Automation and food processing today: It’s about labor
Food processors have found labor scarce, difficult to retain and in need of ongoing training; automation can help.

Photo courtesy of Interroll
When we recently surveyed architectural and engineering/construction firms (A&E/Cs) and asked what trends or forces they see driving automation projects, every firm mentioned “labor” or “workforce availability” in its initial response.
A few years ago, you’d have to make the case for automation, pick a part of the plant to automate as a proof of performance, and then show a return-on-investment (ROI) of a few short years. Now with workforce issues being what they are, automation is getting a more serious look. Even manufacturers who wouldn’t have considered automation before the pandemic have changed their tune.
“Those [processors] that haven’t used automation in the past now have it at the forefront of their growth plans,” says Dan Crist, A M King vice president. “A combination of the labor shortage and the pandemic has created more urgency in implementing automation.” Crist notes that processors have no choice but to research ways to do more with fewer employees. Those that have historically invested in automation have seen effective ROI. However, some manufacturers lacking experience with automation are hesitant to move forward due to the large upfront investment.
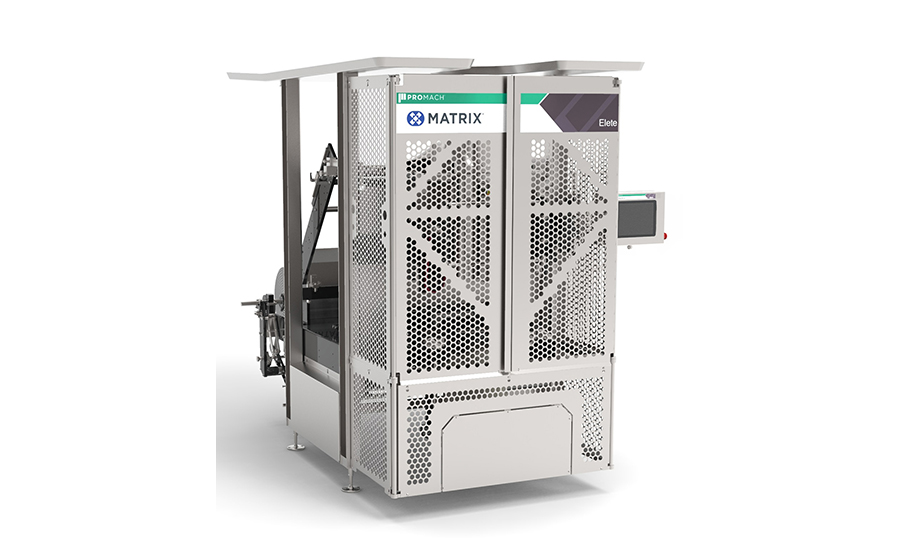
In some cases, it may be difficult to quantify the ROI that automation delivers, such as improvements in quality, operator safety or traceability for food safety, says Jeff Jendryk, vice president, business development, Spec Engineering, a Gray company. “However, most of the time, there are degrees of automation to choose from that will benefit a project at any range of budget. The most costly and elaborate solution is not always the best for any given application, nor will it provide the highest ROI.”
Traditionally, automation was mostly limited to larger manufacturers in the food industry due to the high initial costs and limited flexibility,” says Nate Larose, CMC Design-Build director of project development. “Those costs have been coming down over the past several years, and the cost of labor has been increasing so the ROI is becoming more attractive. Additionally, many owners are having so much trouble attracting and retaining labor in the current market that they are willing to consider options with a longer ROI than they might have in prior years.”
With the labor shortages and increased demand for certain consumer products, processors have found it exceedingly difficult to meet demand, according to Rick Elyar, Haskell director—business development. “Our clients are no longer looking at automation and technology as an investment to reduce costs, but as a necessity to operate efficiently as labor shortages continue.”
Of course, automation is not in all cases a panacea. “Some jobs still lend themselves better to human performance; however, when possible, the task is broken down and parts of it may be automated to address labor availability and improve worker safety,” says David Ziskind, Black & Veatch NextGen Ag director of engineering.
