Investing in Sustainability
While every company wants to be completely sustainable, where investments get made sometimes need to be strategic. This is a look at but a few possible decisions and what’s driving them.
There are many reasons for wanting to make a facility more sustainable. Arguably two of the biggest reasons are, one, appealing to consumers who care about purchasing from companies that align with their own values and, two, reducing operating costs. But the price tag on more efficient equipment or materials used in a facility’s construction is often higher. It leads to the question of whether or not springing for those more efficient purchases is worth it. The obvious answer to the question is, “Yes.” Numerous studies have shown that investing in energy efficiency saves money in the long run. The real question is, though, how quickly that ROI is realized. And, for some investments, there may not be a direct ROI at all.
“Beyond the benefits of direct return on investment, the interest in increasing consumer confidence in their brand as a sustainable manufacturer is outweighing the costs to implement,” says Nathan Arnold, PE, director of client development at Hixson Architecture & Engineering.
Arnold adds that while sometimes technology might be too unproven to invest in, it often comes down to short-term financial goals not meshing with the cost of implementation. But, there are some investments that make a lot of sense to start traveling down that road of sustainability.
“If a company is not already doing it, some great places to start are things like water reduction and reuse, or reducing energy by reclaiming heat from various sources,” he says. “For example, consider things such as boiler blowdown heat recovery, stack economizers preheating boiler feed water, compressed air heat recovery or heat recovery from HTST cooling. These are all common elements in Hixson-designed projects, but some older facilities may not yet have implemented these strategies.”
Renewable Energy
The cost of any energy reliant on fossil fuels has gone up. Period. While it’s true that those costs have come down in recent months, it doesn’t change the fact that a wide, seemingly arbitrary, set of factors affects prices—which in turn affects the bottom line. Facilities that use natural gas in their food production instead of electricity have been impacted more. But making the switch from gas to electricity isn’t always worth it if it can affect product quality.
Colorado-based snack brand Bobo’s recently opened a new state-of-the-art production facility in Loveland. This new 123,000-sq-ft facility is expected to increase production of the company’s bars, bites and toaster pastries by more than three times to help meet growing customer demand while reducing its carbon footprint. The first part of reducing that carbon footprint was facility consolidation. Bobo’s reduced its number of facilities from three to one, with an expected five production lines up and running by February 2023. The company has chosen to purchase additional offsets to ensure product quality.
“We do still use gas ovens versus electric, and that's with the intention,” says Bobo’s CEO TJ McIntyre. “We previously had a combination of electric and gas in our oven network, but we can calibrate the gas just so much better. In our opinion, with the way that we bake, we can't get there with electric. So we're going to have a carbon usage with the ovens that has to be offset because we're going to stick with natural gas.”
