Chilling/Freezing
Upgrade Chilling Equipment to Industrial Heat Pumps
Industrial heat pumps provide chilling and freezing, and reclaim the heat energy lost in chilling to save money on heating water for cooking and cleaning—but is retrofitting possible?

Two heat pumps installed by GEA at a food processing facility move heat from cold rooms to equipment needing hot water. Image courtesy of GEA Systems North America LLC
What’s wrong with this picture? You spend money to purchase natural gas to run your boiler(s) to create steam and hot water to cook, par-boil or pasteurize your product—then you use more energy to chill and freeze your product. Yet, the heat removed from your product most likely exits the plant. Maybe it’s time to think of your refrigeration plant with its compressors as a heat source, a “heat pump.” After all, it removes the heat from your product—but why throw the heat away when you could be reusing or channeling it to cook product or clean the facility? While a heat pump won’t necessarily replace your boiler, it will take some of the load off of it—and save energy in the process. This makes your operation more “green,” which is how you want your customers to think of your product(s) and company.
But should you consider a retrofit for your existing facility or wait until you move to a new greenfield site? The solution needs to be considered and assessed based on the individual case, says Joseph Miller, sales director, industrial refrigeration for Danfoss Climate Solutions. “Certainly, if the existing plant has a refrigeration system, the likelihood of wasting the precious heat is latent, and an evaluation on how to reclaim and boost the required heat source is worth doing. The efficiency (coefficient of performance, or COP) of heat pumps is significantly higher than boiler-based equipment, making them ideal for decarbonization, with a relatively short payback period.”
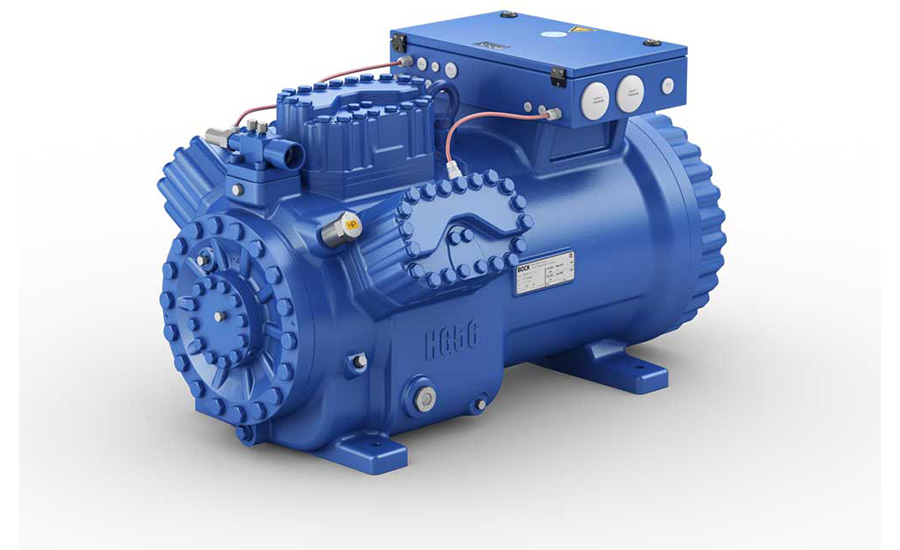
“For processors seeking to lower their carbon footprints, heat pump retrofits absolutely make sense—particularly as effective and sustainable alternatives to traditional fossil fuel-powered boilers,” says Grant Kovac, director of product management at Vilter Industrial Solutions for Copeland. Even if a plant operator may not be able to completely decommission their existing boiler, they could potentially leverage a heat pump in a “base-loading” scenario—i.e., using the boiler only when needed during high peak loads to significantly lower its overall base load, adds Kovac.
“Yes to retrofitting!” answers German Robledo, GEA North America heat pump sales manager, who has actually seen more retrofits than new installations. But, according to Robledo, management needs to be committed to decarbonization and understand what CAPEX demands will be required. Adopting this technology will mean thinking outside the box, and a processor shouldn’t look at heat pumps in the same way as a boiler, refrigeration compressor or an air compressor as the path is different. Decarbonizing is an approach that can take up to seven years to see a ROI—not that it can’t happen sooner, says Robledo. One reason that an ROI will be longer is a retrofit often includes re-piping, new valves, heat exchangers and tanks. Boilers will need to be retained if steam is needed for cooking processes.
