Plant Operations & Engineering
Weather to the Extreme: Can You Survive it?
Prepare in advance for hurricanes, tornadoes, flooding and severe electrical storms to keep your operation up and running with minimal downtime.

New Orleans flood during Hurricane Katrina. Unfortunately, New Orleans is one big basin—mostly below sea level—so while a fun place to visit, is it a good place for a food manufacturing plant? Photo courtesy of David Mark from Pixabay
In the last few years, it seems that hurricanes, tornadoes and resultant flooding have become stronger and stronger. Maybe chalk it up to a warming planet, which amplifies the power of these storms. “Five-hundred-year storms,” have become 100-year storms—or sometimes they seem more like annual catastrophes, especially in, “tornado alley.” As if that weren’t enough, severe electrical storms could just as easily shut you down if you’re not adequately protected.
In 2018, a tornado struck the Marshalltown, Iowa area, causing damage to the JBS pork processing facility. While most of the damage was in the distribution area (rail cars and truck trailers severely damaged), the processing area was apparently still operational. The plant, which processes about 20,000 hogs per day, had to be shut down until damages could be estimated and repairs made primarily to the distribution area. The storm damage meant that the animals to be processed would have to be rerouted temporarily to other facilities. Fortunately, no one at the plant was injured.
Severe thunderstorms and heavy rains came through southwestern Michigan on June 13, 2022, resulting in high winds, hail, power outages and flood damage throughout the area. These torrential storms produced significant rainfall in a short period of time—overwhelming the city’s stormwater system in Sturgis, and resulting in flooding in parts of the city, including areas of Abbott’s baby formula plant.
According to an Abbott statement, Abbott’s facility had reopened its Sturgis, Mich. plant on June 4, 2022, after a voluntary recall had closed the operation in February, but less than two weeks later had to shut down production due to severe thunderstorms causing flooding inside the facility.
As a result of the flood damage, Abbott stopped production of its EleCare specialty formula, which was underway at the time, to assess damage caused by the storm and clean and re-sanitize the plant. The company took time to clean up, and then with the help of a third-party auditor, ensured the plant was safe to resume production. According to an Abbott announcement dated August 26, 2022, the plant has reopened and restarted production of Similac.
“Don’t Build On the Flood Plain…”
Longstanding advice, but in some cases, what areas weren’t flood plains a few decades ago may now be—due to climate changes. In some cases, older food plants have necessarily been located near creeks and rivers (hopefully a safe distance away and above flood stage levels)—either as a source of water or for disposing of wastewater. But what can be done to prevent the ingress of water from these sources during excessive rain?
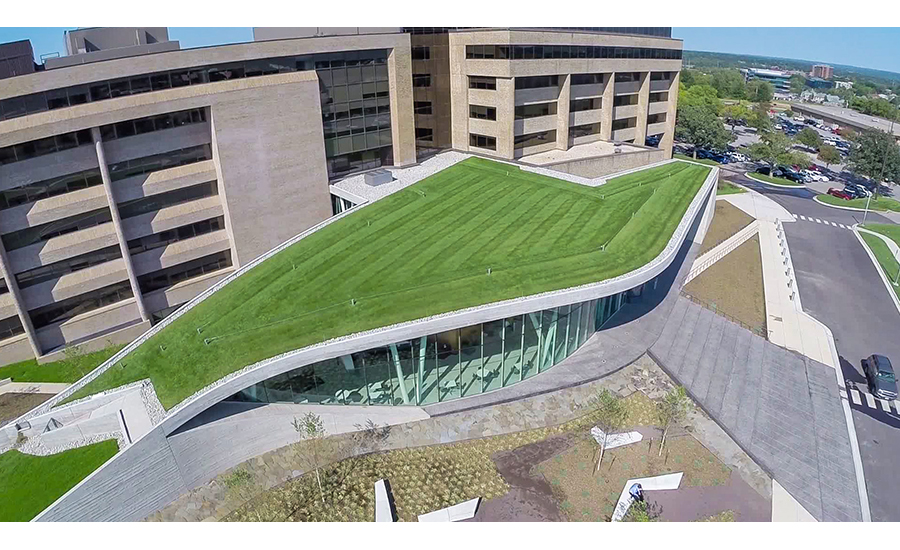
“The first line of defense is to keep all stormwater conveyance and storage systems well maintained,” says David Hird, PE, director of engineering services, Gray. “This can include removal of collected sediment from basins and pipes as well as keeping all storm inlets clear of grass clippings, leaves or other debris. It’s important that the system is inspected and maintained to the final point of discharge. Any disruption within the system can lead to water ingress in unwanted areas of the property.”
