Food Engineering Plant of the Year 2017: Abbott Nutrition
High-tech production of science-based nutritionals

Through the use of redundant packaging equipment, filling system downtime is minimized. Source: Abbott.

The Tipp City facility houses Abbott’s fastest aseptic filling machines in the world, producing 800 bottles per minute. Source: Abbott.

The facility has a lab complex, where incoming, in-process, finished goods and micro testing are performed. Source: Abbott.

The blending system is comprised of a series of slurry tanks that allow continuous processing of multiple batches. Source: Abbott.

The wet processing area contains aseptic surge tanks that provide critical buffer capacity between commercial sterilization and filling operations. Source: Abbott.

The tank farm houses bulk chemical, ingredient and finished product tanks. Source: Abbott.

The facility has a raw ingredient warehouse with high-efficiency flow-through racking. Source: Abbott.







See the 2018 Food Plant of the Year award winner!
With personalized nutrition topping many lists of food trend predictions for 2017 and some of the biggest brands known for their feel-good treats now offering good-for-you food, health and wellness have reached a pinnacle of importance in the food and beverage industry. Further solidifying this is Food Engineering’s coveted Food Plant of the Year Award going to Abbott’s nutrition facility in Tipp City, Ohio.
Consumers might not think of food products when they think of Abbott, but they’re probably familiar with some of its top brands such as Similac and Ensure.
Article Index:
The company is busy responding to the increased demand for its nutritional products. In 2014, while the Tipp City facility was being built here in the US, two other Abbott plants, one in Jiaxing, China and another in Jhagadia, India, were also undergoing construction. The total number of Abbott facilities is 14, with half located in the US, and the other half located in foreign countries.
The ground was broken for the Tipp City facility in 2012. The site selection decision was made for a number of reasons, including it being shovel ready, in close proximity to an interstate and its access to the necessary utilities.
“Abbott’s strategy is to locate our nutrition manufacturing close to our consumers. So, Tipp City was a natural choice for supplying our consumers in North America,” says Angela Doerr, site director for the Tipp City plant.
Ohio’s Interstates 70 and 75 are both nearby, which offer easy transportation to all directions of US population centers, as well as north of the border to Canada. It’s also located only an hour from Abbott’s US nutrition offices in Columbus, Ohio.
“Abbott is choosing to be close to our customers and choosing to invest in the US,” says Jason Smith, senior manager of Abbott’s facility management group.
The 250,000-sq.-ft. plant opened in March 2014 at a cost of $270 million on 81 acres of land, which allows for future expansions. Three adult nutrition brands are made onsite in eight-oz. and 10-oz. bottles, in a variety of flavors, for the US and Canada. The plant’s first line began operating 24 hours a day, seven days a week in 2015. In April 2016, a second filling line was added, making the plant fully operational for the first time.
Linear flow and building design
When Abbott began constructing the building, the overall goals were to optimize operational efficiency and use the latest technology and processes to ensure food safety.
“Driving every facility design decision we made was the question: How can we produce safe, high-quality products while operating the plant more efficiently and smarter?” says Lisa Rathburn, Abbott’s global engineering director of manufacturing technology.
The form of the building’s design is to serve the production functions, with product consistently moving from west to east. The different sections of the plant are aligned with the linear flow of the production process: raw materials’ receiving and storage, batch mixing and processing, filling, secondary packaging and then shipment out to the finished goods warehouse offsite.
Once raw ingredients are received, they are separated into refrigerated storage and ambient storage. Part of the food safety management plan is to only accept raw materials from approved suppliers that go through a stringent qualification process.
“Driving every facility design decision we made was the question: How can we produce safe, high-quality products while operating the plant more efficiently and smarter?”
– Lisa Rathburn
“All raw material and ingredients from vetted suppliers are tested, reviewed and approved prior to use to ensure that they meet our strict quality standards. Food safety is the key focus that incorporates end-to-end process controls from material receipt through production and final distribution,” says Erin Ducko, site quality manager.
Even though the majority of bulk ingredients are coming from company-shared suppliers audited by Abbott, inspection and some testing are performed upon entrance into the facility. Any ingredients that contain potential allergens are kept separate to avoid any cross-contact.
“We focus on hazard analysis and risk management upstream as much as possible,” says Ducko. Multiple batches are processed each day. When ready to produce a batch, ingredients are delivered to the staging area, where employees open bags and feed the contents into the powder addition hopper.
The dry blending of batch components is the only part of the production process that requires manual addition of materials. Therefore, there are multiple ergonomic solutions to ensure worker safety. For example, bulk bags are moved to hand level by a lift table, eliminating the need to bend down. In addition, a variety of dry processing equipment, such as a drum lifter and bulk ingredient hoist, is present to help improve ergonomics. To keep the area clean and safe, a dust collector is employed, as well as a series of cleaning processes. The blending of powders and liquids is segregated by design to help control dust and microbiological risks.
