SUSTAINABILITY
Develop a Plan of Attack to Save Energy
As energy becomes more expensive, formulate a plan to look at and meter all plant utilities—then take action to curb energy usage.

To save energy, conveyors shouldn’t be running unless they have something to convey. Photo courtesy of Imagemakers Inc.
Ancient always-on lighting systems, problematic steam traps, leaky air lines, compressors running full tilt, empty conveyors moving at full speed, improperly controlled CIP systems, excess water waste, excessive utility demand/power factor surcharges, inefficient boilers, scaling in heat exchangers…and the list can go on and on when you start thinking about ways you might save energy in your facility. And, savings in one utility is often coupled with another. For example, saving/reusing water may lower surcharges paid to the POTW (publicly owned treatment works). In some instances, pumping less water means saving energy in running pumps—or reusing wasted heat can lower HVAC costs. What’s not to like about saving energy and money?
Of course, a brand-new facility is designed to save energy. But not all food and beverage processors have the luxury of a brand-new facility that wins an FE Sustainable Plant of the Year, which MycoTechnology had CRB design and build—and complete in 2020. Located in Colorado where water comes at a premium, conserving it is important as Myco’s process consumes a lot of water. Energy efficiency is also a big part of the process, so special attention was paid in physical layout, keeping utility runs as short as possible and providing access for maintenance.[1]
Get a Strategy in Place
Fortunately, that’s not the end of the story. With older plants, there may be plenty of places to save energy—and maybe you’ve attacked a few—but coming up with a list or energy audit is a good place to start. And if you don’t have an “energy guru” on staff, why not contact a system integrator (SI) or engineering house with the expertise to take a look at your facility and come up with a strategy. Most will have well designed energy audit plans and strategies to get energy usage under control.
Energy conservation is a practical first step for organizations to reduce energy costs. Faith Technologies, a Control System Integrators Association (CSIA) member, has focused on LED lighting updates and process automation improvements, such as adding VFDs (variable frequency drives) to electric motor control applications and reducing energy consumption through control optimization techniques, says Matt Zabel, solution architect with Faith Technologies. “These conservation methods are one piece of our 4-step Path to Smarter Energy.”
This four-step plan includes:
- Energy use assessment via energy audits, energy conservation walks and permanent metering data.
- Energy conservation—based on data from metering or audits, for example, unnecessary equipment that is running and can be turned off—or rescheduling equipment based on usage algorithms.
- Energy generation—based on the data, what is the most cost-effective type of onsite energy generation to offset energy usage, depending on what a processor wants to achieve?
- Energy storage and independence—based on the data, design a system of energy storage so that a portion or all of a facility is highly resilient.
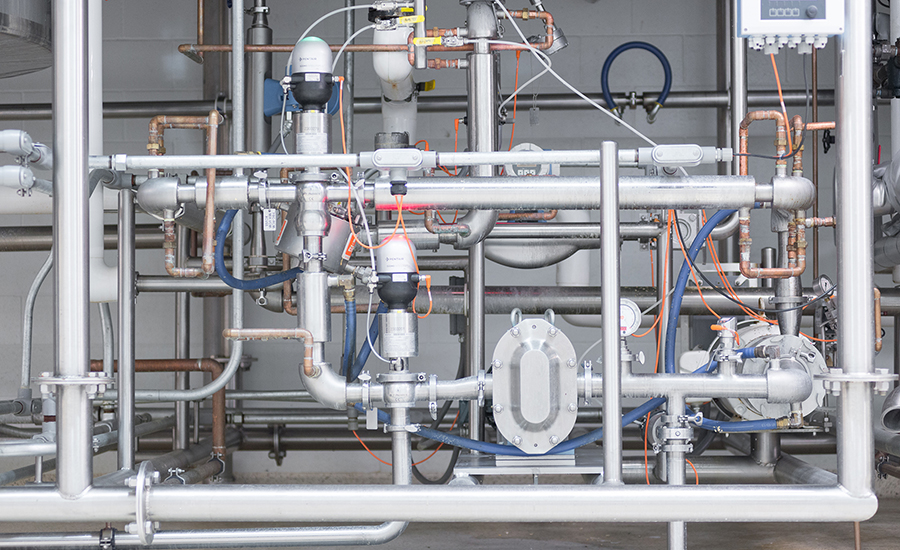
Do an Energy Audit
An architectural and engineering firm can perform a standalone energy audit of a particular system, a facility-wide evaluation or part of a design for an expansion or renovation, says Kevin Hansman, PE, LEED AP O&M, vice president and manager, plumbing systems and fire protection engineering, Hixson Architecture, Engineering & Process. Hixson begins with understanding a client’s goals for energy consumption reduction. “We often recommend a sustainability audit of client facilities: This can be beneficial for both old and newer facilities to help identify gaps between their current systems versus what their goals are for the facility,” says Hansman.