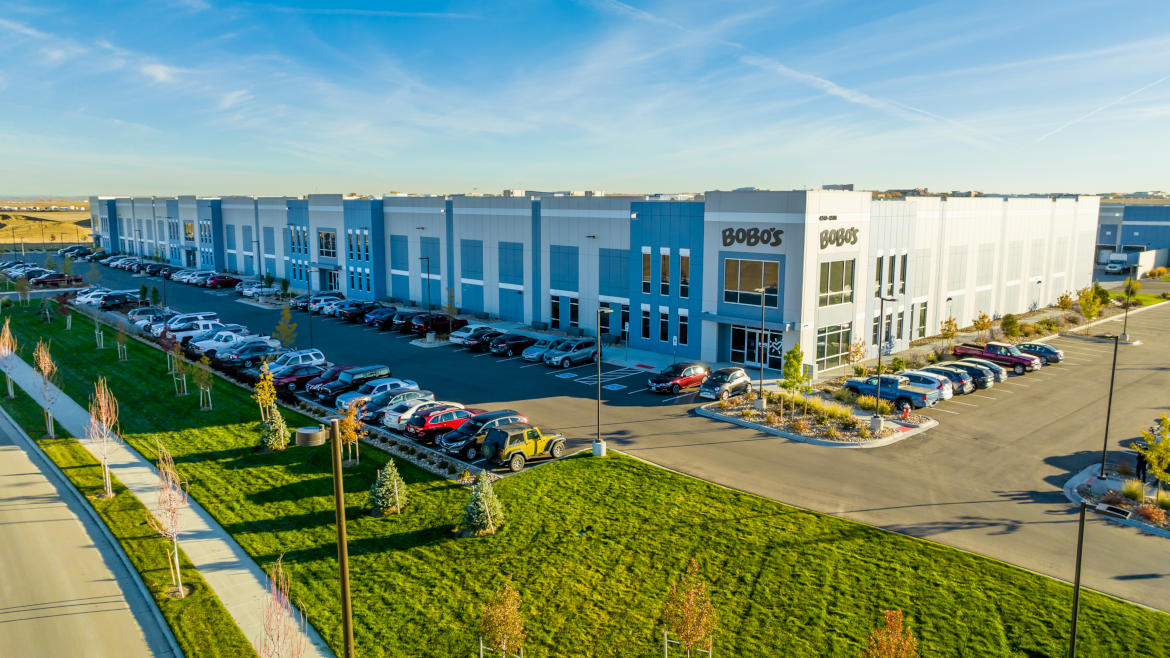
Bobo’s is offsetting the majority of its carbon usage through wind power. In a program similar to what Kerry’s Rome, Ga., facility uses for its renewables, Bobo’s is taking advantage of the Platte River Power Authority’s GreenSwitch Program. Customers that purchase electricity from the City of Loveland, including residents, small businesses or large corporations, can opt to buy blocks of GreenSwitch energy. For each block of GreenSwitch energy purchased, $1.20 is added to the monthly utility bill, and as many GreenSwitch energy blocks needed to cover a business’s usage can be purchased.
In the case of Bobo’s, getting started was a simple process of Loveland Water and Power’s customer relations manager, Tracey Hewson, meeting with Bobo’s Jim Stewart, director of environmental health and safety, who had been charged with making sure electric usage is covered by GreenSwitch Blocks. Bobo’s expressed its desire to achieve net carbon neutral goals in the near future and saw this as a great opportunity to support this mission. Bobo’s usage has increased each month since the company has been enrolled in the program because of its rapid growth and bringing on additional manufacturing equipment to support the expansion.
Bobo’s sees that added cost to its utility fees as an essential component of its mission. In fact, the only real difficulty is when people visit the facility. “They’re kind of looing up on the roof like, ‘Where are the windmills?’” says McIntyre. “There are no windmills on the building. I don’t think that really happens with any company that commits to wind power. I think they’re relying on a company focused on wind power to generate that for them.”
Green Shipping
Higher costs for fossil fuels are best seen at the gas pump, which drastically impacts shipping costs, however there aren’t many quick fixes to that problem. Hybrids and EVs are an option for consumer vehicles, but not so much for manufacturing yet. While PepsiCo did receive the first of its promised Tesla Semi trucks this past December, and Anheuser-Busch also has orders in for the EV rigs, the lack of availability coupled with the premium cost (partly because of that lack of availability) means converting to an electric fleet isn’t a realistic option.
In fact, most solutions with regard to shipping require time and planning, but can often pay off by mitigating fuel costs to at least some degree. For example, many brands that use rigid packaging can look into the viability of switching to flexible packaging.
“Flexible packaging is more durable, light, and protective than many alternative packaging options, which are the hallmarks of sustainability,” says Allison Keane, president and CEO of the Flexible Packaging Association. “[F]lexible packaging optimizes volume and weight to maximize storage and transportation efficiency while reducing the amount of packaging waste in need of end-of-life management. Increasing efficiency and reducing packaging waste results in source reduction—the most effective, environmentally preferred method of addressing excess waste.”