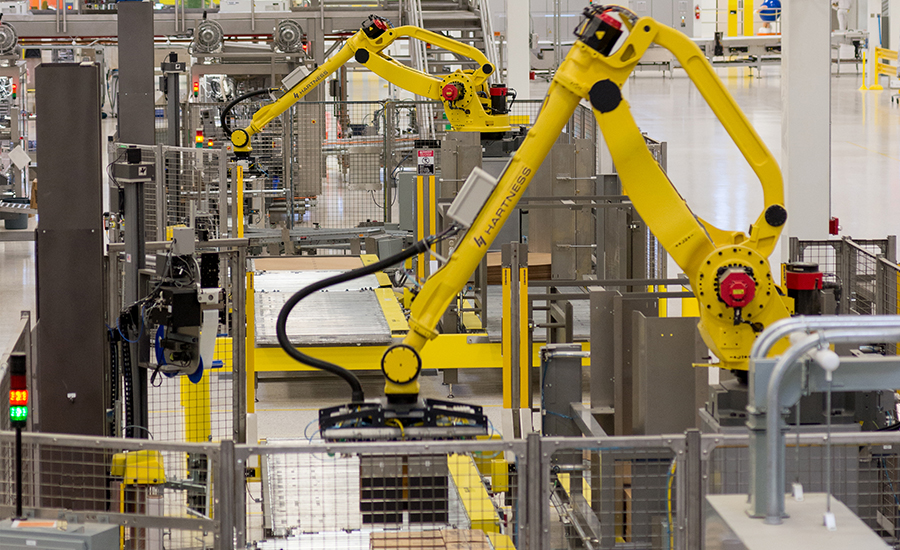
Shift in market and labor—and a new meaning for ROI
“The pandemic shifted the point of sale of many products—specifically food production—from commercial to consumer, creating production bottlenecks for many companies,” says Mike Chambers, Burns & McDonnell project manager, Food & Consumer Products Group. The COVID-19 pandemic also created demand for certain products. Overall, this altered the investment of capital from strictly an ROI exercise to maintaining business continuity. Thus, the combination of evolving demands, production bottlenecks and social distancing significantly increased the need for automating manual tasks, especially those requiring close contact.
According to Tom Wiersma, Integrated Packaging Machinery (IPM) business development manager, the automation ROI calculation has changed over the last 30 months. With a few exceptions, most all of IPM’s clients are seeking more automation. Finding and retaining the people they need to manually monitor, handle, load and sort in the downstream packaging functions are more time-consuming than ever. And the manual work involved only leads to product loss through mishandling, primary package damage and unacceptable product throughput—all of which can lead to damage to a brand.
Packaging benefits from automation
“We have seen increased interest in production automation in response to labor availability issues, improved remote monitoring technology, and labor cost rates,” says Jens Ebert, SSOE group vice president and division manager, food and consumer products. In terms of automation related to reducing personnel counts, Ebert sees an emphasis on the packaging areas. The ROI for automation projects is improving as technology becomes more developed and labor costs increase. Nevertheless, the current supply chain issues related to automation hardware may have a dampening effect in the near future.
“Automation is becoming more popular on the packaging side, especially as labor shortages are more prevalent,” says Jendryk. “Although the investment of robotics will save money, increase production and quality and reduce bottlenecks, the initial investment can provide challenges. Many facilities will choose a specific area or line to start automating in phases to spread out the investment.”
Mark Livesay, VP automated warehousing for ESI Group USA, points out several potential uses for automation in a plant, and it’s interesting to see how many of these tasks are on the packaging and material handling side of an operation. “We are seeing more processing facilities incorporating many pieces of equipment to provide advantages with food safety being at the forefront. X-ray equipment, automatic leak detection for packaging lines, sanitizers, auto- sealers, sorters, overhead power rail systems, automated carcass splitters, hydraulic indexers, automated shrink wrappers, steam tunnels, box erector systems, palletizers and pallet wrappers all contribute to overall output of product safely, but also the health of the employees who work on these lines by reducing repetitive tasks and exposure to harsh environments of these facilities.”