An energy audit should be undertaken by a qualified firm in close consultation with facility staff following the ASHRAE Energy Audit Standard, says Nick Ebbs, Stantec senior sustainability consultant, Stantec Carbon Impact Team. “A Level 1 audit could be appropriate for a focus on low-cost/no-cost operational improvements, while a Level 2 audit provides a more in-depth analysis of reduction opportunities. Ideally it should include the process controls, if only to understand the energy uses better. Reductions are often possible through simple changes that do not impact production.”
An energy audit and roll-out strategy should consist of several elements, says Mike Dieterich, CRB senior director of sustainability services. Here are some of the core areas to get started:
- Energy-efficient lighting: switching to LED lighting, motion sensors and timers
- HVAC optimization: upgrading systems, implementing smart controls and improving insulation
- Equipment upgrades: investing in energy-efficient machinery and appliances
- Waste heat recovery: capturing waste heat from industrial processes for other applications
- Variable frequency drives: installing VFDs on motors and pumps
- Energy management systems: implementing automated systems to monitor and control energy usage. This allows for continual monitoring and optimization of all systems
- Employee training and awareness: educating staff on energy-saving practices
Even without an energy monitoring system (or using it to inform the process), an energy audit and subsequent plan/roadmap are critical to not only identify opportunities for energy-savings, but also quantify and then measure the impact of implementing them, says David Ziskind, Stantec market lead, food & beverage. Energy recovery is also important to evaluate. Are you sending waste heat into the atmosphere when it could be used to heat the facility in the winter or even keep process equipment closer to temperature? Is appropriate pipe insulation in place? Can spot heating/cooling be used to address comfort concerns?
When you suspect a particular system needs a look at energy usage, often suppliers are a good start as they fully understand the resource needs of their own systems. Retorts are a good example, and they use a lot of energy and utilities. “We have for years now, and continue to, offer various types and levels of audits on retort systems to determine if there are opportunities to improve or optimize processes and/or operating efficiencies,” says Jeff Arthur, technical sales manager at ProMach/Allpax.
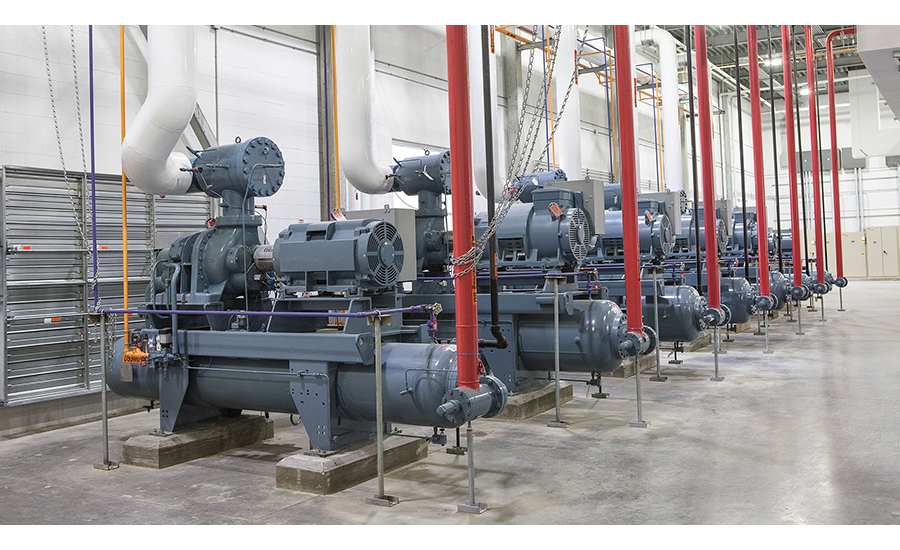
“We can help processors determine if the processes they have prescribed and/or that are being delivered by the retorts are optimized to achieve a good balance between conservatism for food safety, product quality and utility efficiency,” adds Arthur. “And it’s important to ensure that the instrumentation, valves and other control devices on the machinery are calibrated and functioning properly for delivering a safe and efficient process, thus maximizing operating efficiency.”