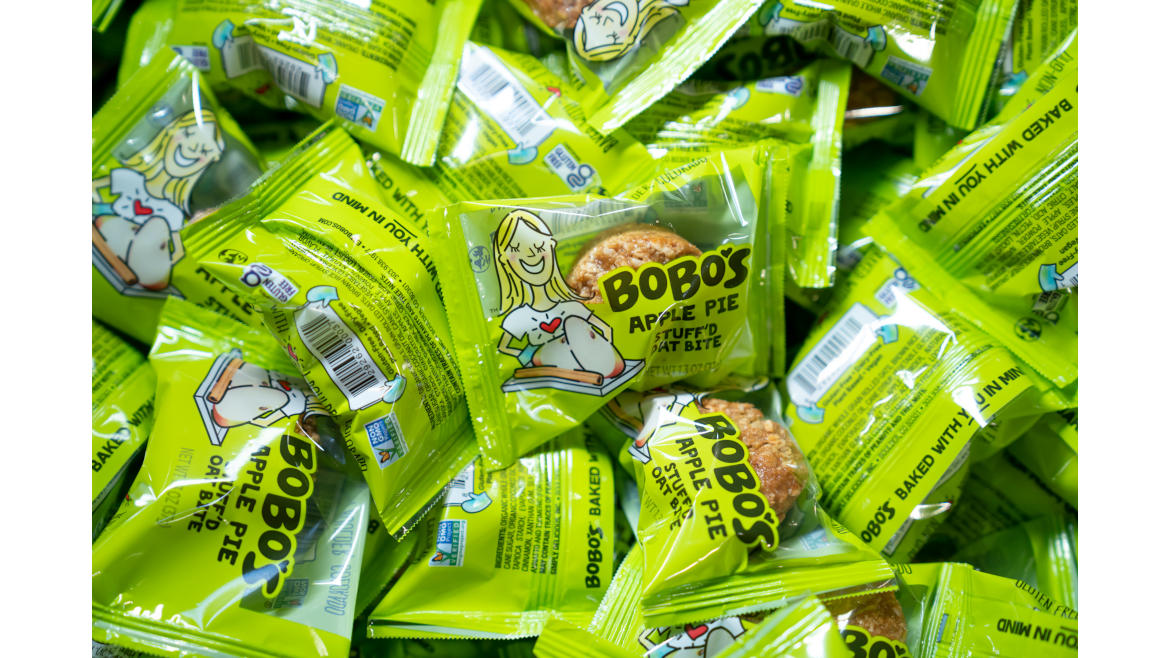
Additionally, flexible packaging can help improve shelf life. “Flexible packaging can be designed with high-barrier materials and air-tight seals, ensuring gas and moisture ingress or egress can be avoided and can also be suitable for pasteurization and retort applications,” says Paula Birch, global sales director of flexible packaging manufacturer, Parkside. “This extended freshness means less product is sent to landfills due to spoilage. In addition, the ability to reseal also reduces the consumer's reliance on secondary plastics, such as cling film, in the home.”
Packaging materials all need energy and resources to create, so cutting down on material usage cuts down on energy usage. Although the reduced energy usage isn’t necessarily something food processors see the direct benefits of, they could see financial benefits by not having to purchase as many materials.
Another underutilized way to improve sustainability in shipping operations is by taking a look at what the products are set upon for shipping: pallets.
“A plastic pallet can be one of the most important assets in a food manufacturing environment,” says Alison Zitzke, senior product manager for ORBIS. “Most consumers don’t think about how their food travels in the supply chain and gets distributed. Throughout every step of the supply chain, from inbound raw materials to delivery to the store, a plastic pallet can provide superior efficiencies and product protection.”
Zitzke says that plastic pallets are a sustainable and efficient alternative to wood because of their extreme durability, high load capacity and long service life. “The durability of reusable plastic pallets allows them to make a tremendous number of trips before being recycled, representing great savings over wood pallets on a cost-per-trip basis. In eliminating cardboard corrugated packaging and wood pallets, you also eliminate their waste. The long service life of reusable plastic pallet solutions reduces negative environmental impacts as they take hundreds of cycles through the supply chain before being recycled. Their recyclability adds to their environmental benefits, as reusables can be recycled and reprocessed into new packaging solutions at the end of their useful life,” she says.
