Lilliputian principles of design

Positive displacement kinetics is applied in the BSP to improve precision and reduce damage when conveying materials. Vertical rotating disks create lock-up zones to achieve linear mass flow from a hopper inlet to a discharge outlet. A defined transport channel is created without any pulse movement, resulting in greater accuracy than screw conveying can deliver.
K-Tron claims to achieve volumetric accuracy to within 0.1 percent, compared to 2 percent for screw feeders.
The basic technology is licensed from Gardena, CA-based Stamet, Inc. (shorthand for solids transport and metering). Stamet's engineers developed the technology in the late 1970s for the transport of oil shale for processing. When that market dried up, inventors Donald Firth and Mort Winston adapted the system to feed lumps of coal to power plant mills with units measuring 6 ft. in diameter. Currently, Stamet is applying a $1 million Department of Energy grant to create a mechanical rotary disk feeder for granular coal into systems pressurized at up to 500 pounds per square inch (psi).
K-Tron's original intent was to modify Stamet's system to handle plastic pellets, but the precision and gentle handling were obvious benefits for dry, bulk foods. The Pitman, NJ-based firm is in the process of rolling out three versions of BSP that feed anywhere from 0.07 to 160 cu. ft. of material per hour.
Jim Foley is vice president and chief technical officer of K-Tron. He holds an undergraduate degree in mechanical engineering and a master's in software engineering. Foley joined K-Tron in 1982, serving as a project engineer before getting involved with product development.
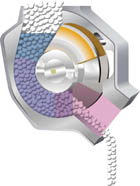
Foley: We came across the technology in the 1990s and worked on it for about five years before releasing a product to our injection molding-equipment division about two years ago. We thought the technology was unique and elegant in design. In 1999, we secured the licensing rights for units up to 24 in. in diameter, though we can go as wide as we want by simply adding more ducts. In early 2003, we acquired Pennsylvania Crusher Corp., a maker of size-reduction equipment that had licensed the technology for units larger than 24 in. in diameter.
Stamet realized this was really a pump that can displace materials against pressure, which is the definition of a positive displacement pump. They're now developing pumps that operate under more than 200 psi of pressure for advanced combustion and gasification systems. Our license limits us to plus or minus 3 psi.
FE: In adapting the pump for food and other granular materials, what were some of the obstacles you faced?
Foley: Reduction in cost was a major emphasis, so different materials were tried. You wouldn't think of the BSP as a low-wear device to look at it, but once material is locked up between the disks, there is very little drag, friction and wear. We actually developed a plastic version using a highly engineered polymer, but there were some issues so we turned to metal construction, beginning with aluminum. The largest unit comes in stainless steel, as well.
Much of Stamet's work only applied to coal, and the same rules of thumb didn't necessarily transfer. Coal is a friable material, and the tremendous torque of the Stamet system would easily crush any coal that was in the wrong place. With plastics and food, a pellet in the wrong place could stall the pump and increase maintenance costs. We engineered the pumps to make sure that can't happen.
A lot of design work is in the geometry of the disk. In order to get higher flow rates, you can stack disks side by side and still have a pump with a reasonable diameter. Wear occurs if you starve the device, and feeding material at a fast enough rate was a challenge in designing the smallest pump, which has a correspondingly small throat size. The solution was to keep the speed relatively slow, a maximum of 30 RPMs, compared to 300 or 400 RPMs for a screw conveyor.
FE: Once material enters the pump, what kinetics occurs?
Foley: Basically, it works with friction. If there was no friction, material would flow right through. Instead, there is particle-to-particle friction and friction between the particles and the walls. The combination of head pressure and inter-particle friction pushes the material against the walls, causing it to stop free-flowing and locking it into the chamber. Material then rotates with the walls until it reaches the discharge point. There is no surging at discharge, and that is a huge advantage.
FE: It seems paradoxical that movement based on friction would produce gentle handling.
Foley: Once the material locks up between the disks, there's no more dynamic friction. Static friction takes over. Particles want to push outward, and once they lock into the walls, there is no more movement and no opportunity to degrade the material. The only drag is on the glide surface, on the back end of the device.
We've fed cornflakes through the pump without crushing them. They slid along the back surface and through the discharge. There was less damage than you'd experience with a belt feeder, which pulls material through the inlet and tends to sheer the top. There's almost no material degradation through this pump.
FE: How does the pump deliver its accuracy?
Foley: There's a known volume per revolution with positive displacement. That can't be said about a screw. A rotary valve has a known volume, too, but as you increase the speed, it tends to become less precise. With this device, you can calculate the volume of the disks, so it's truly volumetric feeding, and it's continuous, which is unique.
The problem with volumetric feeders is that all bulk materials vary in density. A 0.5 percent variance can create havoc. A gravimetric feeder can compensate for those changes, and that's what we're pushing for in critical applications.
For gravimetric feeding, we add a scale, controls and feedback loops to compensate for differences in bulk density. We also use brushless stepper motors to provide constant torque and very accurate speed control. The advantage over AC or DC motors is that we eliminate any gear reduction and drive the pump directly. To get digital control over the motor, we synthesized two sine waves digitally in our proprietary drives, rather than using square waves that step from one pole to the next. That makes it act more like a smooth-running synchronous motor, but with the accuracy of a stepper motor at very low speeds.
FE: What is the range of particle sizes that will work with the pump?
Foley: We can scale the pump to handle larger particles, though 5 mm is probably a realistic top end for current units. If particles won't flow into the chamber, you have a problem. The inlet itself is the restriction to the application.
We're saying particles have to be greater than 100 microns and granular in nature. In reality, we've already fed powders through the device. The critical factor isn't so much the size, but rather how the material flows. If it is not free flowing, it won't go into the disks on its own and won't work.
FE: How can you assure users that the first particles in will be the first particles out?
Foley: There is no place for material to hang up. Once it goes in, it's guaranteed to stream out in exactly the same way. On a screw feeder, there are always dead zones in the hopper; even with a belt feeder that can happen.
FE: Contact surfaces are dimpled. How did you arrive at that design?
Foley: We tried grit blasting, grooved surfaces and other solutions, but found that dimples were the best solution to enhance friction on the disk, based on a minimum 0.25-in. radius, as specified in 3A (sanitary design) standards. It's easy to clean, and friction is enhanced without trapping the material.
FE: Is this adaptable to packaging operations?
Foley: We've looked at that. A lot of packaging is volumetric, so this could easily be integrated.
A DC motor tends to coast a bit, but the stepper doesn't, so using the stepper motor in a packaging application would result in very high accuracy. To vary the amount of material filled in a given package, all you have to do is manipulate the rotational speed.
Looking for a reprint of this article?
From high-res PDFs to custom plaques, order your copy today!