Steam: Minimize the Losses, Save Energy
Steam is too valuable a commodity to lose

Whether you use steam as a food ingredient (culinary grade) or for cooking, with today’s natural gas and oil prices trending upward, conservation is not only important from a corporate sustainability viewpoint, but especially the bottom line. Today, think the three R’s—reduce, reuse and recycle—wherever possible. For example, reuse and recycle condensate? It’s already water, it’s treated—and it’s hot. Consider cost of production in terms of BTUs per pound of food produced or per barrel of beer. Where and what are the common losses of steam energy?
“Steam venting systems are the largest point of energy loss, but can be effectively managed with strategic solutions,” says Sam Simkowski, process engineer III at Stellar. A properly balanced steam system can help reduce energy losses and overall boiler emissions. To accomplish this, plants should try to minimize or eliminate the amount of steam released into the atmosphere. Rather than venting steam, plants can recover and recycle flash steam to support plant needs, such as heating water in processing areas. Incorporating heat exchangers or condensers enables facilities to use the flash steam’s energy, which can make a significant positive impact on overall costs. Another way to prevent losses due to venting is by incorporating a flash tank or cascading system in a high-pressure steam system. This method provides a source of low-pressure steam that can be used elsewhere within the plant, adds Simkowski.
The primary source of flash steam occurs when saturated condensate drops to a lower pressure, says Jonathan Clark, PE, mechanical engineer at CRB. When the steam condensate passes through the steam trap of the equipment that it is connected to, the resulting pressure drop across the steam trap will result in some flash steam generation. This is perfectly useful steam and in many cases is overlooked as a source of steam for equipment. If the operating conditions of the equipment allow, it can be recovered and used elsewhere if there are users that can accept the flash steam.
Key takeaway, says Clark, “Flash steam that is not recovered is both an energy loss and a water loss. For each pound of unrecovered flash steam, there is an associated pound of makeup water required. The engineer evaluating the steam system can determine the cost of these losses.”
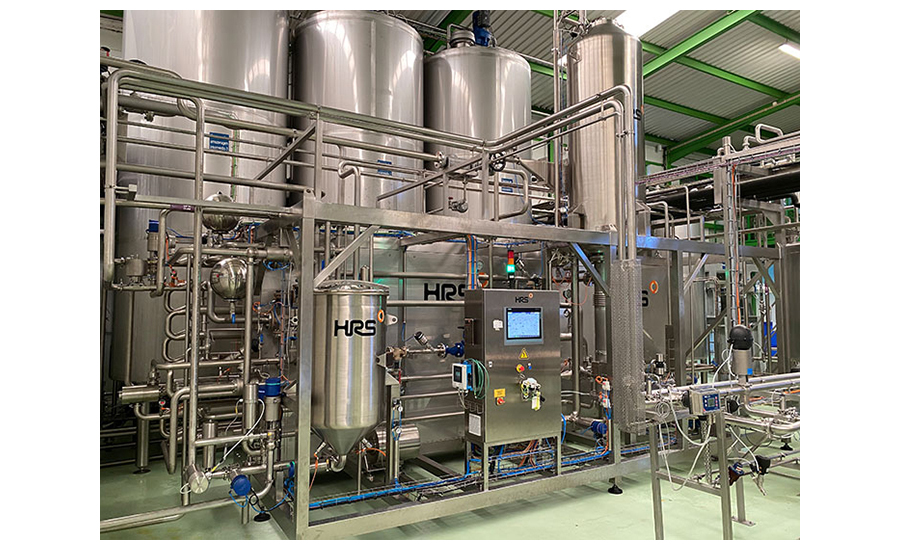
Designing Steam Systems
“The steam system designer should evaluate the available condensate streams for flash steam recovery,” adds Clark. A flash steam separator may be used between the higher and lower pressure condensate streams for recovery of useful steam to be used in low-pressure heating applications. The operational characteristics of the flash steam recovery and low-pressure user also need to be considered to ensure that there is a sufficient and consistent supply available.
Another method for flash steam recovery is to allow high-pressure condensate to flash to a lower pressure and be reused, says Dennis Group’s Gabriel Legorburu, PE, PhD, senior process engineer. This approach can be used when there are multiple steam pressures at a facility. For example, consider an application where high-pressure steam is used to heat fryer oil at 415°F. The condensate leaving the steam-to-oil heat exchanger could still be greater than 200 PSIG. Ideally, this high-pressure condensate would be flashed in a vessel with a back pressure regulator set at 200 PSIG or less. Then the lower pressure steam could then be used for equipment requiring less pressure than the fryers.
