Training
Help Wanted: Food Industry Technician Program Surges Forward
This innovative training program, started by the Food Processing Suppliers Association (FPSA) in 2019, develops essential plant skills that allow workers to flourish in early career settings.

Recent graduates from the FPSA’s FIT program. Three instructors run the program and instruct students on 35 pieces of donated equipment from FPSA members. Image courtesy of the Food Processing Suppliers Association
U.S. manufacturing construction spending touched a 20-year high in April 2023, when it reached a $194 billion annual rate, according to the Federal Reserve. Not surprisingly, the food industry is part of this story. IMI SalesLeads research cites 74 new construction or modernization food and beverage projects will start by the end of this year.
With explosive growth in the industry, food brands and original equipment manufacturers (OEMs) are working hard to add younger employees and leverage older workers or mentors. The opportunity to pass down skills from “greybeards” will only be here briefly and, according to the Bureau of Labor, Deloitte, and PEW Research, 10,000 boomers reach retirement age daily and represent 27% of the U.S. manufacturing workforce.
To address this pressing need, the Food Processing Suppliers Association (FPSA) created the industry’s first national Food Industry Technician (FIT) Certification program in 2019. The program's mission statement addresses the acute need for more technicians to manage and service complex equipment and machinery in processing and packaging.
“Since the program started, we have employed a continuous quality improvement mode for every aspect of the program, including hands-on training via donated food processing equipment to education trainers hosting field trips at manufacturing facilities,” says David Seckman, president and CEO of FPSA. “Clearly, there is a great need for trained technicians in the food industry.”
Of course, OEMs are hiring and investing in their workers too. Handtmann Inc. is an OEM supplier to the food processing industry—filling, forming and process line solutions for meat, bakery, dairy and pet food—and has been a leader in promoting and developing the FIT program from the beginning.
“For years, we noticed people were going to traditional colleges, but not so much toward technical training or a trade school,” says Shawn Kentch, training manager at Handtmann Inc.
“At the inception of the training program, we brought in more than two dozen executives from different companies and numerous subject matter experts in engineering and maintenance,” says Bob Greaney, consultant with the Food Industry Technician program. “Everybody in those meetings had some years of experience working with a community college or vocational educators in a mechanical internship program.”
After refining the curriculum from those meetings, FPSA chose Lincoln Tech (LT) as its foundational educational provider and decided to open the program at LT’s Indianapolis campus. Three instructors run the program and instruct students on 35 pieces of donated equipment from FPSA members.
“We cover 26 chapters on maintenance topics that you simply wouldn't find in an Electronic Engineering Technology (EST) program,” says Greaney. “We’re also teaching soft skills, such as talking to technical people and writing maintenance reports.”

With input from the FIT board, the training also offers hands-on experience. “For example, we create situational exercises where students need to disassemble, inspect and document the condition of gearboxes,” says Greaney. “The students have to remove the fasteners from the gearbox using proper tools and reattach the inspection cover using a torque wrench.”
“The FIT program is working well because students are getting hands-on experience and learning that there are so many opportunities in the food industry,” adds Su Luwin, live operations HR coordinator at Miller Amish Poultry.
Varied Workforce Requirements
Besides the critical hands-on training at Lincoln Tech, students learn about different types of valves, fittings, hydraulics, pneumatics, automation, sensors, electrical and pumps. “We created a separate sensor lab, since they are so common in the plant and have to be replaced,” says Greaney. “So students learn about different sensors, wiring and power supply.”
For Handtmann, the food industry equipment supplier needs a well-rounded knowledge base for its service technicians who travel to customer sites. “We don't need an electronics or mechanical expert at all,” says Kentch. “We need somebody with a good understanding of how things work, and we help them build upon those skills with our own training program at Handtmann.”
Handtmann’s approach includes giving new technicians time in the field with a mentor so they can work through issues and build “muscle memory for the equipment they will need to service or troubleshoot,” according to Kentch.
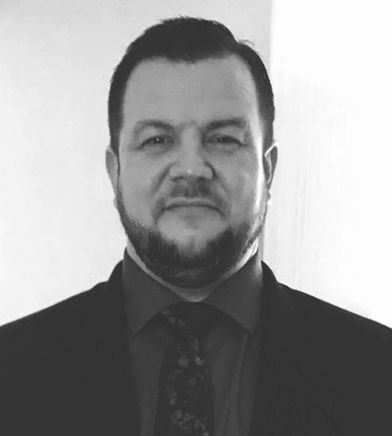
We don't need an electronics or mechanical expert at all. Handtmann needs people with a good understanding of how things work.”
— Shawn Kentch, training manager, Handtmann Inc.
Image courtesy of Handtmann Inc.
“I think it's also something that has fallen by the wayside is employers investing in their employees,” says Kentch. “Typically, they bring them onboard and they think this person is ready, but they don't understand the need to invest in more training to maintain and retain these employees.” Handtmann has hired nine students over the past three years, and several have moved higher within the company.
Food Processing Demand
The FPSA’s FIT program prides itself on providing students with a foundation so food companies can recognize talent and direct these workers to specific applications. “Pay scales in processing plants have increased due to demand,” says Greaney. “Food processing plants offer a hundred different pieces of equipment and it’s attractive to graduates. Students realize a solid baseline of skill is important in working on many different types of equipment.”
Going forward, the FIT program keeps evolving and is always looking for feedback. Recently, a food company leader suggested adding more troubleshooting examples in the plant, such as putting bad bearings on a machine so they could actually see what these look like. Moreover, the LT program is adding more plant floor and equipment video content.
“Since we don’t have every piece of equipment that is part of a production plant, we offer a vast array of videos on different types of food processing equipment,” says Seckman. Also, companies visit the LT campus during open house days and meet future graduates. Instructors meet the companies, ask about onboarding processes and help place graduates.
The FPSA is excited about the early returns on the training program and understands that demand is only increasing. “One of our main focuses right now is ensuring that we offer more classes and FIT graduates to help us fill the industry’s hiring needs,” says Seckman. “We’re looking at additional campuses for the program in various locations throughout the country.”
Looking for a reprint of this article?
From high-res PDFs to custom plaques, order your copy today!