“Clean-in-place [CIP] is done multiple times per week based on the facility’s validated cleaning procedures and product requirements,” says Andy Cudney, plant operations manager.
Also located in the dry blending area is a separate weigh room, where micronutrients and flavoring, which require precise measurement, are weighed and dispensed for a particular batch’s recipe.
Liquid processing and filling
Ingredients are blended into different slurries and then combined into blend tanks prior to processing through the high-temperature, short-time (HTST) equipment and homogenization step. Once the product is processed and put into the holding tanks, the final vitamins and minerals are added.
In an extension from the wet processing area is the finished product tank alcove. Here, the finished product is held under controlled temperature until the product is ready for commercial sterilization and aseptic filling. In-process samples are collected and tested according to product specifications to ensure that all regulatory labeling requirements are met. The intent of the finished product storage is to ensure that product is always available for filling.
Throughout wet processing, visual management tools, including signage, electronic dashboards and audible alarms, are used to signal the status of cleaning activities to ensure employee safety. When the product is ready to be filled from the finished product tanks, the fluid goes through ultra-high-temperature (UHT) equipment to accomplish commercial sterilization before being transported to the centerpieces of the plant—the aseptic Shibuya fillers.
The Shibuya fillers are Abbott’s fastest aseptic machines in the world, producing 800 bottles per minute. These net weight fillers are only the fourth and the sixth Shibuya installations in the United States. On each filler, there are 72 peroxide heads, 108 filler heads and 32 capping heads.
The fillers, nicknamed Thunder and Lightning, are sized and customized to Abbott’s production needs. The aseptic technology enables increased manufacturing flexibility with optimal changeover and product capability. The technology was utilized to produce Abbott’s most recent product launch for Ensure Enlive utilizing the re-closable plastic bottle design.
“By taking an existing technology and applying it in a unique way we can use ingredients that would not be possible using the traditional retort sterilization,” says Ducko.
The key to aseptic processing is independent sterilization of the product’s components—bottles, caps and the fluid—then bringing them all together in the sterile environment of the filler. This is different than the retort process, where the product is packaged and then sterilized after filling.
Automation and monitoring
To accommodate the aseptic sterilization process and to provide steam and utilities, five miles of piping had to be installed.
“All utilities are remotely monitored, and each filling line has highly automated controls and instrumentation to ensure that all critical process parameters are maintained,” says Jay Smithberger, plant engineering and maintenance manager.
In between the two lines is the filler control room, which is where employees monitor the high-speed fillers. The continuous monitoring extends to the entire facility itself, with temperature and humidity being collected and controlled by a centralized building management system.
The plant’s main processing areas use Allen-Bradley programmable logic controllers (PLCs) from Rockwell Automation. The human machine interface was developed using Rockwell Software FactoryTalk View Site Edition (SE) and uses a network distributed process with an application server and redundant HMI servers.
The Plant PAx system was developed using the Rockwell Automation process library, which provides views of each device, including pumps, valves, analog devices and more, on one screen. This allows for consistency throughout the plant and reduces engineering time.
The Rockwell Automation FactoryTalk Batch product provides supervisory batch control to coordinate the processing across the multiple areas. Four quad-monitor operator stations are in the control room, where plant operators are able to interact with the process control system using the FactoryTalk View HMI.
Secondary packaging
The packaging hall is designed with high-speed conveyors and accumulation points in order to optimize the efficient supply of bottles and caps to the filler and secondary packaging post filling. The filling and packaging are achieved with no human touch. To provide safe, ergonomic and easy access to all areas, a series of stairs and platforms are built around the conveyors and equipment.
The bottles undergo one final rinse in the filler before they are conveyed to the accumulation table in the secondary packaging hall. The bottles, which are hermetically sealed during the filling operation, then proceed to the sleeve labeler and steam tunnel, where the overwrap technology provides the tamper-evident seal integrity of the full package.
Installed in November 2016, a variable cartoner is the newest piece of equipment used in the plant. The machine has the flexibility to support multiple carton configurations. Alternatively, the bottles can be processed loose or through Hi-Cone machines that apply a plastic carrier. The case packing equipment packages the loose bottles, cartons or carriers into cases that are formed around the product and glued to ensure package integrity throughout distribution. Then, a robotic palletizer stacks the cases, enabling shipment to the offsite storage warehouse. The close proximity of the shipping dock to the line allows the product to be easily transferred to the truck.
