Understanding the Increased Demand for Industrial Switches in Food and Beverage Plants

Photo by Joshua Sortino on Unsplash
Industry 4.0 has made considerable inroads into America with more than 36,500 food and beverage processors. Machine-to-machine (M2M) communication, big data and machine learning are rapidly being adopted to increase profitability in an industry long characterized by its low margins. Industry 4.0 is improving efficiencies up and down the enterprise, from the enabling of predictive maintenance programs and supply chain monitoring, to the generating of traceability data for government compliance. Data collected from smart sensors on the plant floor is being analyzed for purposes as diverse as taste consistency, logistics management, predicting product shelf-life, packaging accuracy and employee safety.
While the food and beverage (F&B) industry has lagged behind automakers and energy producers in embracing Industry 4.0, no other industry category could benefit more from it. New digital technologies are now helping the F&B industry respond with agility to changing consumer demands and emerging opportunities. Network technologies are also keeping the industry compliant with stringent government regulations for food safety, traceability, nutrition and sustainability. In addition, it allows companies to gain a competitive advantage by leveraging operational intelligence in decision making that increases productivity and lowers operating costs.
One of the concerns that held the F&B industry back from fully embracing Industry 4.0 is the perceived fragility of industrial networking devices. Here’s why: The food and beverage markets have strict hygiene requirements for machinery, systems and components, including equipment like plant-level sensors, industrial switches, actuators and other networking devices. Outlined in the FDA’s “Preventive Controls for Human Food” rule, these hygiene requirements ensure that “reasonable measures and precautions” are taken to minimize the risk of food contamination. Notwithstanding the fact that network devices rarely have direct contact with food, they are, all the same, subjected to FDA rules which puts them in the crosshairs of high-pressure water spray during sanitary wash downs, along with subjecting them to harsh cleaning agents, vapor, corrosion and humidity. It’s not difficult to see why plant owners might have second thoughts about introducing sensitive network devices into this less-than-ideal environment.
As a result, the obligation has fallen on network component manufacturers to harden their technologies. This is especially true for mission-critical industrial Ethernet switches that act as network backbones. While a malfunctioning Ethernet switch in a commercial setting represents a serious problem, in a food and beverage plant it can lead to catastrophic losses in production, government-mandated recalls, regulatory fines and damage to a brand’s reputation.
F&B processors have another unique problem. Raw products used in manufacturing usually have a relatively short shelf life since most are organic in nature. When a process line experiences extended downtime due to a malfunctioning or failed switch, raw product must be discarded in an environmentally responsible manner. This can entail solid waste disposal fees and fines, not to mention the considerable cost to replace the raw materials themselves, plus the time required to wash down the line before startup.
With the advent of Industry 4.0, Ethernet switches have moved from the safe confines of IT’s management and control level to the harsh realities of OT’s plant floor where performance is threatened daily by a host of environmental hazards. This article addresses what qualities to look for in an industrial Ethernet switch that can provide long-term reliability in an F&B plant.
Understanding Ethernet Switches
Before we discuss the value of an industrial Ethernet switch in an F&B plant, first let’s talk about what an Ethernet switch actually does.
An Ethernet switch serves as an intermediary. It receives units of data or “frames'' at one of its ports, reads the frame’s MAC address, determines the destination and forwards the data to a targeted port in a process measured in nanoseconds. Data can be received and sent in both directions simultaneously at bit rates of 100 Mbit/s (“Fast Ethernet”), 1 Gbit/s (“Gigabit Ethernet”), and increasingly, 10 Gbit/s (“10 Gigabit Ethernet'').
Ethernet switches are either managed or unmanaged. The choice of installing one or the other largely depends on the plant owner’s performance needs. In general, basic line topology networks will use unmanaged switches that permit connected devices to communicate with each other, but little else. Unmanaged switches are neither visible nor addressable in the IP network. As plug-and-play devices, their chief advantage is that they provide quick, inexpensive installation requiring no configuration and trouble-free device replacement. Unmanaged switches are useful in smaller networks for adding additional ports where data control, diagnostics and other intelligent management functions are performed by another device. For example, an unmanaged switch may handle a subsystem for measuring a specific ingredient on the process line, but not the complex management of an IP video surveillance system transmitting high-definition images in real-time of the plant floor.
As its name implies, a managed switch is an intelligent administrative device. Using managed switches permits remote management, configuration, monitoring and the troubleshooting of network problems via a web browser GUI or SSH/Telnet/serial CLI. Each managed switch has its own IP address, so it is visible as a member of the network. Shared networks in a plant are also made possible by managed switches.
Complex and redundant ring topology networks will require features found only in a managed switch. Managed switches allow for redundant topologies in ring structures to protect against the loss of connections without a communication breakdown. In other words, a managed switch must be installed to build a network with genuinely uninterrupted data communication. A managed switch provides route changing when a failure occurs in the regular route. The time required to find and use new routes in the network, sometimes referred to as switchover or recovery time, is a key parameter of switch performance. Because of the critical nature of a redundant network in processing, the managed switch you select should support the Ethernet Ring Protection Switch protocol that achieves <50ms recovery time to the network.