LEED Certification versus ‘Built to LEED’
The question of whether or not to certify a building that’s been built to the U.S. Green Building Council’s (USGBC) Leadership in Energy and Environmental Design (LEED) has been around almost as long as the rating system has been in existence.
While some facility owners choose to follow through with certification, others feel that the added costs for certification aren’t worth it if the guidelines have been followed. But findings by Ball State University, Browning Day and Turner Construction on the Indianapolis High Performance Building Cost Effectiveness Study suggests that the costs of certification are insignificant when compared to the total ROI of a certified facility.
“The study reviewed the additional hard and soft project cost increases with each level of certification of the building completed in Indianapolis,” says Daniel Overbey, LEED AP, LEED Fellow, assistant professor at Ball State University and director of sustainability at Browning Day. “They found that while working to achieve LEED v4 did increase upfront project costs, they also emerged with a better understanding of how to avoid these costs with actions taken earlier in the process.”
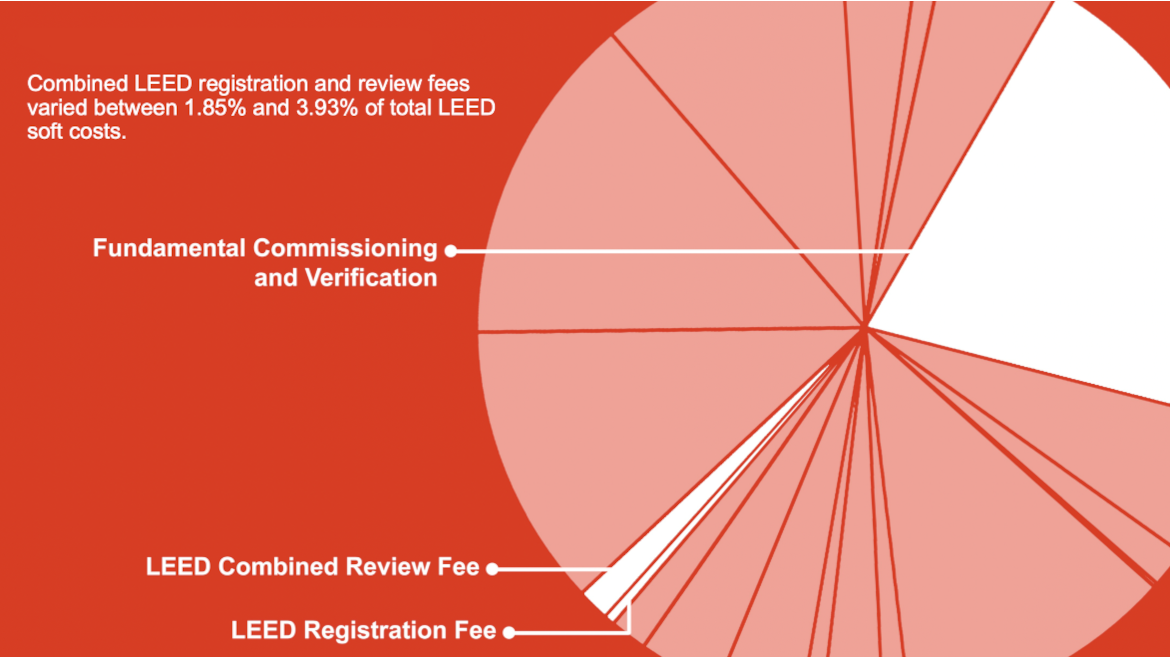
Overbey says that owners can get a positive ROI on the cost of certification, even if those adaptations to pursue LEED were made late in development.
“The LEED project registration and certification process combined amounted to roughly 2 to 4% of the project’s soft costs,” he says. “This is a small price to pay for the rigor of third-party review and certification. The findings of this study can be relevant to any city in the United States and helps to clarify why there is truly a business case for LEED.”
Consumer Sentiment
As Hixon’s Arnold addressed earlier, the most intangible reason to invest in sustainability may also be the most powerful: consumer sentiment. Study after study has shown that consumers are demanding greater social responsibility from manufacturers, especially Gen Z. They want to buy products from companies that display an alignment with their own core values. With a steadily rising concern for the environment, brands need to take notice.
