Process Control
Your window to the process: Clear view or obstructed?
Today’s process control software is tasked to keep machine interfaces easy to configure for both engineers and operators

ICONICS KPIWorX provides a powerful self-service visualization and analysis tool for any food or beverage process. Photo courtesy of ICONICS
Chances are, you’ve probably been using the same HMI, MES or SCADA program for some time in your operation, and you’ve been through several version upgrades too. Providers of these products work hard to make their software backward compatible with equipment and operating systems as well as create new features users want.
The challenge is making the window to control systems and their data transparent, and supplying information the operator needs without providing excess buttons and alarms. In addition, users are looking for systems that work on plant terminals, tablets and phones, and have a consistent interface while connecting to devices. And, the software has to be easy to configure and program for engineers.
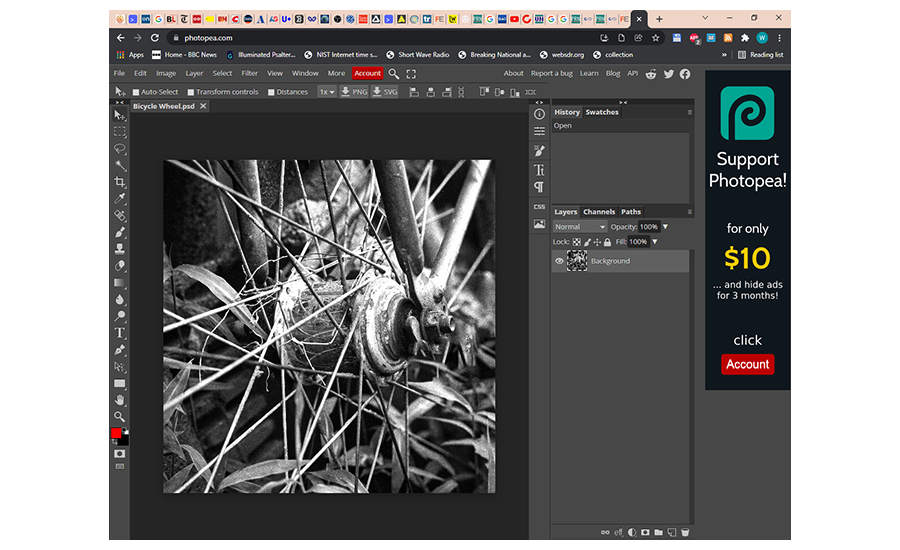
Improving usability for control system builders and end users
HMI/SCADA software has to be easy for both programmers and end users like plant operators. One approach ADISRA has taken with its SmartView HMI/SCADA software is to provide control system builders and programmers with the ability to make changes on a live application during runtime, says Leandro Coeli, EVP of consulting services at ADISRA. This includes creating, configuring, deleting and changing tags, triggers, scheduler, alarms, drivers, database and history.
Templates are essential. Coeli says that a HMI/SCADA template can be built for a machine/process/line. This template can then be added to the application at runtime, and easily customized using pre-set user interfaces and drag-and-drop logic that have been predefined initially in the development environment.
At the user end, the system’s run-time visual capability with its intuitive graphical interface and preconfigured approach provides an easy setup for multiple machines or lines. Platforms are more malleable, providing agility to customize applications and deploy quickly in operations, says Coeli.
Adaptive run-time customization capabilities allow a plant floor end-user with little or no programming ability to modify their HMI/SCADA application at runtime to meet their specific needs, such as creating dashboards and screen layouts, adding or changing PLCs, configuring or changing alarms, trends, and recipes, adds Coelli.
Rich Carpenter, GM of product management for Emerson’s machine automation software business, says Emerson has consolidated application software into two main tool chains. One for the machine control applications based on IEC61131, and one for automation software applications associated with connectivity, local HMI, full plant production monitoring and supervisory control.
“For the automation software, this substantially reduces the learning curve for end users who often have needed one tool for local HMI, another for data collection and distribution, and yet another for HMI/SCADA applications,” says Carpenter. “We have also delivered a ‘Wizard Development’ capability we use internally to simplify the task of deploying plant analytic applications. The wizard asks a few required questions and then auto-generates the configuration. All of these help reduce the burden on integrators/developers of the plant software application.”
Emerson eliminated the need for writing scripts to implement basic functionality like setpoints or screen changes. OPC UA serves as the core communications protocol for PLCs/PACs, connectivity, local HMI, supervisory control and plant analytic applications. With this common data backbone, it’s easy to develop an application once and apply it to equipment—even from different vendors.