“In order to enable the highest overall equipment efficiency [OEE] of our operation, the secondary packaging lines include redundant equipment,” says Cudney.
Moreover, all of the equipment in the facility has quick changeover times to ensure flexibility and efficiency in production and packaging. This all helps to support the just-in-time manufacturing practices of having all the right materials at the right place and at the right time.
“The key to the operation is our highly skilled and trained team enabling optimal production with minimal human process interaction,” says Cudney. “This allows for better uptime, more flexibility and less human error.”
Site and building innovations
The building has 40-foot high ceilings made of concrete and was built using post-tension construction. This allows for few columns and less structural elements with horizontal surfaces, which can harbor accumulations of dust, dirt and other materials.
“The plant is LEED certified and has just obtained ISO 50001 certification, which demonstrates Abbott’s commitment to environmental sustainability and utilities conservation,” says Doerr.
“In order to achieve LEED certification, we reduced one-third of our water use, developed a storm water management program, diverted three-fourths of construction waste from landfill and 15 percent of our building materials were recycled,” says Smithberger.
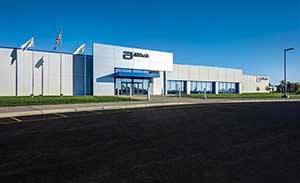
The main entrance into Abbott’s Tipp City, Ohio facility. Source: Abbott.
According to ISO, the new standard is about “recognizing the scope of responsibilities and creating a management structure and resources appropriate to the needs of the organization.”
To meet the ISO standard, the plant uses a number of energy-efficient practices, such as the use of LED lighting in many areas. To conserve water, more than one-third of water is reclaimed and reused in the process. A storm water management plan is in place to protect receiving stream channels from excessive erosion. The building’s roof surface has a solar reflectance index meeting the LEED credit requirements.
All utilities are located in a Central Utilities Building (CUB). Housed within this facility are the plant’s air compressors, boilers, chillers, water softeners, water filtration system and power systems. A utility pipe bridge is used to connect the CUB to the main production building. This separate location helps control the noise levels, provides closer storage of bulk liquid to the end-use points and enables future expansions.
As for the air handling equipment and other building management systems, they are located on an interior mezzanine. This allows maintenance workers to service them from within the facility and not on the roof. Also, this mezzanine allows sterile water generators, wet processing utilities and steam-reducing stations to be located above the points of use, rather than being piped from a utility room or taking up processing space.
Continuous improvement
The overall goal of Abbott is to be best-in-class in all aspects, including safety of employees, safety and quality of products and the environment. All plant managers make it clear that people at Abbott are their greatest asset, and the company strives to have engaged and satisfied workers. A lot of that begins with employee training.
“Our technical training program incorporates adult learning concepts and tools to facilitate comprehensive learning and retention,” says Jackie Craine, plant business human resources manager.
The onboarding process begins with time invested in a classroom dedicated to the essential elements of quality and safety. Then, new team members are paired up with experienced learning mentors when they move to the production areas for hands-on training. The team members learn the why, the how and the impact of their responsibilities and must demonstrate knowledge of all the production steps, including the order of ingredient addition, before being certified to work independently. The training culture has enabled the rapid expansion and stability of the operation.
“Once you know the why, the how becomes easy,” says Craine.
Abbott also has a pledge to continuous improvement and encourages employees to contribute any suggestions that might make the production process easier, safer or more efficient. Over 3,000 ideas were submitted last year plant-wide, and of those, more than 2,000 were implemented. Furthermore, team members are empowered by a “just do it” system to bring ideas for a team vote and rapidly implement them.
The cross-functional teams perform root cause analyses to rapidly solve problems. The management operating system (MOS) that utilizes a tiered structure enables rapid decision-making based on review of plant performance at the equipment, line and plant levels.
As for continuing sustainability efforts, the plant is currently striving to achieve zero landfill waste. To do this, the plant has programs focused on eliminating inline waste, as well as recycling and reusing the materials.
Abbott is continuing to foster its relationship with the plant’s surrounding community of Tipp City. Even before the company broke ground on the site, Abbott held a number of town hall meetings to introduce Abbott to the community. That engagement continued—in 2016, the company sponsored over 40 events in the community.
“Consumers rely on Abbott to provide them with the nutrition to live their best lives. This is why we put the safety and quality of our products first, and it is built into the culture and everything we do at the Tipp City facility. We are proud to be Abbott’s newest US manufacturing facility,” says Doerr.
Looking for a reprint of this article?
From high-res PDFs to custom plaques, order your copy today!