Vacuum Fundamentals: Utility Applications and Oil Sealed Technology
Defining the fundamentals of vacuum and discussing the utility applications of oil-sealed vacuum technology.

Image courtesy of Getty Images / fotojog
I can’t for the life of me recall the guy’s name, but I clearly remember my junior high science teacher standing in front of my 8th grade class proclaiming in chalk and a slow loud voice that “Vacuum doesn’t suck!” I never would’ve guessed that nearly 30 years later, I’d be giving regular seminars and classes teaching, at its core, this very same principle.
The word “vacuum” is a little mysterious. It conjures in the imagination starships’ doors getting ripped off and tossed like soda cans into the black void of space, astronauts gasping for one last breath before their bodies go cold.
In the realm of the industrial manufacturing world, however, the word “vacuum” is used as a bit of a misnomer for what really should be called “sub-atmospheric pressure.” Sadly, “Rogers Sub-Atmospheric Pressure Systems” just doesn’t have the same ring to our marketing department.
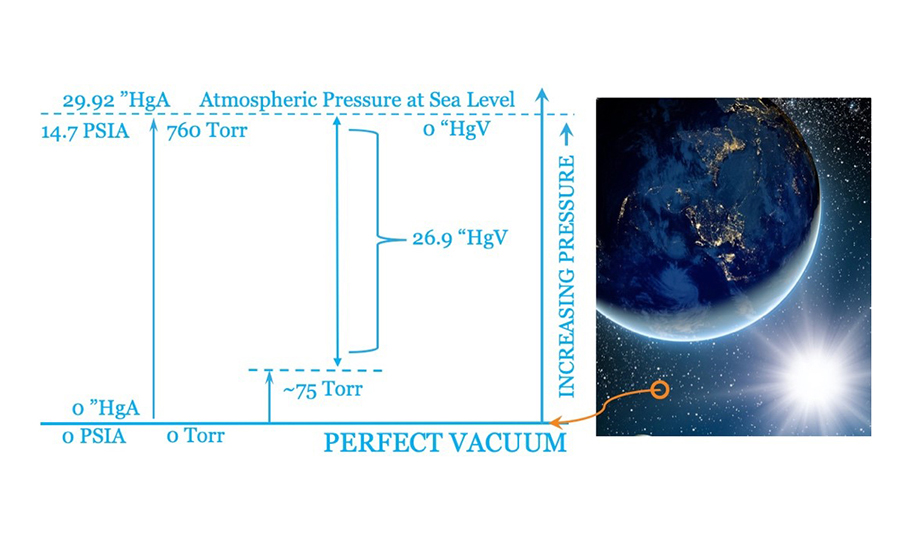
Throughout the last 20 years, I’ve heard countless production supervisors and maintenance personnel speak (ahem) loudly and emphatically into my safety-muffled ear, “I need more vacuum! Thirty inches. I need 30 inches!”
If you look up “vacuum” in a dictionary, you’ll get some sort of definition about a three-dimensional space being completely devoid of matter—as in zero solids, no liquid and absolutely no gas. If there is absolutely nothing there in that space, then there is no such thing as “more” vacuum. Unless, of course, you can figure out how to get something out of nothing in order to make nothing even less.
So, I nod in agreement and understanding to what they are asking for, not describing to them that what they need for that to happen is to move the entire facility to Death Valley or to somehow seal off every one of the building’s walls and doors from leakage to the outside world, then pressurize the inside of the building and never allow anyone to leave—at least not until the door on the CNC table is finished being routed by the robotic arm.
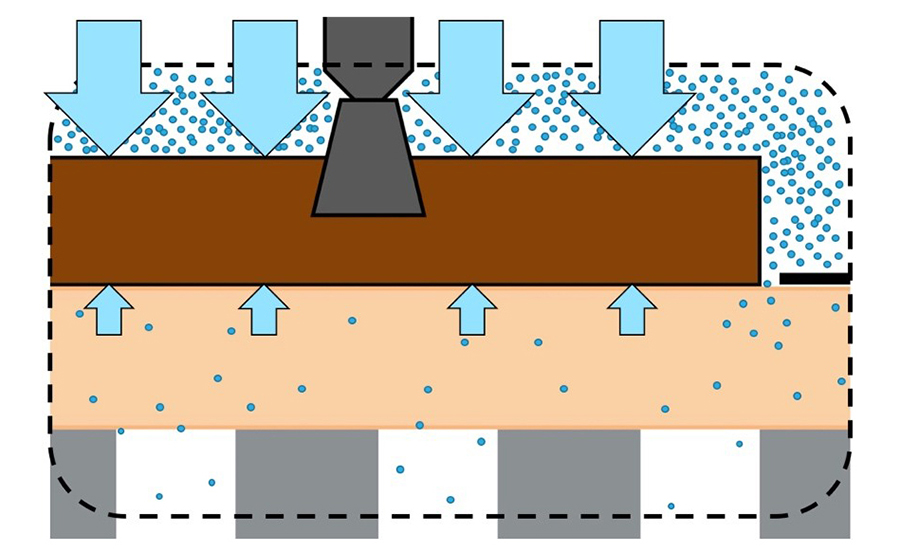
One must flip thinking upside down just a bit to fully comprehend what Mr. Whatshisname explained so long ago. There is only pressure. Or in the case of a “Perfect Vacuum,” the complete lack of pressure.