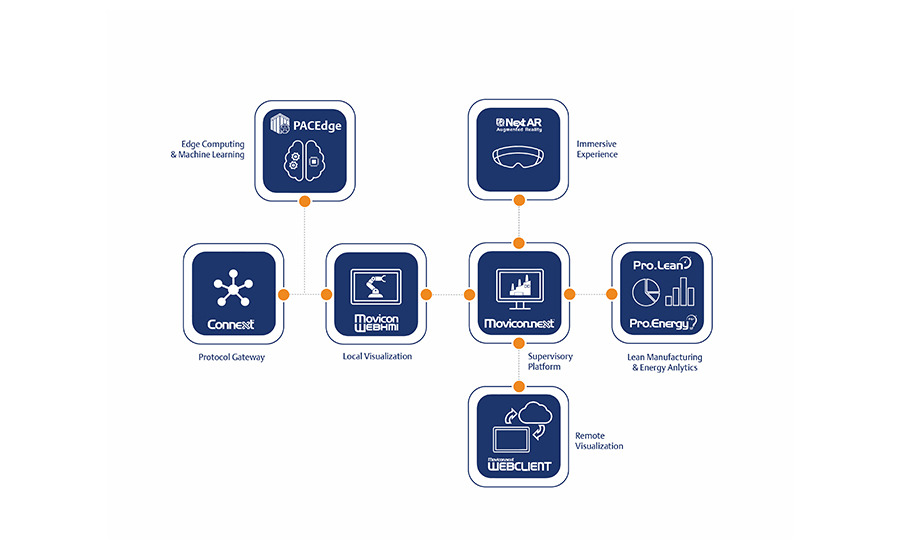
For operators and other end users of the system, having one common set of rules for interfacing with equipment—whether at the supervisory, machine control or IIoT application—simplifies the end user training and ease of use. By incorporating voice and gesture control, non-traditional ways to interact with the system are also possible, adds Carpenter.
Similar to Carpenter’s description, configuration of most projects can often be looked at as being “visualization” or “server-side” functions, two distinct but interrelated parts of the design process, says Jotham Kildea, ICONICS/solution sales engineering supervisor. On the server side, ICONICS uses a Workbench environment with a variety of auto-configuration and bulk deployment tools to expedite development. Templating is key here, as ICONICS makes use of an asset-centric model to organize all relevant aspects of the equipment such as data connectivity, data historizing, alarming, and analytics.
“On the visualization side, reusability and scalability of designs have been the keys to success within our platform in delivering interfaces that are quick to deploy and future-proof,” adds Kildea. “Here we really have the integrator’s needs in mind, as the configuration has tools that facilitate users to reuse standard symbols and core controls such that these not only are easy to get up and running, but also are adaptable to continue to be compatible with the solution as the project evolves and changes over time.”
Better connections make life easier
Connectivity is vital to plant floor digitization, and involves more than just connecting systems and devices such as PLCs, controllers and sensors. It is also important to achieve seamless interconnection between application programs such as databases, other HMI/SCADA, a manufacturing execution system (MES) and an enterprise resource planning (ERP) system, says Coeli.
If there’s one important aspect of connectivity, OPC UA and OPC DA are key protocols to link together PLCs, controllers, sensors, and other devices such as robots, bar code readers and conveyors—and all three of our interviewees talked about the merits of OPC UA.