Retorts aren’t the only energy users that may need a little fine tuning to save energy. If you have an older CIP system where you program the run times based on the process that just completed, you could be wasting water, chemicals and the energy needed to heat them. The addition of optical and conductivity sensors to monitor water quality in the system can make a difference. “For example, placing ultraviolet (UV) sensors at the inlet and outlet of CIP lines, and monitoring soil load in real time can reduce CIP time by over 20%, saving energy,” says Ola Wesstrom, senior industry manager, food & beverage, Endress+Hauser USA.
Beyond CIP, Wesstrom asserts that steam is a major concern for saving energy. A failing steam trap or valve, or a technician’s error that removes an insulation section is all it takes for wet steam to form. Dry steam fraction is directly related to available energy. Wet steam is both a safety and efficiency concern.[2]
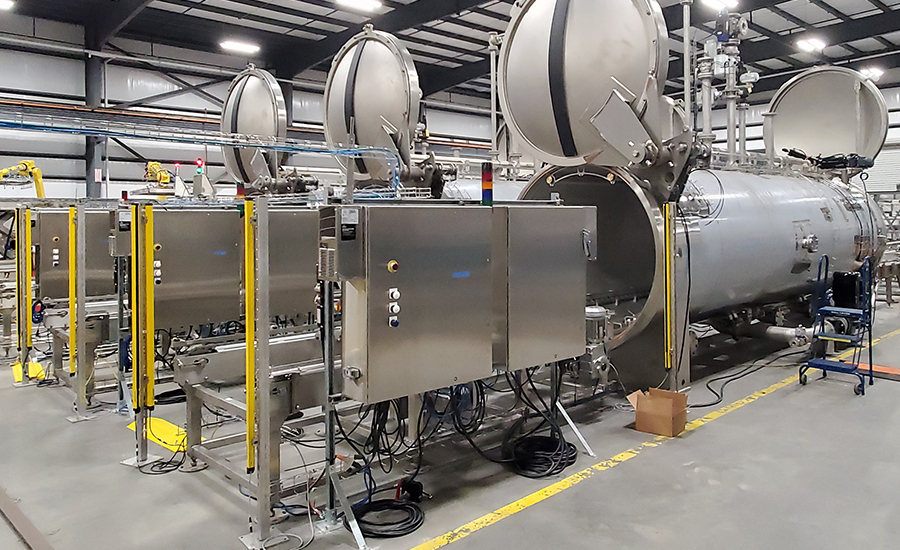
Low-hanging Fruit Not Completely Picked?
The “low-hanging fruit” we often think about are fixing those basic energy wasters noted in the first paragraph of this article. Everybody has remedied these, right? Well…not so much.
“While many facilities know what the low-hanging fruit is, we find that not a lot of them have taken those steps,” says Faith Technologies’ Zabel. “For some, obtaining capital for those efforts, even though they might be considered low-hanging fruit, can be difficult when budget dollars are competing with expansions, new equipment, etc.”
Oftentimes the “low-hanging fruit” opportunities have already been completed, says Hixson’s Hansman. “However, we routinely find additional opportunities to reduce energy consumption. Key things that anyone can do is identify the obvious areas of waste such as leaking steam or condensate or fixing compressed air leaks. Additional low-hanging fruit would include changing lighting fixtures to LED, installing motion sensors on lighting in less occupied areas, and conducting steam trap and compressed air audits.”
Not all processors have the capital to make lighting improvements, says CRB’s Dieterich. However, at the end of a piece of equipment’s life, like a motor, it is prudent to have a replacement plan to switch in a VFD motor. This approach maximizes the life of existing equipment and allows the company to upgrade slowly over time.
“A reluctance to make investments means that it can take longer to make an investment decision than the payback of the measure,” says Ebbs. “Lots of opportunities [exist] to further optimize process and process-adjacent equipment that facility staff are reluctant to adjust.”
“As it relates to retorting systems, in general there is probably still a lot of low-hanging fruit opportunities out there for processors to save energy,” says Allpax’s Arthur. These include optimizing thermal processes, adding or inspecting/repairing insulation on retorts and piping, ensuring all mechanical and electrical components are maintained well and working properly, automating equipment/operations and implementing the latest energy and water recovery systems.