It’s important to consider for both options—new and retrofit—the specific needs of the site, budget and timeline of the project, says Tania Herrera, Güntner US LLC key account and product engineer. For existing facilities, retrofitting with heat pumps can offer efficiency improvements and cost savings, though it may require careful planning to overcome compatibility and space issues. For new facilities, designing with heat pumps from the outset allows for optimal integration and efficiency. Heat pumps can be more energy efficient than boilers, especially in moderate to high ambient temperatures. However, it’s important to review every case on its own.
A Special Note on Refrigerants
Refrigerants are typically grouped into natural refrigerants (e.g., water, ammonia, CO2 and hydrocarbons such as butane and propane) and synthetic, which includes hydrofluorocarbons (HFCs)—and alternative synthetics such as hydrofluoroolefins (HFOs) and hydrochlorofluoroolefins (HCFOs). HFCs are being phased out in the U.S. by the EPA as these gases have been known to deplete the Earth’s ozone layer. While HFOs were developed as an alternative to HFCs, HFOs are also considered fluorinated greenhouse gases (F-gases). HCFOs are also an F-gas with the same issues as HFOs, and both are said to have trifluoroacetic acid (TFA) formulation risks. HFOs/HCFOs have become increasingly popular because of their high COP, but because of their breakdown into TFA, they have raised environmental and health concerns by various groups, though neither the U.S. EPA nor the United Nations Environment Program (UNEP) suggest there is a problem.1
A recent report, entitled “The Rising Threat of HFOs and TFA to Health and the Environment,” states that the refrigerant HFO-1234yf is considered a PFAS “forever chemical” by the Organization for Economic Co-operation and Development (OECD). Fugitive emissions from the refrigerant are said to produce an atmospheric degradation product, TFA, that is also a PFAS. TFA descends to the earth in rainfall across a wide geographic area, accumulating in waterways that supply drinking water. While some action in the U.S. by the EPA and FDA has been taken to eliminate PFAS from the environment, EPA’s definition excluded many HFC and HFO refrigerants as well as TFA. More work still remains to be done to verify if TFA toxicity levels in the U.S. are a problem.2
[1] “Consistent Refrigerant Policy Is Essential for Investment in Industrial Heat Pump Market Transformation,” ACEEE, January 2024 (Downloadable as a PDF from ACEEE)
[2] “The Rising Threat of HFOs and TFA to Health and the Environment,” ATMOsphere, October 2022. (Downloadable from ATMOsphere)
According to Nick Ertel, P.E., manager of refrigeration engineering for Gray, when deciding between retrofitting a heat pump at an existing brownfield site or installing a new system in a facility, several factors should be considered to access the return on investment (ROI):
Retrofit considerations: Retrofitting a heat pump can be cost-effective if the existing infrastructure is sound. It allows for incremental improvements, minimizing downtime and disruption. However, challenges may include space constraints, system compatibility issues and the need to update ancillary equipment.
New facility design: Designing a new system from the ground up allows for optimal integration, tailored to specific operational needs, energy efficiency goals and future scalability. This approach can incorporate the latest technologies, ensuring the facility meets modern food processing demands. Cost implications of new facility design and construction, along with potential land acquisition, also play pivotal roles in the decision.
Design considerations: Key steps in designing heat pump systems include assessing heating and cooling requirements, planning integration with existing systems, evaluating load profiles between heating and cooling needs, optimizing energy efficiency, ensuring safety and compliance and planning for scalability.
Applications benefiting from heat pumps: Heat pumps are beneficial in food and beverage applications like dairy processing, meat and poultry processing and breweries, where they recover and reuse energy for simultaneous heating and cooling. Not all applications allow for full energy recovery due to heating and cooling demand, system resiliency requirements and space allocations.
