Saving energy: Steam generators and retorts
Steam generators are efficient by design, but today’s retorts have improved efficiency, thanks to intelligent controls and ancillary equipment

This retort steam recovery system is located near the retort room and keeps precious heat energy from literally going down the drain. Photo courtesy of Allpax
An article discussing both steam generators and retorts may seem a little odd, but the connection is one of saving energy and sustainability, especially when fuel prices are rising. First, a steam generator provides steam when you need it without keeping it in reserve as a large boiler does. Second, the retort—at least anything larger than a lab-sized or pilot device—is a voracious user of steam, and probably more often than not, will require a large conventional boiler, and maybe more boilers if the retort room is large enough, containing several retorts. But new technology has tamed the retort’s use of energy.
Makers of steam generators will tell you that when applied correctly, these boilers are quite efficient, even when operated at less than the full firing rate. Typically, steam generators use about one-third the floor space of conventional boilers, provide quick startup—in many cases going from cold to full steam in less than five minutes—and have reduced blowdown compared to a conventional boiler, often about one-tenth the amount required for a standard boiler, which saves fuel, water and chemicals.
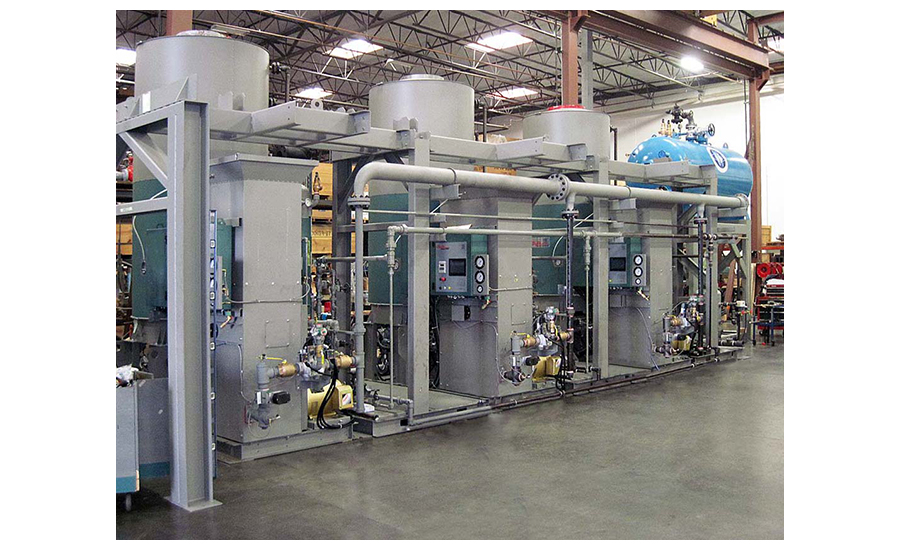
“Generally speaking, steam generators are not typically recommended for production retort applications,” says Jeff Arthur, Allpax technical director. The volume, variability of need and sustained pressures required are not conducive to steam generators, particularly when you consider the other steam demands involved in a food processing plant, which a steam supply system must be able to handle, like in the kitchen for heating product, or to create hot water for cleaning. A steam boiler is much more adaptable than a steam generator in terms of meeting both current and potential future needs of an industrial food processing facility, adds Arthur.
Steam generators are a potential option, however, for a pilot or lab retort application where steam demand (volume) is minimal and typically isolated to serving the pilot/lab retort only, says Arthur.