If continued localized flooding is experienced during a typical storm, a civil engineer should be engaged to analyze the effectiveness of the stormwater system, says Hird.
“Keeping flood water out of your building requires giving it somewhere else to go,” adds Ryan Townsend, Black & Veatch director of architecture. “If you have enough land, a detention pond is an excellent flood defense. A detention pond is normally a low space in your landscaping that becomes a pond during occasional periods of heavy rainfall. The water diverted to the detention pond stays away from your building, then slowly recharges the ground water table.”
On a smaller site, a green roof is an excellent way to reduce runoff that can cause flooding, says Townsend. Instead of diverting roof water through gutters and downspouts, a plant-filled green roof absorbs rainwater and releases it slowly back into the atmosphere as the plants grow. Due in part to its high insulation value, the EPA estimates that a green roof can lower the cost to air conditioning an average building by 10%-30%.
“At the very minimum—check your downspouts. They should be clear of debris and they should carry water at least 6 ft. away from your building before it goes to the ground,” adds Townsend.
FEMA Information May Help You Avoid Water Ingress after Serious Flooding
For existing buildings already located in a floodplain, the Federal Emergency Management Agency (FEMA) has published FEMA 551 (March 2007): “Selecting Appropriate Mitigation Measures for Flood-prone Structures,” says Steve Guyer, PE, manager, civil engineering, Hixson Architecture & Engineering. These mitigation measures include drainage improvements, barriers (floodwall/levee), wet flood-proofing, dry flood-proofing, elevation, relocation and acquisition. (Note that depending on site conditions, these may or may not apply.)
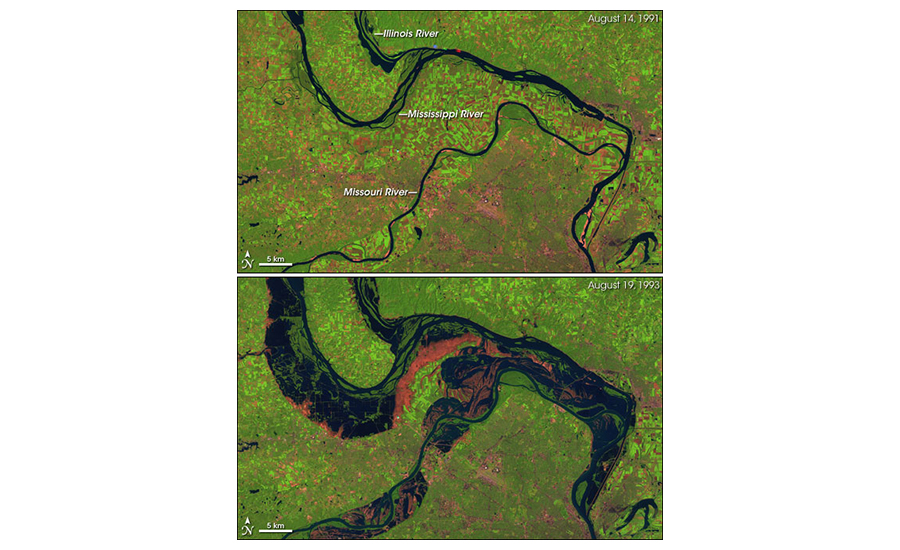
If you’re looking for a potential “new” site, FEMA has developed a National Tool (NT) software database application that catalogs floodprone structures and helps to determine potentially appropriate mitigation measures.
The ultimate goal of the NT is to provide a standardized, systematic approach to collecting and interpreting property data and mitigation project development. While the focus of the NT is on data collection for repetitive loss (RL) properties, it can also be used to gather information related to flood risk, building construction and building value for any structure.
Tornado Alley
A few years ago, I visited a greenfield food plant, and since it is located in tornado alley, the processor had also built protection for employees. But does it make more sense to build a separate and dedicated facility or construct an internal area that will survive these storms?