Here are a few questions to ask as to whether to purchase a managed or unmanaged Ethernet switch.
- Is your network isolated and made up of a limited number of devices? If so, an unmanaged switch should be sufficient.
- Does the network infrastructure feature multiple systems and a variety of devices, creating complex connectivity requirements? In this case, only a managed switch will suffice.
- Do data streams have to be separated? Again, only a managed switch can provide this capability.
- How important is security? Chances are it’s mission critical. Managed switches are the obvious choice to help mitigate potential risks to devices and networks.
- Do you need to future proof the current network? A high-port count managed switch with an equally high PoE budget will make it much easier to add devices and subsystems going forward.
Standard vs. Industrial Switches
A commercial-grade, off-the-shelf Ethernet switch will not withstand industrial use, even if contained within a cabinet. Commercial-grade switches are designed for installation in a home or business and lack protection against elevated levels of EMC, shock, vibration and moisture, among other environmental threats. They are rated within a very narrow temperature range, and use a single AC power supply.
Conversely, industrial Ethernet switches are purpose-engineered for demanding environments, whether in a food and beverage plant, an oil refinery or an automotive manufacturer. They are built with high-grade components, much better than commercial grades in terms of heat dissipation, electromagnetic compatibility and service life. Instead of AC power, they increase reliability with an external redundant DC power supply. Resistant to shock, EMC, moisture, gases, chemicals, corrosion and dust, an industrial Ethernet switch can be installed in almost any harsh environment in temperatures as low as -40°C or as high as 70°C. Ruggedized metal enclosures are a must, as are tight, waterproof connectors that will not disconnect due to heavy equipment vibration.
One of these types of waterproof connectors is called an M12, the M standing for “metric” and the 12 referring to the length of the diameter across the outside of the threads, in other words 12mm. Because they are circular in shape, they possess high current capabilities and can obtain ingress protection (IP) ratings easier than standard rectangular connectors since they are better at keeping out the dirt, sand and water that can cause corrosion and other problems. All this makes an Ethernet switch with M12 connectors ideal for food and beverage processing plants subject to high levels of moisture. Also, M12 connectors come in a variety of pin positions that vary depending on the signal type and number of signals, connection couplings and code. Most gigabit M12 Ethernet connectors are “X-Coded” for error-free, high-speed data transfers. A metal cross (X-shaped) in the connector safely separates the four data pairs.
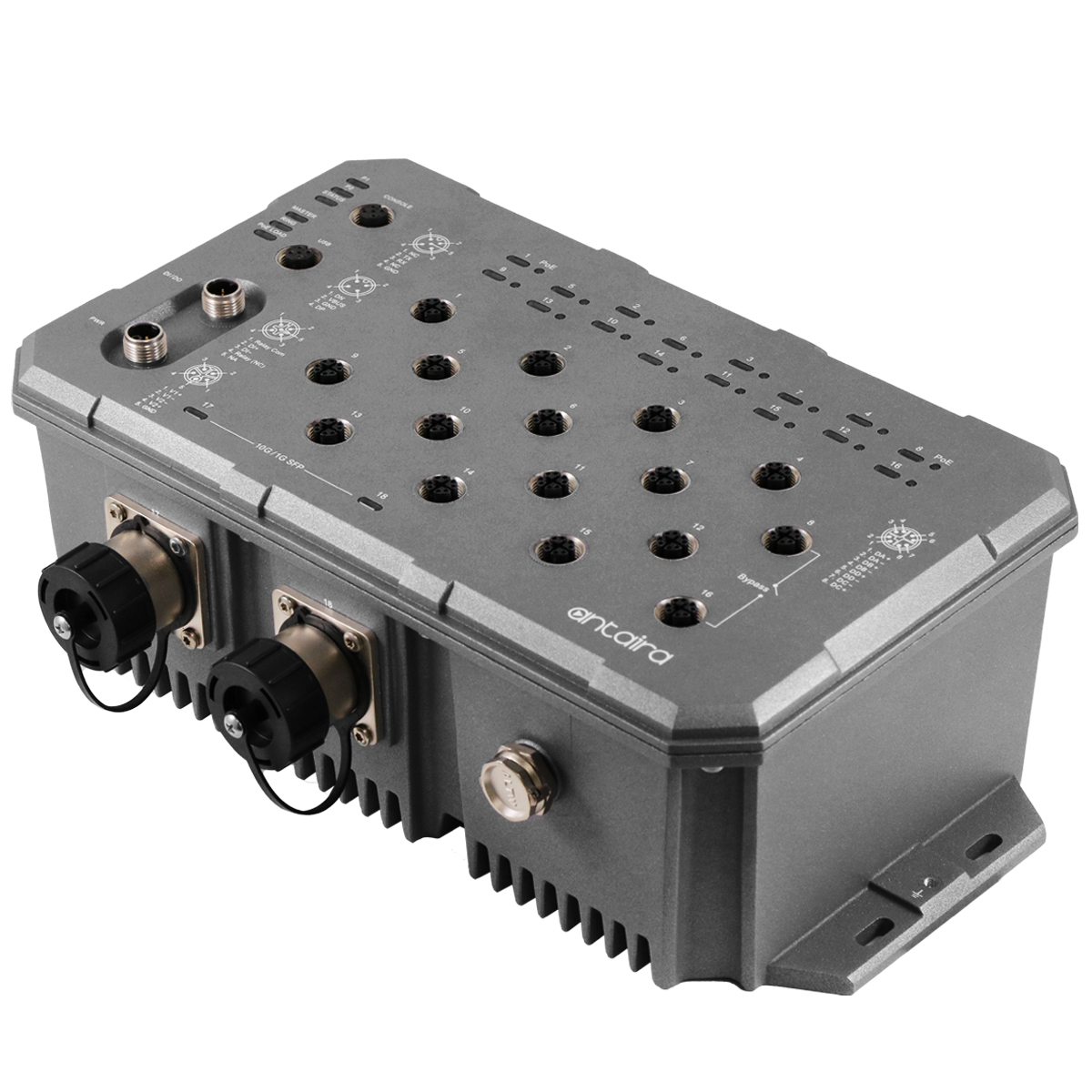
No Cabinet Required
Harsh industrial environments typically call for DIN-rail mounting Ethernet switches inside a remote cabinet or the main control cabinet. This approach requires running long, bulky cables for connected devices. Besides increasing cost and complexity, running cables throughout a plant may create a trip and fall hazard. A ruggedized, metal IP67 (waterproof) housing combined with M12 connectors allows Ethernet switches to be wall or machine-mounted outside the control cabinet, reducing the long cable runs and eliminating the need to buy larger cabinets. Metal housings will also withstand dings from tools and equipment in an F&B processing environment plus maintain the highest standards in safety and hygiene. Smoothed edges on a switch housing can prevent bacteria growing or water from pooling.
