Sorting Operations
Today's sorting and grading solutions help apple packhouses meet operational challenges

Apples of every size, shape and color need to be sorted once they have been picked and cleaned. Today's automated sorting systems can make quick and accurate work of this job. All photos courtesy TOMRA Food

The Tomra UltraView inspection module integrates with Spectrim to take ‘seeing’ power to the next level.


Although apples are one of the world’s most widely-consumed fruits, their popularity doesn’t make it any easier for businesses growing, sorting and packing them. If anything, the standards required in apple production are getting tougher.
Because apples are in plentiful supply all year round, consumers are reluctant to purchase any that are sub-standard. This puts retailers and packhouses under pressure to deliver consistent product quality all the time. So, too, do food safety regulations, especially in export markets. Now more than ever before, apples require accurate and consistent sorting and grading.
As the global supply of apples generally keeps pace with demand—some 86 million metric tons are grown every year—profit margins can be tight. This increases the pressure on packhouses to improve operational efficiencies and minimize cost-per-kilogram. And as consumers and retailers increasingly expect the food industry to adopt sustainable business practices, there is further pressure to improve packing efficiencies in order to reduce food waste.
Packhouse challenges
All this is complicated by the fact that growers are striving to achieve bigger yields and better packout by introducing new varieties. This means packers will be required to acquire knowledge about the new fruit, its possible internal and external imperfections, and how to grade it accurately.
These challenges mean that packhouses must strike a balance between quality and quantity. While product quality has to meet customers’ requirements, over-delivering on quality is no smarter than over-delivering on quantity. The right products must be packed in the right box every time.
At the same time as striving to achieve this balance, many packhouses face another challenge: those who have traditionally relied on manual labor to handle grading and packing are now finding it difficult to recruit and retain people. Labor shortages, immigration constraints, and changing demographics are all having an effect. What’s more, many packers need to reduce their dependence on labor—or deploy workers to other tasks in the plant which add greater value—for their businesses to be financially sustainable.
There is, however, much to look forward to—and not only in the future, but starting right now. The huge value of the global apple market—approximately $79 billion per year—can profitably sustain the many thousands of growers and packers able to stay competitive. And staying competitive is made much easier by adopting today’s state-of-the-art sorting and grading technologies, which solve the challenges faced by packhouses today.
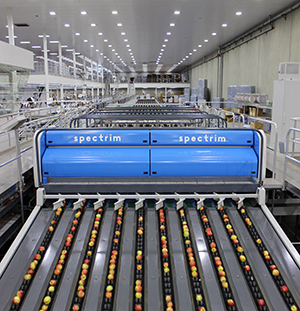
Inspecting, sorting, grading and protecting
TOMRA’s solutions for apple packhouse operations include the Model 5S Advanced sorting and sizing platform, Spectrim sorter and grader, UltraView inspection module and Inspectra2 apple grading system.
The TOMRA 5S Advanced sorter, which first became available in 2021, builds on the performance of Compac’s Multi Lane Sorter (Compac was acquired by TOMRA in 2016), but was redesigned from the ground up. This sorting platform is designed for hygienic operation, with toolless cleaning and sanitization—and 100% stainless steel and food-safe polymer contact areas. The machine’s specialized software connects to the TOMRA Insight data platform.
The TOMRA 5S Advanced’s software features provide for optimization and efficiency across the line and include programs for element mixing, exact packout optimization, and throughput control, as well as a Dynamic Lane Balancer system. These features improve productivity, quality and efficiency—and can be controlled easily via the sorter’s intuitive graphic user-interface.
Connectivity to the cloud-based TOMRA Insight subscription service can make sorting machines the digital heart of packhouse operations, meeting the industry’s evolving needs over the next 10 years or more. TOMRA Insight enables better flow of information up and down the supply chain, and opens a pathway to traceability from bin to pack. It also empowers packhouses to improve efficiencies by making better, data-driven decisions.
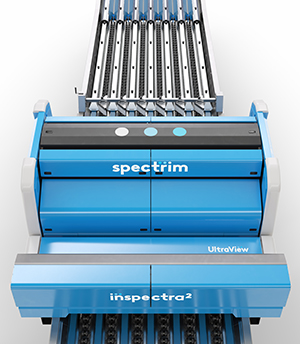
Inspectra2 is a non-invasive solution for internal defect grading. This platform’s near-infrared spectrometer can detect brix, core rot, internal browning, water core, firmness, hue and bleeding. These detection capabilities keep bad apples out of a good box and reduce fruit giveaway.
Utilizing all these capabilities, packhouses can greatly reduce or eliminate some of their toughest daily operational challenges, optimize efficiency and provide customers with precisely the product quality they’ve asked for. And by having the ability to separate out the bad apples from the good, packhouses find intrinsically more worth. In a world where the market value of many brands depends mostly on intangible assets including brand equity, packhouses also protect their customers’ brand reputations.
Looking for a reprint of this article?
From high-res PDFs to custom plaques, order your copy today!