Boiler elimination: Heat pumps can reduce or sometimes eliminate the need for traditional boilers with certain considerations, but they will often lead to lowering energy consumption, greenhouse gas (GHG) emissions, and operating costs when properly designed.
“The choice between retrofitting and building new depends on specific circumstances. Retrofitting may be cost-effective, but a new design offers greater flexibility, efficiency and growth potential,” says Ertel. “Integrating heat pumps can lead to significant energy savings and improved operational efficiency.”
In terms of efficiency, three compressor types are used in heat pumps—piston, screw and centrifugal—and by nature, piston-type compressors typically have the highest COP, says Robledo. Piston-type heat pumps coupled with ammonia will deliver highest possible COP compared to any other type of compressor and refrigerant.
Screw-type compressors always have a lower COP compared to piston-based machines—due to their physics—but they cover large range capacities where piston-based devices are limited, adds Robledo. For a large-capacity plant, processors may need a greater number of piston units versus screw-type compressors, but can opt to go with screw-based machines to reduce the number of units and probably CAPEX as well—but will sacrifice COP.
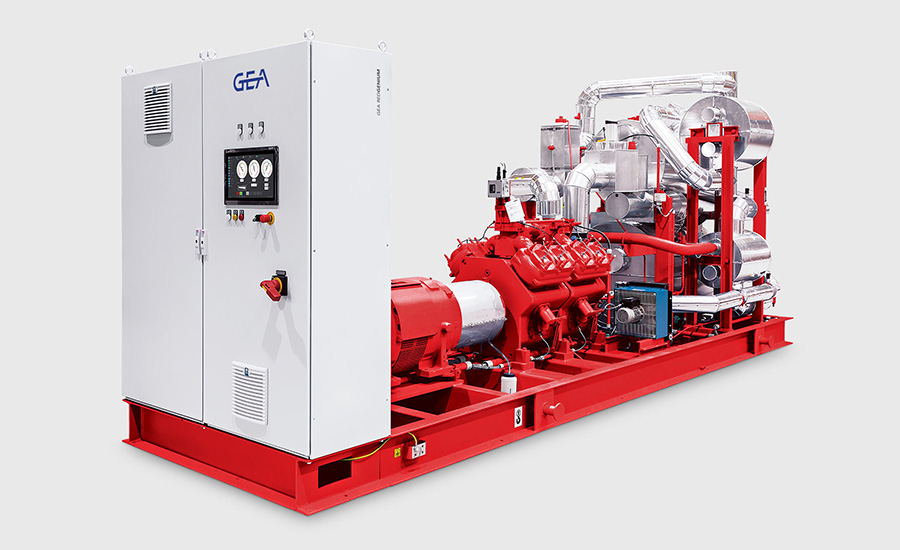
Processors will need to ask the experts on the type of refrigerant and compressors to be used. While ammonia is the most often used in food facilities, special needs may require other combinations of machines and refrigerants.
Integration of Heating and Cooling Systems
Integration is the operative word in connecting heat pumps with existing systems. “Plant operators must ensure that heat pump retrofits integrate seamlessly with existing processes and/or resources, without impairing productivity or operational efficiencies,” says Kovac. “One way to do that is to install a buffer tank or thermal energy storage (TES), which is essentially a large water repository that can be heated by the heat pump and used when needed.”
Water side management is also essential, says GEA’s Robledo. The use of TES is essential, and there’s a science to sizing the tank, integrating and properly using it. Many consultants and designers fail to get it right. A heat pump does need the TES as part of the system as hot water can’t be drawn on demand directly from the heat pump, which is a recipe for disaster. Another important note: One thing that hurts a heat pump is a phenomenon called internal condensation, which is when the vapor gas condenses into liquid before reaching—or inside—the compressor. Should a compressor run with liquid, it will break. There are rules to avoid such a situation, but full integration will prevent problems.