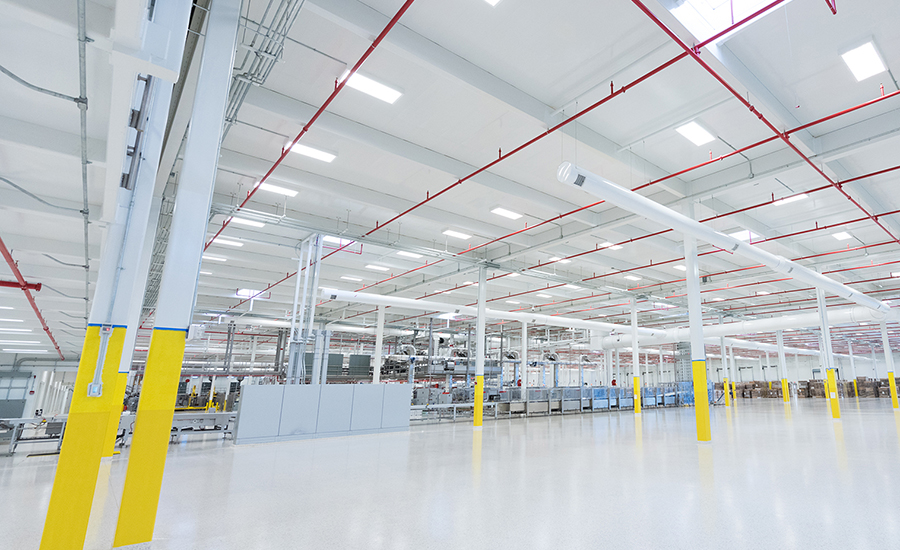
Monitor Energy Usage to Save Energy
“An energy monitoring/management system is a critical investment, as it will help enable tracking of all energy sources across the production site, identify inefficiencies within the manufacturing process, interpolate the data and correlate energy usage with production performance, validate energy savings projects, record and report on emissions, and meet regulatory requirements,” says Sinethemba Zulu, sustainability technology architect at Rockwell Automation.
It’s hard to improve what you don’t measure, so adding at least some level of data monitoring and trending hardware and software is always a good idea, says Allpax’s Arthur. Coming up with a well-thought-out plan about what and how you are going to measure is key to making sure you get the most out of the data.
Retort systems can use significant amounts of steam energy, compressed air, cooling water and electricity, so installing instrumentation that can help you understand what is being discretely consumed and what is being recovered (maybe on a per piece of equipment basis), can help identify things to focus on, improve or maybe repair, adds Arthur. And monitoring will provide data to help validate or justify changes that have been made.
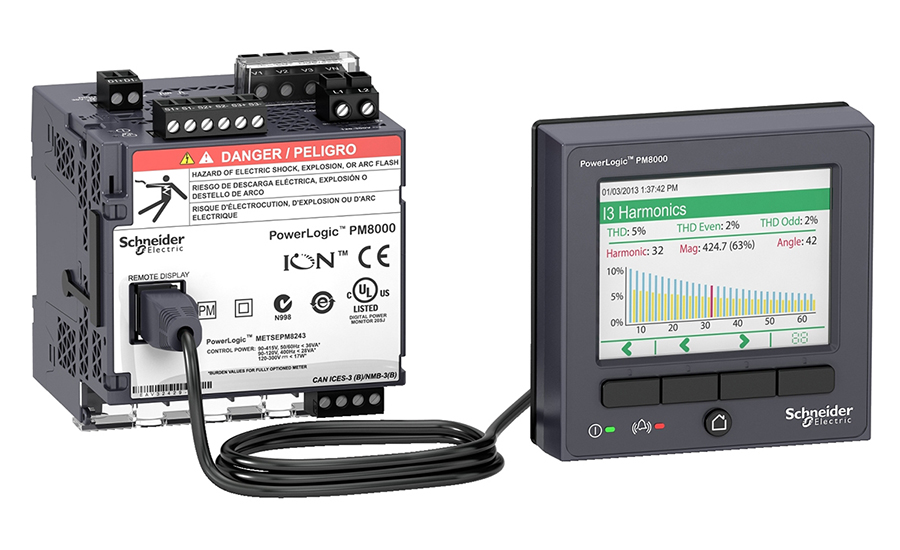
“I absolutely recommend monitoring energy from different parts of the plant to find hidden energy savings,” says CRB’s Dieterich. Metering and tracking your primary utility consumption and the highest energy users across the facility enable you to identify excess energy consumption and opportunities for improvement. “We often find that many of these improvements do not even require capital funds. This starts with installing metering devices to collect data and requires a data management system."
Local power monitoring devices connected to an energy management information system (EMIS) and integrated with the SCADA system is recommended, says Stantec’s Ebbs. Costs have become comparable with temporary metering.