The mass and energy balance of the steam system should include all calculations of the steam system. These calculations are used to determine the operating costs of the steam system from an energy input analysis to generate steam. The calculations for flash steam recovery as part of the mass and energy balance are detailed in the publication by Spirax Sarco, “Design of Fluid Systems, Hook-Ups,” says Clark.
Hidden Energy Waster—The Steam Trap
Failed steam traps cause problems no matter the failure mode. When they fail open, they lose steam and—depending on the operation—can cost up to six figures in wasted energy—not to mention that failed-open traps affect pressure and efficiency. Closed failures can halt heat production and allow pressure to build to dangerous levels. Consider a steam trap survey by a qualified engineer to find out how much energy you may be wasting. (See sidebar, “Steam System Survey Can Reveal System Issues and Waste.”) Also think about installing monitors/sensors on steam traps, which detect failures and can alert operators via network or wireless communications when a failure is about to occur—or has occurred.
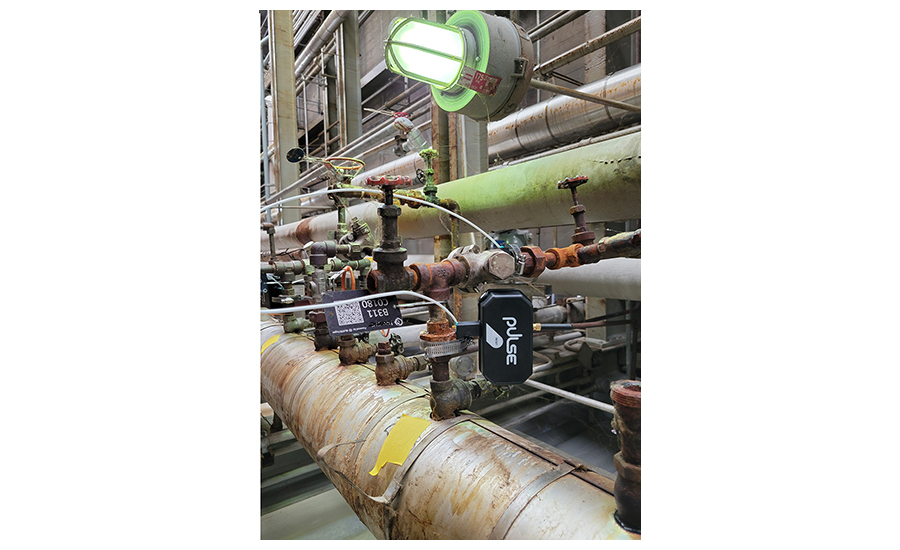
Steam traps in food plants are often in out-of-the-way places, for example above heads and in interstitial spaces or tucked away in inconspicuous places. Through a third-party auditing and installation company, Pulse Industrial, a provider of a software-as-a-service (SaaS) steam trap monitoring solution, installed its software and steam trap monitors for a large food processing plant with 193 steam traps, some of which were challenging to inspect for auditing purposes. In the installation process, the auditing company located and replaced a defective steam trap, savings tens of thousands of dollars in wasted energy per year. This food manufacturer had culinary steam, HVAC and heat exchanger applications in use.
After installing the monitors and the SaaS software, the food company is on its way to meeting its target for reducing energy waste and CO2 emissions. Using the audit company to install the monitoring equipment also allowed the processor to record the size, type and position of the traps so they are easy to locate when they fail. The food manufacturer no longer needs to send personnel to dangerous locations to inspect traps; instead, the wireless monitors keep operations and maintenance up to date on all steam traps in the facility, avoiding manual inspections and keeping workers safer.
A full steam survey of a facility should include an assessment of the following:
- Steam and steam condensate system P&IDs
- The steam system mass and energy balance
- Equipment sizing data from the manufacturer
- Physical inspection of the system
- Physical as-built comparison to the P&IDs
- Inspection for physical losses
- Operating setpoints of all equipment
- Chemical treatment
- Inspection for abnormal operation, damaged equipment, modified system set points, etc.
- Strainer and culinary filter maintenance records
- Boiler operation, maintenance and inspection records
A physical inspection of the steam and steam condensate systems should be a routine task for the facility maintenance personnel. An exterior visual inspection of the system and operation can show the following problems: leaking gaskets, leaking valve stem packing seals, stuck open traps, piping integrity, abnormal boiler operation, left-open drain points, chemical treatment deficiencies and incorrect system modifications.
The system engineering design review and visual inspection should also look at the application design, appropriate use of steam equipment and piping system design.