“Adding an underground tornado shelter to an existing slab-on-grade building is possible, but impractical,” says Black & Veatch’s Townsend. A more cost-effective solution would be to harden an interior room in the building. A reinforced concrete block room, if detailed correctly, will meet FEMA safe room guidelines. Plan for 5 sq. ft. of safe room for every building occupant (FEMA P-361, Section B5.2.1.1, document page 151). If the room doubles as storage or another function on an average day, make sure the empty spaces between boxes and equipment will accommodate everyone.
“Across most of the contiguous United States, current building code wind-load design is for a minimum 90 mph wind event,” says Kate Spille, PE, senior project engineer, Hixson Architecture & Engineering. “Wind design loads in coastal, hurricane-prone areas increase to 150 mph.”
“Factory Mutual requirements, which are common in the food and beverage industry, provide an added level of safety to building components such as wall panels, roofs and rooftop equipment by amplifying both the magnitude of code-prescribed wind loads and the required safety factor,” says Spille.
There are even industry standards (ICC-500 Standard for the Design and Construction of Storm Shelters and FEMA P-361 Safe Rooms for Tornadoes and Hurricanes) for tornado design, including a 250-mph design wind load (equivalent to an F4 tornado) in “tornado alley,” adds Spille.
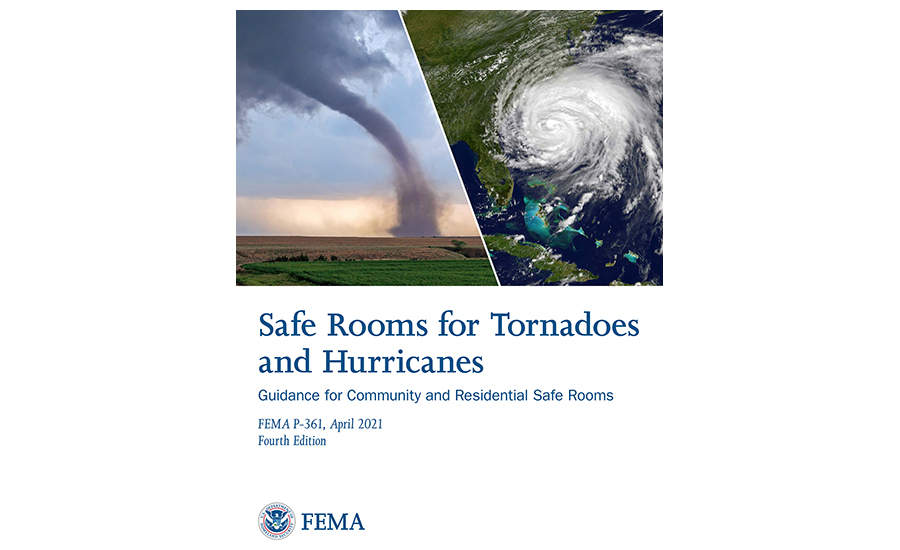
Increased safety against wind events comes at an added cost, says Spille. Retrofitting facilities to increase wind resistance is generally cost prohibitive, although the decreased insurance premiums offered by Factory Mutual can make retrofitting more attractive. Hixson has recently seen an uptick in clients interested in adding tornado shelters for workers, which can provide a satisfactory solution in both new facilities and retrofits to existing facilities. Commercial structures built to withstand tornado loading are generally underground and/or use concrete walls and roofs and have special wind-rated doors. They are often small, dedicated “storm shelters” within a larger facility, which is not designed for tornado-level loads.
“Cost implications of high wind design, lower insurance premiums and added worker safety are good discussions to have with your building consulting team and structural engineer during the early planning stages of a project,” says Spille.
Besides looking at ways to fix building structures, it’s a good idea to take stock of what you have and make sure it’s secured, according to Wesley Perkins, director, A&E Integration, food & beverage, Gray.
“While performing regular facility inspections, it is recommended for [manufacturers] to include assessments for events such as excessive wind, tornados and hurricanes. Loose materials or objects should be secured or stored in protected locations to prevent damage from projectiles. Rooftop equipment should be inspected to ensure panels, doors and other access points are operating, closing, and latching securely.”