Being able to know what you spend where for utilities like natural gas or electricity lets you narrow down heavy energy users in a facility. Hixson has seen an increased need to provide sub-metering for utilities such as natural gas, various water systems, compressed air, electricity, steam, wastewater, etc., says Hansman. This is done with local power monitoring devices and meters located on the utility’s distribution system throughout the plant. These are then tied back into a SCADA system or building automation system to monitor energy usage by process, production line, or by large individual energy users.
“At Faith Technologies, our typical recommendation for a food processing facility would be starting with monitoring switchboard mains with a power quality meter (like the Schneider Electric PM8244) and switchboard sub feeds with a multi-circuit energy meter (like the Schneider Electric HDPM6000R),” says Zabel. “Depending on natural gas, water or steam used in the process, we would recommend monitoring the main for the facility and potentially the main for each large production asset in the facility.”
Inserting thermal mass flowmeters is a straightforward way to get detailed information about air movement in compressed air lines or ducts, says Wesstrom. With continuous monitoring, leaks or idle machines can be addressed immediately. Vortex flowmeters used for natural gas and steam are now capable of measuring the amount and energy value, thus providing actual energy efficiency information.
Key areas of energy savings include being able to identify leaks in piping systems, understanding where VFDs should be installed on motors, discovering usage loads and duration to be able to negotiate energy, water and sewage rates with utility companies, and being able to reduce the operating pressure of gas systems, adds Hansman.
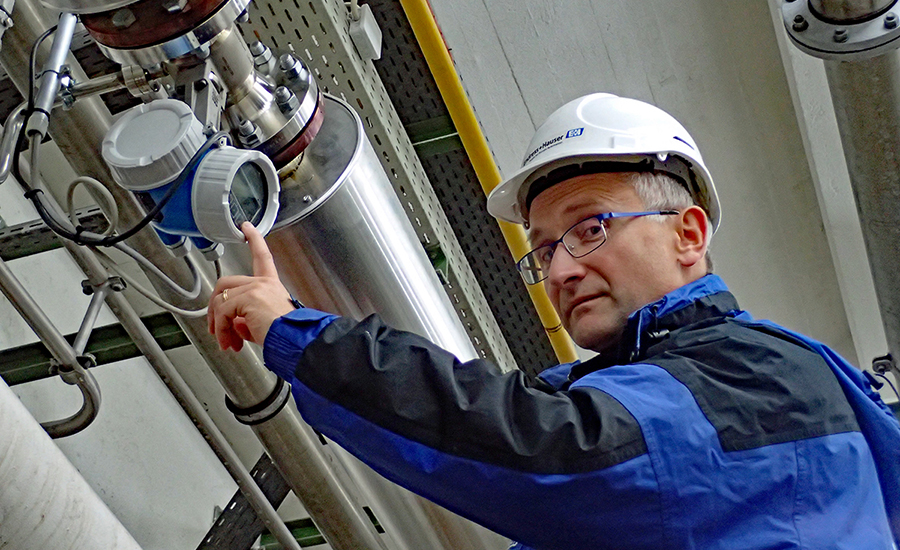
Stack Economizers on Boilers?
Many new food plants I’ve visited over the years employ boiler stack economizers to capture heat that would have otherwise gone up the chimney. But, does it make sense to retrofit existing boilers with stack recovery systems?
“Hixson recommends installing stack economizers on all new boiler installations,” says Hansman. “Retrofitting existing systems with stack economizers can be a very practical solution to reduce energy but you must take into consideration the age and condition of the existing system, as well as make sure there is space available for the retrofit.”
“Heat recovery is always a good option because the waste heat stream is free for the life of the measure,” says Stantec’s Ebbs. “However, any boiler retrofits should be coordinated with longer-term capital planning. You want to avoid investing in a boiler that is soon to be replaced or installing a brand-new gas boiler when the intent is to electrify in the near term, stranding the asset.”
“Other options to reduce energy in a boiler system include continuous blowdown, blowdown heat recovery units, O2 trim—and installing variable speed drives,” says Hansman. “If the age and condition of the system is unfavorable, it is worth considering the installation of more efficient heating options such as condensing boilers or direct contact water heaters with heating loops if steam is not required in the process.”
“Addressing heating needs through the lowest-grade heat possible is the best approach,” says CRB’s Dieterich. “These can include optimization of boiler operation, including reviewing pressure and temperature requirements and reducing load.” With technology evolving so rapidly in terms of smaller and more efficient, proper planning and a staged approach to boiler systems makes sense.