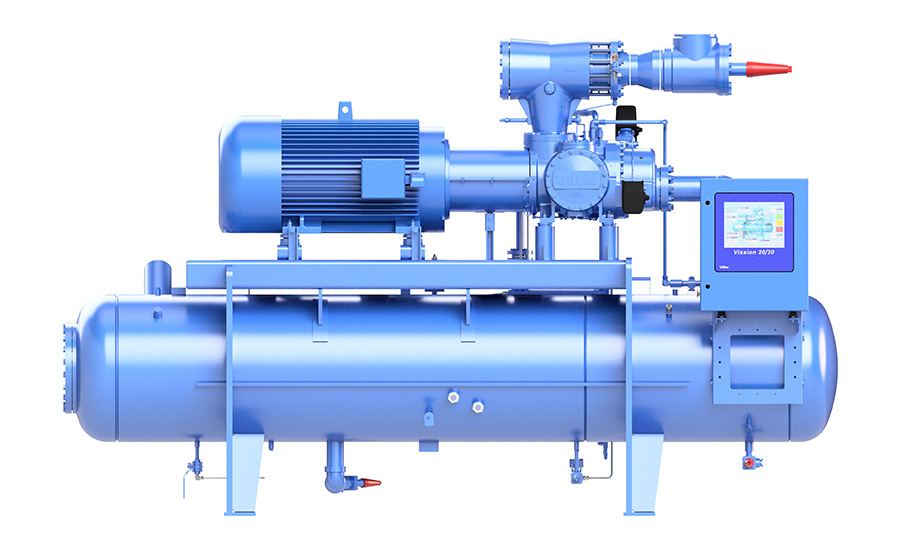
As Ertel notes, another consideration for industrial heat pumps is understanding their potential for simultaneous cooling and heating. “Since most food and beverage processes need both refrigeration and heat, chiller and heat pump systems should be designed to maximize their dual-purpose capabilities,” adds Kovac. “Simply put, every chiller can be used as a heat pump, and every heat pump can be used as a chiller. So, the system must be sized appropriately to produce the required cooling or heating and designed to leverage the beneficial byproduct of the cycle, whether that’s heating or cooling, respectively.”
Benefits from an Integrated Heat Pump System
Benefits of an integrated heat pump system include operational efficiency where waste heat from processes like refrigeration, air compression or other processes can be reused for heating elsewhere in the facility, reducing the need for separate systems and streamlining operations, says Brian Hafendorfer, director, mechanical engineering at Gray. The reduction in equipment footprint can potentially lead to freeing up floor space for the facility. Heat pumps are often more energy efficient than traditional boilers, leading to reductions in energy use and costs when applied correctly. Lower utility needs for the site can provide potential reduction of wiring or piping sizes, or even elimination in some cases, and offer environmental benefits such as lower greenhouse gas emissions, aiding in achieving sustainability targets.
Compared to a traditional boiler, an industrial heat pump typically has three to five times higher COP, depending on the heat potential of the source and other application-specific conditions, says Kovac. These efficiencies may equate directly to long-term, cumulative energy savings, which could significantly lower the total cost of ownership (TCO) throughout the lifecycle—all while cutting GHG emissions by reducing reliance on boilers.
There is a visible and traceable trend of combining the refrigeration and heating COP, says Danfoss’ Miller. “The general efficiency (COP) of heat pumps is far higher than the theoretical 1.0; depending on the use, heat source temperatures and refrigerants, it could range between 2.5 to 7.0 or higher, while fossil fuel-based burners are merely reaching 0.9. The combined system COP (refrigeration combined with heating) could help the individual COP reach higher levels.”

Lower operational costs from enhanced efficiency results in lower lifetime operational costs, adds Hafendorfer. Fewer moving parts and streamlined systems can also reduce maintenance needs. However, the initial investment may result in higher upfront costs that can be offset by long-term savings in energy and maintenance. Return on investment calculations can be provided to assess a variety of system and product strategies to fully optimize the site footprint when considering the building use. Each refrigeration system has its own safety and regulatory considerations, and these can vary greatly by refrigerant type.