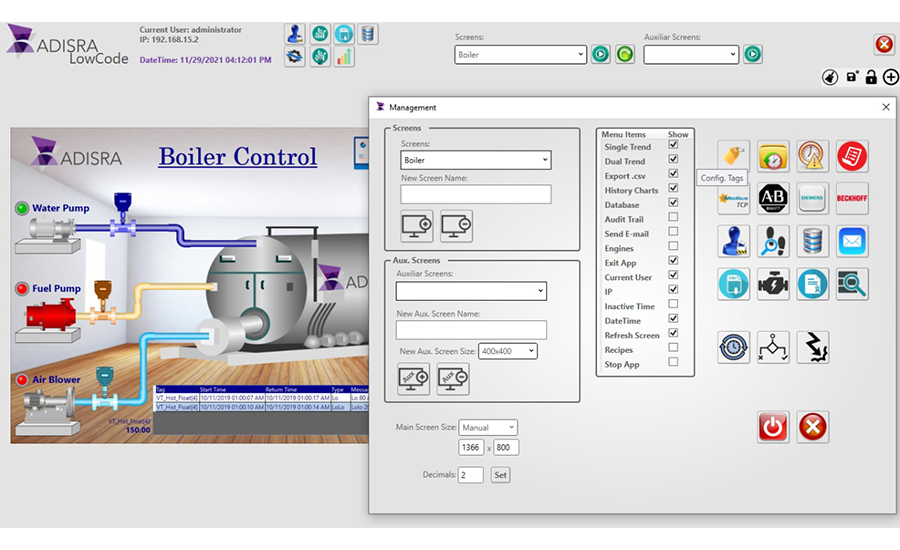
“We strive to use common protocols that have a longstanding history throughout controls networks globally, such as OPC UA, Modbus and CC-Link, as well as widely accepted protocols more commonly seen on the corporate network such as MQTT, AMQP (advanced message queuing protocol), REST (representational state transfer) and others,” says ICONICS’ Kildea. This approach provides a versatile set of options for connecting to process data as well as a strong foundation on which to integrate with other applications and further analyze this data.
Data gateway functions in the Movicon products are carefully constructed to support all aspects of connectivity, says Emerson’s Carpenter. Data may come in over traditional protocols like Modbus but then is cleansed and converted to OPC UA, so in turn it can then be published via OPC UA, MQTT, or any other device protocol. The data can also be routed to a database through SQL or logged directly to the cloud via SQL Azure.
Connectivity also involves breaking down “data silos,” which are collections of data held in various systems, but not easily or fully accessible by other systems, says Coeli. It is important for the HMI/SCADA package to have built-in data connectivity. Look for HMIs that connect to any SQL database (Microsoft SQL Server, MySQL, Sybase, Oracle) or Microsoft Access as well as to MES and ERP systems.
Other connectivity options include simple network management protocol (SNMP) and MQTT. A HMI like SmartView uses SNMP to share information with different devices on the network. SNMP allows users to integrate their industrial devices with a network management system or a service management system. MQTT is a protocol to allow HMI applications to integrate with cloud computing, big data storage or cloud-based analytic tools.
From desktop to web interface
ICONICS was founded in 1986—pretty much when character-based graphics (non-GUI) was available in DOS or IBM’s OS/2, and Windows NT a few years later. Screens of 640x480 pixels were the norm, and 1024x768 was yet in the near future.
Kildea has seen a dramatic shift over the past several years such that 90% of the solutions ICONICS delivers today rely on web-based GUIs. “This shift has come about for many reasons, but some of the leading ones are that the ‘thin client’ nature of web deployments means no installation or software dependencies on the client station, as well as the speed and ease with which companies can push out updates and adjustments to their applications,” he says. With a unified development environment, users can program traditional GUIs or web-based interfaces with no special knowledge required.
“From a technology and deployment standpoint, web-based GUIs are preferred due to the low footprint and zero-deploy capability of HTML5/SVG in a browser,” says Carpenter. Emerson fully supports this approach through the integrated development environment (IDE) in Movicon. “However, there are limitations in HTML5/SVG that may prohibit a richer experience for operators where the business logic needs to be implemented on the client side. For this reason, we simultaneously support a rich client experience using WPF/XAML within the same IDE.”
Like many suppliers today, the Emerson core philosophy is to build the application once and be able to deploy it on any pane of glass, be it a browser, mobile device, or operator console. With this philosophy, Emerson has pushed the limits of what is capable with HTML5/SVG by eliminating as much as possible the need for client-side scripting—yet enabled the full capability in the rich clients, according to Carpenter.
Knowing the user’s application, process, preferences and environment will be important factors in making a decision: Web or GUI? “Traditional GUI is important for processes requiring setup or close monitoring where someone really must be physically present near the machine,” says ADSIRA’s Coeli. For example, safety critical controls require closer monitoring.
The obvious disadvantage to traditional GUI is that a user must be physically present by the machine. So, if an emergency happens on another machine down the line or in another building, it may not be accessible via the GUI local to an operator. Therefore, more staffing is required to maintain the line or plant. But, with a web-based GUI, an operator can be in touch with a distant machine. Web-based GUIs also allow users to monitor equipment that might not have a traditional GUI attached, e.g., a wind turbine or a wastewater pump. Of course, the obvious disadvantage, says Coeli, is loss of internet—and potential security issues.
Looking for a reprint of this article?
From high-res PDFs to custom plaques, order your copy today!