Avoiding Fire in Fire-Prone Areas
Maybe your site isn’t located in an area where hurricanes or tornadoes are relatively common, but instead in a dry climate where offsite fires could potentially spread to your buildings. If your facility is surrounded by vegetation, it could be damaged by fire that starts outside the plant—think wildfire in California.
The key to preventing wildfires from becoming disasters is to keep them from entering and spreading into the built environment. Once they’re in the built environment, whether or not your facility catches fire will be dependent upon the measures taken to prevent a fire from igniting exterior walls, surfaces, windows and roofs.
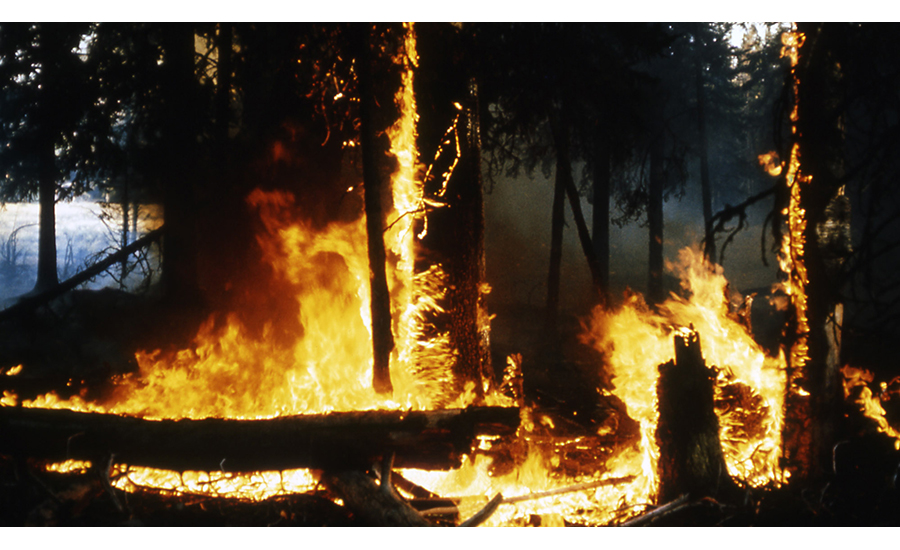
“To prevent a building from catching fire due to a nearby forest fire or structure fire, the best practice is to keep everything within four feet of the building nonflammable—concrete and gravel or other landscape rock are best,” says Black & Veatch’s Townsend. Trees and large shrubs should be at least thirty feet from the building; this gives firefighters enough room to work safely if a fire does occur. Avoid bark mulch, keep trees trimmed and clean up fast-burning dead leaves in the fall to reduce the amount of fuel available.
Perkins points out other flammable materials that should be kept away from structures, for example, fuel tanks, vehicles, “boneyard” materials and more. “New structures can be designed with fire-resistant materials such as precast concrete walls and Class A roof membranes,” adds Perkins.
“There are some limited tools that architects and structural engineers can use to keep the perimeter of a building wet as wildfire approaches, e.g., constructing with fire-resistant materials, installing fire protection sprinklers,” says Hixson’s Spille. However, most of the protection comes with good site planning and proper land/facility maintenance.
“Constructing walls and roofs with precast or cast-in-place concrete provides the best protection against heat/ignition from nearby fires. Reinforced masonry would be the next best protection for the walls. However, doors, windows and roofing systems are still vulnerable to damage from excessive heat. Fire shutters could be installed to help protect the windows. Smaller roofs would benefit from slate or tile roofing systems; but this is not practical for larger flat roofs,” says Townsend.
Electrical Storm Damage
In earlier practice as a wireless engineer, I saw firsthand the catastrophic lightning damage—twisted and exploded panels and cabinets, fried wiring and building damage—to industrial sites when breaker/contactor panels, conduits and the like are not adequately protected or grounded. And even when they are, lightning can do strange things—like, for example, completely vaporize a tower-mounted VHF antenna. However, proper grounding and cabling protected the transmitter in the equipment building below such that only an antenna switch was damaged. While the right lightning protection procedures won’t necessarily guarantee a perfectly good result with a major lightning hit, the right preparation can help with safety in several ways.