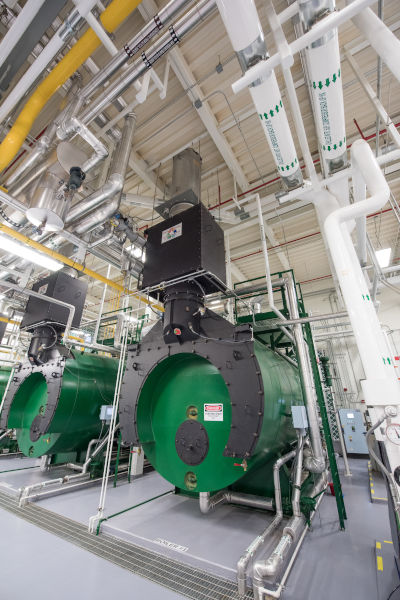
Other Areas of Energy Savings
“With a thoughtful strategy, chillers, cooling towers, compressed air and HVAC optimization can provide robust and cost-effective energy savings,” says CRB’s Dieterich. Metering these systems can help you prioritize projects based on your biggest users and waste points.
There is also a direct correlation between water savings and energy savings, he adds. “There is efficient HVAC equipment that will provide a plant’s complete heating and cooling needs without a cooling tower, significantly reducing water and HVAC costs. It’s a win-win.”
Retort systems use a lot of steam, water, air and electricity, says Arthur. “Most customers we interface with are keenly interested in water recovery systems in particular. Such systems can usually pay for themselves within a very short period of time. If the plant has a use for hot water, then steam recovery systems can potentially provide for short paybacks as well.”
“While many plants start with LED lights, which are good projects with great payback, we typically start by looking at the larger equipment in the facility such as compressors, HVAC, vacuum systems, large conveyance, fans and pumps,” says Zabel. “Electrically, we ask where the largest breakers are that feed equipment or lines.”
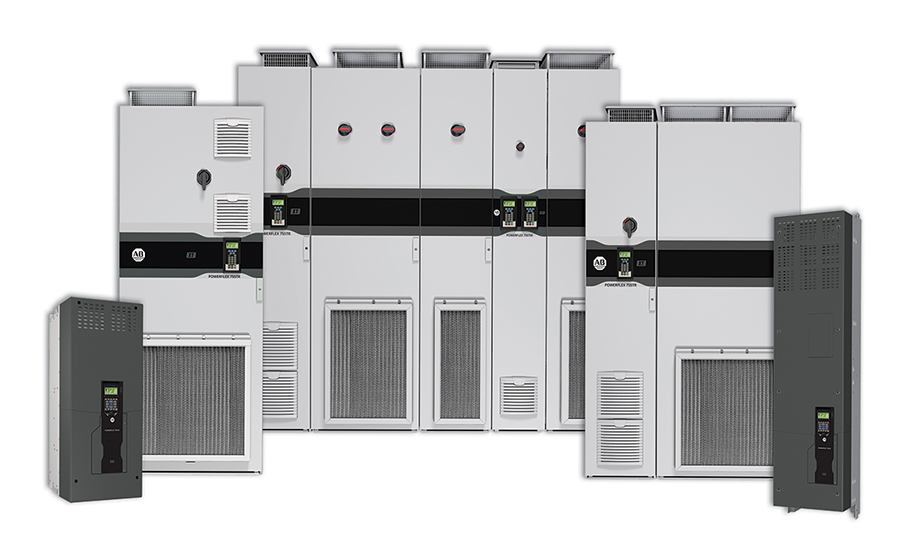
Taking a holistic approach is generally most effective and efficient in maximizing the impact of energy savings, says Stantec’s Ziskind. Reducing overall energy is a good first step, and the next step is reuse, which can include using waste heat or cooling to preheat/precool to bring the process closer to temperature will help reduce the overall energy consumption.
Finally, Ziskind provides some good advice: “Just replacing equipment without a clear energy-reduction plan can be capital intensive and may not yield the best return on investment, however if there is already a capital plan to replace the equipment, it would be prudent to evaluate all energy-savings options. Sometimes prioritizing small changes can provide momentum and excitement for future, larger changes.”
References:
[1] “Food Engineering’s 2020 Sustainable Plant of the Year: MycoTechnology commits to a sustainable culture,” FE, November 2020.
[2] “Steam: Minimize the Losses, Save Energy,” FE, March 2023
Looking for a reprint of this article?
From high-res PDFs to custom plaques, order your copy today!