An integrated heat pump system can provide significant operational benefits, including energy savings, reduced maintenance costs and a lower total cost of ownership compared to conventional systems, says Güntner’s Herrera. “Real-world installations demonstrate that heat pump systems can deliver substantial benefits, particularly in terms of efficiency and sustainability, making them a viable option for modern food processing facilities. In Sweden can be found Gothenburg’s Östermalm Food Market, which has demonstrated to have achieved significant energy savings and reduced carbon emissions compared to traditional heating and cooling systems. Also Nestlé has implemented heat pump systems in several of its facilities because of substantial energy savings and reduced operational costs of the integration of a heat pump system. In the U.S., Cargill has adopted heat pump technology in various locations to optimize energy use for their industrial processes. It’s an option that has started to grow in the U.S. Industry.”
Real-World Examples, according to Hafendorfer include:
- Dairy plants: Recover heat for pasteurization and cleaning, cutting energy use and costs.
- Breweries: Manage heating and cooling efficiently, lowering energy costs.
- Meat processing plants: Recover heat for hot water, eliminating the need for separate boilers.
Five Reasons to Switch to Natural Refrigerants
Natural refrigerants refer to water, ammonia, CO2 and hydrocarbons such as butane and propane, etc. Synthetic refrigerants typically include fluorine within the molecular structure.
- Cost efficiency: Businesses can achieve significant savings through improved energy efficiency, lower operational costs and reduced need for future retrofits, making natural refrigerants a smart financial investment.
- Sustainability credentials: Adopting natural refrigerants enhances a company’s sustainability profile, boosts brand reputation, and meets consumer and shareholder expectations for environmental responsibility.
- Regulatory compliance: Switching to natural refrigerants helps companies stay ahead of regulatory changes, avoiding potential fines and operational disruptions while ensuring long-term compliance.
- Enhanced food safety and quality: Optimal temperature control extends product shelf life, reduces spoilage and ensures compliance with stringent food safety regulations, guaranteeing the highest quality for consumers.
- Proven technology: Companies benefit from reliable, proven technology that ensures efficient and effective cooling solutions, backed by industry leaders like Güntner.
— Tania Herrera, Güntner US LLC Key Account and Product Engineer
Maintenance and Related Costs
A heat pump has a compressor and rotating equipment, so maintenance is important to protect the investment, says GEA’s Robledo; compressors need proper care. GEA has redesigned and revamped both its piston and screw compressors to protect them from adverse conditions that may occur, especially with condensation.
“Conventional boiler systems have been the norm in many places, with parts and or service more readily available compared to heat pumps,” says Danfoss’ Miller. “More technician training on heat pumps is needed to fully take advantage of heat pumps on a larger scale. That could result in a higher cost of ownership than that of conventional boilers. However, in many cases, some components used in refrigeration systems are already upgraded to the same rating of heat pumps, and this may start equalizing the costs by simplifying maintenance.”
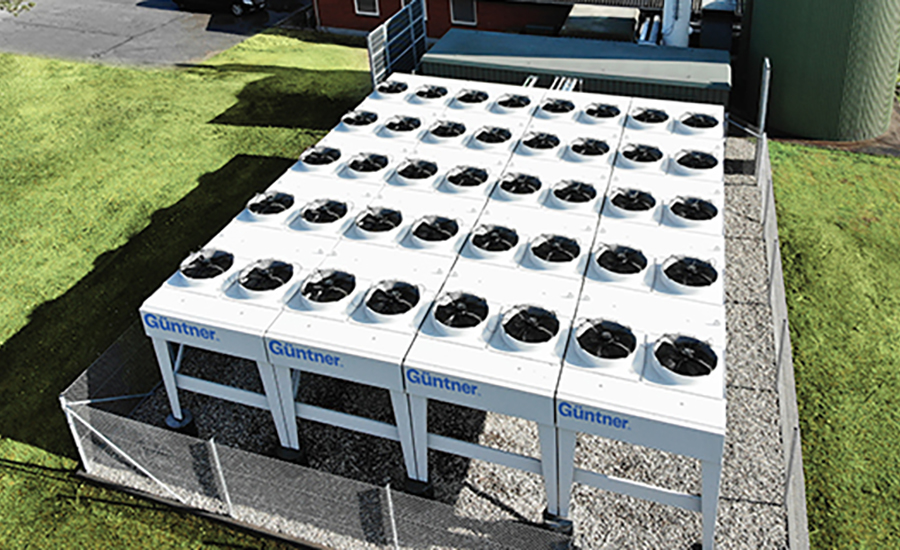
“In terms of preventative maintenance schedules and costs, an industrial heat pump and refrigeration system would have very similar requirements to a traditional boiler system,” says Copeland’s Kovac. “In fact, with the enhanced reliability and durability of the Vilter single-screw compression platforms, operators can expect significant reductions in unplanned maintenance and lost production time. Some customers have reported experiencing more than 50,000 hours of runtime without an unplanned maintenance event.”