“In addition to the benefits related to lightning strikes, a properly bonded and grounded electrical system can increase electrical system reliability and safety,” says David Ziskind, PE, director, Black & Veatch NextGen Ag. Bonding the building steel is another good practice. While generally building lighting protection is not required on a national level, some states/AHJs (authorities having jurisdiction) require lightning protection systems, adds Ziskind.
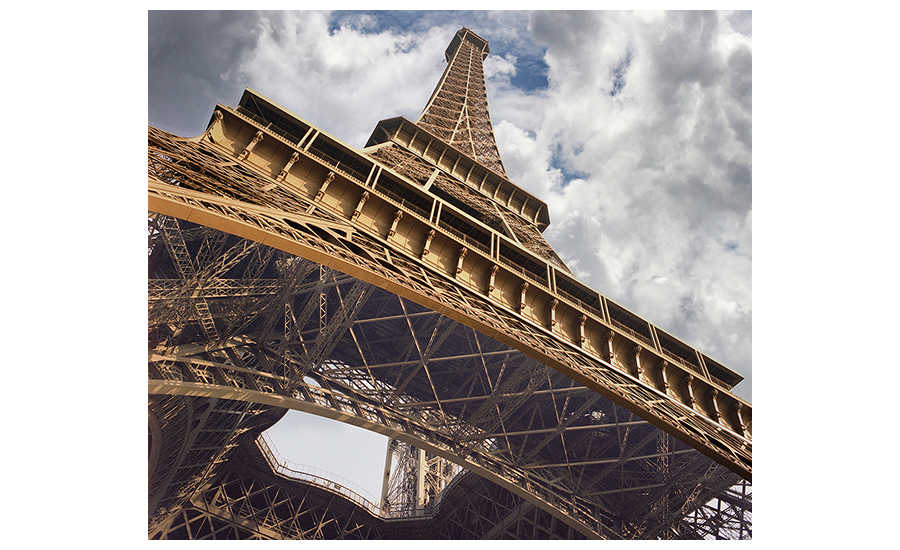
Certain food and beverage operations require proper grounding of equipment and vessels to minimize the possibility of a dust or vapor explosion caused by lightning or any number of other spark creators such as electrical or friction, impact, static electricity, etc. Aapplications needing this protection include, for example, grain or sugar milling, dryers and distillery operations. In fact, according to The Distilled Spirits Council of the U.S., lightning sparked 12 distillery fires from 1954 through 2003 with two of them resulting in explosions.
“There are best practices for lighting protection systems which should be followed. NFPA 780 and the Lightning Protection Institute Standard 175 are two go-tos, which address the design, installation and inspection of lighting protection systems,” says Ziskind. “A lightning risk assessment can help inform the need for a lighting protection system, taking into account personnel safety, risk of a lightning strike and potential damage in the event of a strike. A properly designed, installed, and regularly inspected and maintained lightning protection system can be a key part of a risk mitigation strategy against facility lightning strikes. For key equipment, surge protection may also provide additional equipment protection.”
Plan for Power Outages: Priorities and Risks
Any of the weather events we discussed can cause short- to long-term power outages. Lightning strikes may cause very short-term (milliseconds to seconds) power brown outs and localized blackouts. While short-term outages may not put a cooler or freezer out of commission, production line automation could take some time to get back on line and resynchronized, assuming no damage or memory loss has occurred. You need to determine your priorities and risks, and decide how to plan for these events.
“Priorities for emergency power are determined by what they will be used for: life safety systems, critically or legally required systems, equipment backup and optional standby,” says Michael Kelly, electrical engineering manager, Gray.
“Once these are established, an order of operations and load shedding plan can be built to make sure as many assets are as protected as possible,” adds Kelly. “The order of operations can be manual (requiring maintenance or human intervention) or automatic (requiring a high level of control systems and cost).”
“A power outage risk analysis can be done for all equipment and systems, looking at the probability/likelihood/frequency of the power loss occurrence, and the impact/severity if it occurs,” says Ziskind. Things to consider include equipment recovery time and loss of product, balanced against the cost of backup power (both the initial cost as well as ongoing inspection and maintenance).
The likely range of the length of time of an outage should also be considered to evaluate the best backup system. A recent history from the power utility can be helpful to understand power quality, frequency of outages and length of outages. Another consideration is whether a temporary power interruption can be tolerated (for example, several seconds to allow a diesel generator or other backup source to come online), or whether it needs to be truly uninterrupted (such as with an uninterrupted power source [battery]).