“According to 2020 data from IBM and Morning Consult reported by Vogue Business, Gen Z is willing to pay 50% more for an item that is sustainable and Millennials up to 33% more,” says Carl Tiu, first vice president for F&B financing at BHI. “A 2020 article in the magazine Glossy noted that 82% of Gen Z and Millennials would switch to a natural product with comparable results, while 77% would switch to a sustainable product when the product efficacy was the same.”
Deciding whether or not to change how a product is made to be more sustainable is not an easy choice to make. Bobo’s ultimately decided to find other ways to be sustainable to ensure its products still have that homemade element.
The effect is being seen by retailers as well, which is spurring them to ask their suppliers to adapt. But some, like Bobo’s are already seeing how social responsibility affects business.
“The social side of our mission has always been front and center and will continue to be,” says McIntyre. “But this commitment [to sustainability] we're making as a company is one our customers are going to be really happy to hear about. Some customers aren’t asking for yet it, but they're going to be. And they’re going to be really happy that we did it with others because we're achieving scale with them. They're demanding it. And we've got the right answers.”
“Food processors are increasingly aware that sustainably designed facilities offer many opportunities to improve their environmental footprint, and being a company at which employees are proud to work and from which consumers proud to purchase,” says Arnold. “Yet because there is no 'one-size-fits-all' approach to sustainable design, these companies often struggle with how to define and implement sustainable solutions that make sense financially and operationally. In these cases, it is best to consult with a reputable, experienced A&E firm to determine realistic, results-oriented sustainable solutions that are appropriate for your facility based on budget and level of interest.”
BIM
The U.S. Energy Information Association says that while progress has been made to be more energy efficient, many buildings in various sectors show increasing energy consumption. “The industrial sector uses more delivered energy than any other end-use sector, consuming about 54% of the world’s total delivered energy,” according to the U.S. EIA. This is why building information modeling (BIM) has become an essential tool for maximizing a facility’s energy efficiency, and any company embarking on a new construction project or renovation can likely stand to benefit.
“BIM offers actionable data that can guide the design-build process and optimize sustainability. It allows builders and owners to analyze different iterations of a proposed facility’s conceptual model before approving the final design,” says Leo Fernandez, Assoc AIA, design production manager for Stellar. “BIM’s underutilized power lies in the data embedded in every object within the puzzle of a building’s design. Every puzzle piece and every shift to that puzzle is seen and understood across disciplines, streamlining the design-build process and providing a wealth of knowledge about a project before finalizing design, during construction and throughout the lifetime operation of the building.”
Fernandez says that there are four ways in which BIM can maximize sustainability on a project:
- Increased energy efficiency — BIM maximizes energy efficiency by allowing designers to foresee potential opportunities and issues. This includes innovations like solar studies, which assess how much energy the building will require for heating and cooling in regard to its orientation of the sun, and energy savings if, for example, the building were rotated 90 degrees. Also, BIM can establish how the new facility might affect neighboring buildings (creating shadows) and calculate energy consumption based on the building’s shape, size and volume.
- Material selection — BIM can help identify the best-suited materials for a certain project, including specifications that can lower environmental impact by integrating BIM with a modified search algorithm and supplier performance rating. Cost and environmental comparisons can then be generated based on different material combinations and building designs.
- Waste reduction — Streamlining construction minimizes opportunities to squander resources by ensuring that everyone knows where the materials should be for that specific section of the project. This insulates against unnecessary moving, handling and potential loss of supplies. Carbon emissions, as well as environmental impacts to the surrounding site, can also be calculated.
- Track long-term operational energy usage — BIM can assess and track the energy use of a building in real time, which helps identify inefficient systems and weak points such as heating, cooling and energy consumption “hot spots.” BIM’s ability to predict long-term costs enables clients to compare and select the most sustainable engineering system product packages.
Looking for a reprint of this article?
From high-res PDFs to custom plaques, order your copy today!