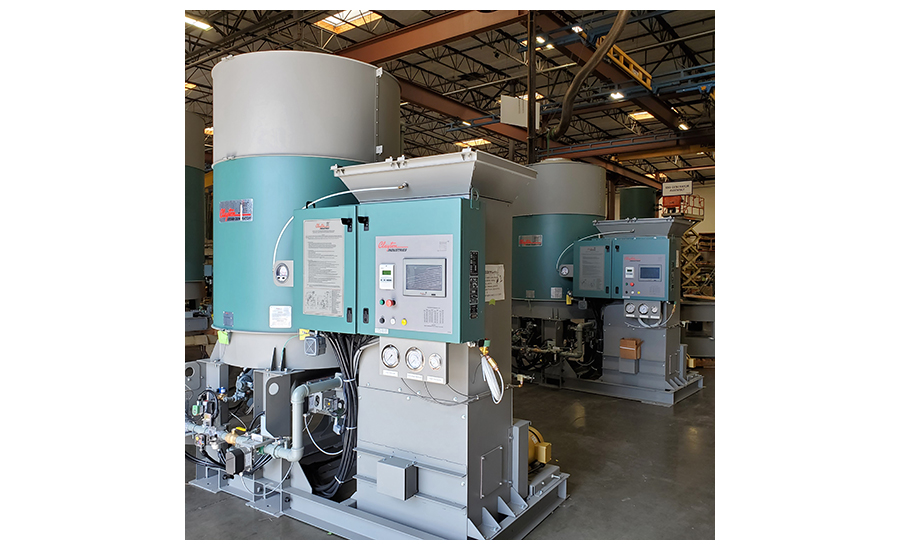
Consider applications carefully for steam generators
Keeping in mind that a steam generator provides steam on demand, we asked Venkat Venkatesh, senior project engineer at Clayton Steam Solutions, to describe the possibility of supplying steam to a retort and the conditions of operation.
“The primary criterion for the proper operation of the steam retort is having the required quantity and quality of steam supply under varying load conditions,” says Venkatesh. “A steam generator with low water content and regulated water supply is best suited to respond quickly to rapid changes in the steam requirement. Unlike a conventional boiler, the steam generator does not have fixed water level and can respond more quickly to fluctuating process demands.”
The sizing of a steam generator is subjective and depends on process conditions, adds Venkatesh. Typically, the steam capacity, the turndown and future steam requirements are taken into consideration when selecting a steam generator. The steam generator horsepower size would be comparable to that of a conventional boiler.
Capture and reuse saves energy, money in retort systems
An Allpax user installed a capture and reuse system in its large, multi-vessel retort room used for sterilizing canned foods. Plant operations estimated that the steam-capture-and-reuse system for its saturation steam retorts creates up to 70 gallons per minute of flash-concentrated180°F hot water during the come-up-vent-open cycle. Total duration time for capturing steam is 480 minutes er day.
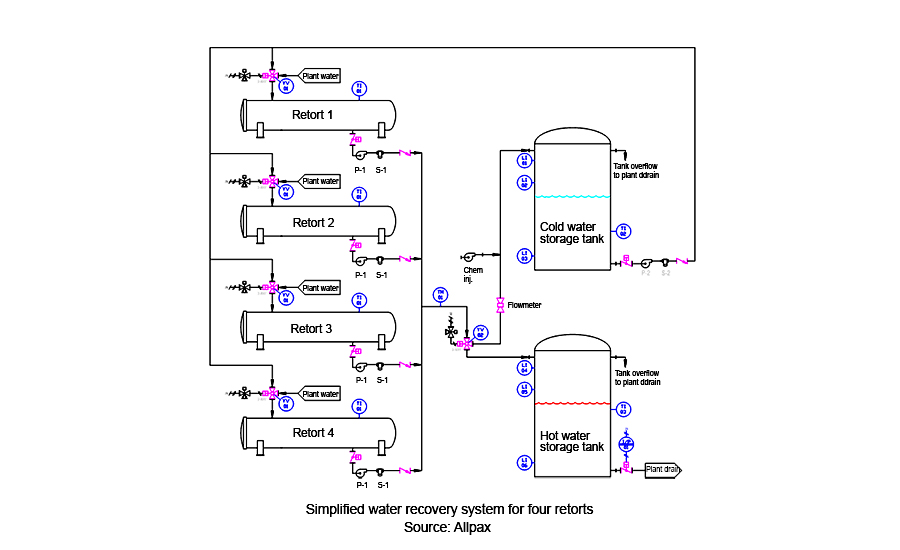
This means that the plant captures and reuses 33,600 gallons of 180°F water per day. Based on a U.S. average price of $6.23 per 1,000 cu.-ft. of natural gas (MCF), $.0638 per kilowatt-hour (kWH) and an average 57°F ambient temperature of water entering the plant, the daily savings of capture and reuse can be estimated to be about $632 (kWH) and $209 in MCF.