Typical loss points in steam and steam condensate include the following:
- Flash steam waste
- Incorrect operation or inefficient operation
- Improper boiler treatment
- Faulty traps and vents resulting in steam passthrough
- Improper condensate return system design
- “Once through steam” where condensate is sent to the drain instead of being returned
- Atmospheric leaks
Older food facilities that have been through a multitude of expansions, facility retrofits and line expansions can present unique challenges in system surveys. Sometimes the engineering design isn’t available for the overall system or is not current. It is a worthwhile effort to maintain the system mass and energy balance and system drawings to reflect the existing state of the facility.
— Jonathan Clark, PE, Mechanical Engineer, CRB
The Issue with Return Lines
Condensate return lines let you reuse the water you’ve already treated. But these lines can be problematic and may waste energy depending on their location and distance back to the boiler feed tank. In most plants today, these lines usually wind up in the interstitial space, which means condensate will have to be pumped upward and travel a long distance back to the feed tank.
“Running utilities in the interstitial space is a growing trend in new facility design, but it presents unique challenges in the overall design because condensate is generated at a lower elevation than the main condensate return line,” says Stellar’s Simkowski. “Process equipment on the process floor that generates a substantial amount of condensate creates opportunities to generate long-term cost savings and boost overall boiler efficiency. A pump is required to overcome the head associated with getting the condensate up into the interstitial space and connected to the main condensate return line.”
“Steam and steam condensate piping installed above the steam users can present challenges in returning the condensate from the users back to the header,” says CRB’s Clark. “A common misconception that can be observed in many plants is that a steam trap is all that is needed in a vertical riser return application. This is not correct. To lift steam condensate, either a dedicated pump trap to the equipment should be used, or if multiple users in an area are present where condensate can gravity drain to a common receiver, then a shared condensate return system may be installed in that area.”
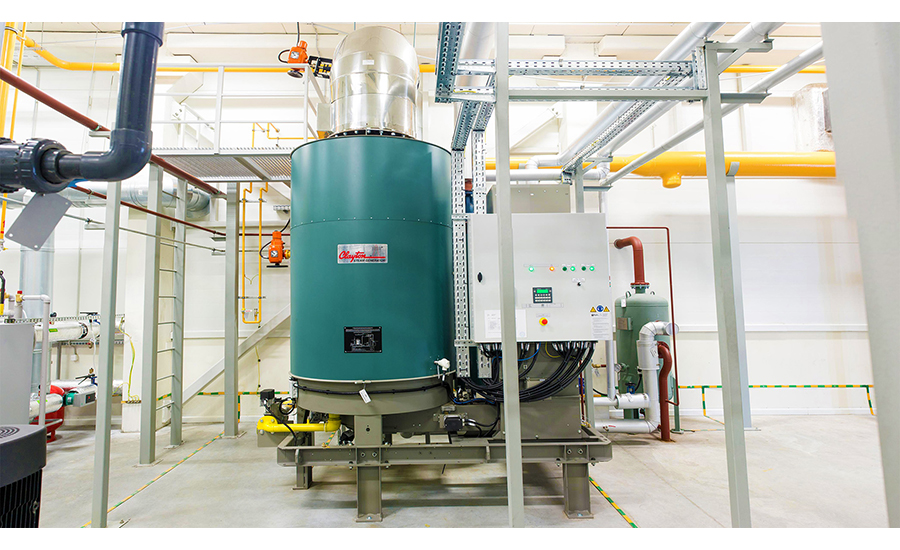
“Since main condensate return lines are typically sloped toward the boiler, gravity will take over,” adds Stellar’s Simkowski. When applicable, condensate from the same or similar equipment can often share a common condensate pump to optimize the design. Operating the system requires less energy with this solution. In addition, this approach helps minimize the amount of piping and equipment required and reduces installation costs, generating further savings.
“Shared condensate return system applications often require an open receiver when condensate at multiple temperatures is entering the receiver,” says Clark. Condensate in this scenario is often returned by use of electric return pumps or motive pressure powered pumps. Motive pressure powered pumps may use either steam or compressed air as the motive pressure to return the condensate. Electric centrifugal condensate return pumps have several limitations in their use in anything but low-pressure steam systems. The manufacturers of these pumps detail these limitations in their application bulletins, but the primary limitations are maximum temperature capability and cavitation potential. The type of condensate return pump used should be thoroughly evaluated to the condensate streams that will be entering the receiver.
Location of the boilers to steam users should be kept as close as reasonable to reduce overall system piping, adds Clark. Long piping runs require more drip traps in the mains which result in small flash steam losses. Motive condensate return pumps utilizing steam as the motive force should operate at the manufacturers recommended pressure above the pressurized return header pressure to minimize wasted steam. Avoid returning trapped condensate lines into pumped return headers which can lead to functional issues with the trap.