You mean the vacuum cleaner tube I’m holding in my hand isn’t actually sucking up my dog’s 15,823rd wad of dog hair from the living room floor? No. Instead, the higher-pressure atmospheric air in the room is rushing toward the low pressure sub-atmospheric space contained within the vacuum-cleaner’s filter housing, and that same mass of air is happening to grab the wad of fido’s fluff as it flies on by the tube’s entrance.
The scientific principle in play here is simple. Higher pressure always flows toward lower pressure. Truly, vacuum does not suck.
Types of Vacuum
In the manufacturing industry, “vacuum” applications can be broken down into two basic types: utility and process.
A process application is one where it is all about controlling the contents of a vessel. What is the gas makeup inside the vessel? How much of it is in there? All means to control a chemical and/or thermodynamic reaction so that ingredients A through J can change forms into a saleable product K. Because of these ingredients-based needs, process applications most commonly use a measurement scale of absolute pressure contained within the vessel.
An absolute pressure scale starts with zero (0) pressure measurement at “perfect” vacuum, meaning no molecules of gas contained within a given volume, and only increases as more and more gas is allowed to flow into that lower pressure space. PSIA, Torr and milliTorr, Bar and mBar, and Pascals are all examples of Absolute Pressure scales.
Utility applications, on the other hand, are all about utilizing the differential pressure between the inside of the vacuum system and the higher positive pressure of the atmosphere to perform a work-based-task in the physical world.
Measuring this differential pressure and the resulting vocabulary gyrations is where much of the confusion about “vacuum” starts. People get all sorts of creative with trying to describe how much suction they need, when truly there is no such thing as suction. Accordingly, these frustrating misconceptions, negative PSI or negative mBar creep into engineering specifications and control programs with extreme regularity when “negative pressure” isn’t a thing. It doesn’t exist.
What there is, instead, is pressure differential; and the scale of differential pressure measurement we most commonly use in vacuum applications is "Inches of Mercury, Vacuum,” annotated “HgV. This is a bit of an unfortunate name since its use is the root of the production supervisor’s perspective that he or she might need “more vacuum” in a similar way that he or she might want “more pressure” out of a compressed air system. This, along with an inch being a measurement of length, all helps to lead to additional confusion.
Alas, it is what we have. So, we’re gonna go with it.
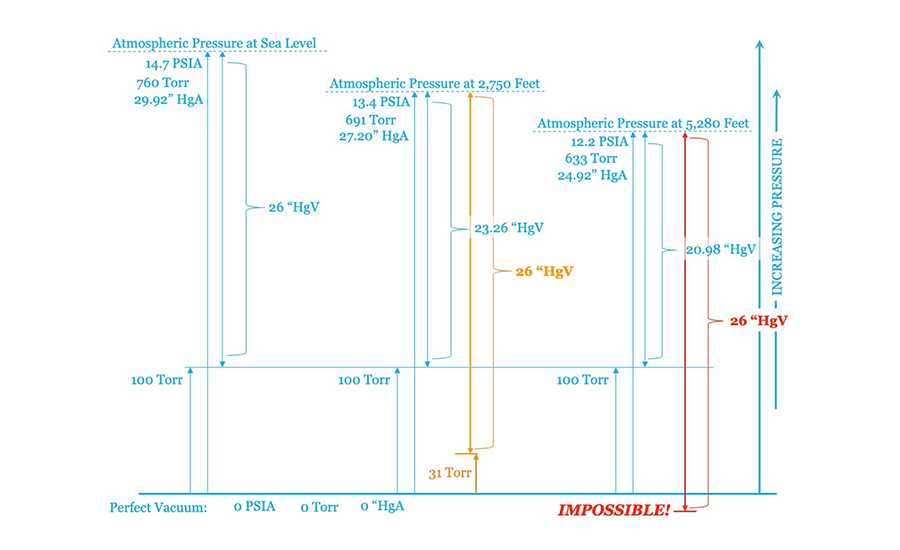
I’ll save the history and development of this scale, dynamics with the atmosphere and proper methods of conversion from one scale to another for another article. For now, it’s enough to understand that Zero Inches of Mercury, Vacuum (0 “HgV) equates to the inside of the vacuum system being at the same pressure as the outside world’s atmosphere; meaning a zero (0) pressure differential exists at whatever tool or table it is in the manufacturing center that requires vacuum. With zero pressure differential at 0 “HgV, this would also be known as, it won’t work.