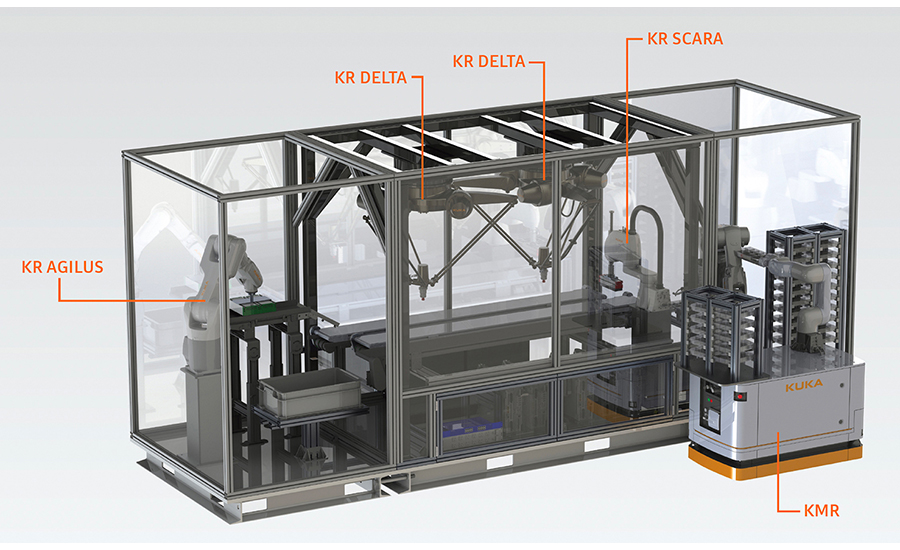
Here’s an unexpected bonus of automation, according to Livesay: Management teams have seen an overall attendance increase when an effort is made to invest in equipment that helps employees with their daily work at hand by allowing them more control over line performance, which can help the team increase output and performance.
Automated material handling and warehouse automation
“With food & beverage product demand at an all-time high, processors have looked to advanced automation solutions to offset the workforce challenges,” says Tyler Cundiff, president, Gray, Inc., Food & Beverage Group. Manufacturers are investing in newer equipment, robotics, and material handling solutions such as automated guided vehicles (AGVs) and autonomous mobile robots (AMRs). In the past, processors were hesitant on investing in advanced automation, but as labor rates increase and advanced technology costs decrease, ROI is found in the freeing up of workers to do more value-added tasks, which also promotes a higher skilled workforce.
Besides the use of robotics in processing applications, Faithful+Gould has seen a continued increase in automation in the warehouse using automated storage-retrieval systems (AS/RSs), where the key drivers are the availability and cost of the workforce, according to Greg Franzen, program director, agrifood.
Automated warehousing can significantly reduce long-term costs, according to Livesay. An AS/RS has a typical life expectancy of 25-plus years and a typical payback of 3-5 years depending on the system complexity.
Strategically implementing automation
By strategically investing in automated technologies, including smart equipment, predictive robotics and integrated systems capable of real-time data capture and analysis, food manufacturers are maximizing their return on every dollar they spend to improve existing facilities and optimize future expansions. Meeting efficiency goals through automation and digitalization doesn’t necessarily mean taking on a large-scale, end-to-end operational overhaul. Incremental investments can have a big impact, especially if manufacturers look for strategic ways to implement the right technologies across the whole manufacturing lifecycle, including downstream warehousing and distribution systems.
There are many benefits to automation, but there are associated costs to consider. Often automation can increase throughput and reduce operator count, which allows for easier social distancing. Once appropriately tuned, automation can help produce more consistent product and maintain tighter tolerances. A large benefit to the staff is reducing repetitive and dangerous tasks that can lead to employee injury over time. Plus, as you’ll often hear, robots show up for work every day.
The main concern in planning for automation is typically the upfront capital cost. If it is uncertain whether to invest in automation, a suitable payback period should be set and compared to a model of operating cost reduction or increased production. Proper planning by an engineering firm can help facilitate this process. A few other important considerations include the need for higher-skilled maintenance staff, continuous training of personnel and footprint space of equipment.