Boilers: Look at Efficiency, Determine Capacity
“Clayton recommends beginning efficiency studies with targeting the boiler itself,” says James Adgey, thermal sales, Clayton Industries. “An aging or poorly designed boiler suffering from efficiency loses is a prime suspect in any underperforming steam system, and heat loses from the boiler shell may also be contributing. While different companies may use different names, Clayton refers to this survey as a ‘Steam Load Profile,’ which will take the operational data from your facility and convert it into a simple summary of how well your boiler is performing and get an idea of areas of loss and potential improvement. Further consideration should be paid to heat exchangers, steam lines and steam traps for any potential heat loses, as they can also be responsible,” says Adgey. A review of the chemical logs and treatment would also be recommended to see if there are any potential scaling issues.
“Boiler blowdown is a necessary operational characteristic of any fired boiler,” says CRB’s Clark. Chemical treatment optimization and boiler maintenance have a direct impact on the frequency of boiler blowdown. Water treatment companies that specialize in boiler treatment can evaluate the water system for the optimal chemical treatment plan to reduce blowdown to the minimal possible while reducing boiler fouling.
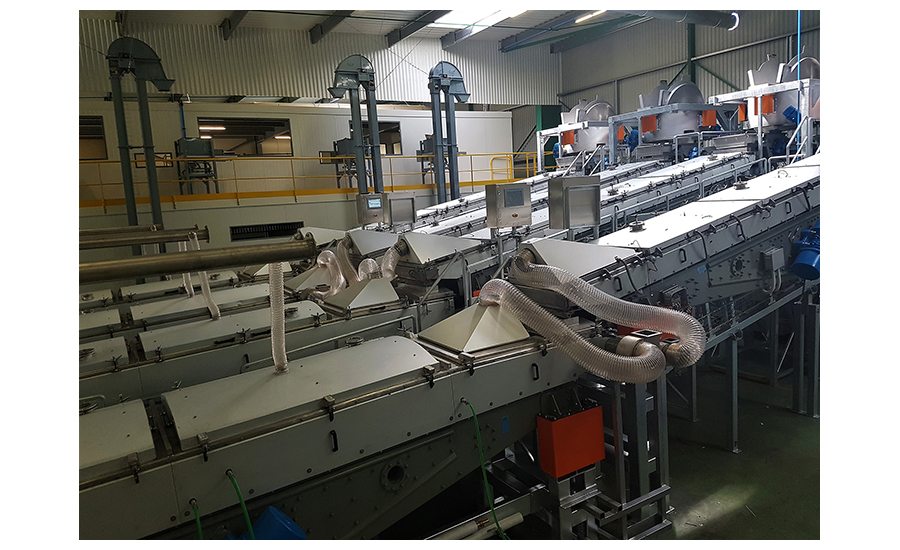
Steam Generator/Boiler Location and Culinary vs. Utility Steam
In general, placing steam generators closer to the point of application is a great idea in any facility, as a shorter run of pipe contributes to fewer loses and a cheaper installation, as well as the added benefit of a reduced wait to begin production by the simple fact that the steam has a shorter distance to travel, says Clayton’s Adgey. “Your installation may even be suited to placing small generators throughout your plant at the points of use, as opposed to keeping them all in a centralized location, but this would be circumstantial. “
“In any facility, the steam system must meet the requirement of 21CFR173.310 and 40CFR parts 141, 142 and 143 for direct injection into food for human consumption,” says Clark. If existing boilers or planned boilers do not meet these requirements, a capital assessment of retrofit of an existing system for food use or installation of a dedicated food-safe boiler for the application needs to be performed.
Hygienic, or clean, steam is typically produced either with an electric hygienic steam generator or a steam-to-steam heat exchanger if the operating characteristics of the system allow, adds Clark. In either scenario, a capital and operational cost assessment of both systems should be performed to aid in the decision of which type to use.
“With regard to a culinary facility, using utility steam in any situation where your steam doesn’t come into direct contact with your product is always a good option, given that utility steam does not require the same level of chemical treatment and filtration, and is therefore more cost effective to produce,” says Adgey. “However, depending on your facility’s size and level of production, it would have to be determined if it is worth the effort to produce two separate steam qualities or include a steam-to-steam generator.”
Electric or Fossil Fuel for Steam Boilers?
While natural gas remains the predominant choice for steam boilers and generators, electrically powered steam generators would seem to have several advantages over natural gas. For example, they have no release of CO2 or other gasses (zero carbon footprint), achieve nearly 100% conversion efficiency, require minimal maintenance because they have far fewer parts and associated equipment (e.g., air blowers) to service and would seemingly have less downtime.
