Industry 4.0’s impact on the food and beverage industry
Tetra Pak discusses why food and beverage manufacturers should be seriously looking at adopting new technology in their plants.
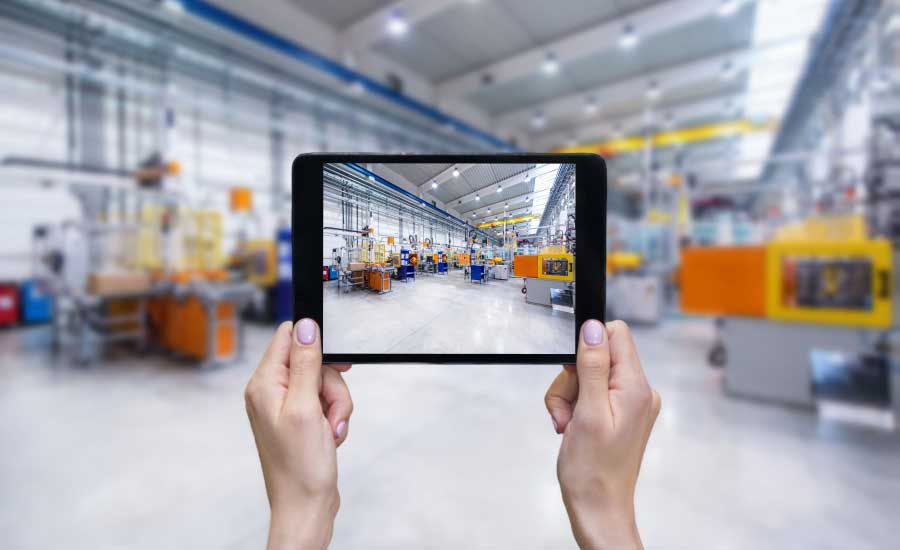
The speed of change is rapidly increasing, and food and beverage manufacturers are trying to keep up with the challenges driven by shifting consumer attitudes, retailers’ demanding more, tighter regulations and more pressure from business owners.
To address these concerns, Tetra Pak recently hosted a webinar on Industry 4.0 and explained why it sees a tremendous opportunity Industry 4.0 poses to the food and beverage industry, including increased vigilance over food safety, improved productivity, improved quality assurance and a greater ability to manage complex global supply chains.
To learn more about Tetra Pak’s vision about Industry 4.0, best practices and what it means for the future, FE talked to IIka Dunder, digitalization director for Tetra Pak Service.
FE: The increasing challenges F&B producers are facing are largely consumer and retail driven. Can you discuss what these are and how Industry 4.0 can help?
Dunder: F&B producers are facing an ever-increasing demand for high quality products, traceability and on a large scale, at a consumer-friendly price. Embracing Industry 4.0 can lead to increased productivity, reduced costs and deliver increased profitability for businesses. To the workforce it also provides the opportunity for continued progression and upskilling, creating new jobs for employees.
Industry 4.0 will support manufacturing productivity and flexibility of a plant. The solutions will vary depending on plant and equipment installed. Here are a few examples of areas:
- Optimizing inbound and outbound logistics to the factory
- Reduce cost through real time production control across the entire plant
- Improved productivity through optimization of specific processes by empowering employees through. Visualization of data and KPIs, making key information easily accessible to all key employees
- Automation of Warehousing.
Industry 4.0 allows businesses to optimize the four levels of their operations by giving greater oversight of the whole process, ensuring greater traceability and performance monitoring, and allowing more intelligent decision making. It allows for better oversight of:
- Things: Individual parts of individual pieces of equipment such as sensors collecting data which allows businesses to monitor how a particular part is performing;
- Equipment: Where a company monitors and controls the performance of a whole machine or line of machines;
- Manufacturing Operations Management: Where a business connects and monitors the performance of the whole factory.
- Business Systems: Where a company monitors the planning and performance of the whole enterprise, or of multiple factories within its business. For example, looking at how sales are related to what is being produced on the shop floor, ensuring the company is producing the right goods in the timeliest fashion.
FE: Some people might say, “The concepts of Industry 4.0 and connecting the whole plant has been discussed for years, how is this different?” What would be your response?
Dunder: It’s true that embracing digital technology has been done across a lot of industries, but if we look at the F&B category alone, the entire sector is behind. At Tetra Pak we feel that it is important that food and beverage businesses start thinking about the opportunities, and what they can do and how they can partner with others. It’s the customer need that is driving this now. Three years ago, this was not on the table for any company but the thoughts around it and the results people want has escalated quickly. We have been in constant dialogue with our partners and feel we are now is a position to help them.
FE: What capabilities might be unlocked by using Industry 4.0 technology? What are some specific areas of the plant that these solutions can help?
Dunder: It’s important to remember that every business has a different journey and starting point. A variety of solutions are available depending on the size and the need of the customer. We are working with our customers and technology partners to find solutions that suit them. Some of the thing that we’re working on include: Automated restocking of material, Automated quality control, Augmented reality remote support, Predictive maintenance.
One way we’ve seen industry 4.0 is impacting those on the factory floor is removing the need for Tetra Pak employees to travel and several days of downtime for our customer. Our customers are using increasingly complicated equipment in order to ensure consistent food safety and quality. This means that machine issues have become significantly more complex for the engineer to manage.
Previously, if there is a machine issue that requires specialist knowledge, the onsite engineers would have to connect with specialists via phone or email and in many cases would have to travel long distances to resolve issues, which can cost time and money.
We are now using Microsoft's mixed reality technology, HoloLens, which enables manufacturers to connect the onsite engineer to the Tetra Pak specialist who can see the machine in real time. This removes the need for travel for us and several days of downtime for the customer.
FE: With all these potential benefits, why has F&B been typically late in adopting new technology?
Dunder: Organizations considering upgrading their technology have to contend with both the costs of implementing technology and training the staff to use it correctly. This can be intimidating. However, F&B companies are catching on as it becomes increasingly clear that digital tools like Internet of Things and advanced data analytics are central to helping us navigate new challenges. These include increasingly complex supply chains and faster changing consumer demands.
FE: Why is this moment in time specifically important for F&B to invest in Industry 4.0?
Dunder: The pressure to be more efficient and to stay ahead of rivals makes investing in Industry 4.0 a necessity. This isn’t a “one-off” moment to some bright new future. Investing in digital technologies is a step-by-step journey that will allow businesses to continuously learn about and improve their own production processes.
FE: Where might be a good place for an F&B plant to start employing Industry 4.0? Or in other words, what solution is an easy one to first implement in the F&B plant?
Dunder: There are several places to start the journey. One good place to start to start is to make existing data and KPI transparent and available to all relevant end users (from the operators on the shop floor to the management). The key is to make the visualization and basic analysis easy. E.g. easily customizable dashboard customer dashboards etc. There are several ready-made tools on the market that can help to get going quickly. Another quick win is to contact the OEM for your equipment in the factory and ask what they have available in form of services and products.
FE: Anything else you’d like to mention?
Dunder: At Tetra Pak, we are committed to helping the Food and Beverage sector on its journey towards Industry 4.0. That’s why we’ve released this white paper; to demystify these new technologies. It is designed to help food manufacturers gain an understanding of the full opportunities available, and the sorts of investments they might need to make if they are to seize them. It also looks at what ‘best practice’ looks like, and how businesses can decipher some of the more technical aspects of the concepts involved
Looking for a reprint of this article?
From high-res PDFs to custom plaques, order your copy today!