Food Safety
Are you doing all you can to keep glass out of your products?
Food processors must develop and maintain a program to manage glass and brittle plastic in their plants.
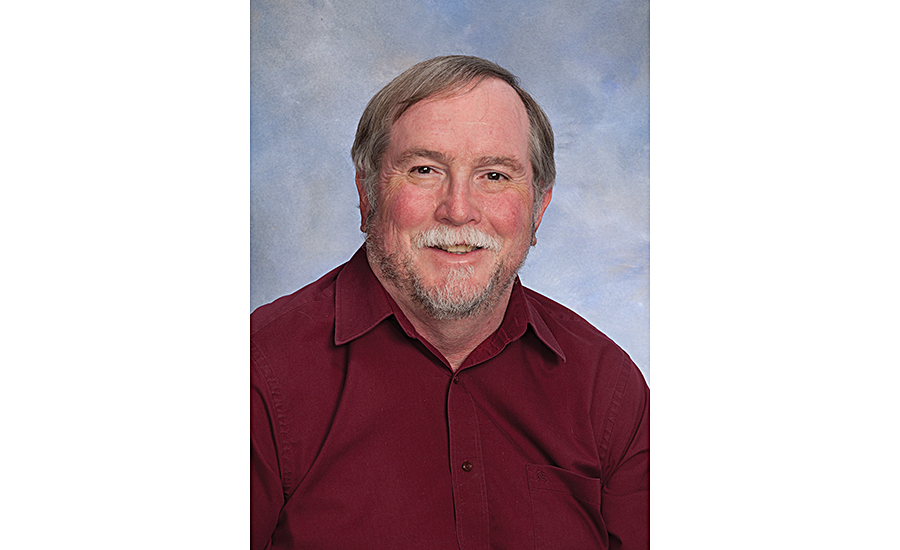
Any food product with glass in it is, of course, deemed to be adulterated. Consequently, it is imperative each food processor develops, documents, implements and maintains a program to manage glass and brittle plastic in its plant.
The Pure Food, Drug and Cosmetic Act states:
“A food shall be deemed to be adulterated (3) if it consists in whole or in part of any filthy, putrid or decomposed substance, or if it is unfit for food; or (4) if it has been prepared, packed or held under insanitary conditions whereby it may have become contaminated with filth, or whereby it may have been rendered injurious to health.”
According to this act, any foreign material in a food or ingredient, whether it is glass, wood, metal or plastic, renders that product adulterated. And, knowingly distributing an adulterated item is a violation of the act. This is why we see recalls with the phrase, “May contain XX,” in the notices released by FDA, USDA and the Canadian Food Inspection Agency.
Upon examining such a recall, one usually finds a disclaimer stating this situation would not cause injury, and no injuries have been reported. In this case, the company initiated the recall to adhere to the law, and to protect itself and the public.
The role of a processor’s glass and brittle plastic program, according the act, should be: “To minimize the potential for cross-contamination with glass or brittle plastic to ensure that foods and ingredients are safe and will not result in injury to end-users.”
When companies tell me they do not need a glass and brittle plastic program, because they don’t allow glass in their plant nor do they pack in glass, I ask them if there are any light bulbs or gauge covers in their plant. This one question is usually enough to end the discussion.
The first step in implementing a glass and brittle plastic program is to establish rules mandating no ceramics or glass—including watches and eyeglasses—in the processing areas, shops or warehouses. Eyeglass lenses should be made of hard plastic; workers who don’t have plastic lenses in their eyewear should have the option of wearing protective goggles.
In addition, all windows and light fixtures in production and warehouse areas must be shatterproof, shielded or covered with plastic to contain breakage. Shatterproof LED lights offer food processors an option that not only protects their product from contamination, it utilizes less energy and may even provide better lighting.
The next step for establishing a program is to inventory all glass and brittle plastics in areas where foods and ingredients are stored or handled, including the warehouse, production and packaging areas, and shops. The inventory should specify the location of glass or plastic; the type of glass or plastic (if possible); and whether it is shielded or strengthened in any way. The inventory must also include the area or areas where glass and brittle plastic are stored. Then, each item should be transferred to a master list.
Once this has been created, the food safety team should conduct a risk assessment focused on the potential for breakage and product contamination for each item on the list. Potential risk can be ranked numerically or as low, medium or high.
The master list should be used as a basis for regular internal audits of the glass and brittle plastic in the plant. The food safety or HACCP team should determine how often these are conducted based on overall risk. When any cracked, damaged, broken or ill-fitting items are noted, corrective actions should be initiated immediately. In addition, all employees should be trained on the program and instructed to report any observed breakage.
The glass and brittle plastic program must also include protocols for transporting glass through the facility. For example, whenever a light bulb, gauge cover or other item on the master list needs to be replaced, maintenance personnel must ensure it is transported in its original box or contained in some way, so that if it is dropped and breaks, it is fully contained.
The final element of the program must address what to do if a glass breakage incident occurs. Some of these steps include:
- If glass or brittle plastic breaks in the production area or warehouse, operations must cease immediately.
- All exposed product must be segregated and placed on hold.
- Workers in the breakage area will remain where they are, so they do not spread the material throughout the plant. Their shoes will be inspected prior to the workers leaving the area and cleaned, if necessary.
- Broken glass and brittle plastic must be cleaned up using designated tools and disposed of in designated containers.
- Glass and plastic breakage will be recorded in a Glass and Brittle Plastic Breakage Log, noting the type of breakage, the location, whether any product was affected and, if so, the disposition of the product.
- Plant management will meet to discuss all incidents; determine their cause; and implement a corrective/preventive action plan to minimize the potential for future incidents.
Again, it is imperative all employees are trained on this element of the program, and the training is properly documented. A processor packaging in glass obviously needs an expanded program, since glass breakage may likely be a daily occurrence. For instance, the glass and brittle plastic program for a typical glass-packing operation might establish how much product is to be removed from the line in the event of breakage and/or the distances on either side of the breakage from which all product (in opened and unopened containers) will be removed from the line and inspected and/or destroyed.
In addition, the type of product being packaged and processed affects the program. For example, a baby food manufacturer will probably have more stringent requirements than a processor that packages jams or jellies.
The final element any glass packager should include in its program is the verification of online washers. A processor can verify its washers’ effectiveness by “spiking” some bottles or jars with glass particles, paper or other potential contaminants, marking the spiked containers and passing them through a washer. After rinsing the containers, the processor should pour the water through filters to collect any contaminants. If any are recovered, the processor knows the washer is not doing its job.
A glass and brittle plastic program should be part of each and every food processor’s program to protect its products from contamination with foreign materials. And, that program should be a part of the training all employees receive, since they play an integral role in ensuring the program actually works as designed.
Looking for a reprint of this article?
From high-res PDFs to custom plaques, order your copy today!