, NJ firm.
Fortified food defense
For years, food companies have greeted antimicrobial additives for floor coatings with a collective shrug, but suppliers and installers say food safety considerations are making manufacturers more receptive to the idea. BASF is making an antimicrobial based on silver ion-technology available, backed by research on its efficacy. “Anybody can add an antimicrobial and say it is going to be effective,” says Davidson. “Food companies want to go a step beyond, but first they want to understand what it means in terms of effectiveness.”“Mold won’t feed on the plastic” in seamless floor coating, allows Pat Scudder, president of Protective Industrial Polymers (PIP) in Berea, OH, “but what about a divot or fracture where microbes find a food source?” His firm is introducing a concrete pretreatment with an antimicrobial additive that has been demonstrated to be effective in inhibiting mold and bacteria growth in the substrate. The additive also can be included in the flooring’s top coat to create an antimicrobial system, he says.
PIP developed an epoxy primer to address vapor intrusion from a cement substrate, replacing air in the cement with a colloidal gel. Chemists started experimenting with various antimicrobial additives, gradually increasing the ratio of additive to epoxy until tests could confirm the gel’s effectiveness. The CTE rate increases, which means the concrete doesn’t expand or contract as much as it normally would, helping to extend the floor’s life. While that functional benefit seems compelling by itself, the antimicrobial additive is attracting the most interest, Scudder says.
Describing it as “a belt and suspenders preventative solution,” Concare’s Puszynski says his firm has recommended the material to end users because of its ability to penetrate six inches or more into the substrate, thereby stabilizing the infrastructure.
Additives and pretreatments that improve a floor’s performance have merit, but many within the flooring business itself are skeptical about antimicrobial elements. “To me, this is still a marketing gimmick,” says Klaus Huenermann, technical director for Silikal America, a Carrollton, GA division of a German manufacturer of methacrylate resins that Huenermann describes as “enhanced MMA.” “It’s way beyond epoxy in terms of durability and gripability,” he adds.
Gripability is particularly important on ladders and platforms, two common applications for the plasma stream deposition of metal alloy particles done by Detroit-based SlipNOT Metal Safety Flooring. The difference between “the peaks and valleys” of those particles determines the COF of the slip-resistant coating, says Christina Molnar-Metrose, vice president of business development. For food plants, a Grade 1 coating is recommended for bakeries and other sites where ease of cleaning also is desired, while Grade 2 is appropriate for a packing house where grease and water make a high COF a priority.
Absent a COF standard, comparisons of the traction of different floor coverings are difficult, notes Molnar-Metrose. The type of footwear worn in the plant further complicates the issue, she adds. That said, SlipNOT usually defers to the OSHA 88 standard for quantifying COF. Most of its food application coatings rate 0.85 or greater. No end user has ever disclosed the impact of better traction on slips and falls, but some report productivity improvements when workers are more sure-footed, says Molnar-Metrose.
Installation isn’t an issue for Slipnot, which fabricates plates or coats drain covers and other components in its facility and then ships them to the food company or its equipment fabricator. For many other flooring suppliers, ensuring the integrity of the installation work is an ongoing struggle. “We are selling a capital investment that should last more than five or 10 years, so we don’t sell materials to anyone else,” says Brawley of Cornerstone, which maintains its own installation teams. The oversight is particularly important in food plants, where proper clothing and food safety protocols must be observed. Painters typically bring xylene and other chemical solvents to job sites, but xylene is strictly prohibited in food manufacturing facilities. Ensuring work teams adhere to those restrictions and requirements is almost as important as following the proper installation steps, he says.
Grout in tiles and brick is a breeding ground for bacteria, and many food manufacturers are replacing those durable floor coverings with seamless coatings. Suppliers have differing opinions of whether a seamless topping can be poured over existing brick, or if the old flooring must be removed. But there’s no disagreement on the importance of qualified and conscientious installers. Regardless of the performance requirements or the material type, the service life of a new floor is contingent on the workers who paint or trowel the material.
The marks of good housekeeping
Lean manufacturing initiatives are notable for their bottom-up assessment of plant practices-quite literally, in the case of flooring, when 5S teams order the placement of pallet outlines and directional information on the factory floor.Installers of industrial flooring are tapping a growing business for cautionary warnings and position markings that are part of a floor’s top coat. “Corporate safety departments drive a lot of it,” acknowledges Ron Puszynski, president of Concare Inc., Melrose Park, IL, but interest in waste elimination is playing an expanding role. As an adjunct to kaisen events and other continuous improvement efforts targeting processes and procedures, lean practitioners are taking a hard look at how housekeeping adds to or reduces waste. The 5S technique lends itself to reevaluation of floor organization.