Therefore, is your protection goal against frequent micro-outages or to cover more severe, multi-day outages? An uninterrupted backup system could also provide some smoothing for micro-outages and other power quality issues. Regardless of the system, regular testing, inspection and maintenance are necessary to ensure these systems will respond as intended during an event, says Ziskind.
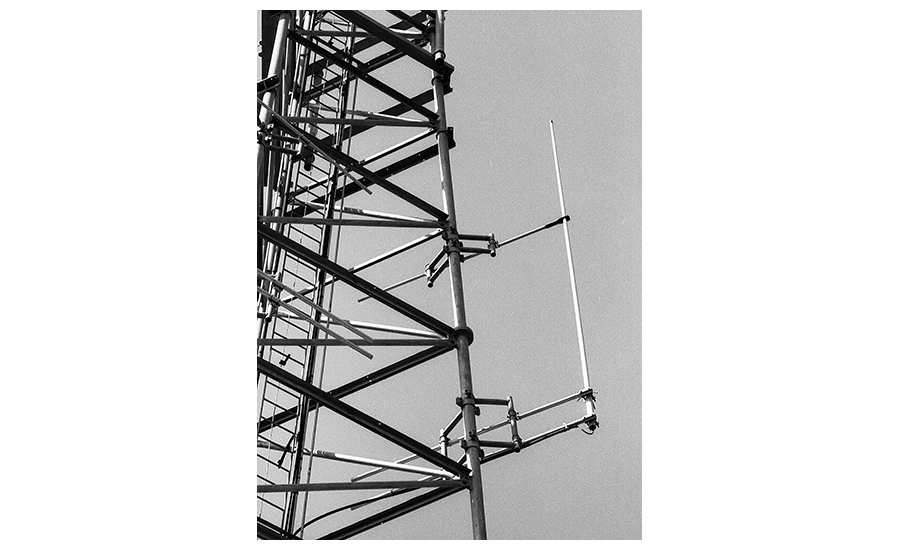
Depending on what type of outage occurs determines the plan for emergency sources, adds Kelly. Full facility permanent backup offers a consistent peace of mind but comes with high upfront and ongoing maintenance costs. If worried about a planned utility outage or short-term relief provisions, a roll-up generator can be added to the design. The most cost-effective prevention is to put life safety and critical loads on permanent generators to allow any equipment to be fed when needed from a roll-up generator. The other option is microgrid or cogeneration solutions. These are utilized when you supplement utility power with an onsite generation system that can be used to feed power back to the grid. Solar, batteries, natural gas and diesel all have options that provide backup to a facility and offset energy charges.
And—don’t forget maintenance because backup systems of any type tend to be forgotten until an emergency occurs. “It’s recommended that onsite generator systems are tested regularly per manufacturer recommendations,” adds Kelly.
Speaking of backups, Gray’s Hird suggests that owners may want to look for properties where the utilities are either looped or fed from multiple sources. In the event of a local outage (dropped power line or broken water main), the provider is better equipped to minimize the loss of use having a secondary means to provide the utility. But keep in mind that certain regions may have limitations on power, water and gas usages during times of extreme weather conditions, such as droughts, deep freezes or extreme heat.
Resources:
“Marshalltown, Iowa, JBS Plant Suffers Tornado Damage,” Sara Brown, Farm Journal’s Pork Business, July 20, 2018
“Selecting Appropriate Mitigation Measures for Floodprone Structures,” FEMA 551, March 2007; https://www.fema.gov/sites/default/files/2020-08/fema_551.pdf
“Safe Rooms for Tornadoes and Hurricanes: Guidance for Community and Residentail Safe Rooms,” FEMA P-361, April 2021; https://www.fema.gov/sites/default/files/documents/fema_safe-rooms-for-tornadoes-and-hurricanes_p-361.pdf
“2020 ICC 500 ICC/NSSA Standard for the Design and Construction of Storm Shelters,” International Code Council (ICCSafe); https://codes.iccsafe.org/content/ICC5002020P1
Looking for a reprint of this article?
From high-res PDFs to custom plaques, order your copy today!