— Jason Robertson, CRB, Vice President, Food + Beverage
Long-term thinking when investing in an AS/RS is prudent as additional savings can be seen through reduced labor, less damaged product, and lower maintenance costs, all the while increasing accuracy and productivity within the warehouse, notes Livesay. An AS/RS can be sized for heights up to 150 feet or as low as 20 feet, whether a processor is looking to retrofit an existing building or build a tall rack supported building to fit your current property.
Livesay outlines two types of order picking systems:
Layer picking—A pallet is automatically brought down and conveyed into a layer picking area where a gantry robot will pick a layer off the pallet and build a mixed pallet with different layers of product.
Case picking—Individual cases are stored in a mini-load AS/RS or multi-shuttle where individual cases are picked and conveyed to a palletizer.
Keep in mind, says Livesay, the closer you get to individual piece picking, the automation costs go up exponentially.
Automated guided vehicles (AGVs) are more often being accepted and used in warehouses and distribution centers. There are basically two types of AGVs. There are forklift models that can store and retrieve product on multiple levels, and there are pallet movers—where the product is either conveyed onto or off the AGV, or the pallet is placed onto a cart where the pallet is towed to the desired location, adds Livesay.
Updating automation tools
We used to think of outdated automation equipment as being 30 or more years old. That’s no longer true. Craig Cheevers, manager, automation engineering at Hixson Architecture & Engineering explains: “One area in which manufacturing plants continue to focus on is upgrades to existing automation systems. The impetus can be a failure of an existing installation or a new installation that requires integration into an existing one. The driver, though, is usually the same: outdated technology, both hardware and software, which can no longer be supported. And today, outdated can sometimes mean only 10 years for hardware and as short as five years for software. So, whether a plant is trying to prevent unwanted downtime resulting from unexpected failures, or plan for future growth, they must always factor in their existing automation systems.”
As industries quickly pivoted to catch up, automation trends emerged, including obsolescent upgrades, such as certain equipment and process upgrades and Windows-based operating system upgrades, says Burns & McDonnell’s Alfredo Valadez, project manager, Manufacturing Group. Businesses began to implement thin client technology—allowing users to access sensitive project information simply and safely by remotely connecting to a server-based computing environment—as well as realize the benefits of the virtualization of distributed human-machine interface applications. Safety programmable logic controllers, safety input/output (I/O) and hot swappable distributed I/Os became priority. “The challenge of how to seamlessly integrate new technology and execute projects, however, still exists, mainly as they relate to safety lockout/tagout, duration of projects and anticipated downtime,” says Valadez.
In many cases, thin client architecture has moved from local on-site servers—sometimes known as edge servers—to the cloud where operators have access from mobile devices. “Reliable, resilient Wi-Fi enabled network infrastructure that puts real-time data at the fingertips of employees on the plant floor can assist with visualization, alarm and event monitoring, downtime, and manufacturing KPI tracking, as well as asset management, change management and access control data,” says Dan McCreary, Dennis Group senior partner.
“Data access has become a requirement instead of an option,” says Cundiff. Access to data across building, utility and process systems is now viewed as a common practice for new or retrofit installations as well as gathering and reporting on a common platform. Increased access to data and reporting continues to support modernization or cost-saving projects with expectations for reduced yield loss and increased quality control.
Even newer, smarter technologies are learning the process. “Within this new world of business, industries started to witness real-world case studies of AI and machine learning in automation projects,” says Valadez. For example, a large parcel company now is using AI to help sort small parcels that were not able to be sorted automatically due to size and shape complexity. The system will continue to learn and improve uptime—and the more it runs, the more it learns and gets better at its task. AI helped the company reduce the physically demanding task from operators, and it is expected that there will be more of these applications this year as well as various solutions that address other difficult-to-automate tasks.
Looking for a reprint of this article?
From high-res PDFs to custom plaques, order your copy today!