At the opposite end of this scale and at a location which exists only at a sea level elevation on the planet earth on a normal weather day, the maximum theoretical pressure differential achievable equates to what we humans have defined as 29.92 “HgV. If we were somehow able to achieve such a thing as perfect vacuum, with a complete absence of all matter inside a given volume, then 29.92 “HgV would correlate directly to measuring the difference in pressure inside that vessel versus the sea level atmosphere outside of it.
There are a few distinct ranges in increasing depth of vacuum from 0 “HgV differential up to 29+ “HgV.
Light Utility Vacuum Applications
Utility applications requiring “light” vacuum are often defined as having pressure differential of less than around 10 or 12 “HgV. These applications commonly involve utilizing atmospheric air as a means to motivate or fluidize some sort of particulate into the air stream to move said particulate from point A to point B. When performed at sub-atmospheric pressures, this is referred to as vacuum conveying; in contrast to pneumatic conveying systems which operate slightly above atmospheric pressure.
Many of these kinds of applications require very light vacuum, perhaps only a few inches of mercury vacuum or less. The depth of vacuum required is related to the particulate being conveyed: The larger, heavier, smoother and denser the particle is, the more likely you’ll need a higher differential pressure, aka “deeper vacuum,” to reliably convey it.
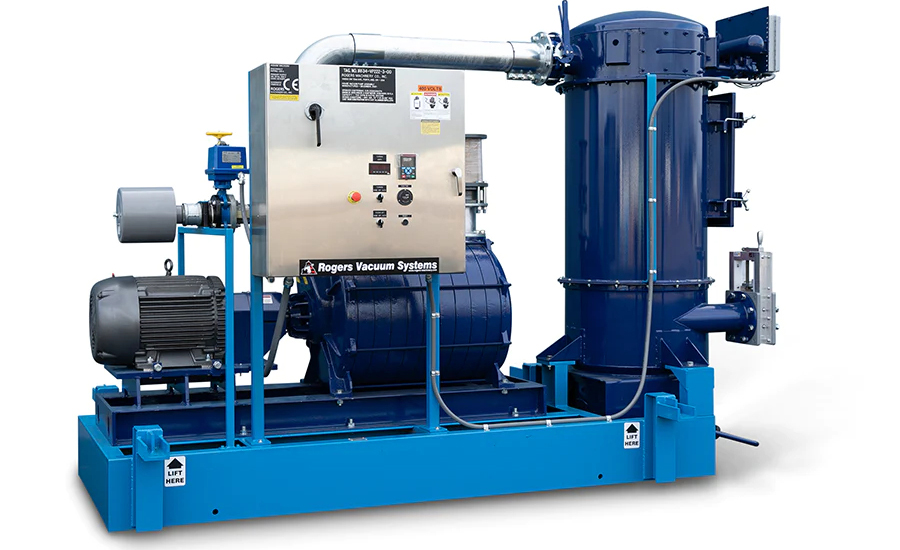
Because these light vacuum applications are often more about moving large volumes of air through the system, and because the air in the system is not terribly rarified, the kinds of compression elements utilized differ from applications which require higher pressure differential.
Light vacuum applications are commonly served by fans, regenerative and rotary lobe exhausters, and multistage turbines. These are all inherently “oil-free” technologies since the compression element is running at a low enough pressure differential which does not require the seal the oil provides on the internal surfaces of a compression element with higher differential pressure capabilities. This is a good thing, since the light vacuum also means a much higher mass flow rate of air through the vacuum system, which would run counter to the ability for an oil separation system to effectively function.
Roughing Utility Vacuum Applications
Proceeding “deeper in vacuum” with our utility vacuum applications, we reach the “roughing vacuum” realm of a half an atmosphere, or ~15 “HgV, up to a differential pressure measurement of around say 28 or 29 “HgV. The increase in differential pressure required by these applications coincides with the change in vocabulary of the compression element itself, now using the phrase vacuum pump, in lieu of vacuum exhauster.
Above 15 “HgV but below 20 “HgV, we have a handful of common applications, most notably among which is the medical field. Hospitals and other industry will use vacuum to “dense phase” convey liquids through vacuum tubes for centralized collection and disposal. Because there is the potential for bulk liquid and condensable vapors to be entrained in the air stream as it propagates toward the vacuum pump, these kinds of systems are often applied using oil-free technology as well, since we don’t want to mix water with the lubricating and sealing oil inside the vacuum pump. With proper bulk liquid separation and filtration ahead of the vacuum pump inlet, however, oil sealed technologies can be successfully applied in these kinds of utility applications.
Oil-Sealed Utility Vacuum Applications
Progressing to yet higher-pressure differentials of 20+ “HgV, we begin to see a plethora of utility applications common to application of the large and healthy “vacuum pumping” industry.