Unlike a conventional boiler, the steam generator does not have a reservoir of hot water in the drum. Therefore, the efficiency of the steam generator is unaffected at partial loads. In fact, the efficiency is higher at partial loads since the area of the heat exchanger is constant and the flow of fuel, air and water is regulated to suit partial load conditions, Venkatesh says.
Site-specific conditions need to be carefully analyzed before making purchasing decisions. The steam demands of various process conditions should be considered in selecting the capacity of a steam generator. Typical CIP loads are smaller than retort maximum demands, so no additional steam capacity would be expected—as long as CIP and retorts aren’t operating at the same time.
Choosing steam equipment needs to consider not only maximum load conditions but varying loads. “The steam systems must be suitable for fluctuating load conditions and must be capable of responding quickly to the process demands,” says Venkatesh. “Also, the steam system should maintain the steam quality. The system must maintain efficiency under all load conditions, especially under part load conditions.”
Retorts and saving energy
Most modern retort vessels are insulated and clad to help reduce radiant heat loss, thus improving energy efficiency, says Allpax’s Arthur. These features and systems can result in significant energy savings compared to the old batch retort systems of the past.
"Unlike a conventional boiler, the steam generator does not have fixed water level and can respond more quickly to fluctuating process demands." —Venkat Venkatesh, senior project engineer, Clayton Steam Solutions
Today’s controls go a long way in saving energy. Most modern retorts have relatively sophisticated controls systems that completely automate the retort process cycle, thus eliminating human errors, risk and inefficiency that are typical of manual process control systems, says Arthur. Process instrumentation and control valves are used to closely monitor and control time, temperature, pressure, level, agitation speed (as needed) and other critical control factors to deliver a precise and efficient process that is both gentle on the package and meets the exacting needs of the product.
Most retorts do not have any kind of “CIP” system, and they must be cleaned manually. The frequency of cleaning can be greatly minimized by the proper use of water treatment chemicals, as needed. It is possible in some retorts (e.g.: water spray retorts) to set up a “cleaning recipe” and run such a process cycle in conjunction with an appropriate chemical injection system. Such capabilities must be well thought out to avoid chemicals that could damage materials used in the construction of the retorts and to discharge effluent safely.
Energy recovery systems (capture and reuse) coupled directly to the retorts, along with integrated controls, are the most significant way to save energy, but need to be matched to the retort system. Many suppliers will custom design and manufacture retort ancillary equipment to the specific needs of the retort system package that will deliver the optimal process results, depending on the package type/size and the type of process that is executed by the retort, thus ensuring the most efficient and effective process to minimize energy usage.
Retort boiler requirements
In most cases the processor provides the engineering, internally or externally, to specify the most appropriate type and size of boiler(s) needed to provide steam to the retorts and to satisfy other plant needs as well. But retort manufacturers, says Arthur, work with these resources, including the boiler system provider, to make sure they fully understand the pressure, flow durations and other steam characteristics (i.e.: quality), and the steam piping connection specs to the retorts that are required to feed steam properly and efficiently into the retort, or banks of retorts.
In addition, retort manufacturers will often coordinate with the boiler manufacturer—in conjunction with the processor’s infrastructure engineering team—to ensure an adequate steam supply to the retort(s) so they can deliver the most efficient process possible when called upon. The typical minimum required supply pressure to a retort is 90 psig, necessary to avoid long come-up times and/or inefficient venting of the retort. Maximum steam supply pressure is usually around 120 psig. Pressures above this can result in control valve issues, thus upstream pressure-reducing valves are typically employed to ensure consistent steam supply pressure to each retort, says Arthur.
Resources
“A steamy situation turns out better,” FE, Aug. 2005
“Cooking with steam and getting hot water in return,” FE, May 2016
Looking for a reprint of this article?
From high-res PDFs to custom plaques, order your copy today!