Heat Pump Maintenance Costs vs. Conventional Refrigeration and Boiler Systems
Maintenance costs comparison:
- Heat pump system: Heat pumps typically incur lower maintenance costs due to their simpler, integrated design. They operate by transferring heat rather than generating it, which means fewer components are subject to wear and tear. Modern heat pumps often have advanced controls and monitoring systems that help predict and prevent issues before they become serious.
- Conventional refrigeration and boiler system: Traditional systems, which separate refrigeration and heating, usually have higher maintenance requirements. Boilers need regular inspections, cleaning and parts replacement to ensure safe operation. Refrigeration systems also require ongoing maintenance to address issues like refrigerant leaks and compressor wear.
Lifecycle of equipment:
- Heat pump system: Heat pumps generally have a long lifecycle, often lasting 15-20 years with proper maintenance. Their efficiency and fewer mechanical parts contribute to their extended lifespan, leading to a lower total cost of ownership.
- Conventional systems: Boilers typically last around 10-15 years due to the harsh operating conditions, and refrigeration systems may have a similar life expectancy, though components like compressors might need earlier replacement.
Costs and payback:
- Initial costs: Heat pump systems have higher upfront costs due to advanced technology and integration. However, this initial investment is often offset by lower operational and maintenance costs over time. As technology is advanced, costs are coming down.
- Payback period: The payback period for heat pumps varies but often ranges from 5-10 years, with significant cost savings continuing thereafter. This is very system specific and requires careful evaluation to ensure all aspects of cost are considered.
- Long-term savings: Over their lifespan, heat pumps usually have a lower total cost of ownership compared to conventional systems due to reduced energy consumption and maintenance costs.
Advantages and disadvantages:
- Advantages: Heat pumps are more energy-efficient, offer environmental benefits with low-GWP (global warming potential) refrigerants, and provide precise temperature control, enhancing product quality in food processing.
- Disadvantages: Higher initial investment and installation complexity can be barriers. Performance can also be affected by ambient temperatures, requiring supplemental heating in extremely cold climates. In recent years, cold climate technologies have rapidly advanced which will allow for fewer locale restrictions.
Heat pump systems present notable long-term benefits over conventional refrigeration and boiler systems, including lower maintenance costs, extended equipment life, and significant energy savings. Despite higher initial costs and installation complexity, their operational efficiencies and environmental advantages make them an appealing choice for food processors.
— Nick Ertel, P.E., Manager, Refrigeration Engineering at Gray
“Heat pump systems generally offer lower maintenance costs, longer-term energy savings and environmental benefits compared to conventional refrigeration and boiler systems,” says Güntner’s Herrera. They can have higher initial costs and may require specialized maintenance. Conventional systems might be cheaper to install and simpler to maintain but tend to have higher ongoing costs and a greater environmental impact. To evaluate the best option, it’s important to consider factors such as the local weather, energy prices, if there’s any incentive available (which there usually are) and the specific needs of the facility.
The lifecycle of a heat pump is about 20 years, the same level as refrigeration systems, adds Miller. The payback period needs to be evaluated on a case-by-case basis. In general, the higher the COP of the particular application, the faster the payback period.
For more on maintenance, see the box, “Heat Pump Maintenance Costs vs. Conventional Refrigeration and Boiler Systems.”
Resources:
“Industrial Heat Pumps are the Past, Present and Future,” By Wayne Borrowman, FE, May 2024
“GEA to Supply RedGenium Heat Pump to Canadian Dairy Processor,” FE, July 2024
Looking for a reprint of this article?
From high-res PDFs to custom plaques, order your copy today!