A manufacturing best practice from Japan, 5S is awkwardly translated into English as sort, set in order, shine, standardize and sustain. Masking tape can suffice for entry-level directionals, but many firms are taking the concept well beyond. “They’ll mark where a sanitation cart goes, where the pallet goes,” says Puszynski. “The objective is creating an automated process for the people in the plant.”
Permanent markings might not be an option if it means taking an area out of production. However, advances in material science are removing that obstacle. For example, a thin-film coating from the Netherlands cures instantly with the help of a machine resembling a lawnmower that brings UV light close enough to the film to be effective. The coating, developed by Royal DSM N.V., emits near-zero levels of volatile organic compounds.
“Thin film isn’t for everything,” Puszynski cautions, “but it can be helpful to lean teams seeking improved factory flow and worker safety.”
Food & Beverage Industry Flooring Suppliers
Atlas Mineral and Chemicals Inc.1227 Valley Rd., P.O. Box 38
Mertztown, PA 19539
800-523-8269
www.atlasmin.com
BASF Construction Chemicals-Building Systems
889 Valley Park Dr.
Shakopee, MN 55379
952-496-6000
www.buildingsystems.basf.com
Blome International Inc.
1450 Hoff Industrial Dr.
O’Fallon, MO 63366
636-379-9119
www.blome.com
ChemMasters
300 Edwards St., Madison, OH 44057
800-486-7866
www.chemmasters.net
Concare
2081 North 15th Avenue
Melrose Park, Illinois 60160
708-681-8800; 866-CONCARE
www.concare.com
Cornerstone Flooring
750 Patrick Place, Brownsburg, IN 46112
800-659-7699
www.cornerstoneflooring.com
Corro-Shield International Inc.
7059 Barry St., Rosemont, IL 60018
847-298-7770
www.corroshield.com
Crossfield Products Corp.
3000 E. Harcourt St.
Rancho Dominguez, CA 90221
310-886-9100
www.crossfieldproducts.com
Dur-A-Flex, Inc.
95 Goodwin St.
East Hartford, CT 06108
860-528-9838
www.dur-a-flex.com
Fortified Systems Inc.
126 Eisenhower Ln. N.
Lombard, IL 60148
630-916-0438
www.fortifiedsystems.com
Garon Products Inc.
P.O. Box 1924, Wall, NJ 07719
732-223-2500
www.garonproducts.com
High Performance Systems
22 Hillcrest Blvd.
Warren, NJ 07059
800-928-7220
www.highperfsystems.com
Protective Industrial Polymers
140 Sheldon Road, Berea, OH 44017
440-243-4560
www.protectiveindustrialpolymers.com
Kagetec Industrial Flooring Systems
309 Elm Ave. SW, Montgomery, MN 56069
612-435-7642
www.kagetecusa.com
SaniCrete
24535 Hallwood Court
Farmington Hills, MI 48335
248-893-1000
www.sanicrete.com
Sherwin-Williams Protective
& Marine Coatings
101 Prospect Ave.
Cleveland, OH 44115
800-524-5979
www.sherwin-williams.com
Sika Industrial Flooring
Division of Sika Corp.
201 Polito Ave., Lyndhurst, NJ 07071
800-637-7793
www.sikafloorusa.com
Silikal
609-B Fertilla Street, Carrollton, GA 30117
888-830-1404
www.silikalamerica.com
SlipNOT Metal Safety Flooring
2545 Beaufait St., Detroit, MI 48207
800-754-7668
www.slipnot.com
Stonhard Inc.
One Park Ave., Maple Shade, NJ 08052
800-257-7953
www.stonhard.com
Surface Solutions Inc.
5689 W. 73rd St.
Indianapolis, IN 46278
866-858-4080; 317-388-8000
www.surfacesolutionsusa.com
Tennant Company
701 N. Lilac
Minneapolis, MN 55440
763-540-1200
www.tennantco.com
Tnemec Co. Inc.
P.O. Box 165770, Kansas City, MO 64116
800-Tnemec-1, 816-326-4254
www.tnemec.com
For a complete of flooring suppliers, see Food Master or visit.
www.foodmaster.com
Looking for a reprint of this article?
From high-res PDFs to custom plaques, order your copy today!