In a Chromalox white paper entitled, “Experience a lower total cost of ownership with an electric steam generator,” the author compares the relative cost of ownership of a 10 -MBtu/hr (2,931 kW) boiler powered by electricity, natural gas and oil. While he did not state the electrical rate used for comparison, he did suggest that the cost of electricity would be twice that of comparable natural gas, but the total cost of ownership (TCO) would be less than half of that of a natural gas steam boiler—and given over a 20-year lifespan, the electric boiler would still have a TCO less than half of natural gas.
Of course, without comparing actual energy rates these TCOs could be a moving target in today’s energy markets. With natural gas and oil rates skyrocketing, the electric utilities are bound to pass along these costs. Though the author’s TCO comparison over 20 years is still less for electricity—what is the actual cost to run high-voltage service to the boiler location, especially if high voltage service is not available? Also, when the power goes off, the electric steam boiler is out of service.
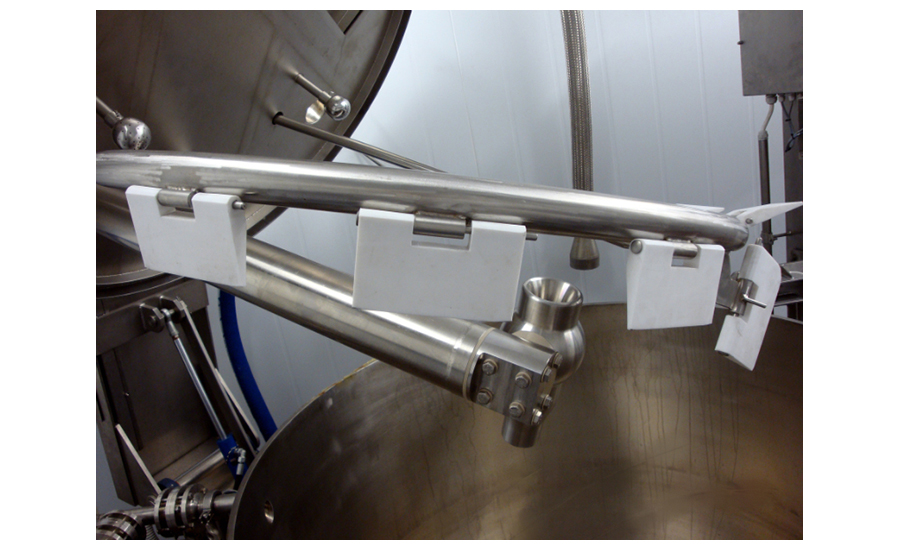
Steps to Minimize Loss
“Processors should evaluate their existing equipment to determine if it is being operated efficiently,” says Clark. “Verify that system setpoints haven’t been modified to account for poor maintenance practices or operational inefficiencies. Evaluate the long-term operational costs of reducing flash steam to the initial capital requirements of the added equipment. If a comparative analysis hasn’t been provided, request one to aid in the business case for capital improvements.”
Plants should incorporate a preventative or predictive maintenance program for their steam systems, says Stellar’s Simkowski. When the components of the system—traps, valves, condensers, heat exchangers and coils, to name few—are not working properly, the reliability and efficiency of the system is reduced.
In the case of a new installation, invest in high-efficiency equipment with a proven record of quality, says Adgey. While this will represent a higher initial cost, a system with even a slightly higher efficiency rating not only minimizes your losses, but can provide a return on investment many times higher than your installation cost, sometimes in the first year alone. To be sure of a product’s quality, ask your suppliers to provide a real-world breakdown of its efficiency and potential ROI, tailored to the needs of your plant. Don’t settle for a vague and idealized description, as your plant will be anything but.
“A final point to consider is insulation,” says Adgey. Steam pipes and heat exchangers can be problematic with regards to radiant heat loss, so keeping your lines insulated is always recommended, as well as checking regularity for areas that should be replaced.
Resources:
“What is LoRaWAN Specification,” LoRa Alliance, https://lora-alliance.org/about-lorawan
“Experience a lower total cost of ownership with an electric steam generator,” Mark Wheeler, director of systems & service, Chromalox Inc. (March 2, 2020).
“Moving dry food sterilization ahead full-steam,” FE, “Engineering R&D,” May 13, 2013
“Consider Cellular Wireless Networks for Today’s IIoT Systems,” FE, Sept. 28, 2022
Looking for a reprint of this article?
From high-res PDFs to custom plaques, order your copy today!