Other Considerations
Network switches are often overlooked but vitally important pieces of the networking puzzle. Selecting the right network switch for your food or beverage processing plant is dependent on your network’s size, complexity, traffic and number of connections. Below are additional features in an industrial switch that can help support a switch in its role within a network infrastructure, although the list is far from exhaustive:
High Power over Ethernet (PoE) Budget
PoE combines data and power over a single Ethernet cable, thus reducing the complexity of the installation and the costs of long-term maintenance. Managed switches deliver power to IEEE 802.3at/af compliant powered devices (PDs) with 30W per port and a total PoE budget of 240W. PoE M12 managed Ethernet switches help you streamline your communication infrastructure by reducing the amount of additional equipment, wires and outlets needed. For power saving purposes, many M12 managed switches also support PoE scheduling and PoE limit function to set up PoE output duration and Watt-at-Will. When specifying a switch, select one that allows you to individually set available power for each port to the exact requirements of the individual connected device, therefore optimizing the switch’s PoE budget.
Multiple Gigabit Ethernet ports
Ethernet switches with multiple 1G uplinks are a must when installing or upgrading networks—the more ports, the better to ensure future-proofing. Additional Gigabit ports enable easier expansion and provide needed flexibility.
Light Layer 3
A light layer 3 (LL3) managed switch is an affordable alternative to a full layer 3 switch and an upgrade to a layer 2 switch. It can make decisions based on IP addressing and static policies similar to the layer 3 switch. The difference is that a light layer 3 switch does not support routing protocols, only static routing. A light layer 3 switch allows VLAN creation, VLAN routing and IP routing based on static routes.
Cybersecurity Protection
Cyberattacks on the food industry have been proliferating, with at least five major food companies being hit with ransomware attacks since 2017. A light layer 3 switch monitors and controls the network so that active threats can be shutdown. Many Ethernet switches offer comprehensive network security by supporting multi-user accounts, ACLs, RADIUS, TACACS+, SSH, HTTPS/SSL, IP Source Guard, 802.1x and more.
Quality of Service (QoS)
Many managed switches support QoS for classifying traffic types marked by the network into different service classes. In doing so, they reduce congestion on the network by dropping or throttling low-priority traffic during periods of peak use. Traffic routing reduces or eliminates congestion in critical sectors of the network. In addition, managed switches can be enabled as VLANs to isolate devices that are sensitive to higher traffic levels, reducing incidents of collisions and decreasing resources wasted by acting as LAN segments. Having an Ethernet switch with both QoS and VLAN will help future-proof a communications network.
Ingress Protection (IP) 67 Rating
IP67 is a rating signifying that an enclosure protects the device inside from the harmful effects of water and dust. IP67-rated industrial switches offer dust-tight protection against solid ingress from food particles or waste. Combined with water resistance from hose sprays, it’s easy to see why integrators specify IP67-rated M12 managed switches for their food and beverage processing networks.
Sourcing the right industrial Ethernet switch is a key part of making sure your industrial networks are reliable, safe and cost-effective.
Looking for a reprint of this article?
From high-res PDFs to custom plaques, order your copy today!