Vacuum hold-down is commonly applied at a roughing vacuum level of 20 to 26 “HgV. Imagine a part being held in place on a flat or contoured surface by the force of atmospheric air pushing down on it. This is only possible if the underside of the table on which the part lies is held at a lower sub-atmospheric pressure. A router bit or a laser or any number of other cutting devices may then carve away large or microscopic chunks of material from the rigidly held part.

Once complete, vacuum is broken and atmospheric air rushes into the underside of the table, allowing the part to be easily moved away to the next part of the process. The larger and heavier the part, the more likely that a lower level of pressure differential from atmospheric is required. If the part is lighter and more delicate, it’s likely a deeper vacuum will be required to successfully hold the part in place during cutting.
Vacuum-bagging of fiberglass is a utility application where a part is assembled in a mold. A flexible bag is sealed to the edges of the part and air is evacuated from the bag so that the atmospheric air presses the part firmly into the mold while also allowing the resin to disperse throughout the fibers evenly while curing occurs.
A utility application called “vacuum chucking” is very similar to vacuum hold down, except in this case it is now a small suction cup or some other sealing surface which is attached to the part and the part can be lifted, rotated and manipulated in space until which time vacuum is broken, and the part becomes instantly detached from the chucking head. These applications often require 24 to 29 ”HgV, since the size of the sealing surface is likely small and a greater differential pressure is required to lift a part against the force of gravity.
Utility Vacuum Applications with Process Gasses
There are, what could be considered, some cross-over applications as well. In the electronics industry, wafers undergo etching by solvent to be turned into microchips. Wafer size increases yield a higher number of chips per wafer but also must be manipulated in the vacuum chucking method described above. With increased wafer size comes increased wafer weight, which in turn requires increased pressure differential, aka deeper vacuum, at the tool head.
Additionally, while much of the gas stream in these applications is air, the gas stream propagating toward the vacuum pump inlet is also subject to the etching solvents and chemistry required by the wafer. It is for this reason that these kinds of systems are widely referred to as “Process Vacuum Systems” even though the primary use is utilitarian in nature. It is well understood, in this case, that the gas stream contains process gasses which should not be mixed with oil-sealed vacuum pumping technology.
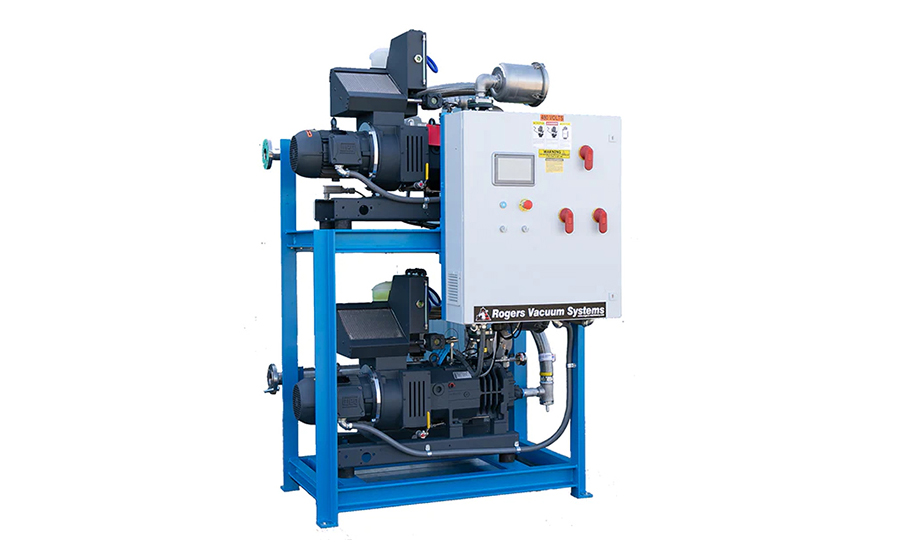
Similarly, many a university laboratory require removal of air, and namely oxygen, from the contents of a beaker or test tube. While technically, this is a process application controlling the contents of a container where chemistry could be involved, these lab systems are very commonly applied with utility vacuum hardware since the level of experimentation being performed in these settings does not require an ultra-conditioned environment to yield the proper result.
For most all utility applications, the motive gas is by far predominantly atmospheric air. Because this is the case, we can very commonly select oil-sealed technologies for utility applications, particularly when that application requires 20 “HgV, or more, pressure differential from atmosphere.
The Engineered System Solutions team at Rogers can help you identify the best suited vacuum technology, system packaging and integrated controls solution, engineered for your specific utility application. Drop a line and we’ll be more than happy to explain exactly why our Rogers Vacuum Systems (RVS) do not suck.
Looking for a reprint of this article?
From high-res PDFs to custom plaques, order your copy today!